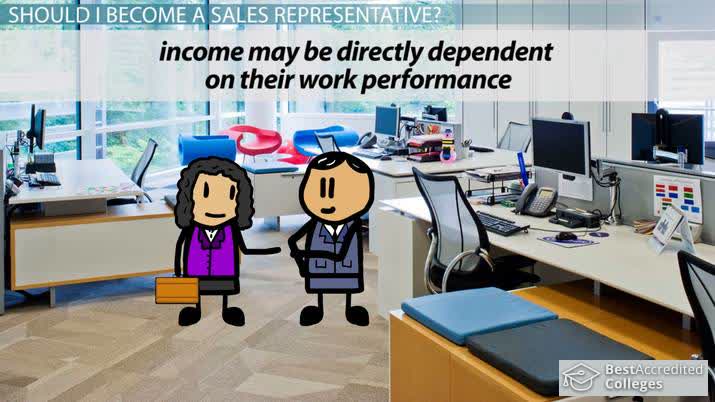
The SCOR Model is a reference process model, developed by Supply Chain Council. This model is widely used across industries. It helps businesses better understand business processes, operational performance and goals. It allows companies to identify areas of improvement, and compare their performance against that of their competitors.
The model is divided into three major segments: process modeling, performance measurements and supply chain best practices. The first part of the model focuses primarily on planning, procurement, production and delivery. It also includes product return handling and market interactions.
This section of the model provides you with more than 150 Key Performance Indicators (KPIs), which can be used to measure your operation's success. As an example, you could evaluate the delivery performance from your suppliers to determine if they deliver quality products for a reasonable rate.
Also, you can look at customer returns and determine how much money you could save by having your suppliers reduce their return rates to 20 percent. This will help you to identify areas where your processes could be improved in order to save you money.
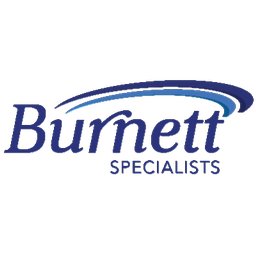
The SCOR model can be confusing to those who are unfamiliar with it. The main goal of the SCOR model to help create an efficient, standardized supply chain management system.
The system breaks down the supply chain into ideal processes and then categorizes them based on their value to your business. The system makes it simple to compare and co-ordinate different supply chains activities within and across your industry.
The second part of the model is the performance measurements. These metrics can be used to evaluate your supply-chain operations. These metrics can be used to evaluate a variety of performance areas, including inventory management, transportation costs, supplier quality, and customer service.
Using performance measurement data, you can find out where your company stands in these areas and create action items to improve the operations. It is important to note that these measures are only useful if you take the time to do something about them.
You will first need to create a list with current KPIs you can monitor. After that, you can start reviewing each of these KPIs monthly to see what your company's performance is in each category.
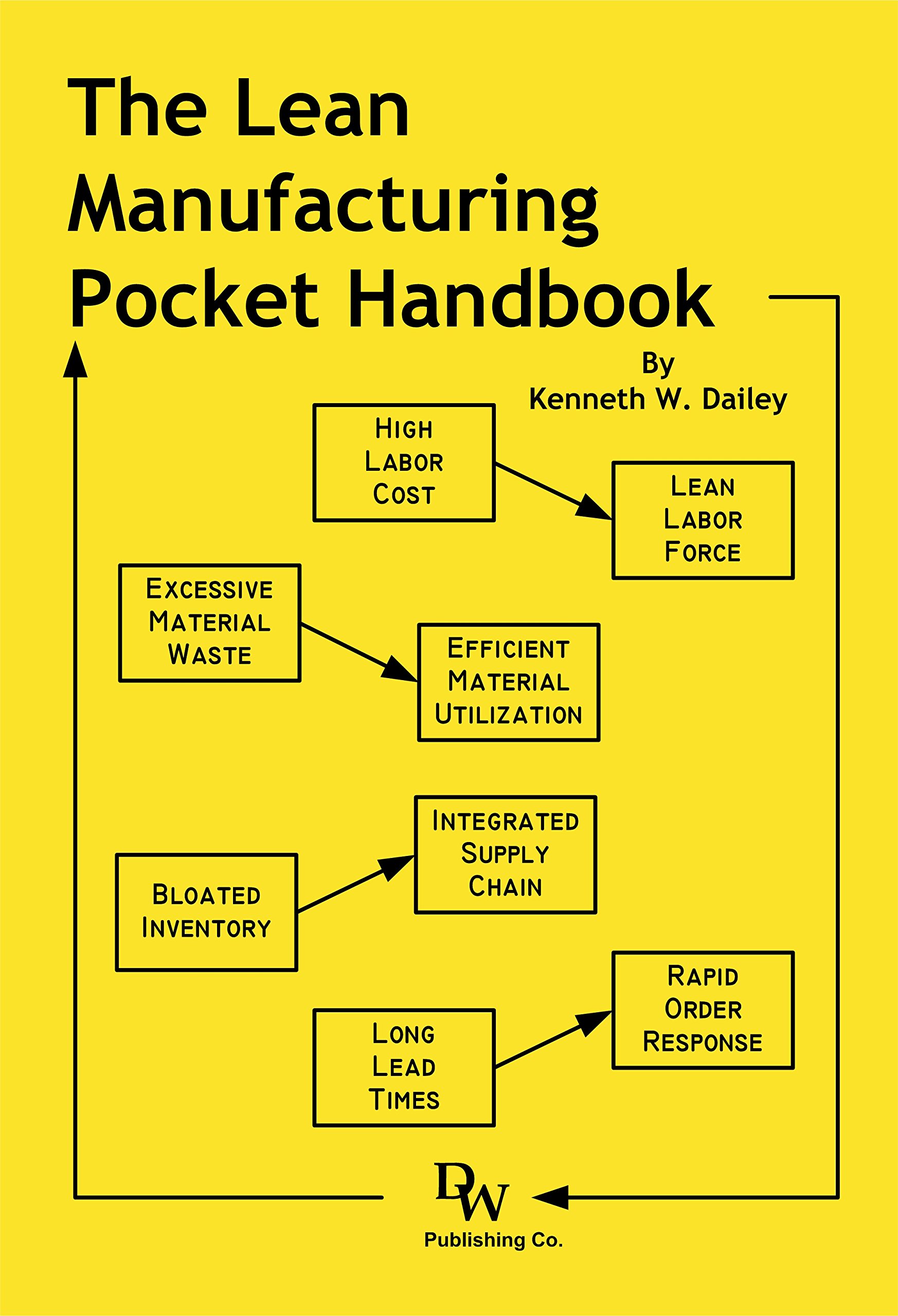
It is time to think about new business processes your company could implement that would help improve its operation and increase profits. Then, you can compare the new processes to those of your current operations to ensure that they are efficient.
This is the perfect way to get your entire team started on improving your company's operations. In addition, the SCOR model provides an opportunity for companies to collaborate with their suppliers and customers by sharing a common language and framework for measuring and analyzing supply chain performance.
FAQ
What are the responsibilities of a logistic manager?
Logistics managers ensure that goods arrive on time and are unharmed. This is done using his/her knowledge of the company's products. He/she must also ensure sufficient stock to meet the demand.
What are the jobs in logistics?
There are many kinds of jobs available within logistics. Some examples are:
-
Warehouse workers - They load and unload trucks and pallets.
-
Transportation drivers – These drivers drive trucks and wagons to transport goods and pick up the goods.
-
Freight handlers are people who sort and pack freight into warehouses.
-
Inventory managers: They are responsible for the inventory and management of warehouses.
-
Sales representatives - They sell products.
-
Logistics coordinators - They plan and organize logistics operations.
-
Purchasing agents - They purchase goods and services needed for company operations.
-
Customer service agents - They answer phone calls and respond to emails.
-
Shippers clerks - They process shipping order and issue bills.
-
Order fillers - They fill orders based on what is ordered and shipped.
-
Quality control inspectors - They check incoming and outgoing products for defects.
-
Others - There are many types of jobs in logistics such as transport supervisors and cargo specialists.
Why is logistics important for manufacturing?
Logistics is an integral part of every business. They help you achieve great results by helping you manage all aspects of product flow, from raw materials to finished goods.
Logistics also play a major role in reducing costs and increasing efficiency.
What makes a production planner different from a project manger?
The major difference between a Production Planner and a Project Manager is that a Project Manager is often the person responsible for organizing and planning the entire project. While a Production Planner is involved mainly in the planning stage,
What does manufacturing industry mean?
Manufacturing Industries refers to businesses that manufacture products. Consumers are those who purchase these products. To accomplish this goal, these companies employ a range of processes including distribution, sales, management, and production. These companies produce goods using raw materials and other equipment. This includes all types manufactured goods such as clothing, building materials, furniture, electronics, tools and machinery.
Statistics
- (2:04) MTO is a production technique wherein products are customized according to customer specifications, and production only starts after an order is received. (oracle.com)
- In the United States, for example, manufacturing makes up 15% of the economic output. (twi-global.com)
- Job #1 is delivering the ordered product according to specifications: color, size, brand, and quantity. (netsuite.com)
- Many factories witnessed a 30% increase in output due to the shift to electric motors. (en.wikipedia.org)
- [54][55] These are the top 50 countries by the total value of manufacturing output in US dollars for its noted year according to World Bank.[56] (en.wikipedia.org)
External Links
How To
How to use lean manufacturing in the production of goods
Lean manufacturing refers to a method of managing that seeks to improve efficiency and decrease waste. It was created in Japan by Taiichi Ohno during the 1970s and 80s. He received the Toyota Production System award (TPS), from Kanji Toyoda, founder of TPS. Michael L. Watkins published the original book on lean manufacturing, "The Machine That Changed the World," in 1990.
Lean manufacturing can be described as a set or principles that are used to improve quality, speed and cost of products or services. It emphasizes the elimination of defects and waste throughout the value stream. Just-in-time (JIT), zero defect (TPM), and 5S are all examples of lean manufacturing. Lean manufacturing is about eliminating activities that do not add value, such as inspection, rework, and waiting.
Lean manufacturing can help companies improve their product quality and reduce costs. Additionally, it helps them achieve their goals more quickly and reduces employee turnover. Lean manufacturing has been deemed one of the best ways to manage the entire value-chain, including customers, distributors as well retailers and employees. Lean manufacturing can be found in many industries. Toyota's philosophy, for example, is what has enabled it to be successful in electronics, automobiles, medical devices, healthcare and chemical engineering as well as paper and food.
Five principles are the basis of lean manufacturing:
-
Define Value - Identify the value your business adds to society and what makes you different from competitors.
-
Reduce Waste - Remove any activity which doesn't add value to your supply chain.
-
Create Flow: Ensure that the work process flows without interruptions.
-
Standardize & simplify - Make processes consistent and repeatable.
-
Build relationships - Develop and maintain personal relationships with both your internal and external stakeholders.
Lean manufacturing is not a new concept, but it has been gaining popularity over the last few years due to a renewed interest in the economy following the global financial crisis of 2008. Many companies have adopted lean manufacturing methods to increase their marketability. Some economists even believe that lean manufacturing can be a key factor in economic recovery.
Lean manufacturing has many benefits in the automotive sector. These include improved customer satisfaction, reduced inventory levels, lower operating costs, increased productivity, and better overall safety.
It can be applied to any aspect of an organisation. Because it makes sure that all value chains are efficient and effectively managed, Lean Manufacturing is particularly helpful for organizations.
There are three types of lean manufacturing.
-
Just-in Time Manufacturing: This lean manufacturing method is commonly called "pull systems." JIT refers to a system in which components are assembled at the point of use instead of being produced ahead of time. This method reduces lead times, increases availability, and decreases inventory.
-
Zero Defects Manufacturing - ZDM: ZDM focuses its efforts on making sure that no defective units leave a manufacturing facility. You should repair any part that needs to be repaired during an assembly line. This is true even for finished products that only require minor repairs prior to shipping.
-
Continuous Improvement (CI), also known as Continuous Improvement, aims at improving the efficiency of operations through continuous identification and improvement to minimize or eliminate waste. It involves continuous improvement of processes, people, and tools.