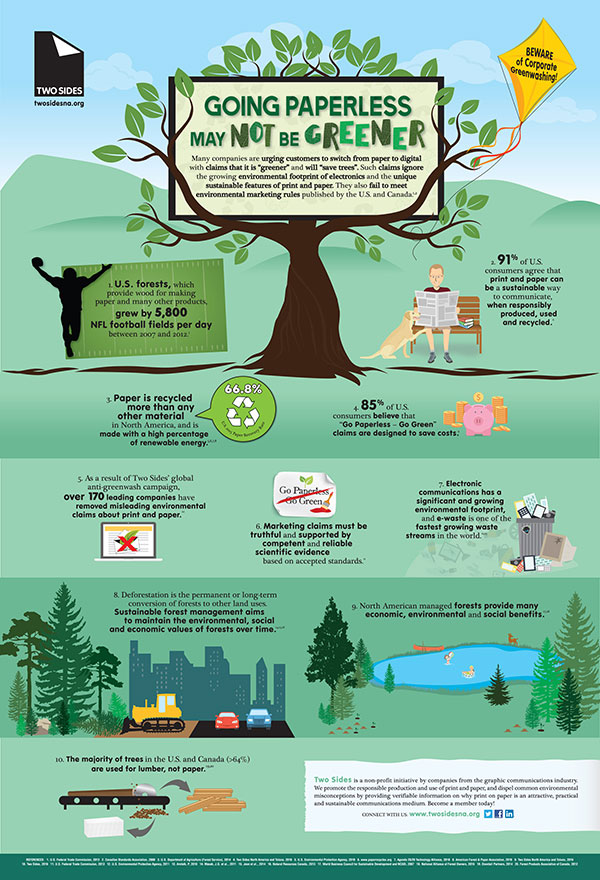
Amazon is seeking Supply Chain managers with proven leadership skills and senior track records to lead cross-functional strategic operations. These roles will manage projects that support new products and operations, while working closely with business departments around the globe. They will manage large-scale projects and develop cross-functional teams.
Manager, Purchasing and Supply Chain
Amazon Purchasing and Supply Chain managers are charged with a wide range of responsibilities. This includes driving cost savings, optimizing processes and mitigating risk. These responsibilities require strong analytical, negotiation, and communication skills.
The ideal candidate for this role is a self starter who can communicate well and pays attention to detail. He or she should be able work independently, meet tight deadlines and manage their workload well.
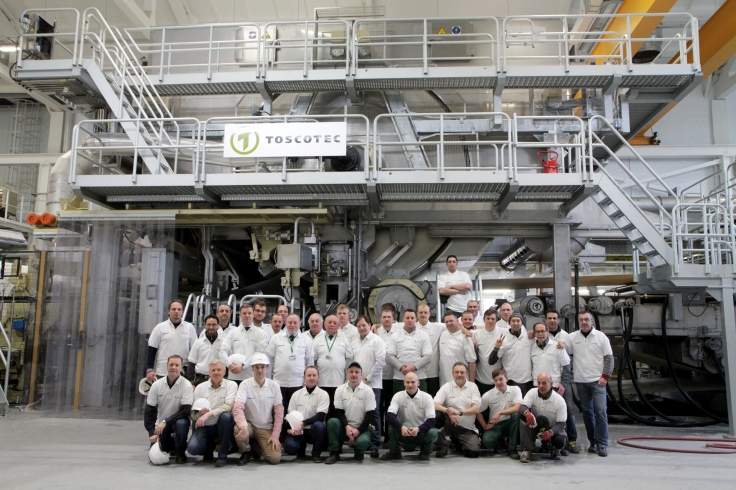
Cost analyst
Amazon's supply chains are an integral part of its success. It includes fulfillment, transportation, forecasting, and all other aspects. It requires someone who is highly analytical and has a passion about details. The person will use data analysis to help understand the company's operation. Global stakeholders will collaborate with the analyst to interpret data and draw conclusions. For their analysis, they can use MS Excel (or SQL).
The Amazon supply chain is one of the most innovative in the world. Amazon invests in warehouse technology, trucking capabilities and many other areas. Amazon is also investing heavily into drones and cargo planes.
Manager of the program
Amazon program manager supply chain jobs require extensive knowledge in areas such as supply chain planning, manufacturing and logistics. The successful candidate will also have the ability to work in a team and take data-driven decisions. In addition, he or she will be tasked with building and administering systems and processes for scale, quality control, and risk management.
The salary of a Supply Chain Program Director varies depending upon the city where the job is located. Some managers earn more than $168,000 annually, while others only earn $52,500. On average, Program managers earn between $87,500 and $127,500 annually. However, salaries can vary by nearly $40,000 depending on the region in which they work and the amount of experience they have.
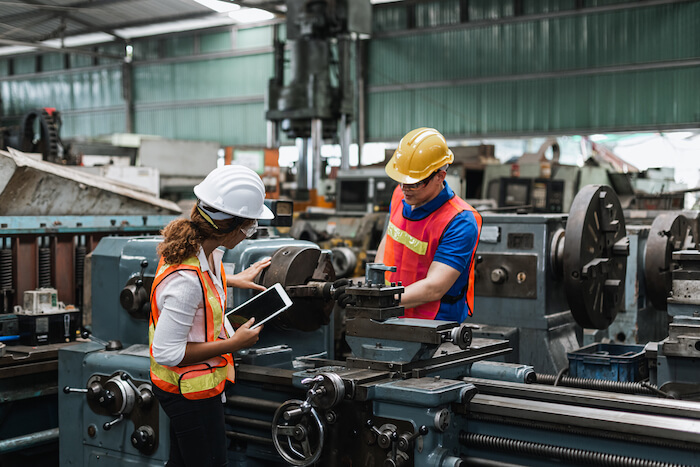
Warehouse manager
Warehouse management jobs are highly sought-after, and the demand for them is growing. While there are no specific educational requirements for a warehouse manager, many employers prefer to hire individuals who have some sort of experience. You do not need a bachelor's to be able to apply for this position. However, it will help increase your chances of being hired.
Warehouse managers have many responsibilities, including customer service and inventory management. They also have a huge impact on the experience for shippers and operators. They manage the supply chain performance and create initiatives to increase efficiency. Additionally, they can work with multiple Amazon teams and gain broad exposure to their operations.
FAQ
What skills do production planners need?
A production planner must be organized, flexible, and able multitask to succeed. You must also be able to communicate effectively with clients and colleagues.
What are the 7 R's of logistics?
The acronym 7R's for Logistics stands to represent the seven basic principles in logistics management. It was published in 2004 by the International Association of Business Logisticians as part of their "Seven Principles of Logistics Management" series.
The following letters form the acronym:
-
Responsive - ensure all actions are legal and not harmful to others.
-
Reliable - have confidence in the ability to deliver on commitments made.
-
Be responsible - Use resources efficiently and avoid wasting them.
-
Realistic – consider all aspects of operations, from cost-effectiveness to environmental impact.
-
Respectful – Treat others fairly and equitably.
-
Resourceful - look for opportunities to save money and increase productivity.
-
Recognizable - provide customers with value-added services.
What type of jobs is there in logistics
There are many jobs available in logistics. Here are some:
-
Warehouse workers - They load and unload trucks and pallets.
-
Transportation drivers - They drive trucks and trailers to deliver goods and carry out pick-ups.
-
Freight handlers - They sort and pack freight in warehouses.
-
Inventory managers - They oversee the inventory of goods in warehouses.
-
Sales representatives - They sell products.
-
Logistics coordinators are responsible for organizing and planning logistics operations.
-
Purchasing agents: They are responsible for purchasing goods and services to support company operations.
-
Customer service representatives - They answer calls and emails from customers.
-
Shipping clerks: They process shipping requests and issue bills.
-
Order fillers - They fill orders based on what is ordered and shipped.
-
Quality control inspectors – They inspect incoming and outgoing products to ensure that there are no defects.
-
Others – There are many other types available in logistics. They include transport supervisors, cargo specialists and others.
What is the role and responsibility of a Production Planner?
Production planners ensure that all project aspects are completed on time, within budget and within the scope. A production planner ensures that the service and product meet the client's expectations.
What does it take for a logistics enterprise to succeed?
To be a successful businessman in logistics, you will need many skills and knowledge. For clients and suppliers to be successful, you need to have excellent communication skills. It is important to be able to analyse data and draw conclusions. You need to be able work under pressure and manage stressful situations. In order to innovate and create new ways to improve efficiency, creativity is essential. You must be a strong leader to motivate others and direct them to achieve organizational goals.
You must be organized to meet tight deadlines.
What are the four types of manufacturing?
Manufacturing is the process of transforming raw materials into useful products using machines and processes. It includes many different activities like designing, building and testing, packaging, shipping and selling, as well as servicing.
Statistics
- (2:04) MTO is a production technique wherein products are customized according to customer specifications, and production only starts after an order is received. (oracle.com)
- [54][55] These are the top 50 countries by the total value of manufacturing output in US dollars for its noted year according to World Bank.[56] (en.wikipedia.org)
- In the United States, for example, manufacturing makes up 15% of the economic output. (twi-global.com)
- It's estimated that 10.8% of the U.S. GDP in 2020 was contributed to manufacturing. (investopedia.com)
- According to a Statista study, U.S. businesses spent $1.63 trillion on logistics in 2019, moving goods from origin to end user through various supply chain network segments. (netsuite.com)
External Links
How To
Six Sigma and Manufacturing
Six Sigma refers to "the application and control of statistical processes (SPC) techniques in order to achieve continuous improvement." Motorola's Quality Improvement Department created Six Sigma at their Tokyo plant, Japan in 1986. Six Sigma's main goal is to improve process quality by standardizing processes and eliminating defects. Many companies have adopted this method in recent years. They believe there is no such thing a perfect product or service. Six Sigma seeks to reduce variation between the mean production value. This means that you can take a sample from your product and then compare its performance to the average to find out how often the process differs from the norm. If you notice a large deviation, then it is time to fix it.
Understanding how your business' variability is a key step towards Six Sigma implementation is the first. Once you've understood that, you'll want to identify sources of variation. Also, you will need to identify the sources of variation. Random variations are caused by human errors. Systematic variations can be caused by outside factors. These are, for instance, random variations that occur when widgets are made and some fall off the production line. If however, you notice that each time you assemble a widget it falls apart in exactly the same spot, that is a problem.
Once you identify the problem areas, it is time to create solutions. The solution could involve changing how you do things, or redesigning your entire process. Test them again once you've implemented the changes. If they didn't work, then you'll need to go back to the drawing board and come up with another plan.