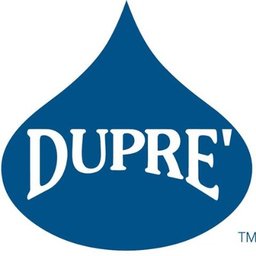
San Diego, whether you're new in the city or just looking to switch careers, is home to some the best logistics jobs nationwide. These positions range from entry-level positions to director jobs that pay well over $100,000 a year.
A company's supply-chain is not complete without logistics jobs. They assist in moving products from manufacturers to consumers. These jobs also include those that deal with warehousing, storage, inventory management and distribution.
The United States has some of the biggest companies. General Dynamics is one of them, as are BAE Systems or NASSCO, shipbuilders and repairs.
Your career as a logistics professional could take you to any part of the globe. This field offers many opportunities for people who are organized and enjoy structure.
Many industries offer entry-level positions in logistics that don't need a degree. However, you may want to pursue a higher education if you're planning to oversee a larger supply chain or other department.
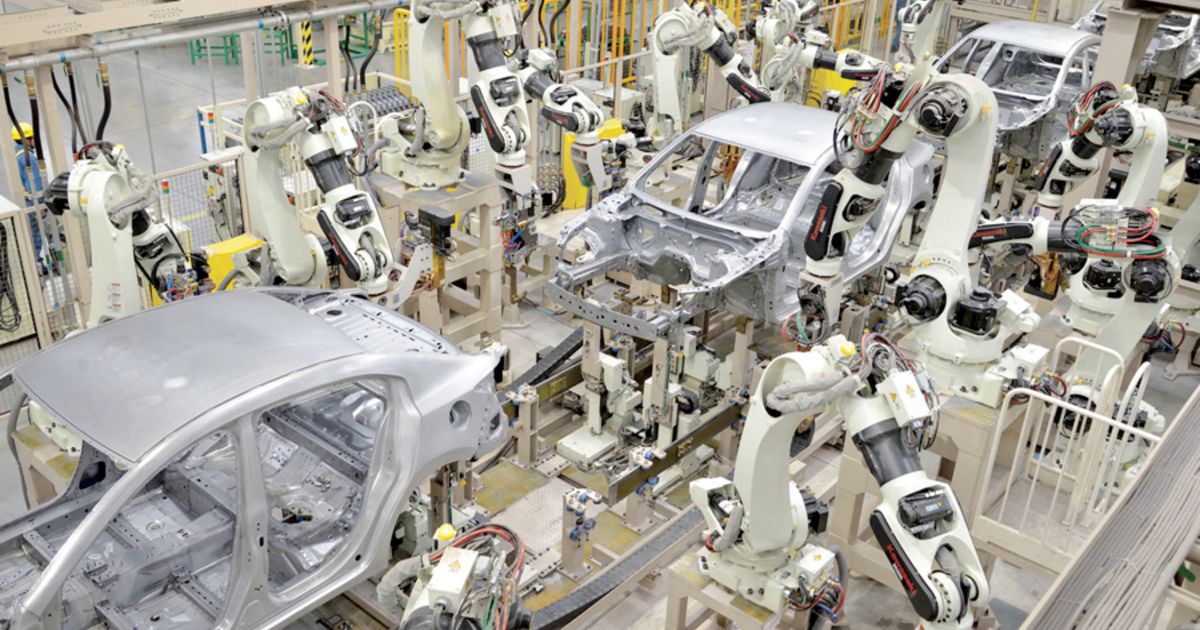
Logistics jobs in San Diego include analysing data about transportation and determining the most efficient routes to transport products. These jobs are a great opportunity to improve your resume while earning a decent salary.
Trucking and shipping jobs are also available in the logistics industry. These involve delivering packages and freight to different destinations. These jobs require a valid driver's licence and a clean criminal record.
Warehouse manager is a second option for people interested in a logistical job. This can be a high-level position that pays well and can offer you the opportunity to work with large amounts of inventory and equipment.
Logistics companies in San Diego offer many services including transportation and warehousing. These companies can be a great way to make sure your supplies get from the manufacturer to your warehouse on time and in perfect condition.
Some of the most popular San Diego logistics companies include Omni Logistics, WWEX, and Worldwide Express. These businesses offer a variety freight services including domestic transportation and international shipping.
They're known for their customer service, which is why they're a top choice among companies in San Diego. They will go the extra mile to make sure your shipments are delivered on time and in great condition.
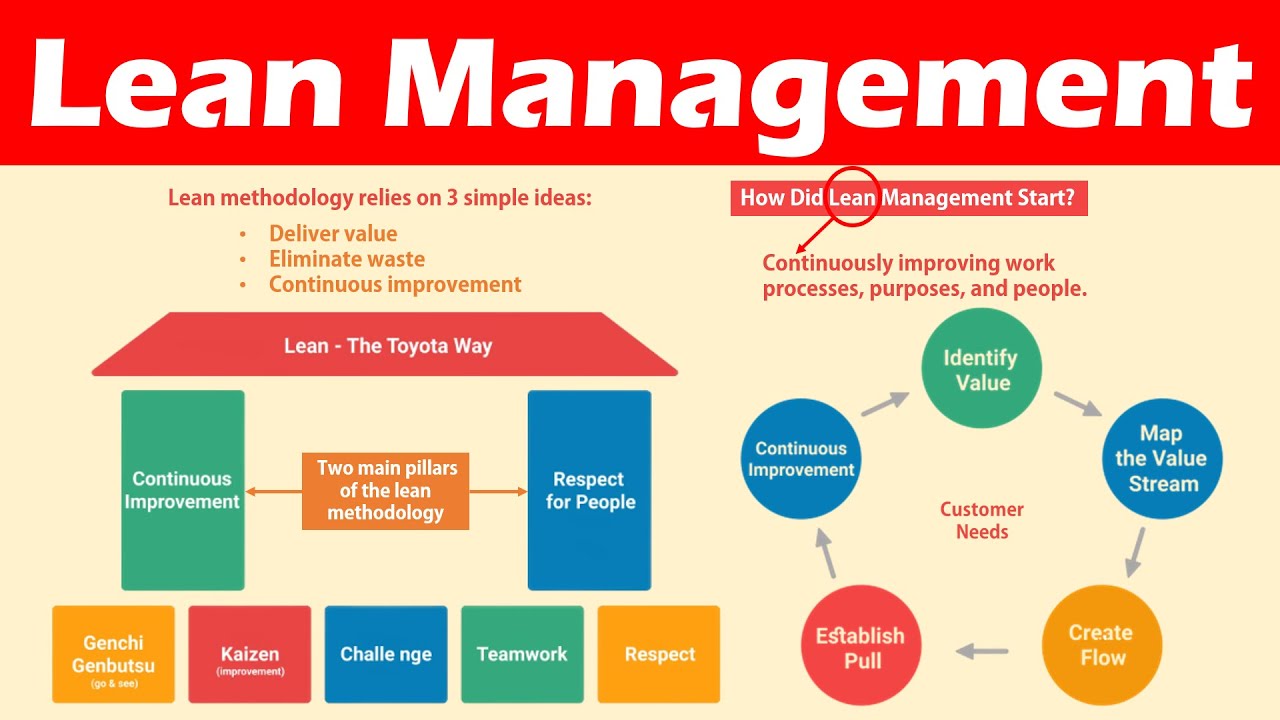
Zion Transport provides a high-quality service in San Diego at competitive prices. The company provides trucking and shipping services for all types of businesses - from small start-ups to large corporations.
These services are a crucial part of any business, and they can often be difficult to manage. The services can be both time-consuming as well as costly. That's why it's important to work with a shipping firm that is reliable and can help you cut costs.
Our Salary Tools will help you determine what salary you can expect for different positions in San Diego. This information will help you determine if this career is right for you.
FAQ
What's the difference between Production Planning & Scheduling?
Production Planning (PP), also known as forecasting and identifying production capacities, is the process that determines what product needs to be produced at any particular time. Forecasting and identifying production capacity are two key elements to this process.
Scheduling is the process that assigns dates to tasks so they can get completed within a given timeframe.
What are the responsibilities of a production planner
Production planners ensure all aspects of the project are delivered within time and budget. They ensure that the product or service is of high quality and meets client requirements.
Are there any Manufacturing Processes that we should know before we can learn about Logistics?
No. No. However, knowing about manufacturing processes will definitely give you a better understanding of how logistics works.
What skills does a production planner need?
Production planners must be flexible, organized, and able handle multiple tasks. Communication skills are essential to ensure that you can communicate effectively with clients, colleagues, and customers.
Why automate your warehouse
Modern warehousing has seen automation take center stage. The rise of e-commerce has led to increased demand for faster delivery times and more efficient processes.
Warehouses must adapt quickly to meet changing customer needs. Technology investment is necessary to enable warehouses to respond quickly to changing demands. Automating warehouses has many benefits. Here are some benefits of investing in automation
-
Increases throughput/productivity
-
Reduces errors
-
Accuracy is improved
-
Safety increases
-
Eliminates bottlenecks
-
Companies can scale up more easily
-
Makes workers more efficient
-
This gives you visibility into what happens in the warehouse
-
Enhances customer experience
-
Improves employee satisfaction
-
It reduces downtime, and increases uptime
-
This ensures that quality products are delivered promptly
-
Removing human error
-
It ensures compliance with regulations
Statistics
- According to the United Nations Industrial Development Organization (UNIDO), China is the top manufacturer worldwide by 2019 output, producing 28.7% of the total global manufacturing output, followed by the United States, Japan, Germany, and India.[52][53] (en.wikipedia.org)
- It's estimated that 10.8% of the U.S. GDP in 2020 was contributed to manufacturing. (investopedia.com)
- You can multiply the result by 100 to get the total percent of monthly overhead. (investopedia.com)
- Many factories witnessed a 30% increase in output due to the shift to electric motors. (en.wikipedia.org)
- [54][55] These are the top 50 countries by the total value of manufacturing output in US dollars for its noted year according to World Bank.[56] (en.wikipedia.org)
External Links
How To
How to use the Just In-Time Production Method
Just-in-time is a way to cut costs and increase efficiency in business processes. It's a way to ensure that you get the right resources at just the right time. This means you only pay what you use. The term was first coined by Frederick Taylor, who developed his theory while working as a foreman in the early 1900s. After observing how workers were paid overtime for late work, he realized that overtime was a common practice. He decided that workers would be more productive if they had enough time to complete their work before they started to work.
The idea behind JIT is that you should plan ahead and have everything ready so you don't waste money. Look at your entire project, from start to end. Make sure you have enough resources in place to deal with any unexpected problems. If you anticipate that there might be problems, you'll have enough people and equipment to fix them. This way, you won't end up paying extra money for things that weren't really necessary.
There are many types of JIT methods.
-
Demand-driven: This type of JIT allows you to order the parts/materials required for your project on a regular basis. This will allow to track how much material has been used up. This will allow you to calculate how long it will take to make more.
-
Inventory-based: You stock materials in advance to make your projects easier. This allows for you to anticipate how much you can sell.
-
Project-driven: This means that you have enough money to pay for your project. If you know the amount you require, you can buy the materials you need.
-
Resource-based JIT: This type of JIT is most commonly used. This is where you assign resources based upon demand. You might assign more people to help with orders if there are many. If there aren't many orders, you will assign fewer people.
-
Cost-based: This is a similar approach to resource-based but you are not only concerned with how many people you have, but also how much each one costs.
-
Price-based: This is very similar to cost-based, except that instead of looking at how much each individual worker costs, you look at the overall price of the company.
-
Material-based is an alternative to cost-based. Instead of looking at the total cost in the company, this method focuses on the average amount of raw materials that you consume.
-
Time-based: This is another variation of resource-based JIT. Instead of worrying about how much each worker costs, you can focus on how long the project takes.
-
Quality-based JIT: This is another variation of resource based JIT. Instead of worrying about the costs of each employee or how long it takes for something to be made, you should think about how quality your product is.
-
Value-based JIT: One of the most recent forms of JIT. In this instance, you are not concerned about the product's performance or meeting customer expectations. Instead, your goal is to add value to the market.
-
Stock-based: This is an inventory-based method that focuses on the actual number of items being produced at any given time. This is used to increase production and minimize inventory.
-
Just-in-time planning (JIT): This is a combination JIT and supply-chain management. It is the process of scheduling components' delivery as soon as they have been ordered. It reduces lead times and improves throughput.