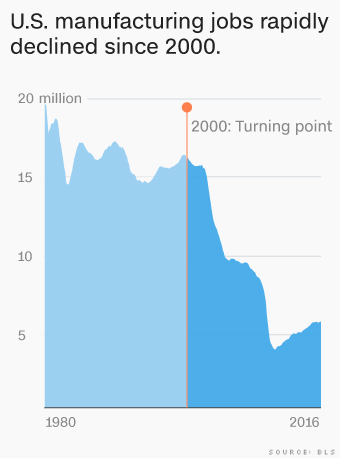
The director of manufacturing oversees the company's production process. They play a vital role in overseeing the manufacturing process from design through production. For this job, you must have a great deal of manufacturing experience and be familiar with all new technologies. These technologies include 3D printing and robotics. The director who is up-to-date with these technologies will be a valuable asset to the company. The director's role in the manufacturing industry will change as it evolves. He or she will need to work closely with engineering and operations, as well as placing greater emphasis on quality control in the manufacturing plant.
Salary for a director of manufacturing
The salary of a Director of Manufacturing can vary depending on where they are located. Director of Manufacturing salaries can range from low to mid-six figures. However, some directors earn considerably more than others. The salary of a Director of Manufacturing may also vary significantly based on years of experience and education. Consider these factors when determining how much you will earn in your local area.
Although the salary for a Director of Manufacturing can vary depending on your experience, the average salary is higher. The cost of living and the location can also impact salary. Living in a big city will result in higher salaries. But, be aware that your salary might not reflect the cost of living. You should always be prepared to negotiate to get a higher salary if the opportunity arises.
A Director of Manufacturing Operations can earn between $181 500 and $66,000 annually. The salary for a director of manufacturing operations is variable. It can vary up to 8% from one city to the next. The average salary for a director of manufacturing operations in Fremont is $128,493 to $164,500. This is significantly higher than the national average. The salary for a Director, Manufacturing Operations is dependent on where the job is located, what experience the person has, and the company.
Education required
The director for manufacturing is responsible in managing a manufacturing plant and supervising the production process. This position includes the hiring of new employees, quality assurance oversight, collaboration with designers, and ensuring that operations standards are met. A director of manufacturing typically reports to the senior management team and executes policy and sales initiatives. Candidates must have experience in manufacturing and communicate well. There are different educational requirements to become a director in manufacturing.
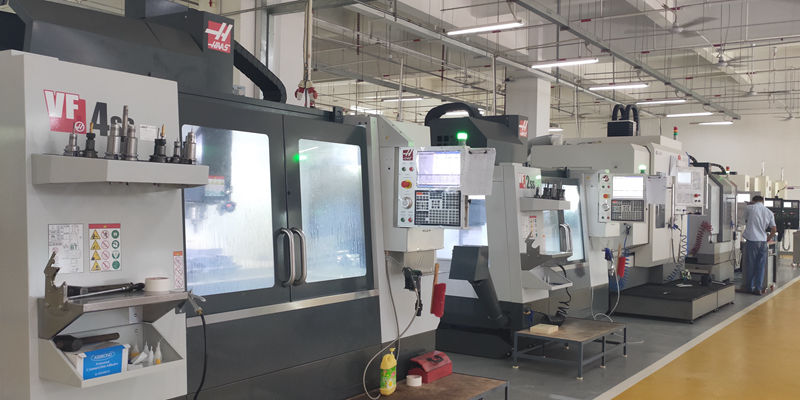
Although a graduate degree in engineering is not always required for director of manufacturing jobs, a post-secondary education in a related field will greatly enhance your skill set and knowledge base. An MBA program in industrial management or business administration is a great choice for this position, as it helps candidates to learn about management, economics, and organization. You will ultimately be responsible for managing diverse groups of people.
You will collaborate closely with engineers and designers as a director for manufacturing during the product development phase. You will participate in the evaluation of new processes and setting quality standards before investing resources into larger productions. As well as overseeing production, directors can also serve as coaches to employees. They will guide them in risk mitigation and best practice. They will also mentor them on best practices and risk mitigation.
Experience required
This position often requires a bachelor's degree in a relevant area and five to ten years of progressive work experience. For this job, most manufacturing companies prefer to use their own employees. The ideal candidate should have a solid understanding of the manufacturing process as well as business objectives. Employers may require a graduate degree. Candidates may also need additional training in the chosen industry or field.
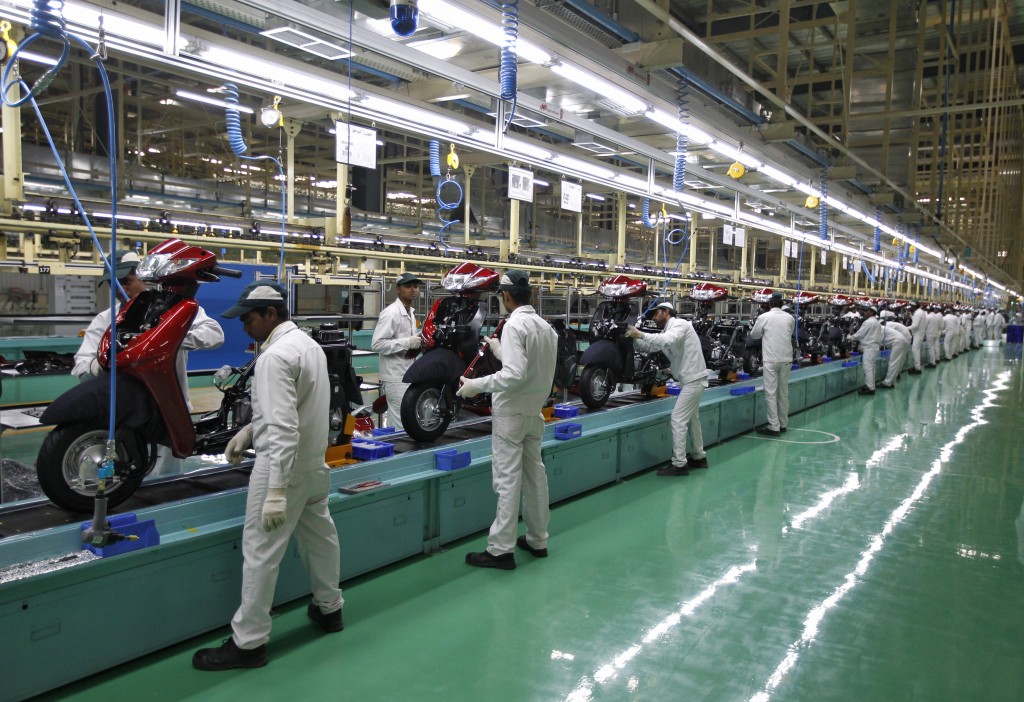
The production process is overseen by a director of manufacturing, which includes engineers, supervisors, workers, and other personnel. They may be responsible solving problems or finding a solution. A director of manufacturing may not only oversee production but also develop and implement quality-control programs. The manufacturing director reports directly to the chief executive of the organization. Experience in manufacturing is essential. If you are looking to succeed in the manufacturing management position, it is important that you have some experience.
Experience as a manufacturing director will be an asset. Directors must have at least 10 years of relevant experience in a manufacturing environment. These individuals may have had previous experience as managers or technicians. They should also possess strong communication skills. The director of manufacturing must also be able to understand business strategy. The director of manufacturing should also be able work well with other departments in the company. In this capacity, the director oversees the production process and ensures that it meets the highest quality standards.
FAQ
Why automate your warehouse
Modern warehouses have become more dependent on automation. Increased demand for efficient and faster delivery has resulted in a rise in e-commerce.
Warehouses have to be flexible to meet changing requirements. To do so, they must invest heavily in technology. Automation warehouses can bring many benefits. Here are some benefits of investing in automation
-
Increases throughput/productivity
-
Reduces errors
-
Increases accuracy
-
Boosts safety
-
Eliminates bottlenecks
-
Allows companies scale more easily
-
It makes workers more efficient
-
The warehouse can be viewed from all angles.
-
Enhances customer experience
-
Improves employee satisfaction
-
Reducing downtime and increasing uptime
-
Quality products delivered on time
-
Eliminates human error
-
This helps to ensure compliance with regulations
What do we need to know about Manufacturing Processes in order to learn more about Logistics?
No. It doesn't matter if you don't know anything about manufacturing before you learn about logistics. However, knowing about manufacturing processes will definitely give you a better understanding of how logistics works.
How can manufacturing avoid production bottlenecks
You can avoid bottlenecks in production by making sure that everything runs smoothly throughout the production cycle, from the moment you receive an order to the moment the product is shipped.
This includes planning for both capacity requirements and quality control measures.
This can be done by using continuous improvement techniques, such as Six Sigma.
Six Sigma Management System is a method to increase quality and reduce waste throughout your organization.
It emphasizes consistency and eliminating variance in your work.
What does warehouse refer to?
A warehouse, or storage facility, is where goods are stored prior to being sold. It can be an outdoor or indoor area. In some cases it could be both indoors and outdoors.
What can I do to learn more about manufacturing?
Hands-on experience is the best way to learn more about manufacturing. However, if that's not possible, you can always read books or watch educational videos.
What are manufacturing & logistics?
Manufacturing is the process of creating goods from raw materials by using machines and processes. Logistics is the management of all aspects of supply chain activities, including procurement, production planning, distribution, warehousing, inventory control, transportation, and customer service. Manufacturing and logistics can often be grouped together to describe a larger term that covers both the creation of products, and the delivery of them to customers.
Statistics
- According to the United Nations Industrial Development Organization (UNIDO), China is the top manufacturer worldwide by 2019 output, producing 28.7% of the total global manufacturing output, followed by the United States, Japan, Germany, and India.[52][53] (en.wikipedia.org)
- According to a Statista study, U.S. businesses spent $1.63 trillion on logistics in 2019, moving goods from origin to end user through various supply chain network segments. (netsuite.com)
- You can multiply the result by 100 to get the total percent of monthly overhead. (investopedia.com)
- It's estimated that 10.8% of the U.S. GDP in 2020 was contributed to manufacturing. (investopedia.com)
- Many factories witnessed a 30% increase in output due to the shift to electric motors. (en.wikipedia.org)
External Links
How To
Six Sigma: How to Use it in Manufacturing
Six Sigma is "the application statistical process control (SPC), techniques for continuous improvement." Motorola's Quality Improvement Department created Six Sigma at their Tokyo plant, Japan in 1986. Six Sigma is a method to improve quality through standardization and elimination of defects. Since there are no perfect products, or services, this approach has been adopted by many companies over the years. Six Sigma seeks to reduce variation between the mean production value. This means that if you take a sample of your product, then measure its performance against the average, you can find out what percentage of the time the process deviates from the norm. If you notice a large deviation, then it is time to fix it.
Understanding the nature of variability in your business is the first step to Six Sigma. Once you understand that, it is time to identify the sources of variation. This will allow you to decide if these variations are random and systematic. Random variations occur when people do mistakes. Symmetrical variations are caused due to factors beyond the process. If you make widgets and some of them end up on the assembly line, then those are considered random variations. You might notice that your widgets always fall apart at the same place every time you put them together.
Once you identify the problem areas, it is time to create solutions. It might mean changing the way you do business or redesigning it entirely. After implementing the new changes, you should test them again to see if they worked. If they don't work you need to rework them and come up a better plan.