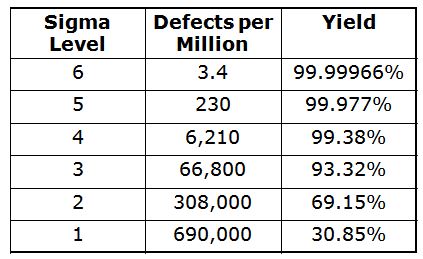
Lean service is a method that applies lean manufacturing production techniques in the service sector. HMRC in England and the US are examples of companies who have adopted this approach in their production processes. Lean services are intended to reduce waste and increase customer satisfaction while reducing costs. You can make your business more efficient, whether you are a startup or a multinational corporation.
Lean manufacturing
Lean manufacturing is a process that is based on eliminating waste. The process improves productivity, lowers operating costs and increases employee satisfaction. Ultimately, it can increase profits. It can reduce the time it takes to produce a product, and increase profits. Additionally, lean manufacturing can help companies improve their customer base to increase their revenue streams.
Lean manufacturing requires a team approach and a lot of talent. It is vital that everyone on the team knows the process. Additionally, they must be able adapt the practices to suit the company's needs. Simpler manufacturing processes are the first step of lean manufacturing. Complex manufacturing processes can make identifying waste and inefficiencies difficult. Simplifying the process can improve visibility and foster a culture for continuous improvement. This will empower employees to seek out inefficiencies.
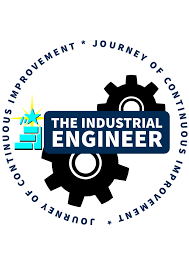
Lean manufacturing services can be used to improve efficiency and decrease lead time. MXGlobal, one of these companies that offers lean implementation has successfully consulted Japanese firms with a U.S. present. The firm's lean production services are designed to help companies grow internationally and meet their business goals.
Businesses can create a lean manufacturing environment to maximize their profits. They help businesses reduce waste and improve productivity. There are eight types. These include overproduction, inventory, transport, and defects. These wastes can lead to higher costs and lower customer satisfaction.
Management of lean operations
Lean operations management is a process that enables organizations to identify their goals and objectives. As the name implies, it is a systematic approach that seeks to create value for the end customers. Customers expect value from products and services. It is what drives sales. You can start by mapping out all the steps involved with the creation and delivery of a product. Then ask yourself: "What adds the most value to the customer?"
Lean management systems aim to continuously improve their processes. This is the most important part of lean management. It ensures your team can deliver work assignments more quickly and with less effort. This reduces waste from production processes and optimizes overhead and storage. The four principles of Lean Management include continuous improvement and minimization, minimizing waste, reducing cycles time, and ensuring continuous workflows.
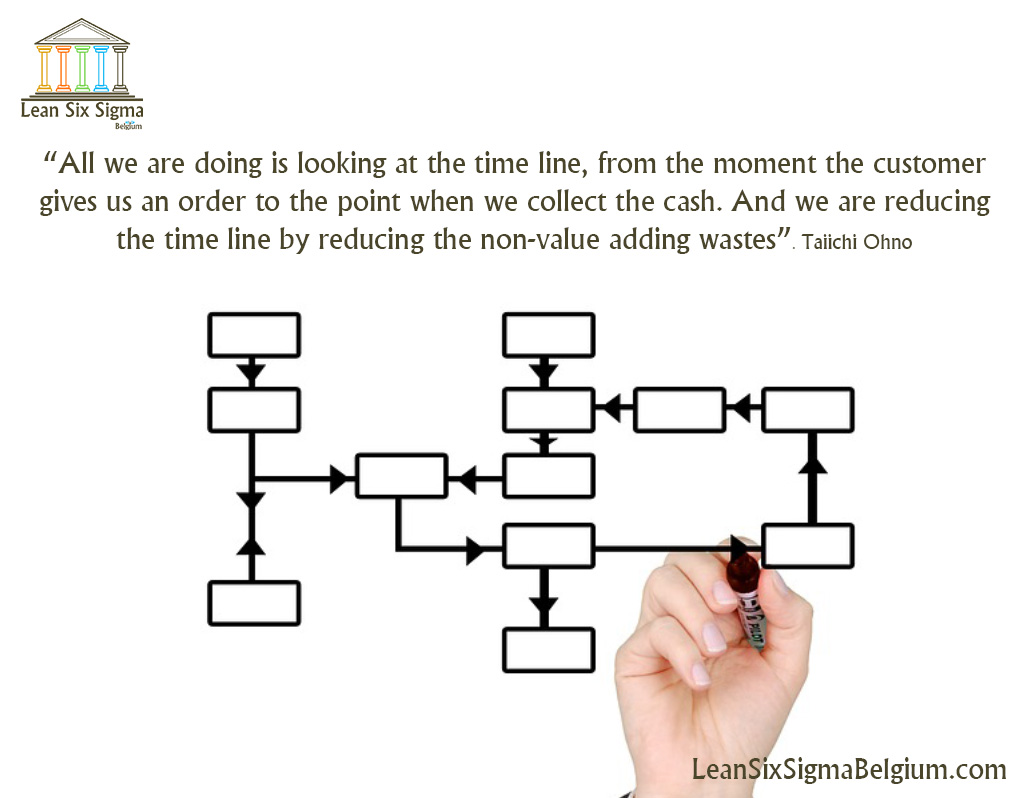
Lean operations management for lean services focuses on creating more value for customers with fewer resources. Intangible wastes are harder to identify in a service environment, but lean principles work to reduce and eliminate them. Companies can increase their customer value and maximize profits by eliminating waste.
FAQ
What are the jobs in logistics?
There are many kinds of jobs available within logistics. Some of them are:
-
Warehouse workers – They load, unload and transport pallets and trucks.
-
Transportation drivers – They drive trucks or trailers to transport goods and perform pick-ups.
-
Freight handlers - They sort and pack freight in warehouses.
-
Inventory managers – These people oversee inventory at warehouses.
-
Sales representatives: They sell products to customers.
-
Logistics coordinators are responsible for organizing and planning logistics operations.
-
Purchasing agents – They buy goods or services necessary to run a company.
-
Customer service representatives are available to answer customer calls and emails.
-
Shipping clerks: They process shipping requests and issue bills.
-
Order fillers – They fill orders based upon what was ordered and shipped.
-
Quality control inspectors (QCI) - They inspect all incoming and departing products for potential defects.
-
Other - Logistics has many other job opportunities, including transportation supervisors, logistics specialists, and cargo specialists.
How is a production manager different from a producer planner?
The main difference between a production planner and a project manager is that a project manager is usually the person who plans and organizes the entire project, whereas a production planner is mainly involved in the planning stage of the project.
Can we automate some parts of manufacturing?
Yes! Since ancient times, automation has been in existence. The Egyptians discovered the wheel thousands and years ago. We now use robots to help us with assembly lines.
Actually, robotics can be used in manufacturing for many purposes. These include:
-
Line robots
-
Robot welding
-
Robot painting
-
Robotics inspection
-
Robots that create products
Automation can be applied to manufacturing in many other ways. For example, 3D printing allows us to make custom products without having to wait for weeks or months to get them manufactured.
Do we need to know about Manufacturing Processes before learning about Logistics?
No. No. Knowing about manufacturing processes will help you understand how logistics works.
What are my options for learning more about manufacturing
You can learn the most about manufacturing by getting involved in it. You can read books, or watch instructional videos if you don't have the opportunity to do so.
Statistics
- [54][55] These are the top 50 countries by the total value of manufacturing output in US dollars for its noted year according to World Bank.[56] (en.wikipedia.org)
- According to the United Nations Industrial Development Organization (UNIDO), China is the top manufacturer worldwide by 2019 output, producing 28.7% of the total global manufacturing output, followed by the United States, Japan, Germany, and India.[52][53] (en.wikipedia.org)
- Many factories witnessed a 30% increase in output due to the shift to electric motors. (en.wikipedia.org)
- It's estimated that 10.8% of the U.S. GDP in 2020 was contributed to manufacturing. (investopedia.com)
- In 2021, an estimated 12.1 million Americans work in the manufacturing sector.6 (investopedia.com)
External Links
How To
How to Use the Just In Time Method in Production
Just-in-time (JIT) is a method that is used to reduce costs and maximize efficiency in business processes. This is where you have the right resources at the right time. This means that you only pay the amount you actually use. Frederick Taylor, a 1900s foreman, first coined the term. He noticed that workers were often paid overtime when they had to work late. He then concluded that if he could ensure that workers had enough time to do their job before starting to work, this would improve productivity.
The idea behind JIT is that you should plan ahead and have everything ready so you don't waste money. Also, you should look at the whole project from start-to-finish and make sure you have the resources necessary to address any issues. You will have the resources and people to solve any problems you anticipate. This will ensure that you don't spend more money on things that aren't necessary.
There are many JIT methods.
-
Demand-driven: This JIT is where you place regular orders for the parts/materials that are needed for your project. This will allow for you to track the material that you have left after using it. This will let you know how long it will be to produce more.
-
Inventory-based: This allows you to store the materials necessary for your projects in advance. This allows one to predict how much they will sell.
-
Project-driven: This method allows you to set aside enough funds for your project. You will be able to purchase the right amount of materials if you know what you need.
-
Resource-based JIT is the most widespread form. You assign certain resources based off demand. If you have many orders, you will assign more people to manage them. If you don't have many orders, you'll assign fewer people to handle the workload.
-
Cost-based: This is the same as resource-based except that you don't care how many people there are but how much each one of them costs.
-
Price-based: This is similar to cost-based but instead of looking at individual workers' salaries, you look at the total company price.
-
Material-based: This approach is similar to cost-based. However, instead of looking at the total cost for the company, you look at how much you spend on average on raw materials.
-
Time-based JIT: A variation on resource-based JIT. Instead of focusing on how much each employee costs, you focus on how long it takes to complete the project.
-
Quality-based JIT - This is another form of resource-based JIT. Instead of looking at the labor costs and time it takes to make a product, think about its quality.
-
Value-based: This is one of the newest forms of JIT. In this case, you're not concerned with how well the products perform or whether they meet customer expectations. Instead, you focus on the added value that you provide to your market.
-
Stock-based: This inventory-based approach focuses on how many items are being produced at any one time. It is used when production goals are met while inventory is kept to a minimum.
-
Just-in time (JIT), planning: This is a combination JIT/supply chain management. It is the process of scheduling components' delivery as soon as they have been ordered. It is essential because it reduces lead-times and increases throughput.