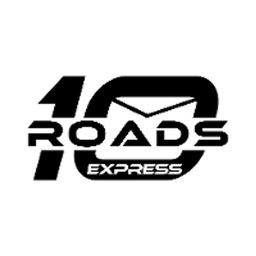
It is easy to forget, in a world of globalization and factory relocations to other countries that plenty of products are still being manufactured in America. Many of America's favorite products are made here, including candy, reliable vehicles and many of the country's most popular beers.
Find American-Made Products
Made in America, which is a powerful label in the industry, evokes patriotism as well as an unspoken promise to quality. It shows that the company values the safety of workers and the future.
It is important to also understand how the actual labeling of a product takes place. The Federal Trade Commission has guidelines that manufacturers must follow when using this phrase.
In general, it's only possible to claim that a product is made in America if all of the significant components, labor, and processing were done in the United States. A manufacturer can make a qualified claim, however, which lets consumers know that their item is made in the United States but only from certain foreign parts.
Julia Solomon Ensor of the FTC says that certain companies may not meet all these requirements when they advertise "Made in the USA". This is particularly true for products like gas grills that are assembled and shipped in the United States, but then sent to a distributor in another country.
The Federal Trade Commission has stepped up its crackdown on companies that make "Made in the USA” claims, but fail to meet the required standards. The agency says that the terms used must be clearly defined, and they must include all the components in the product.
Searching for items that were made in the United States can be done by both category and country. Shoppers who are looking for bedding or furnishings can browse our links and narrow their search by country.
If you're searching for a particular item, you can enter the name or company into the search box to find out if the product is manufactured in the United States. This is a way to show the companies you support that they should do more to promote American manufacturing.
Check out the Made in the USA Website from a business like Wayfair. It does a fantastic job at labeling the products by their country of origin. They even have a special section for items made in America.
You can easily find products made in the United States by visiting their websites. If you have questions about an item, please contact them via our link. The company will respond to your questions as quickly as possible.
It's worth checking these retailers out to see if you can find something you need for your home, whether it's clothing, toys, books, or anything else. Their site lists over 500 products as "Made In The USA". This is a great place to begin your search for American-made items.
FAQ
Why automate your warehouse?
Modern warehousing has seen automation take center stage. E-commerce has brought increased demand for more efficient and quicker delivery times.
Warehouses must be able to quickly adapt to changing demands. To do so, they must invest heavily in technology. Automation of warehouses offers many benefits. Here are some benefits of investing in automation
-
Increases throughput/productivity
-
Reduces errors
-
Increases accuracy
-
Boosts safety
-
Eliminates bottlenecks
-
Allows companies scale more easily
-
It makes workers more efficient
-
This gives you visibility into what happens in the warehouse
-
Enhances customer experience
-
Improves employee satisfaction
-
Reduces downtime and improves uptime
-
Ensures quality products are delivered on time
-
Human error can be eliminated
-
This helps to ensure compliance with regulations
Is it necessary to be familiar with Manufacturing Processes before we learn about Logistics.
No. No. Understanding the manufacturing process will allow you to better understand logistics.
What are the four types in manufacturing?
Manufacturing refers the process of turning raw materials into useful products with machines and processes. Manufacturing can include many activities such as designing and building, testing, packaging shipping, selling, servicing, and other related activities.
What are the 7 Rs of logistics?
The acronym "7R's" of Logistics stands for seven principles that underpin logistics management. It was published in 2004 by the International Association of Business Logisticians as part of their "Seven Principles of Logistics Management" series.
The acronym is made up of the following letters:
-
Responsible - to ensure that all actions are within the legal requirements and are not detrimental to others.
-
Reliable – have faith in your ability and capability to keep promises.
-
Be responsible - Use resources efficiently and avoid wasting them.
-
Realistic – consider all aspects of operations, from cost-effectiveness to environmental impact.
-
Respectful - treat people fairly and equitably.
-
Resourceful - look for opportunities to save money and increase productivity.
-
Recognizable - Provide value-added services to customers
How can we improve manufacturing efficiency?
First, we need to identify which factors are most critical in affecting production times. Next, we must find ways to improve those factors. If you don’t know where to begin, consider which factors have the largest impact on production times. Once you have identified them, it is time to identify solutions.
What is the role of a manager in manufacturing?
Manufacturing managers must ensure that manufacturing processes are efficient, effective, and cost-effective. They should be aware of any issues within the company and respond accordingly.
They should also learn how to communicate effectively with other departments, including sales and marketing.
They should also be aware of the latest trends in their industry and be able to use this information to help improve productivity and efficiency.
Statistics
- It's estimated that 10.8% of the U.S. GDP in 2020 was contributed to manufacturing. (investopedia.com)
- [54][55] These are the top 50 countries by the total value of manufacturing output in US dollars for its noted year according to World Bank.[56] (en.wikipedia.org)
- Job #1 is delivering the ordered product according to specifications: color, size, brand, and quantity. (netsuite.com)
- You can multiply the result by 100 to get the total percent of monthly overhead. (investopedia.com)
- According to the United Nations Industrial Development Organization (UNIDO), China is the top manufacturer worldwide by 2019 output, producing 28.7% of the total global manufacturing output, followed by the United States, Japan, Germany, and India.[52][53] (en.wikipedia.org)
External Links
How To
How to Use the Just-In-Time Method in Production
Just-in-time is a way to cut costs and increase efficiency in business processes. It's a way to ensure that you get the right resources at just the right time. This means that you only pay for what you actually use. Frederick Taylor, a 1900s foreman, first coined the term. He observed how workers were paid overtime if there were delays in their work. He realized that workers should have enough time to complete their jobs before they begin work. This would help increase productivity.
JIT is about planning ahead. You should have all the necessary resources ready to go so that you don’t waste money. Also, you should look at the whole project from start-to-finish and make sure you have the resources necessary to address any issues. You can anticipate problems and have enough equipment and people available to fix them. This will ensure that you don't spend more money on things that aren't necessary.
There are several types of JIT techniques:
-
Demand-driven JIT: This is a JIT that allows you to regularly order the parts/materials necessary for your project. This will allow you to track how much material you have left over after using it. You'll also be able to estimate how long it will take to produce more.
-
Inventory-based: This is a type where you stock the materials required for your projects in advance. This allows you to forecast how much you will sell.
-
Project-driven: This method allows you to set aside enough funds for your project. If you know the amount you require, you can buy the materials you need.
-
Resource-based JIT: This type of JIT is most commonly used. You allocate resources based on the demand. For example, if there is a lot of work coming in, you will have more people assigned to them. If you don't receive many orders, then you'll assign fewer employees to handle the load.
-
Cost-based: This approach is very similar to resource-based. However, you don't just care about the number of people you have; you also need to consider how much each person will cost.
-
Price-based: This is a variant of cost-based. However, instead of focusing on the individual workers' costs, this looks at the total price of the company.
-
Material-based is an alternative to cost-based. Instead of looking at the total cost in the company, this method focuses on the average amount of raw materials that you consume.
-
Time-based JIT: A variation on resource-based JIT. Instead of focusing on the cost of each employee, you will focus on the time it takes to complete a project.
-
Quality-based JIT is another variant of resource-based JIT. Instead of thinking about how much each employee costs or how long it takes to manufacture something, you think about how good the quality of your product is.
-
Value-based JIT: One of the most recent forms of JIT. You don't worry about whether the products work or if they meet customer expectations. Instead, you're focused on how much value you add to the market.
-
Stock-based. This method is inventory-based and focuses only on the actual production at any given point. This method is useful when you want to increase production while decreasing inventory.
-
Just-in-time planning (JIT): This is a combination JIT and supply-chain management. It is the process that schedules the delivery of components within a short time of their order. This is important as it reduces lead time and increases throughput.