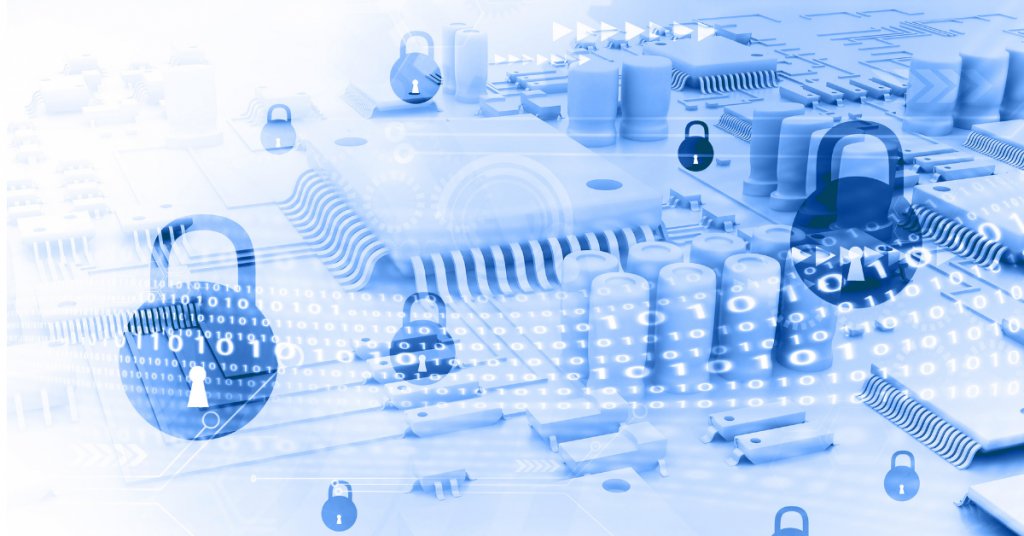
You need to be familiar with the five s's to make your manufacturing process a lean machine. They are Standardize. Straighten. Shine. and Sustain. Here are some steps you should follow. Your lean transformation will be maximized if you train your frontline employees and team leaders.
Standardize
Clean up and organize your workspace as the first step in the 5S Process. This may be a one-time job, but if you standardize the process, it can become a routine. You can use checklists, visual cues, and checklist templates to create a consistent approach to 5S tasks.
These five ss's of Lean can help make your workplace more productive. This will help your staff be more organized and perform their tasks in a more efficient manner. This will help improve your efficiency by organizing your work area. Safety in the workplace can also be improved by using the five s's. A well-organized workplace will reduce accidents and mistakes, increase productivity, and help you avoid them.
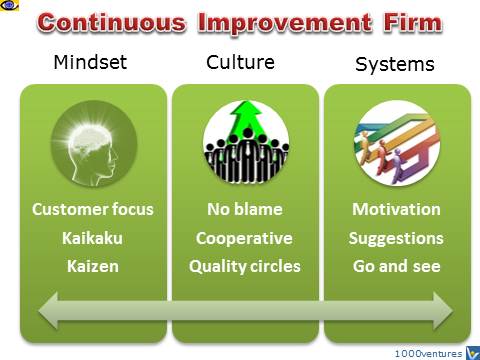
Straighten
It doesn't need to be hard to get your 5 s's in order. Companies can improve their business processes by applying lean principles in a systematic way. For example, by organizing the components of an assembly line, workers will be able to find the components they need more easily. This can help to reduce time spent searching misplaced parts and improve company safety.
Reducing the number and type of items in each workspace will help you save money. This will allow you to reduce your office supply costs. Straightening work cells not only helps you save money but it also increases the efficiency of your production process by improving quality, safety, and standard work.
Shine
The Shine step focuses on inspecting the workspace and identifying potential issues. Shine examines equipment and tools in order to improve flow. Shine can improve the maintenance of a workspace. It allows workers to spot potential problems before they hinder production. It helps increase output by standardizing the layout of a workspace.
Shine is one of the 5S tools used in lean manufacturing. This technique streamlines and automates work processes to reduce waste and increase efficiency. It can be used in all industries, including manufacturing. This applies the 5S principles throughout a company. It assists companies in reducing inventory, work-in progress, and stock.
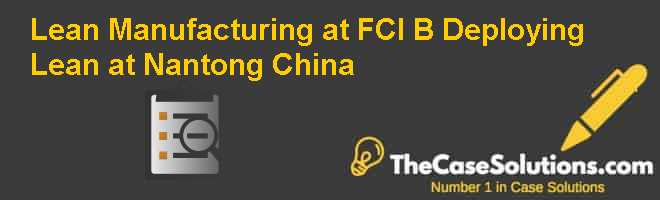
Be a good citizen
Sustaining the 5 s's of lean involves re-introducing a standardized system to a facility. This process is intended to be ongoing and should be repeated to ensure that the facility is functioning at its best. This is why employees need to be trained in 5S auditing.
The 5S Approach emphasizes reducing wasted time, optimizing productivity, as well as maintaining a clean, organized workplace. The 5S approach to organizing workplaces applies the five principles in the Toyota Production System. Hiroyuki Hirano developed it in Japan post-war to improve the efficiency of manufacturing facilities.
FAQ
What does manufacturing mean?
Manufacturing Industries is a group of businesses that produce goods for sale. Consumers are the people who purchase these products. These companies use a variety processes such as distribution, retailing and management to accomplish their purpose. They produce goods from raw materials by using machines and other machinery. This covers all types of manufactured goods including clothing, food, building supplies and furniture, as well as electronics, tools, machinery, vehicles and pharmaceuticals.
What are the 4 types of manufacturing?
Manufacturing refers the process of turning raw materials into useful products with machines and processes. Manufacturing involves many activities, including designing, building, testing and packaging, shipping, selling, service, and so on.
What is the best way to learn about manufacturing?
You can learn the most about manufacturing by getting involved in it. You can read books, or watch instructional videos if you don't have the opportunity to do so.
What is the difference in Production Planning and Scheduling, you ask?
Production Planning (PP) refers to the process of determining how much production is needed at any given moment. This is done through forecasting demand and identifying production capacities.
Scheduling is the process that assigns dates to tasks so they can get completed within a given timeframe.
What is the role of a manager in manufacturing?
Manufacturing managers must ensure that manufacturing processes are efficient, effective, and cost-effective. They should also be aware of any problems within the company and act accordingly.
They should also know how to communicate with other departments such as sales and marketing.
They must also keep up-to-date with the latest trends in their field and be able use this information to improve productivity and efficiency.
How can manufacturing efficiency be improved?
The first step is to determine the key factors that impact production time. The next step is to identify the most important factors that affect production time. You can start by identifying the most important factors that impact production time. Once you've identified them all, find solutions to each one.
Why is logistics important in manufacturing
Logistics is an integral part of every business. They enable you to achieve outstanding results by helping manage product flow from raw materials through to finished goods.
Logistics plays a significant role in reducing cost and increasing efficiency.
Statistics
- In 2021, an estimated 12.1 million Americans work in the manufacturing sector.6 (investopedia.com)
- Many factories witnessed a 30% increase in output due to the shift to electric motors. (en.wikipedia.org)
- [54][55] These are the top 50 countries by the total value of manufacturing output in US dollars for its noted year according to World Bank.[56] (en.wikipedia.org)
- It's estimated that 10.8% of the U.S. GDP in 2020 was contributed to manufacturing. (investopedia.com)
- According to a Statista study, U.S. businesses spent $1.63 trillion on logistics in 2019, moving goods from origin to end user through various supply chain network segments. (netsuite.com)
External Links
How To
Six Sigma in Manufacturing
Six Sigma refers to "the application and control of statistical processes (SPC) techniques in order to achieve continuous improvement." Motorola's Quality Improvement Department, Tokyo, Japan, developed it in 1986. Six Sigma's main goal is to improve process quality by standardizing processes and eliminating defects. Since there are no perfect products, or services, this approach has been adopted by many companies over the years. The main goal of Six Sigma is to reduce variation from the mean value of production. This means that you can take a sample from your product and then compare its performance to the average to find out how often the process differs from the norm. If the deviation is excessive, it's likely that something needs to be fixed.
The first step toward implementing Six Sigma is understanding how variability works in your business. Once you have a good understanding of the basics, you can identify potential sources of variation. It is important to identify whether the variations are random or systemic. Random variations occur when people make mistakes; systematic ones are caused by factors outside the process itself. If you make widgets and some of them end up on the assembly line, then those are considered random variations. However, if you notice that every time you assemble a widget, it always falls apart at exactly the same place, then that would be a systematic problem.
After identifying the problem areas, you will need to devise solutions. This could mean changing your approach or redesigning the entire process. You should then test the changes again after they have been implemented. If they don’t work, you’ll need to go back and rework the plan.