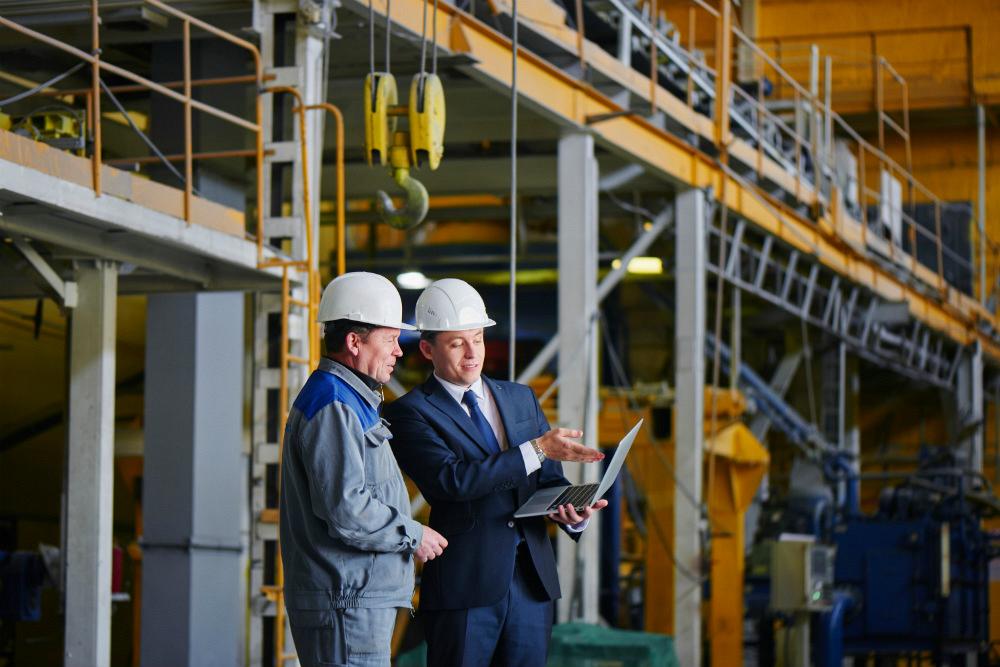
A director in manufacturing is responsible to manage the company's production processes. As they are responsible for managing the entire production process, their role is critical. For this position to be successful, candidates must have experience in manufacturing and familiarity with new technologies. Robotics and 3D printing are two examples of these technologies. It is a benefit to a director who stays current with the latest technologies. As the manufacturing industry continues to evolve, the director's role will become increasingly complex, as he or she must work with the engineering and operations departments, as well as putting a greater emphasis on quality control within the manufacturing plant.
Salary for a director in manufacturing
The pay scale for a Director of Manufacturing depends on where they live. Many directors get a salary in the low six figures, but some earn more than others. A Director of Manufacturing's salary can vary depending on education and years of experience. In order to determine how much you'll earn in your area, consider a few factors that may influence your salary:
The salary for a director of manufacturing varies but it's generally higher if you have more work experience. As with many positions, the cost of living and location may also affect salary. You will earn a higher salary if you live in a large city. However, your salary may not be sufficient to cover the cost of living. If the opportunity presents itself, you should be ready to negotiate for a better salary.
A Director in Manufacturing Operations earns between $181,000.500 and $66,000 per year. The salary for a Director of Manufacturing Operations is highly variable and can vary by up to 8% between different cities. The average salary for a director of manufacturing operations in Fremont is $128,493 to $164,500. This is significantly higher than the national average. However, the salary for a Director of Manufacturing Operations varies greatly depending on the location, experience level, and company.
Education required
Director of manufacturing is responsible to manage a manufacturing facility and supervise the production process. The director of manufacturing is responsible for hiring new workers, overseeing quality control, working with designers, as well as meeting operational standards. A director of manufacturing typically reports to the senior management team and executes policy and sales initiatives. Candidates should have some experience in manufacturing and be good communicators. Each company has its own requirements regarding education for a manufacturing director.
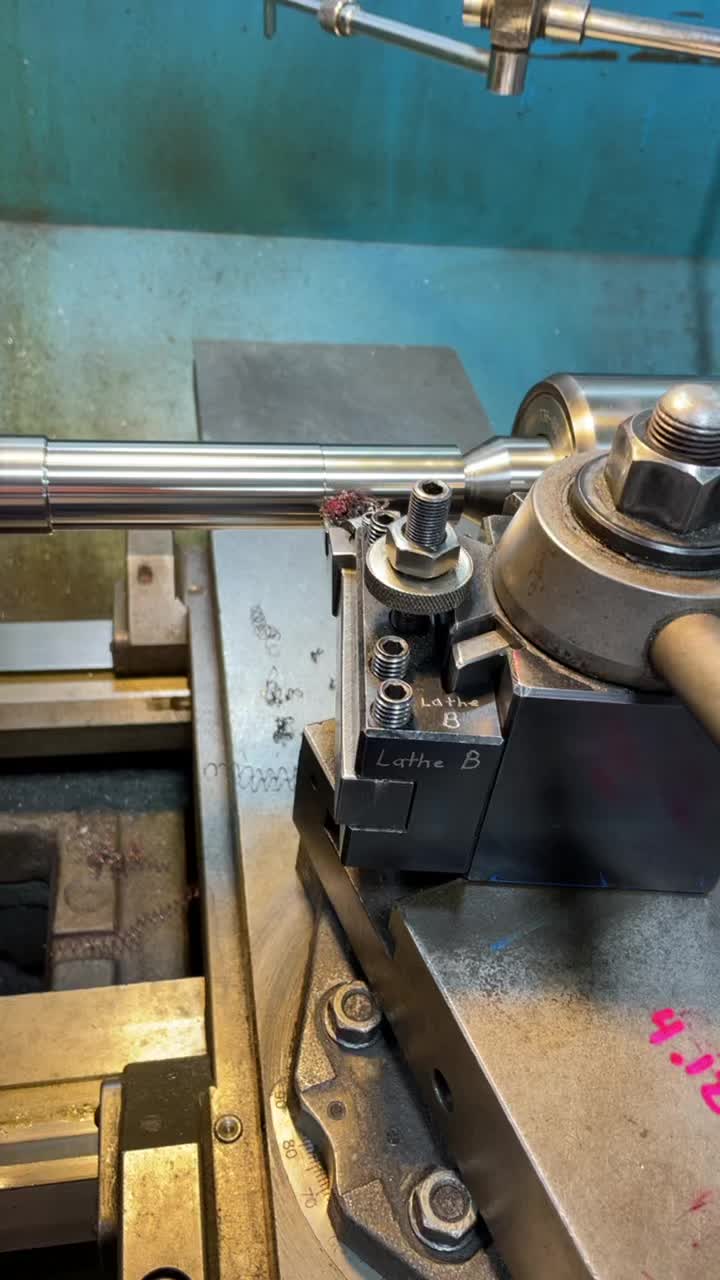
Although a master's degree in engineering does not necessarily make you a director in manufacturing, having a post-secondary education is a great way to increase your knowledge and skill set. An MBA program is an excellent choice for this role, since it allows candidates to learn more about management, business administration, and economics. You will eventually have to manage a diverse workforce.
You will collaborate closely with engineers and designers as a director for manufacturing during the product development phase. You will play a key role in this stage by evaluating new processes and making sure quality standards are met before you commit resources to larger productions. As well as overseeing production, directors can also serve as coaches to employees. They will guide them in risk mitigation and best practice. A manufacturing director must not only oversee the production process but also be able to solve problems.
Experience required
For this job, a bachelor's in a relevant field is required along with five to 10 years progressive work experience. In general, manufacturing companies prefer to hire employees for this job. A candidate who is a good fit for this role will have an in-depth understanding of manufacturing processes and business goals. Employers may want to see a graduate level. Candidates may also need additional training in the chosen industry or field.
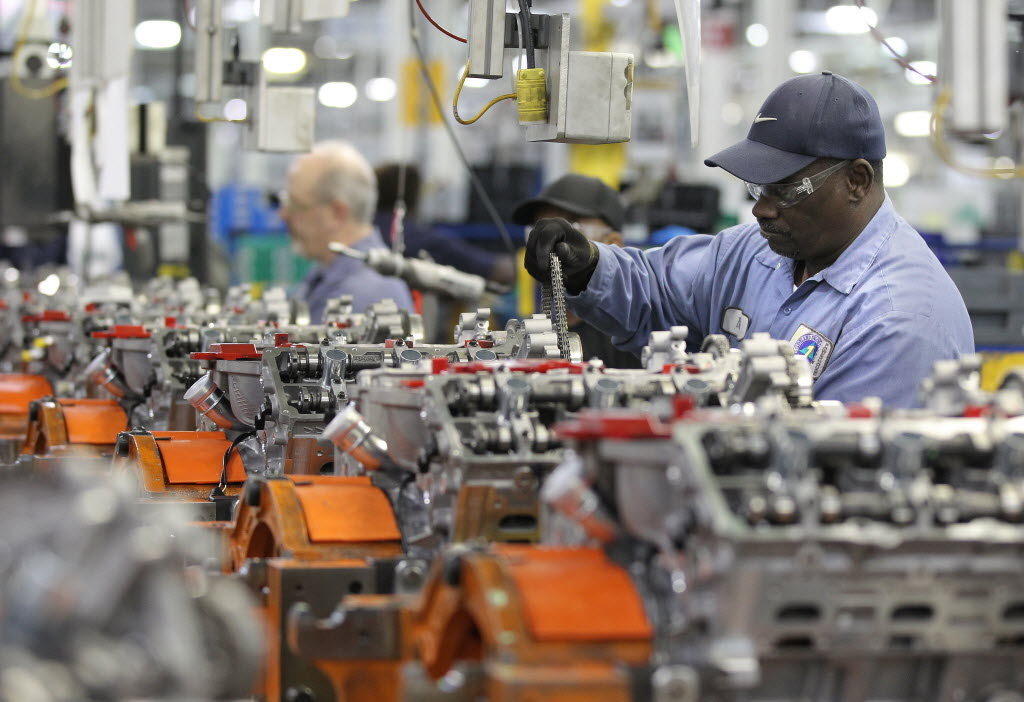
The manufacturing director oversees all aspects of the production process including workers, supervisors and engineers. They could be responsible to solve problems and develop solutions. They may be responsible for overseeing production and developing quality-control plans. The director of manufacturing reports directly the top executive of the manufacturing company. Manufacturing experience is a must. Experience in manufacturing management can help you succeed in this position.
Experience as a manufacturing director will be an asset. Directors must have at the least 10 years relevant experience working in a manufacturing environment. These people might have been employed as technicians or supervisors in manufacturing. They should have excellent communication skills. Also, a director of manufacturing needs to have a good understanding of business strategy. The director of manufacturing should also be able work well with other departments in the company. As such, the director is responsible for overseeing the production process and ensuring that it meets all quality standards.
FAQ
How can I find out more about manufacturing?
You can learn the most about manufacturing by getting involved in it. But if that is not possible you can always read books and watch educational videos.
What is production plan?
Production Planning refers to the development of a plan for every aspect of production. This document ensures that everything is prepared and available when you are ready for shooting. This document should include information about how to achieve the best results on-set. This includes location information, crew details, equipment specifications, and casting lists.
It is important to first outline the type of film you would like to make. You may have already chosen the location you want, or there are locations or sets you prefer. Once you have identified the scenes and locations, you can start to determine which elements are required for each scene. Perhaps you have decided that you need to buy a car but aren't sure which model. You could look online for cars to see what options are available, and then narrow down your choices by selecting between different makes or models.
After you've found the perfect car, it's time to start thinking about adding extras. Do you have people who need to be seated in the front seat? Perhaps you have someone who needs to be able to walk around the back of your car. Maybe you'd like to change the interior from black to a white color. These questions can help you decide the right look for your car. Also, think about what kind of shots you would like to capture. What type of shots will you choose? Maybe you want the engine or the steering wheels to be shown. These details will help identify the exact car you wish to film.
Once you have established all the details, you can create a schedule. You will know when you should start and when you should finish shooting. Every day will have a time for you to arrive at the location, leave when you are leaving and return home when you are done. Everyone knows exactly what they should do and when. Hire extra staff by booking them ahead of time. There is no point in hiring someone who won't turn up because you didn't let him know.
Also, consider how many days you will be filming your schedule. Some projects take only a few days while others can last several weeks. You should consider whether you will need more than one shot per week when creating your schedule. Multiple shots at the same location can increase costs and make it more difficult to complete. If you are unsure if you need multiple takes, it is better to err on the side of caution and shoot fewer takes rather than risk wasting money.
Another important aspect of production planning is setting budgets. As it will allow you and your team to work within your financial means, setting a realistic budget is crucial. Keep in mind that you can always reduce your budget if you face unexpected difficulties. You shouldn't underestimate the amount you'll spend. You'll end up with less money after paying for other things if the cost is underestimated.
Planning production is a tedious process. Once you have a good understanding of how everything works together, planning future projects becomes easy.
What is the importance of automation in manufacturing?
Automating is not just important for manufacturers, but also for service providers. It allows them provide faster and more efficient services. In addition, it helps them reduce costs by reducing human errors and improving productivity.
Why is logistics so important in manufacturing?
Logistics are an integral part any business. Logistics can help you achieve amazing results by helping to manage product flow from raw materials to finished products.
Logistics plays a significant role in reducing cost and increasing efficiency.
How can manufacturing efficiency improved?
The first step is to identify the most important factors affecting production time. We then need to figure out how to improve these variables. If you don’t know where to begin, consider which factors have the largest impact on production times. Once you've identified them all, find solutions to each one.
How can manufacturing avoid production bottlenecks
Avoiding production bottlenecks is as simple as keeping all processes running smoothly, from the time an order is received until the product ships.
This includes both quality control and capacity planning.
Continuous improvement techniques such Six Sigma can help you achieve this.
Six Sigma management is a system that improves quality and reduces waste within your organization.
It focuses on eliminating variation and creating consistency in your work.
Statistics
- In 2021, an estimated 12.1 million Americans work in the manufacturing sector.6 (investopedia.com)
- Many factories witnessed a 30% increase in output due to the shift to electric motors. (en.wikipedia.org)
- Job #1 is delivering the ordered product according to specifications: color, size, brand, and quantity. (netsuite.com)
- You can multiply the result by 100 to get the total percent of monthly overhead. (investopedia.com)
- According to a Statista study, U.S. businesses spent $1.63 trillion on logistics in 2019, moving goods from origin to end user through various supply chain network segments. (netsuite.com)
External Links
How To
How to Use Six Sigma in Manufacturing
Six Sigma can be described as "the use of statistical process control (SPC), techniques to achieve continuous improvement." Motorola's Quality Improvement Department, Tokyo, Japan, developed it in 1986. Six Sigma's core idea is to improve the quality of processes by standardizing and eliminating defects. Many companies have adopted this method in recent years. They believe there is no such thing a perfect product or service. The main goal of Six Sigma is to reduce variation from the mean value of production. You can calculate the percentage of deviation from the norm by taking a sample of your product and comparing it to the average. If the deviation is excessive, it's likely that something needs to be fixed.
Understanding the dynamics of variability within your business is the first step in Six Sigma. Once you've understood that, you'll want to identify sources of variation. Also, you will need to identify the sources of variation. Random variations occur when people do mistakes. Symmetrical variations are caused due to factors beyond the process. Random variations would include, for example, the failure of some widgets to fall from the assembly line. It would be considered a systematic problem if every widget that you build falls apart at the same location each time.
Once you have identified the problem, you can design solutions. It might mean changing the way you do business or redesigning it entirely. Once you have implemented the changes, it is important to test them again to ensure they work. If they fail, you can go back to the drawing board to come up with a different plan.