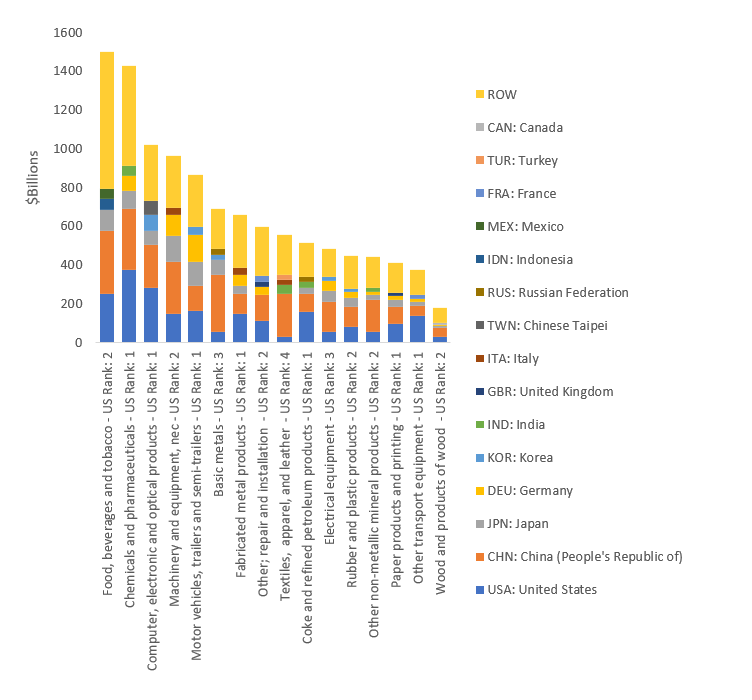
The HEROESPROGRAM can help homeowners or military families find affordable housing. It is a collaboration with web networks, radio stations, and community groups across the country to honor acts of bravery by our servicemen and women. It connects military spouses with lawyers who are experienced in military law, child support, and other issues.
Heroes To Heroes, a 501 (c)(3) non-profit organization, provides peer support as well as suicide prevention to combat veteran veterans. They offer a 12-month program that focuses on emotional strength and a 10-day trip in Israel. Heroes To Heroes helps soldiers who have suffered Moral Injuries. It also offers peer support and suicide prevention training for veterans who have suffered PTSD, combat injuries, and other mental health issues.
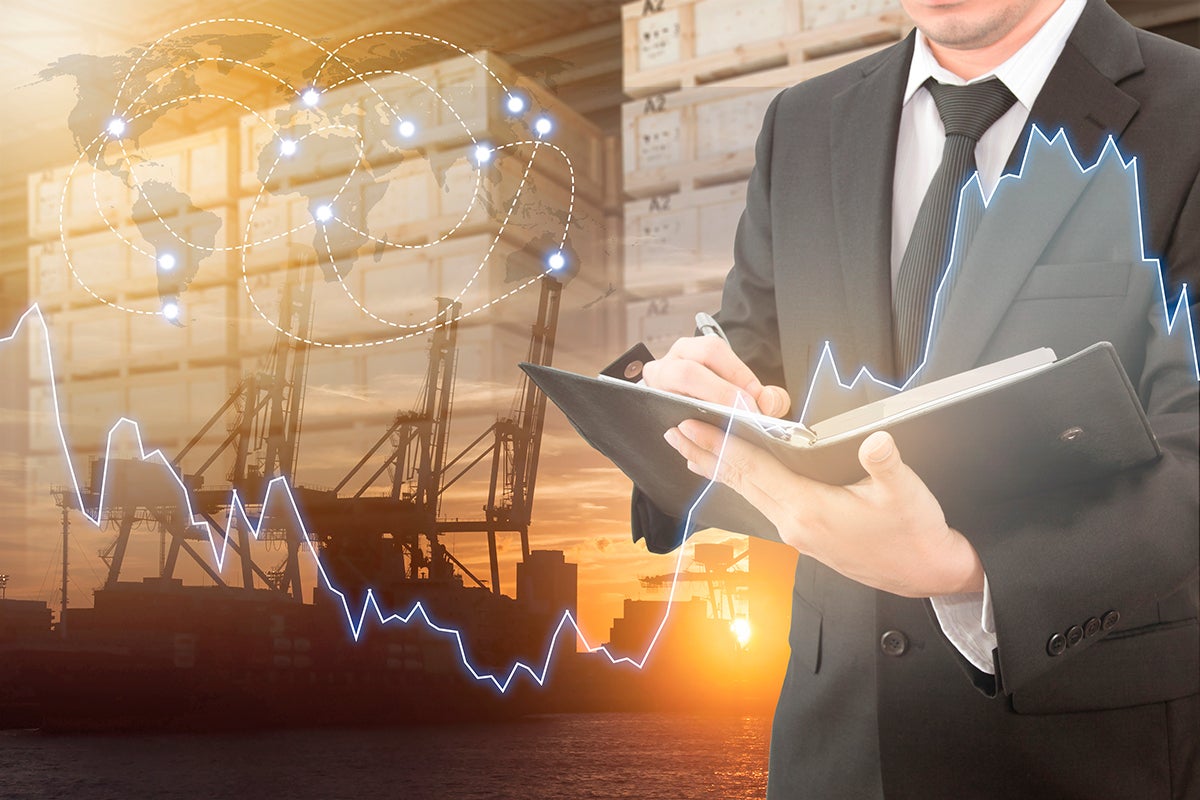
Hiring Our Heroes is a program that helps our veterans find jobs. Hiring Our Heroes helps veterans, active duty military families, and all other members of our military community to identify themselves. The program assists veterans to find employment and provides support for military families with children. Additionally, the organization provides a scholarship to children of veterans and offers other forms assistance.
Heroes MAKE America provides more than just placing veterans in jobs. The program also prepares, certifies, and trains career readiness. Graduates have been placed with 250 companies in 42 US states by the program. They are working closely with local technical schools and organizations to help veteran find work. The program has grown since COVID-19. It will soon have a Georgia training location. Fort Riley is home to its growing programs. It has placed graduates in 136 different military occupational specialties. Veterans looking for employment in the manufacturing sector will find this program a valuable resource.
Fort Riley will continue to expand its Heroes MAKE America program and will introduce new features for 2021. They will feature virtual reality simulations. These virtual training programs will be available to transitioning service members, even those who do not have computers. They will also be able to connect with other veterans who have participated in the program. After COVID-19, the program will expand and continue to assist veterans in finding jobs in the manufacturing sector.
The HEROES leadership project is a group that brings together experience and talent to build a vibrant community for youth. The group creates an environment that youth can feel secure and supported. It is also part the Re-Envisioning Foster Care in America Movement. The members contribute their expertise, talents, and voices to create a more supportive youth environment.
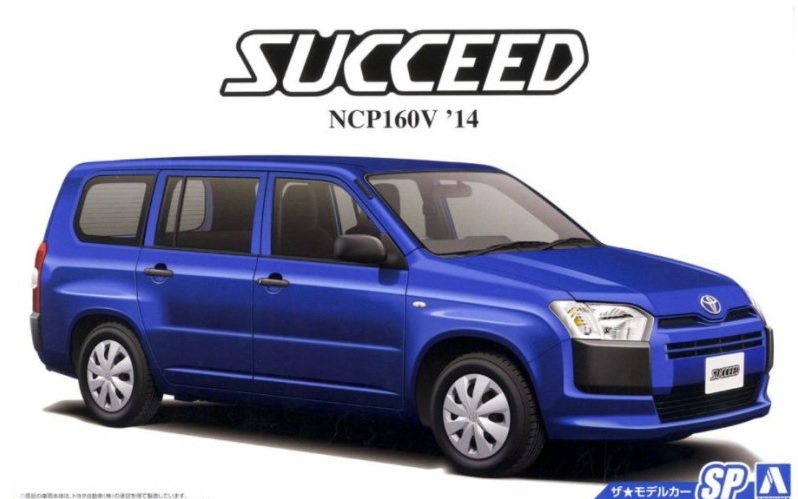
Homes for Heroes provides discounts on real-estate agent commissions as well as home inspection fees. The program has become very popular, and it is now available nationwide. It offers discounts to military veterans, teachers, and healthcare professionals. On average, a Hero saves about $2400.
FAQ
What does warehouse refer to?
A warehouse or storage facility is where goods are stored before they are sold. You can have it indoors or outdoors. In some cases, it may be a combination of both.
What makes a production planner different from a project manger?
The major difference between a Production Planner and a Project Manager is that a Project Manager is often the person responsible for organizing and planning the entire project. While a Production Planner is involved mainly in the planning stage,
What is manufacturing and logistics?
Manufacturing refers to the process of making goods using raw materials and machines. Logistics is the management of all aspects of supply chain activities, including procurement, production planning, distribution, warehousing, inventory control, transportation, and customer service. Manufacturing and logistics can often be grouped together to describe a larger term that covers both the creation of products, and the delivery of them to customers.
What does it take for a logistics enterprise to succeed?
You need to have a lot of knowledge and skills to manage a successful logistic business. Good communication skills are essential to effectively communicate with your suppliers and clients. It is important to be able to analyse data and draw conclusions. You need to be able work under pressure and manage stressful situations. In order to innovate and create new ways to improve efficiency, creativity is essential. To motivate and guide your team towards reaching organizational goals, you must have strong leadership skills.
It is important to be organized and efficient in order to meet tight deadlines.
What skills is required for a production planner?
Production planners must be flexible, organized, and able handle multiple tasks. Also, you must be able and willing to communicate with clients and coworkers.
Do we need to know about Manufacturing Processes before learning about Logistics?
No. You don't have to know about manufacturing processes before learning about logistics. However, knowing about manufacturing processes will definitely give you a better understanding of how logistics works.
What is production planning?
Production planning is the process of creating a plan that covers all aspects of production. This includes scheduling, budgeting and crew, location, equipment, props, and more. This document is designed to make sure everything is ready for when you're ready to shoot. This document should also include information on how to get the best result on set. This information includes locations, crew details and equipment requirements.
First, you need to plan what you want to film. You might have an idea of where you want to film, or you may have specific locations or sets in mind. Once you have determined your scenes and locations, it is time to start figuring out the elements that you will need for each scene. For example, you might decide that you need a car but don't know exactly what model you want. This is where you can look up car models online and narrow down your options by choosing from different makes and models.
After you've found the perfect car, it's time to start thinking about adding extras. Do you have people who need to be seated in the front seat? You might also need someone to help you get around the back. Maybe you want to change the interior color from black to white? These questions will help guide you in determining the ideal look and feel for your car. The type of shots that you are looking for is another thing to consider. What type of shots will you choose? Maybe you want to show the engine and the steering wheel. These details will help identify the exact car you wish to film.
Once you have made all the necessary decisions, you can start to create a schedule. You can create a schedule that will outline when you must start and finish your shoots. A schedule for each day will detail when you should arrive at the location and when you need leave. Everyone knows exactly what they should do and when. Book extra staff ahead of time if you need them. It is not worth hiring someone who won’t show up because you didn’t tell him.
You will need to factor in the days that you have to film when creating your schedule. Some projects are quick and easy, while others take weeks. When creating your schedule, be aware of whether you need more shots per day. Multiple takes of the same location will lead to higher costs and take more time. You can't be certain if you will need multiple takes so it is better not to shoot too many.
Budgeting is another important aspect of production planning. As it will allow you and your team to work within your financial means, setting a realistic budget is crucial. Remember that you can always reduce the budget later on if you run into unforeseen problems. You shouldn't underestimate the amount you'll spend. Underestimating the cost will result in less money after you have paid for other items.
Planning production is a tedious process. Once you have a good understanding of how everything works together, planning future projects becomes easy.
Statistics
- It's estimated that 10.8% of the U.S. GDP in 2020 was contributed to manufacturing. (investopedia.com)
- You can multiply the result by 100 to get the total percent of monthly overhead. (investopedia.com)
- [54][55] These are the top 50 countries by the total value of manufacturing output in US dollars for its noted year according to World Bank.[56] (en.wikipedia.org)
- Job #1 is delivering the ordered product according to specifications: color, size, brand, and quantity. (netsuite.com)
- According to the United Nations Industrial Development Organization (UNIDO), China is the top manufacturer worldwide by 2019 output, producing 28.7% of the total global manufacturing output, followed by the United States, Japan, Germany, and India.[52][53] (en.wikipedia.org)
External Links
How To
How to use 5S in Manufacturing to Increase Productivity
5S stands for "Sort", 'Set In Order", 'Standardize', & Separate>. The 5S methodology was developed at Toyota Motor Corporation in 1954. It assists companies in improving their work environments and achieving higher efficiency.
The basic idea behind this method is to standardize production processes, so they become repeatable, measurable, and predictable. This means that tasks such as cleaning, sorting, storing, packing, and labeling are performed daily. This knowledge allows workers to be more efficient in their work because they are aware of what to expect.
There are five steps that you need to follow in order to implement 5S. Each step involves a different action which leads to increased efficiency. By sorting, for example, you make it easy to find the items later. When items are ordered, they are put together. Then, after you separate your inventory into groups, you store those groups in containers that are easy to access. Make sure everything is correctly labeled when you label your containers.
Employees must be able to critically examine their work practices. Employees must be able to see why they do what they do and find a way to achieve them without having to rely on their old methods. In order to use the 5S system effectively, they must be able to learn new skills.
The 5S method increases efficiency and morale among employees. They feel more motivated to work towards achieving greater efficiency as they see the results.