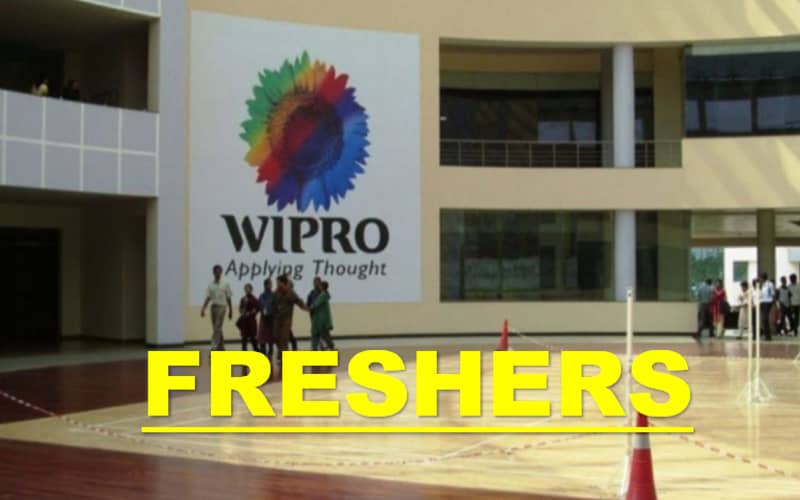
Kaizen integration into manufacturing processes can be difficult. It takes time to obtain inventory and ensure everyone is present. The amount of time needed to improve the manufacturing process depends on the level of participation, the problem area, and the firm. To ensure that your manufacturing process improvement initiative will be successful, follow the proper implementation methodologies and get the necessary resources. In order to make this strategy successful, you need to set up a strong company culture that encourages continuous improvement.
Create a company culture that is focused on improvement
Gallup polls found that 32% of Americans are not engaged in their work. Of those, 17.2% were actively disengaged. Kaizen culture can be implemented to encourage employee engagement. This will lead to improved processes, lower turnover, and more innovation. Engagement will increase employee productivity and satisfaction. Kaizen culture offers more benefits than reducing waste, increasing productivity, and increasing customer satisfaction.
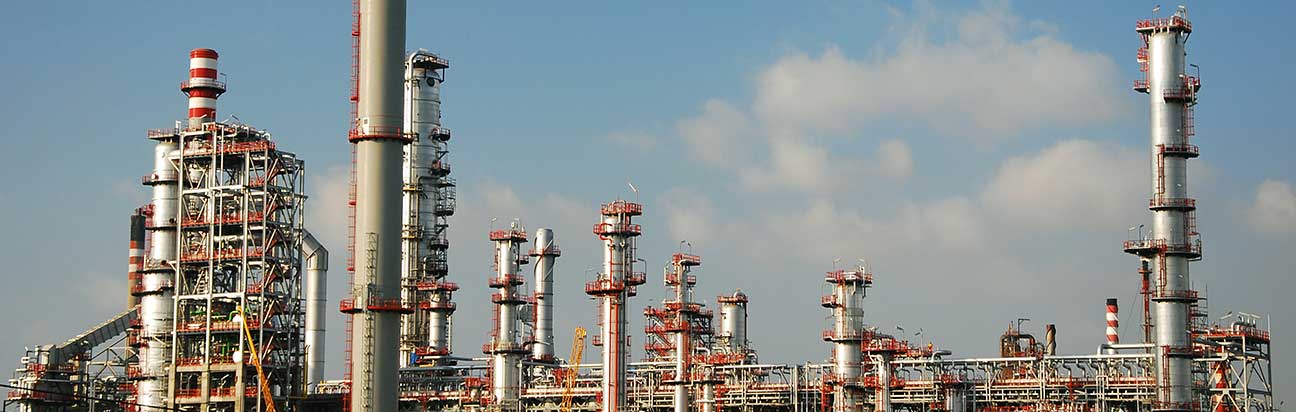
Kaizen is continuous improvement of every aspect of a company. Kaizen isn't about making huge, unproductive changes. It's about incremental improvement. Kaizen can be a method of incremental improvement that leads to reduced costs, increased productivity and better customer satisfaction. It is also a great way to increase employee morale.
Implementing kaizen in manufacturing is difficult
There are some downsides to kaizen implementation. First, implementing Kaizen in a business requires major changes to its management system. Once the changes are in place, it may be difficult to reverse the changes. Second, many businesses find it difficult to change existing work practices, which may pose a barrier to the implementation of kaizen.
Another problem is the fact that many manufacturers work in a "feast or framine" cycle. A machine shop could run into difficulties if there isn't enough demand for the products they produce or enough qualified people to fill their positions. In such a situation, they'll have to lay off employees and close their doors. These machine shops can avoid the "feast-or-famine" cycle by implementing continuous improvement or kaizen. Kaizen will improve the efficiency of a shop and enable it to produce more product.
Kaizen implementation in manufacturing is a success rate
Statistics show that Kaizen implementation in manufacturing is not a success. Only 10% manufacturing firms reported positive Kaizen results. However, that does not make the Kaizen implementation useless. Implementing kaizen can be a key component of lean manufacturing. Here are some tips to increase your manufacturing business's success rate:
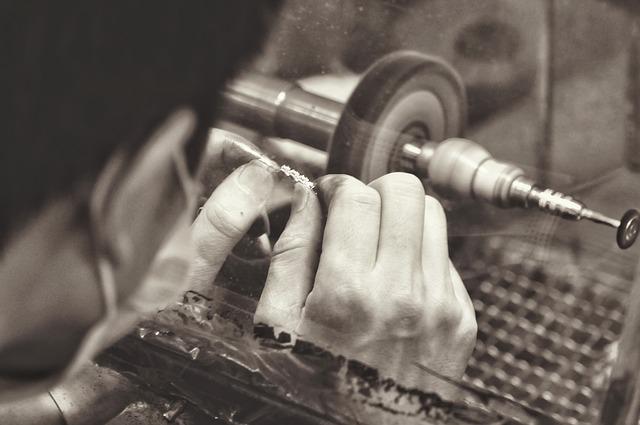
Understanding the state of the world is essential to kaizen. Data is collected and analyzed in order to identify top priorities. Next, improvements are tested by comparing the before and after. A benefit-to-cost analysis is also a useful tool to determine the impact of specific improvements or the entire kaizen process. To assess the program's effectiveness, it is crucial to monitor the results for 60 to 90 days.
FAQ
What type of jobs is there in logistics
There are many jobs available in logistics. Some examples are:
-
Warehouse workers - They load trucks and pallets.
-
Transportation drivers: They drive trucks and trailers and deliver goods and make pick-ups.
-
Freight handlers – They sort and package freight at warehouses.
-
Inventory managers - These are responsible for overseeing the stock of goods in warehouses.
-
Sales representatives - They sell products to customers.
-
Logistics coordinators - They plan and organize logistics operations.
-
Purchasing agents – They buy goods or services necessary to run a company.
-
Customer service agents - They answer phone calls and respond to emails.
-
Shipping clerks – They process shipping orders, and issue bills.
-
Order fillers - They fill orders based on what is ordered and shipped.
-
Quality control inspectors are responsible for inspecting incoming and outgoing products looking for defects.
-
Others - There are many types of jobs in logistics such as transport supervisors and cargo specialists.
How does manufacturing avoid bottlenecks in production?
Avoiding production bottlenecks is as simple as keeping all processes running smoothly, from the time an order is received until the product ships.
This includes both planning for capacity and quality control.
The best way to do this is to use continuous improvement techniques such as Six Sigma.
Six Sigma is a management system used to improve quality and reduce waste in every aspect of your organization.
It's all about eliminating variation and creating consistency in work.
What are the responsibilities for a manufacturing manager
A manufacturing manager must make sure that all manufacturing processes run smoothly and effectively. They must also be alert to any potential problems and take appropriate action.
They should also know how to communicate with other departments such as sales and marketing.
They should be up to date on the latest trends and be able apply this knowledge to increase productivity and efficiency.
What are manufacturing and logistics?
Manufacturing is the act of producing goods from raw materials using machines and processes. Logistics includes all aspects related to supply chain management, such as procurement, distribution planning, inventory control and transportation. Manufacturing and logistics are often considered together as a broader term that encompasses both the process of creating products and delivering them to customers.
What are the responsibilities of a logistic manager?
Logistics managers make sure all goods are delivered on schedule and without damage. This is done through his/her expertise and knowledge about the company's product range. He/she should ensure that sufficient stock is available in order to meet customer demand.
Statistics
- You can multiply the result by 100 to get the total percent of monthly overhead. (investopedia.com)
- It's estimated that 10.8% of the U.S. GDP in 2020 was contributed to manufacturing. (investopedia.com)
- Many factories witnessed a 30% increase in output due to the shift to electric motors. (en.wikipedia.org)
- Job #1 is delivering the ordered product according to specifications: color, size, brand, and quantity. (netsuite.com)
- According to a Statista study, U.S. businesses spent $1.63 trillion on logistics in 2019, moving goods from origin to end user through various supply chain network segments. (netsuite.com)
External Links
How To
How to use the Just In-Time Production Method
Just-intime (JIT), a method used to lower costs and improve efficiency in business processes, is called just-in-time. It's the process of obtaining the right amount and timing of resources when you need them. This means that you only pay for what you actually use. Frederick Taylor, a 1900s foreman, first coined the term. Taylor observed that overtime was paid to workers if they were late in working. He then concluded that if he could ensure that workers had enough time to do their job before starting to work, this would improve productivity.
JIT is an acronym that means you need to plan ahead so you don’t waste your money. It is important to look at your entire project from beginning to end and ensure that you have enough resources to handle any issues that may arise. You will have the resources and people to solve any problems you anticipate. This way you won't be spending more on things that aren’t really needed.
There are many JIT methods.
-
Demand-driven: This is a type of JIT where you order the parts/materials needed for your project regularly. This will allow you to track how much material you have left over after using it. This will allow you to calculate how long it will take to make more.
-
Inventory-based: This allows you to store the materials necessary for your projects in advance. This allows you to predict how much you can expect to sell.
-
Project-driven: This is an approach where you set aside enough funds to cover the cost of your project. When you know how much you need, you'll purchase the appropriate amount of materials.
-
Resource-based JIT : This is probably the most popular type of JIT. You assign certain resources based off demand. You will, for example, assign more staff to deal with large orders. You'll have fewer orders if you have fewer.
-
Cost-based: This is similar to resource-based, except that here you're not just concerned about how many people you have but how much each person costs.
-
Price-based pricing: This is similar in concept to cost-based but instead you look at how much each worker costs, it looks at the overall company's price.
-
Material-based: This is quite similar to cost-based, but instead of looking at the total cost of the company, you're concerned with how much raw materials you spend on average.
-
Time-based JIT is another form of resource-based JIT. Instead of focusing on how much each employee costs, you focus on how long it takes to complete the project.
-
Quality-based JIT is another variant of resource-based JIT. Instead of focusing on the cost of each worker or how long it takes, think about how high quality your product is.
-
Value-based JIT: One of the most recent forms of JIT. In this instance, you are not concerned about the product's performance or meeting customer expectations. Instead, your focus is on the value you bring to the market.
-
Stock-based: This inventory-based approach focuses on how many items are being produced at any one time. It is used when production goals are met while inventory is kept to a minimum.
-
Just-intime planning (JIT), is a combination JIT/sales chain management. This refers to the scheduling of the delivery of components as soon after they are ordered. It's important because it reduces lead times and increases throughput.