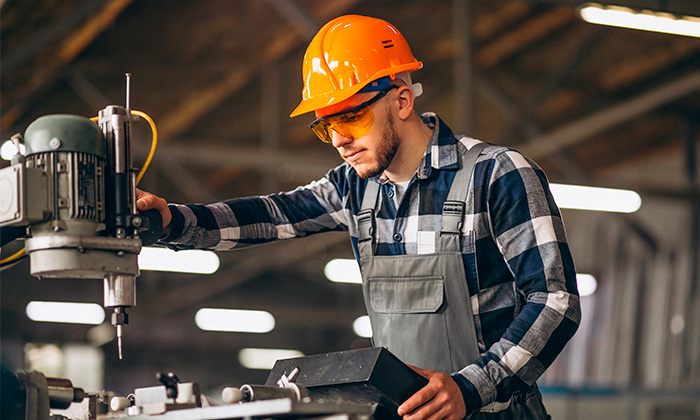
The key elements of bringing back manufacturing to America are reshoring and Opportunity zones, Deregulatory strategy, and lower transportation cost. What can America do to help? Here are a few suggestions:
Relocation
Companies have begun reshoring production back to the U.S., including Intel, which is investing $20 billion to build two new semiconductor plants in Arizona. General Motors is just one company that has started to move its battery production to Michigan. Michigan is poised to become an important hub for lithium-based goods. US Steel has decided to not build its new $3B steelmaking plant overseas, instead choosing to build a plant either in Alabama or Arkansas. Other companies considering reshoring include Lockheed Electric, General Electric, as well as Thermo Fisher.
Opportunity zones
Trump's administration is a staunch supporter opportunity zones. In January of 2017, it established a council, the White House Opportunity and Revitalization Council, to further support the development of these zones. It has also expanded quoting forms, and prioritized them. California has one arm tied regarding opportunity zones. Listed below are five strategies that local investors can follow to maximize their investment opportunities.
Deregulatory strategy
The United States has struggled long to attract large manufacturers. The tide is turning, however. Walmart and other large companies have increased their investments in America. The Manufacturing Institute released a study that shows American manufacturing is 9 percentage cheaper than in nine countries with high-cost manufacturing.
Reduced transportation costs
Reducing transportation costs is one of the most significant factors driving companies to relocate their manufacturing to the United States. As a result, companies are able to bring manufacturing jobs back to the United States, where labor costs are lower than overseas. Relocating manufacturing operations from overseas is not an easy task. It could take years for jobs to be brought back to the United States. The cost of goods will rise, but there would be numerous benefits. Recently, the Covid-19 pandemic brought supply chain issues to the forefront of the American public's consciousness. Products like toilet paper and pharmaceuticals were affected.
Qualified labor
Manufacturing is a key political issue, as has the surprise revelation of recent presidential election results. Commentators declared that "U.S. manufacturing is having a moment." Unfortunately, campaign rhetoric does not translate into long-term commitment. Washington D.C. has a tendency to discuss trade and other issues which don't directly affect manufacturing. They also neglect to address strategies that would support manufacturing communities and clusters.
FAQ
What is production plan?
Production Planning is the creation of a plan to cover all aspects, such as scheduling, budgeting. Location, crew, equipment, props and other details. This document will ensure everything is in order and ready to go when you need it. It should also provide information about how best to produce the best results while on set. It should include information about shooting locations, casting lists, crew details, equipment requirements, and shooting schedules.
The first step is to outline what you want to film. You may have already chosen the location you want, or there are locations or sets you prefer. Once you have identified the scenes and locations, you can start to determine which elements are required for each scene. If you decide you need a car and don't know what model to choose, this could be an example. To narrow your options, you can search online for available models.
After you have selected the car you want, you can begin to think about additional features. You might need to have people in the front seats. Or maybe you just need someone to push the car around. You might want to change your interior color from black and white. These questions can help you decide the right look for your car. It is also worth considering the types of shots that you wish to take. Do you want to film close-ups, or wider angles? Maybe you want to show the engine and the steering wheel. This will allow you to determine the type of car you want.
Once you have determined all of the above, you can move on to creating a schedule. The schedule will show you when to begin shooting and when to stop. Each day will include the time when you need to arrive at the location, when you need to leave and when you need to return home. This way, everyone knows what they need to do and when. If you need to hire extra staff, you can make sure you book them in advance. It is not worth hiring someone who won’t show up because you didn’t tell him.
Your schedule will also have to be adjusted to reflect the number of days required to film. Some projects may only take a couple of days, while others could last for weeks. You should consider whether you will need more than one shot per week when creating your schedule. Multiple shots at the same location can increase costs and make it more difficult to complete. It is better to be cautious and take fewer shots than you risk losing money if you are not sure if multiple takes are necessary.
Budget setting is another important aspect in production planning. It is important to set a realistic budget so you can work within your budget. Remember that you can always reduce the budget later on if you run into unforeseen problems. But, don't underestimate how much money you'll spend. You'll end up with less money after paying for other things if the cost is underestimated.
Production planning is a detailed process. But, once you understand the workings of everything, it becomes easier for future projects to be planned.
What is the job of a manufacturer manager?
Manufacturing managers must ensure that manufacturing processes are efficient, effective, and cost-effective. They must also be alert to any potential problems and take appropriate action.
They should also be able and comfortable communicating with other departments like sales and marketing.
They should also be knowledgeable about the latest trends in the industry so they can use this information for productivity and efficiency improvements.
What does it take for a logistics enterprise to succeed?
It takes a lot of skills and knowledge to run a successful logistics business. Good communication skills are essential to effectively communicate with your suppliers and clients. You should be able analyse data and draw inferences. You must be able and able to handle stress situations and work under pressure. In order to innovate and create new ways to improve efficiency, creativity is essential. You must be a strong leader to motivate others and direct them to achieve organizational goals.
To meet tight deadlines, you must also be efficient and organized.
How can manufacturing avoid production bottlenecks
You can avoid bottlenecks in production by making sure that everything runs smoothly throughout the production cycle, from the moment you receive an order to the moment the product is shipped.
This includes planning for capacity requirements as well as quality control measures.
The best way to do this is to use continuous improvement techniques such as Six Sigma.
Six Sigma management is a system that improves quality and reduces waste within your organization.
It focuses on eliminating variation and creating consistency in your work.
Statistics
- You can multiply the result by 100 to get the total percent of monthly overhead. (investopedia.com)
- In 2021, an estimated 12.1 million Americans work in the manufacturing sector.6 (investopedia.com)
- According to the United Nations Industrial Development Organization (UNIDO), China is the top manufacturer worldwide by 2019 output, producing 28.7% of the total global manufacturing output, followed by the United States, Japan, Germany, and India.[52][53] (en.wikipedia.org)
- According to a Statista study, U.S. businesses spent $1.63 trillion on logistics in 2019, moving goods from origin to end user through various supply chain network segments. (netsuite.com)
- Many factories witnessed a 30% increase in output due to the shift to electric motors. (en.wikipedia.org)
External Links
How To
Six Sigma in Manufacturing:
Six Sigma is defined by "the application SPC (statistical process control) techniques to achieve continuous improvements." Motorola's Quality Improvement Department in Tokyo, Japan developed Six Sigma in 1986. Six Sigma's basic concept is to improve quality and eliminate defects through standardization. Many companies have adopted this method in recent years. They believe there is no such thing a perfect product or service. The main goal of Six Sigma is to reduce variation from the mean value of production. This means that if you take a sample of your product, then measure its performance against the average, you can find out what percentage of the time the process deviates from the norm. If the deviation is excessive, it's likely that something needs to be fixed.
Understanding the nature of variability in your business is the first step to Six Sigma. Once you understand that, it is time to identify the sources of variation. Also, you will need to identify the sources of variation. Random variations occur when people do mistakes. Symmetrical variations are caused due to factors beyond the process. These are, for instance, random variations that occur when widgets are made and some fall off the production line. If however, you notice that each time you assemble a widget it falls apart in exactly the same spot, that is a problem.
Once you've identified where the problems lie, you'll want to design solutions to eliminate those problems. It might mean changing the way you do business or redesigning it entirely. Once you have implemented the changes, it is important to test them again to ensure they work. If they don't work, you will need to go back to the drawing boards and create a new plan.