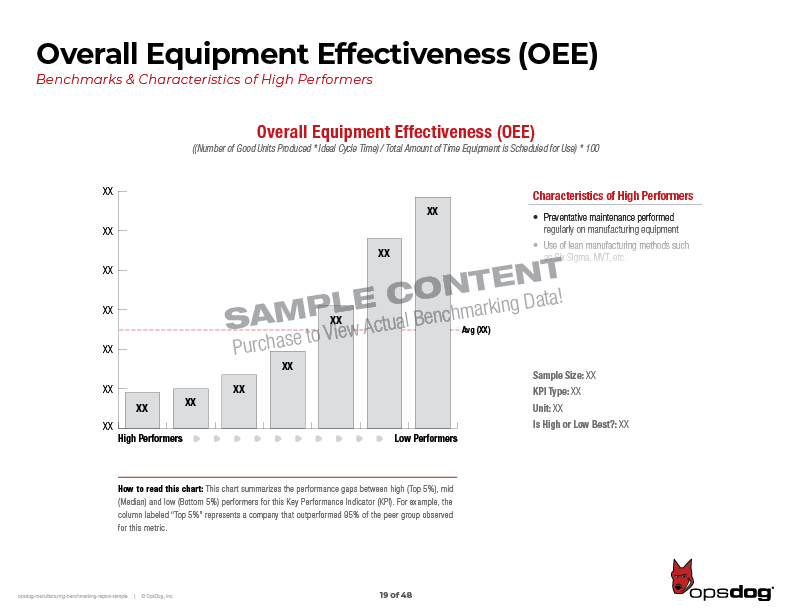
Federal and state government logistics jobs are available in both part time and full time capacities. They offer a number of advantages for job seekers. These include stable income, good benefits, and good income. The government can be a great place to get experience in this industry.
A Logistics Management Specialist, for example, is responsible for coordinating the supply chain. They monitor deliveries, manage contracts and perform audits. They identify supply chain problems and devise contingency plans. This position requires strong communication skills, strong typing abilities, and knowledge of government procurement regulations.
Supply Chain Management officers can work for the Department of Veterans Affairs as well as the Department of Homeland Security. The first role requires an understanding of federal procurement regulations. In the second, the position requires management of logistics operations and sourcing materials. Candidates must have a bachelor's degree, depending on the job. Candidates must have a good understanding of the business culture and regulations in the state where they will be applying. Certain positions may require security clearances. In these cases, a background check may be necessary.

Other government logistics specialists can also be employed to deploy materials quickly after an event. A distribution role in disaster logistics is offered by the North Carolina Department of Public Safety. Candidates need to have at the least four years of relevant work experience. As the position involves managing a team of personnel, candidates are expected to have the ability to work under stressful circumstances.
The departmental level also requires Logistics Management Specialists. The typical logistics management specialist role closely resembles that of the Federal Aviation Administration. The qualifications include an advanced degree, specialized knowledge in operations or project managing, and a background of logistics management.
If you are interested in a career working as a government logistic coordinator, you will need to be able manage large quantities of international travel. You'll also need to have a background in managing procurement negotiations and making supplier bids. Candidates should have at the very least two years of relevant work experience.
The federal government has many other supply-chain management roles you can apply to. These positions include those in transportation, warehousing, distribution, and air transport. These positions comprise almost 25% offered by the federal government and eight percent by the states.
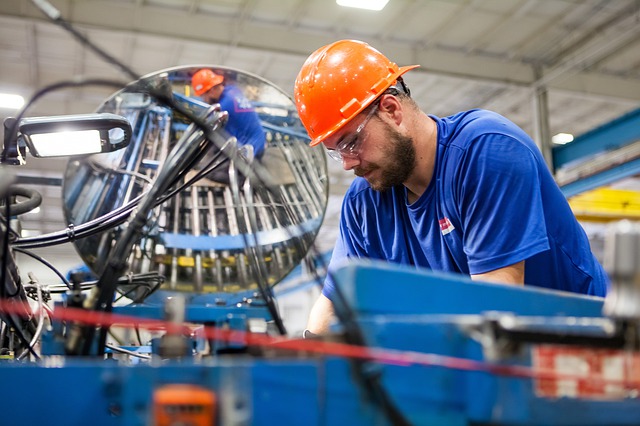
Several jobs can be found by browsing the federal government's website, USAJOBS. You can also search for a title or degree type. The majority of these positions require a minimum of a bachelor's, although some may require master's degrees. Jobs for supply chain specialists are also available at smaller organizations. A majority of supply chain professionals must have at least one (1) year of specialized experience in order to apply for a job.
There are many jobs for data scientists. Data Scientists support government programs and assist in the creation of strategic plans.
FAQ
Why automate your factory?
Automation has become increasingly important in modern warehousing. The rise of e-commerce has led to increased demand for faster delivery times and more efficient processes.
Warehouses must be able to quickly adapt to changing demands. In order to do this, they need to invest in technology. Automation warehouses can bring many benefits. Here are some of the reasons automation is worth your investment:
-
Increases throughput/productivity
-
Reduces errors
-
Accuracy is improved
-
Boosts safety
-
Eliminates bottlenecks
-
This allows companies to scale easily
-
Increases efficiency of workers
-
The warehouse can be viewed from all angles.
-
Enhances customer experience
-
Improves employee satisfaction
-
Minimizes downtime and increases uptime
-
Quality products delivered on time
-
Eliminates human error
-
It ensures compliance with regulations
How does a production planner differ from a project manager?
The difference between a product planner and project manager is that a planer is typically the one who organizes and plans the entire project. A production planner, however, is mostly involved in the planning stages.
Can certain manufacturing steps be automated?
Yes! Since ancient times, automation has been in existence. The Egyptians invented the wheel thousands of years ago. To help us build assembly lines, we now have robots.
In fact, there are several applications of robotics in manufacturing today. These include:
-
Automated assembly line robots
-
Robot welding
-
Robot painting
-
Robotics inspection
-
Robots that produce products
Automation can be applied to manufacturing in many other ways. For example, 3D printing allows us to make custom products without having to wait for weeks or months to get them manufactured.
Statistics
- According to the United Nations Industrial Development Organization (UNIDO), China is the top manufacturer worldwide by 2019 output, producing 28.7% of the total global manufacturing output, followed by the United States, Japan, Germany, and India.[52][53] (en.wikipedia.org)
- You can multiply the result by 100 to get the total percent of monthly overhead. (investopedia.com)
- Many factories witnessed a 30% increase in output due to the shift to electric motors. (en.wikipedia.org)
- Job #1 is delivering the ordered product according to specifications: color, size, brand, and quantity. (netsuite.com)
- In the United States, for example, manufacturing makes up 15% of the economic output. (twi-global.com)
External Links
How To
How to use 5S to increase Productivity in Manufacturing
5S stands to stand for "Sort", “Set In Order", “Standardize", and "Store". Toyota Motor Corporation invented the 5S strategy in 1954. It helps companies achieve higher levels of efficiency by improving their work environment.
The basic idea behind this method is to standardize production processes, so they become repeatable, measurable, and predictable. This means that daily tasks such as cleaning and sorting, storage, packing, labeling, and packaging are possible. Workers can be more productive by knowing what to expect.
Five steps are required to implement 5S: Sort, Set In Order, Standardize. Separate. Each step has a different action and leads to higher efficiency. You can make it easy for people to find things later by sorting them. Once you have placed items in an ordered fashion, you will put them together. Next, organize your inventory into categories and store them in containers that are easily accessible. Labeling your containers will ensure that everything is correctly labeled.
Employees will need to be more critical about their work. Employees must understand why they do certain tasks and decide if there's another way to accomplish them without relying on the old ways of doing things. In order to use the 5S system effectively, they must be able to learn new skills.
In addition to improving efficiency, the 5S system also increases morale and teamwork among employees. Once they start to notice improvements, they are motivated to keep working towards their goal of increasing efficiency.