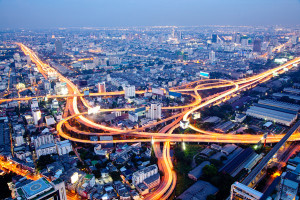
The United States ranks third among the largest manufacturers in the world. In Q1 2018, its manufacturing output topped $2.00 trillion. This is nearly twice what it was prior to the Great Recession. Despite the strong domestic economy, the United States' manufacturing industry continues to take a sloppy approach to solving its current problems. This could be due to a shortage of skilled labor or investment, but we must be more aggressive in dealing with the problems facing our industry.
Since 2000, jobs have dropped by 5 million
The US has lost five million manufacturing jobs since 2000. Although some believe that trade with China has contributed to the decrease in manufacturing jobs, this accounts for only a quarter of the total decline. Trade with China was not the only reason for manufacturing jobs being lost. Local markets were also affected by Chinese imports. But the reasons for the decline in manufacturing jobs are many. Here are some reasons why manufacturing jobs have declined:
Over the past two decades, almost a third have been lost in US manufacturing. It stood at 17 million in 1965, and fell to just 12 million in 2010. Although the decline of manufacturing jobs is not due solely to trade, it is the result structural problems such as a fall in capital investment and output. These are not sustainable. Although productivity gains played a significant role in the decline of manufacturing jobs, they were not enough to compensate. The problem is not productivity gains but automation.
The demand for manufactured products is strong
In the United States, the demand for manufactured goods remains strong despite the fact that the share of consumer spending on these items has decreased over the past few decades. In 1945, personal expenditures on durable goods accounted for 58% of total spending, compared to just 28% today. This is because the cost of manufacturing and sale of these goods has dropped while the content has increased. The result is that computers, televisions and sound equipment have fallen in price.
The US's recovery in manufacturing activity has resulted in an increase in the production of manufactured goods. The Fifth District Manufacturing Activity Survey reveals that the demand for manufactured products is strong, with production increasing rapidly. However, supply chain problems are slowing down output. The increased production has put stress on supply chains, and respondents have reported supply chain disruptions that affect their ability to maintain necessary inventories. Backlogs in orders have increased and so has the time it takes for vendors to respond.
The trade deficit in manufacturable goods has more or less doubled over the past decade
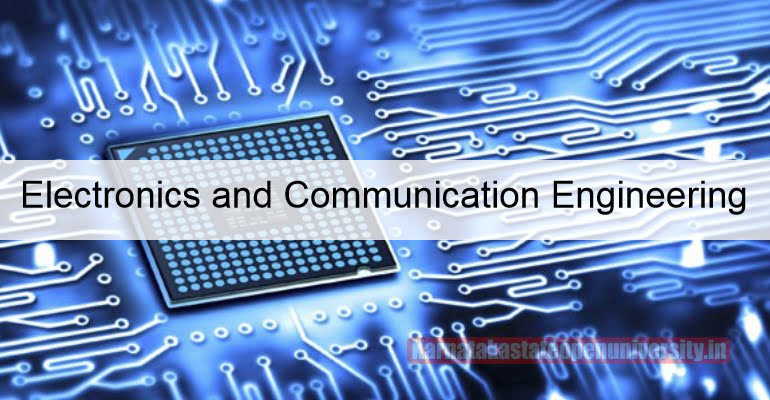
Some economists fear that the U.S.’s trade surplus will lead to lower global GDP and increase instability among its trading partners. Others point out that high imports of US manufactured goods are not necessarily a bad thing for the U.S. economy, which is a key to maintaining global economic stability. Trade deficits may be an inevitable evil since the U.S. is heavily dependent on foreign markets to generate its economy. This may make it more difficult to achieve full employment.
Since 2000, the U.S. manufactured goods trade deficit has almost doubled. Partially, the US trade deficit in manufactured goods has doubled since 2000. The problem is even more severe: this imbalance is concentrated at the manufacturing sector, where wages are down and employment is declining since the 1990s. US manufacturing employment has declined dramatically, from 26 percent in 1970 down to 8.5 percent in 2016. Some economists attribute the decline to China's increased competition, but most attribute the decline to automation, productivity increases, and demand shifting away from goods to services.
Industry follows a shotgun approach
While the US manufacturing industry has a wide range of advanced manufacturing initiatives and is well-established in this field, some countries are taking a single-shot approach to bringing the internet of things into manufacturing. The US, in contrast, is more focused on various technologies and integrates traditional mass media with Internet marketing. The result is a shotgun approach. Companies are able to focus on many technologies while aiming for a wide audience.
FAQ
What are the products and services of logistics?
Logistics is the process of moving goods from one point to another.
They encompass all aspects transport, including packaging and loading, transporting, storage, unloading.
Logisticians ensure that the right product reaches the right place at the right time and under safe conditions. They help companies manage their supply chain efficiency by providing information on demand forecasts, stock levels, production schedules, and availability of raw materials.
They keep track and monitor the transit of shipments, maintain quality standards, order replenishment and inventories, coordinate with suppliers, vendors, and provide support for sales and marketing.
Are there ways to automate parts of manufacturing?
Yes! Yes. The wheel was invented by the Egyptians thousands of years ago. We now use robots to help us with assembly lines.
There are many applications for robotics in manufacturing today. These include:
-
Automated assembly line robots
-
Robot welding
-
Robot painting
-
Robotics inspection
-
Robots that create products
Manufacturing could also benefit from automation in other ways. For instance, 3D printing allows us make custom products and not have to wait for months or even weeks to get them made.
What are the 7 Rs of logistics?
The acronym "7R's" of Logistics stands for seven principles that underpin logistics management. It was developed by International Association of Business Logisticians (IABL), and published as part of their "Seven Principles of Logistics Management Series" in 2004.
The acronym is composed of the following letters.
-
Responsible - ensure that actions are in compliance with legal requirements and do not cause harm to others.
-
Reliable - have confidence in the ability to deliver on commitments made.
-
Use resources effectively and sparingly.
-
Realistic - consider all aspects of operations, including cost-effectiveness and environmental impact.
-
Respectful - show respect and treat others fairly and fairly
-
You are resourceful and look for ways to save money while increasing productivity.
-
Recognizable - provide customers with value-added services.
Statistics
- In 2021, an estimated 12.1 million Americans work in the manufacturing sector.6 (investopedia.com)
- Job #1 is delivering the ordered product according to specifications: color, size, brand, and quantity. (netsuite.com)
- According to the United Nations Industrial Development Organization (UNIDO), China is the top manufacturer worldwide by 2019 output, producing 28.7% of the total global manufacturing output, followed by the United States, Japan, Germany, and India.[52][53] (en.wikipedia.org)
- Many factories witnessed a 30% increase in output due to the shift to electric motors. (en.wikipedia.org)
- It's estimated that 10.8% of the U.S. GDP in 2020 was contributed to manufacturing. (investopedia.com)
External Links
How To
How to use 5S in Manufacturing to Increase Productivity
5S stands to stand for "Sort", “Set In Order", “Standardize", and "Store". Toyota Motor Corporation developed the 5S method in 1954. It improves the work environment and helps companies to achieve greater efficiency.
This method has the basic goal of standardizing production processes to make them repeatable. This means that every day tasks such cleaning, sorting/storing, packing, and labeling can be performed. These actions allow workers to perform their job more efficiently, knowing what to expect.
Implementing 5S involves five steps: Sort, Set in Order, Standardize Separate, Store, and Each step is a different action that leads to greater efficiency. For example, when you sort things, you make them easy to find later. When you set items in an order, you put items together. Then, after you separate your inventory into groups, you store those groups in containers that are easy to access. Finally, when you label your containers, you ensure everything is labeled correctly.
Employees must be able to critically examine their work practices. Employees need to understand the reasons they do certain jobs and determine if there is a better way. They must learn new skills and techniques in order to implement the 5S system.
In addition to increasing efficiency, the 5S method also improves morale and teamwork among employees. They are more motivated to achieve higher efficiency levels as they start to see improvement.