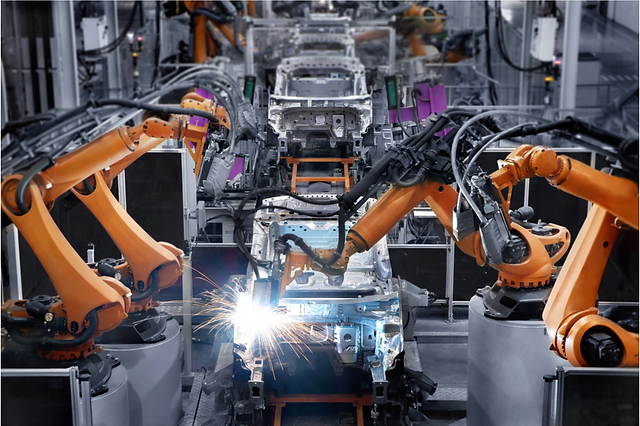
There is a great demand for logistics positions in Jacksonville, Florida. These positions play an important role in the shipping and distribution of goods from factories to customers' homes. This field is highly lucrative, especially if the job is well-paid. Here are some tips to help get you your dream job.
To begin, you should create a Monster profile. This will allow you to receive job alerts for free and a personalized listing of relevant listings. You will also get expert advice. A savvy recruiter will even take the time to explain the perks of working for a certain company, so you'll be armed and ready to slay the competition. It's easy to get the job done if you know what your qualifications are and how they relate to the job you are applying for.
Consider a paid internship while you're at work. The cost of a paid internship is $10 to $15 per hour. You will learn how to work for professionals. In addition, you'll have real-world experiences that you can put to use when you search for a job. This is the best kind of training you can get. Plus, you'll be rewarded with a swag bag of goodies.
The most important piece of information is that you don't have to be a logistics whiz to land the job of your dreams. There are many options for entry-level, low-skilled logistics professionals. Vaco and Penske both offer traditional work environments while others offer flexible options. No matter which route you take, chances are you will find a position that suits your needs in Jacksonville, FL.
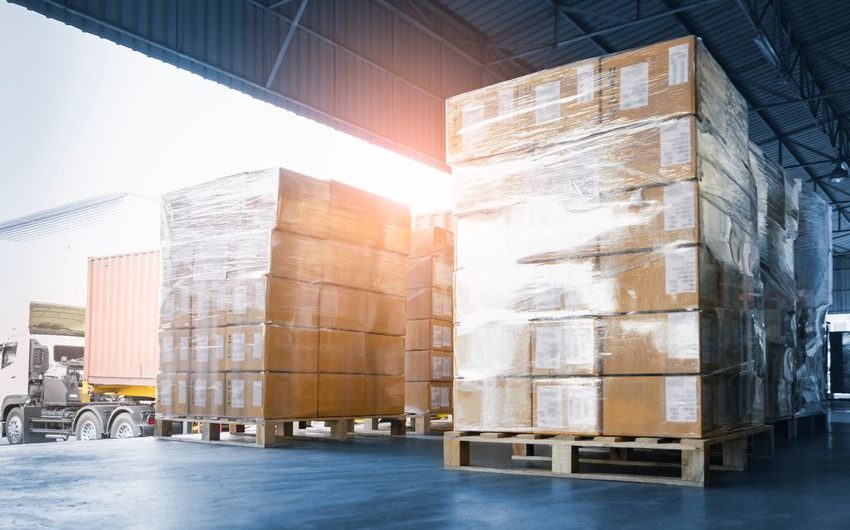
Scott Logistics Corp. and Quaker Transportation are two of the best companies in the region to get you started. Both are 3PLs, which is third-party logistics providers. They will give you the chance to experience what it's like working for a large company. You'll then be able decide which one is right for you. You wouldn't want a career that is lucrative because you don't know where you should look.
FAQ
What is production planning?
Production Planning includes planning for all aspects related to production. It is important to have everything ready and planned before you start shooting. It should also provide information about how best to produce the best results while on set. This information includes locations, crew details and equipment requirements.
It is important to first outline the type of film you would like to make. You might have an idea of where you want to film, or you may have specific locations or sets in mind. Once you have identified your locations and scenes, you can start working out which elements you require for each scene. One example is if you are unsure of the exact model you want but decide that you require a car. You could look online for cars to see what options are available, and then narrow down your choices by selecting between different makes or models.
After you have selected the car you want, you can begin to think about additional features. Are you looking for people to sit in the front seats? Or maybe you just need someone to push the car around. Maybe you'd like to change the interior from black to a white color. These questions will help to determine the style and feel of your car. Also, think about what kind of shots you would like to capture. What type of shots will you choose? Maybe you want to show the engine and the steering wheel. These things will help you to identify the car that you are looking for.
Once you've determined the above, it is time to start creating a calendar. The schedule will show you when to begin shooting and when to stop. Each day will include the time when you need to arrive at the location, when you need to leave and when you need to return home. Everyone knows exactly what they should do and when. If you need to hire extra staff, you can make sure you book them in advance. There is no point in hiring someone who won't turn up because you didn't let him know.
You will need to factor in the days that you have to film when creating your schedule. Some projects can be completed in a matter of days or weeks. Others may take several days. While creating your schedule, it is important to remember whether you will require more than one shot per day. Shooting multiple takes over the same location will increase costs and take longer to complete. It's better to be safe than sorry and shoot less takes if you're not certain whether you need more takes.
Budget setting is another important aspect in production planning. As it will allow you and your team to work within your financial means, setting a realistic budget is crucial. You can always lower the budget if you encounter unexpected problems. However, you shouldn't overestimate the amount of money you will spend. You'll end up with less money after paying for other things if the cost is underestimated.
Production planning can be a complex process. However, once you know how everything works together it will become easier to plan future projects.
What are the responsibilities of a manufacturing manager
A manufacturing manager has to ensure that all manufacturing processes work efficiently and effectively. They should also be aware and responsive to any company problems.
They should also be able communicate with other departments, such as sales or marketing.
They should also be knowledgeable about the latest trends in the industry so they can use this information for productivity and efficiency improvements.
What can I do to learn more about manufacturing?
You can learn the most about manufacturing by getting involved in it. However, if that's not possible, you can always read books or watch educational videos.
What does it take to run a logistics business?
To be a successful businessman in logistics, you will need many skills and knowledge. Effective communication skills are necessary to work with suppliers and clients. It is important to be able to analyse data and draw conclusions. You must be able to work well under pressure and handle stressful situations. You need to be innovative and creative to come up with new ways to increase efficiency. You need to have strong leadership qualities to motivate team members and direct them towards achieving organizational goals.
To meet tight deadlines, you must also be efficient and organized.
What are the four types of manufacturing?
Manufacturing is the process by which raw materials are transformed into useful products through machines and processes. Manufacturing can include many activities such as designing and building, testing, packaging shipping, selling, servicing, and other related activities.
What is the responsibility of a production planner?
A production planner makes sure all project elements are delivered on schedule, within budget, as well as within the agreed scope. They also ensure the quality of the product and service meets the client's requirements.
What do we need to know about Manufacturing Processes in order to learn more about Logistics?
No. You don't have to know about manufacturing processes before learning about logistics. It is important to know about the manufacturing processes in order to understand how logistics works.
Statistics
- It's estimated that 10.8% of the U.S. GDP in 2020 was contributed to manufacturing. (investopedia.com)
- In 2021, an estimated 12.1 million Americans work in the manufacturing sector.6 (investopedia.com)
- Job #1 is delivering the ordered product according to specifications: color, size, brand, and quantity. (netsuite.com)
- You can multiply the result by 100 to get the total percent of monthly overhead. (investopedia.com)
- According to a Statista study, U.S. businesses spent $1.63 trillion on logistics in 2019, moving goods from origin to end user through various supply chain network segments. (netsuite.com)
External Links
How To
Six Sigma in Manufacturing
Six Sigma can be described as "the use of statistical process control (SPC), techniques to achieve continuous improvement." Motorola's Quality Improvement Department, Tokyo, Japan, developed it in 1986. Six Sigma's main goal is to improve process quality by standardizing processes and eliminating defects. Many companies have adopted this method in recent years. They believe there is no such thing a perfect product or service. Six Sigma's main objective is to reduce variations from the production average. You can calculate the percentage of deviation from the norm by taking a sample of your product and comparing it to the average. If there is a significant deviation from the norm, you will know that something needs to change.
The first step toward implementing Six Sigma is understanding how variability works in your business. Once you understand that, it is time to identify the sources of variation. This will allow you to decide if these variations are random and systematic. Random variations occur when people make mistakes; systematic ones are caused by factors outside the process itself. These are, for instance, random variations that occur when widgets are made and some fall off the production line. But if you notice that every widget you make falls apart at the exact same place each time, this would indicate that there is a problem.
Once you've identified the problem areas you need to find solutions. That solution might involve changing the way you do things or redesigning the process altogether. After implementing the new changes, you should test them again to see if they worked. If they fail, you can go back to the drawing board to come up with a different plan.