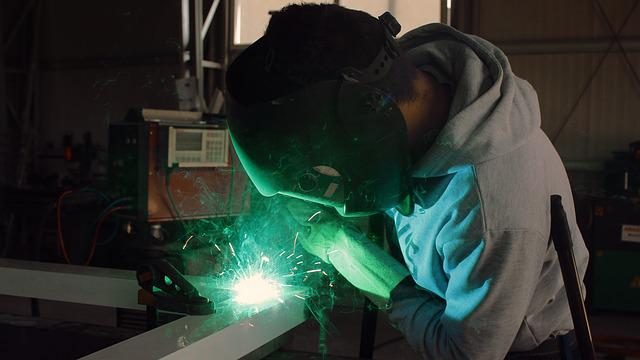
Complex adaptive systems are supply networks, which involve large numbers of companies participating in the delivery of products and services. A supply network is a collection of interrelated industries that provide raw materials, finished goods and other commodities. A supply system can serve more than its traditional function. It can also be used to manage digital flows or resources.
As supply networks evolve, they come in all shapes and sizes. It is essential to design a system which is resilient to unanticipated events. This involves understanding the various supply networks and how they can respond to disruptions. To address this problem, there are several options.
The flow of information is an important aspect of resilience assessment. It is a good place for you to start. It can also be used to assess the strength of a relationship. For example, if the first tier supplier is connected to the second tier supplier, the manufacturer may be able to detect missing links.
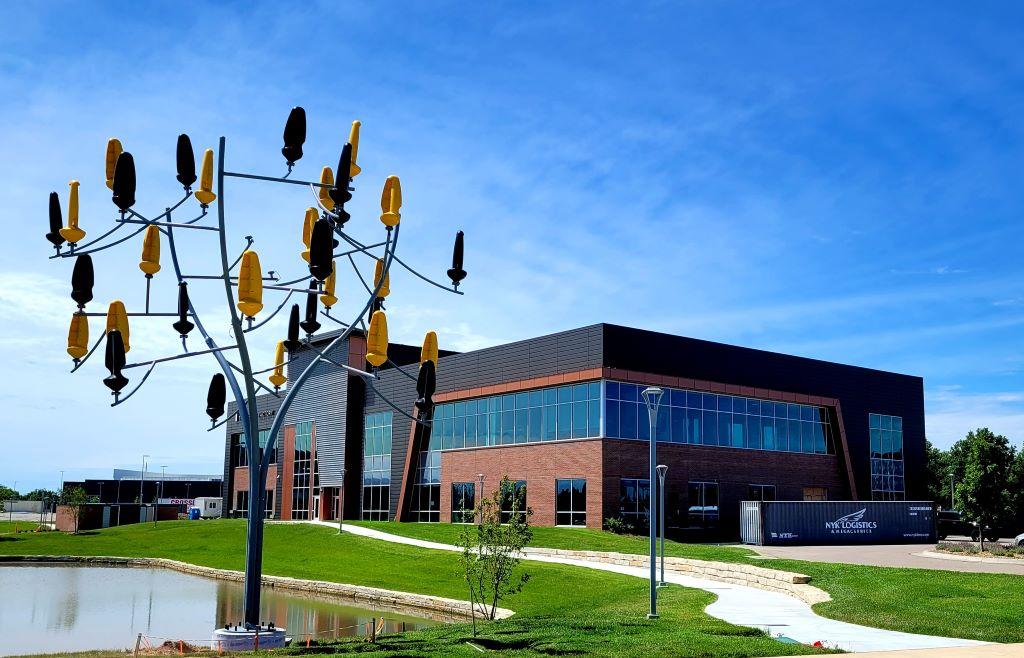
If a supply network allows this type of flow, it can add value to the end customer by delivering the desired product or service. But it's not as simple as it sounds to implement this intelligent approach in supply chain management. First, companies have to figure out a way of overcoming the limitations of existing networks. They must also ensure that their management of the flow information is robust enough to withstand disruptions.
Intermediaries are another important part of the supply chain. These are entities that are not fully understood about their roles in the supply network. For example, a semiconductor manufacturer moves work-in-process material from fabrication to assembly. The right method of moving materials can help manufacturers increase their production speed and efficiency. The same goes for a manufacturing firm that depends heavily on purchasing subcomponents from other businesses. This allows them to scale up or down according to their production needs.
Incorporating the various intermediaries into the supply network model can lead to unexpected results. Improved communication can result in increased productivity and efficiency, among other things. Moreover, developing strong partnerships can help an organisation improve its service to its customers.
Complexity upstream and downstream is a common characteristic of supply networks. This is due to the fact that suppliers must make decisions about which to buy and which to re-sell, while ensuring that the overall network is functional. As a result, power imbalances are quite common. These are easily managed by a few key strategies.
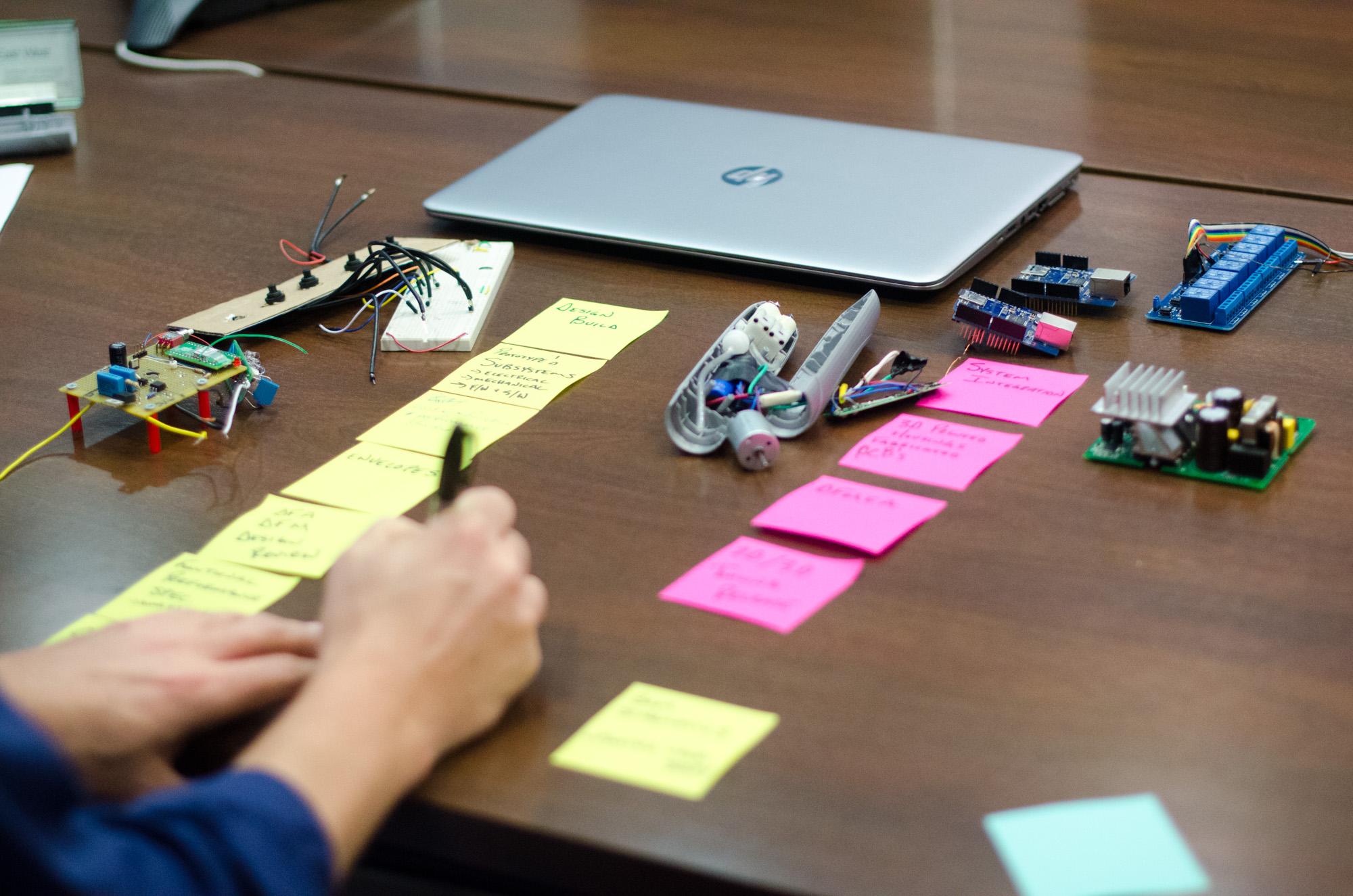
There are several ways to reduce this problem. One way is to set up a control tower that monitors and manages suppliers. Another way is to create a data center to analyse and gather data. A third option is to use an automated decision-making system. Others, which are more complicated measures of resilience, include a rebalancing to correct for imbalances as well as a buffer to protect network in the event of disruptions. Suppliers who are able predict and meet the clients' requirements may be better able than others to prevent a meltdown in their supply networks.
FAQ
What are the responsibilities of a production planner
Production planners ensure that all project aspects are completed on time, within budget and within the scope. They make sure that the product and services meet client expectations.
How can manufacturing prevent production bottlenecks?
You can avoid bottlenecks in production by making sure that everything runs smoothly throughout the production cycle, from the moment you receive an order to the moment the product is shipped.
This includes both planning for capacity and quality control.
Continuous improvement techniques like Six Sigma are the best way to achieve this.
Six Sigma can be used to improve the quality and decrease waste in all areas of your company.
It focuses on eliminating variation and creating consistency in your work.
What are the 7 Rs of logistics.
The acronym 7R's of Logistic is an acronym that stands for seven fundamental principles of logistics management. It was developed by the International Association of Business Logisticians (IABL) and published in 2004 as part of its "Seven Principles of Logistics Management" series.
The acronym consists of the following letters:
-
Responsive - ensure all actions are legal and not harmful to others.
-
Reliable - You can have confidence that you will fulfill your promises.
-
Be responsible - Use resources efficiently and avoid wasting them.
-
Realistic – consider all aspects of operations, from cost-effectiveness to environmental impact.
-
Respectful - treat people fairly and equitably.
-
Be resourceful: Look for opportunities to save money or increase productivity.
-
Recognizable provides value-added products and services to customers
Is it possible to automate certain parts of manufacturing
Yes! Yes! Automation has existed since ancient times. The Egyptians invented the wheel thousands of years ago. Today, robots assist in the assembly of lines.
Robotics is used in many manufacturing processes today. These include:
-
Automation line robots
-
Robot welding
-
Robot painting
-
Robotics inspection
-
Robots that create products
Manufacturing can also be automated in many other ways. For example, 3D printing allows us to make custom products without having to wait for weeks or months to get them manufactured.
What is production planning?
Production Planning involves developing a plan for all aspects of the production, including scheduling, budgeting, casting, crew, location, equipment, props, etc. This document aims to ensure that everything is planned and ready when you are ready to shoot. You should also have information to ensure the best possible results on set. This includes shooting schedules, locations, cast lists, crew details, and equipment requirements.
First, you need to plan what you want to film. You may have already chosen the location you want, or there are locations or sets you prefer. Once you've identified the locations and scenes you want to use, you can begin to plan what elements you need for each scene. If you decide you need a car and don't know what model to choose, this could be an example. If this is the case, you might start searching online for car models and then narrow your options by selecting from different makes.
After you have chosen the right car, you will be able to begin thinking about accessories. Do you have people who need to be seated in the front seat? You might also need someone to help you get around the back. You may want to change the interior's color from black or white. These questions will help guide you in determining the ideal look and feel for your car. It is also worth considering the types of shots that you wish to take. Are you going to be shooting close-ups? Or wide angles? Maybe you want to show your engine or the steering wheel. These factors will help you determine which car style you want to film.
Once you have established all the details, you can create a schedule. You can create a schedule that will outline when you must start and finish your shoots. The schedule will show you when to get there, what time to leave, and when to return home. Everyone will know what they need and when. Hire extra staff by booking them ahead of time. There is no point in hiring someone who won't turn up because you didn't let him know.
You will need to factor in the days that you have to film when creating your schedule. Some projects may only take a couple of days, while others could last for weeks. It is important to consider whether you require more than one photo per day when you create your schedule. Multiplying takes in the same area will result both in increased costs and a longer time. It is better to be cautious and take fewer shots than you risk losing money if you are not sure if multiple takes are necessary.
Budgeting is another crucial aspect of production plan. You will be able to manage your resources if you have a realistic budget. Remember that you can always reduce the budget later on if you run into unforeseen problems. You shouldn't underestimate the amount you'll spend. If you underestimate the cost of something, you will have less money left after paying for other items.
Production planning is a detailed process. But, once you understand the workings of everything, it becomes easier for future projects to be planned.
What is the responsibility of a manufacturing manager?
A manufacturing manager must ensure that all manufacturing processes are efficient and effective. They should be aware of any issues within the company and respond accordingly.
They should also be able communicate with other departments, such as sales or marketing.
They should also be aware of the latest trends in their industry and be able to use this information to help improve productivity and efficiency.
What is the importance of automation in manufacturing?
Not only is automation important for manufacturers, but it's also vital for service providers. It allows them provide faster and more efficient services. It helps them to lower costs by reducing human errors, and improving productivity.
Statistics
- Job #1 is delivering the ordered product according to specifications: color, size, brand, and quantity. (netsuite.com)
- Many factories witnessed a 30% increase in output due to the shift to electric motors. (en.wikipedia.org)
- It's estimated that 10.8% of the U.S. GDP in 2020 was contributed to manufacturing. (investopedia.com)
- [54][55] These are the top 50 countries by the total value of manufacturing output in US dollars for its noted year according to World Bank.[56] (en.wikipedia.org)
- In 2021, an estimated 12.1 million Americans work in the manufacturing sector.6 (investopedia.com)
External Links
How To
Six Sigma and Manufacturing
Six Sigma is "the application statistical process control (SPC), techniques for continuous improvement." Motorola's Quality Improvement Department developed it at their Tokyo plant in Japan in 1986. Six Sigma's main goal is to improve process quality by standardizing processes and eliminating defects. This method has been adopted by many companies in recent years as they believe there are no perfect products or services. Six Sigma's main objective is to reduce variations from the production average. You can calculate the percentage of deviation from the norm by taking a sample of your product and comparing it to the average. If it is too large, it means that there are problems.
Understanding how variability works in your company is the first step to Six Sigma. Once you've understood that, you'll want to identify sources of variation. This will allow you to decide if these variations are random and systematic. Random variations happen when people make errors; systematic variations are caused externally. Random variations would include, for example, the failure of some widgets to fall from the assembly line. But if you notice that every widget you make falls apart at the exact same place each time, this would indicate that there is a problem.
Once you've identified the problem areas you need to find solutions. This could mean changing your approach or redesigning the entire process. To verify that the changes have worked, you need to test them again. If they didn't work, then you'll need to go back to the drawing board and come up with another plan.