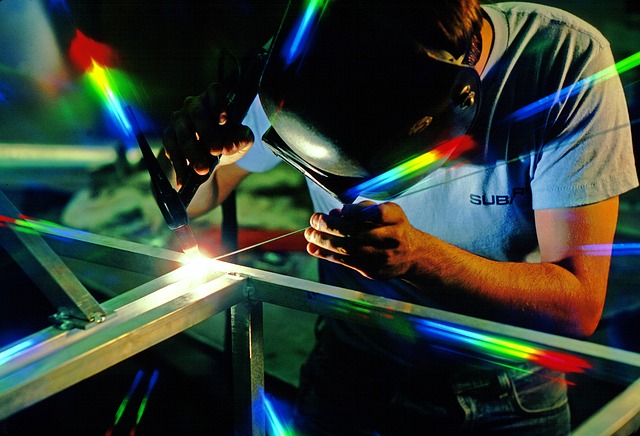
Industrial engineering technicians apply their mathematical and engineering knowledge to improve the efficiency of a business. This includes the development of blueprints for machinery and the analysis of statistical data. A skilled industrial engineer can assist management in making decisions that will improve the company's efficiency.
The typical duties of an industrial engineer technician are to: perform time- and motion studies in order to increase productivity; evaluate performance and implement changes. They may also be needed to analyze data that is part of an industrial health or safety program.
Additionally, they are responsible for technical tasks like preparing diagrams and graphs to show the flow of a process. They also perform numerous quality tests on products to ensure they conform to standards.
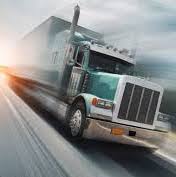
An industrial engineer's most common job duties include planning workflow, analyzing production costs and gauging prototypes. They also assess equipment capacities and develop efficient operating procedures. There are many industries where they can be found, including aerospace and electronics, pharmaceuticals, electronic, food, and automotive. Most work full-time. Their average salary is $53,000 a year, but those with more education or experience may be able to earn a higher salary.
There are no specific degrees required to become an industrial engineer. It is important to have strong math skills and a keen eye for detail. They need to be able speak with employees and be able observe and understand the work processes in a workplace.
A skilled industrial engineer technician will recognize and be able to implement the necessary factors in the most effective workflow. They should be able see the importance in reducing waste and practices. They can then find ways to improve their workplace and save money.
They are also likely to be the first people in their organization to try out new ideas. One of the most common ways to do this is through a strategic outline. It's like putting together the pieces in a large puzzle.
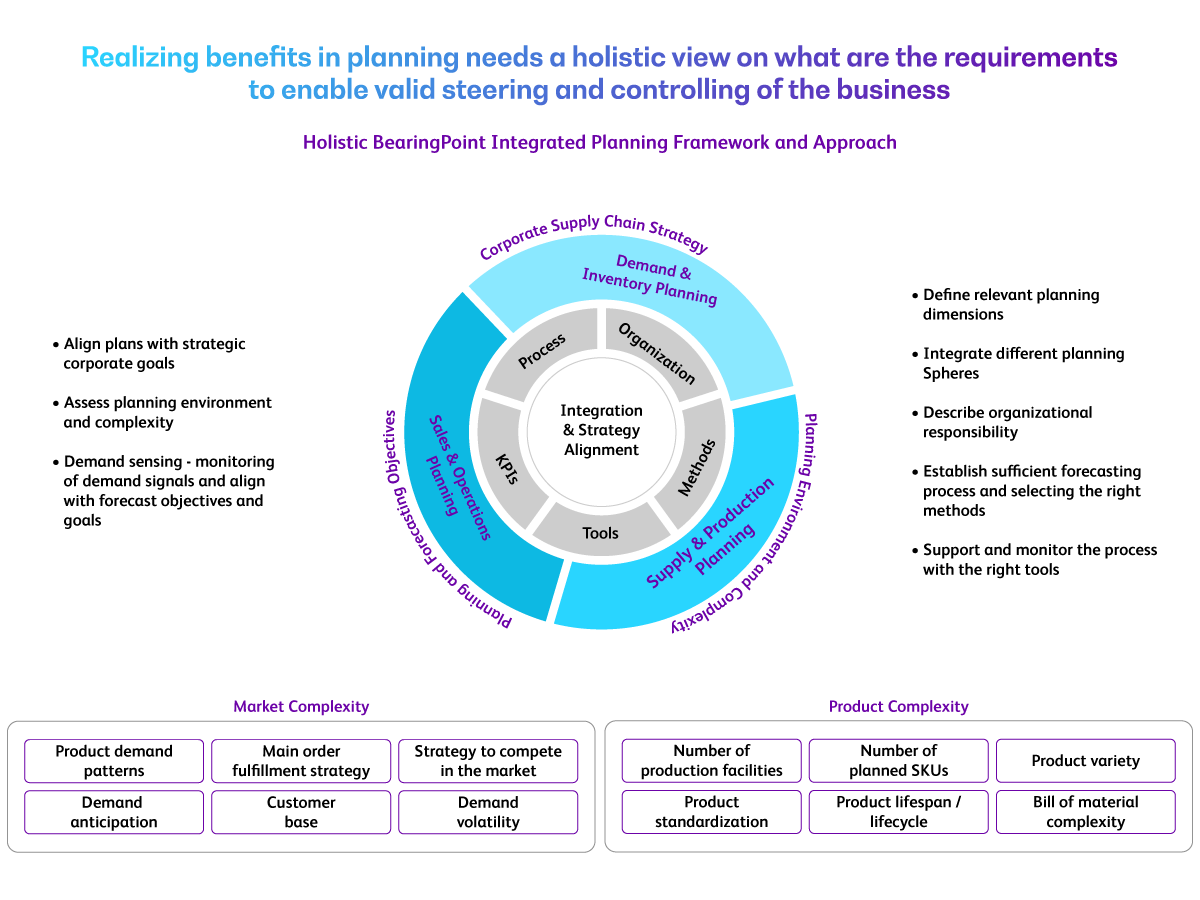
A second important job function for an industrial engineer is to improve the quality and quantity of the product. The automation of more industries will reduce the number jobs but it will not stop the growth of industrial engineering technicians.
When it comes to the best way to measure the performance of a system, an engineer might choose to conduct a time and motion study to determine how long it takes to complete a task. To calculate a standard rate of production, they might use the data from this study. These results will then be used to make improvements to the way an operation is run.
Many universities, including Liberty University offer an industrial engineering program that offers students a range of courses. They include basic machinist skills as well as motor controls, hydraulics, self-management, and hydraulics. This program teaches students how to solve problems and work in teams to reach their goals.
FAQ
What can I do to learn more about manufacturing?
You can learn the most about manufacturing by getting involved in it. However, if that's not possible, you can always read books or watch educational videos.
What do we need to know about Manufacturing Processes in order to learn more about Logistics?
No. It doesn't matter if you don't know anything about manufacturing before you learn about logistics. Knowing about manufacturing processes will help you understand how logistics works.
What does warehouse refer to?
A warehouse is a place where goods are stored until they are sold. It can be either an indoor or outdoor space. Sometimes, it can be both an indoor and outdoor space.
Statistics
- You can multiply the result by 100 to get the total percent of monthly overhead. (investopedia.com)
- Job #1 is delivering the ordered product according to specifications: color, size, brand, and quantity. (netsuite.com)
- Many factories witnessed a 30% increase in output due to the shift to electric motors. (en.wikipedia.org)
- (2:04) MTO is a production technique wherein products are customized according to customer specifications, and production only starts after an order is received. (oracle.com)
- It's estimated that 10.8% of the U.S. GDP in 2020 was contributed to manufacturing. (investopedia.com)
External Links
How To
How to use lean manufacturing in the production of goods
Lean manufacturing is an approach to management that aims for efficiency and waste reduction. It was first developed in Japan in the 1970s/80s by Taiichi Ahno, who was awarded the Toyota Production System (TPS), award from KanjiToyoda, the founder of TPS. The first book published on lean manufacturing was titled "The Machine That Changed the World" written by Michael L. Watkins and published in 1990.
Lean manufacturing, often described as a set and practice of principles, is aimed at improving the quality, speed, cost, and efficiency of products, services, and other activities. It emphasizes the elimination and minimization of waste in the value stream. Just-in-time (JIT), zero defect (TPM), and 5S are all examples of lean manufacturing. Lean manufacturing seeks to eliminate non-value added activities, such as inspection, work, waiting, and rework.
Lean manufacturing improves product quality and costs. It also helps companies reach their goals quicker and decreases employee turnover. Lean manufacturing is considered one of the most effective ways to manage the entire value chain, including suppliers, customers, distributors, retailers, and employees. Lean manufacturing practices are widespread in many industries. Toyota's philosophy, for example, is what has enabled it to be successful in electronics, automobiles, medical devices, healthcare and chemical engineering as well as paper and food.
Lean manufacturing includes five basic principles:
-
Define Value - Identify the value your business adds to society and what makes you different from competitors.
-
Reduce Waste - Eliminate any activity that doesn't add value along the supply chain.
-
Create Flow: Ensure that the work process flows without interruptions.
-
Standardize & Simplify - Make processes as consistent and repeatable as possible.
-
Building Relationships – Establish personal relationships with both external and internal stakeholders.
Lean manufacturing is not a new concept, but it has been gaining popularity over the last few years due to a renewed interest in the economy following the global financial crisis of 2008. Many businesses have adopted lean production techniques to make them more competitive. Some economists even believe that lean manufacturing can be a key factor in economic recovery.
Lean manufacturing is now becoming a common practice in the automotive industry, with many benefits. These include higher customer satisfaction, lower inventory levels, lower operating expenses, greater productivity, and improved overall safety.
Any aspect of an enterprise can benefit from Lean manufacturing. It is especially useful for the production aspect of an organization, as it ensures that every step in the value chain is efficient and effective.
There are three types principally of lean manufacturing:
-
Just-in-Time Manufacturing (JIT): This type of lean manufacturing is commonly referred to as "pull systems." JIT means that components are assembled at the time of use and not manufactured in advance. This approach is designed to reduce lead times and increase the availability of components. It also reduces inventory.
-
Zero Defects Manufacturing, (ZDM): ZDM is focused on ensuring that no defective products leave the manufacturing facility. You should repair any part that needs to be repaired during an assembly line. This is true even for finished products that only require minor repairs prior to shipping.
-
Continuous Improvement: Continuous Improvement aims to improve efficiency by continually identifying problems and making adjustments to eliminate or minimize waste. Continuous improvement involves continuous improvement of processes and people as well as tools.