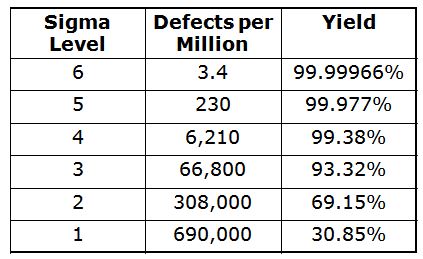
Tennessee is a state with a diverse and dynamic economy. It also offers many career options. Tennessee offers many career options, regardless of whether you're interested in a manufacturing job or something else.
Manufacturing Jobs In Tennessee
MNI has collected data showing that over 6109 companies in the state employ 408 131 workers. These companies make a wide variety of goods such as automotive and industrial parts, fabricated metal products, and industrial machinery.
Transportation Equipment Manufacturing: The largest industrial sector in the state, transportation equipment manufactures trucks and other vehicles and is also a major producer of commercial and military aircraft parts. Nissan has expanded its production in Smyrna, and Volkswagen has increased its production in Chattanooga.
Industrial Machinery: This sector is second in size only to transportation equipment. It produces parts for many industries including agriculture, defence and energy. DENSO Manufacturing Tennessee is located in Maryville. Maremont Exhaust Products is in Loudon.
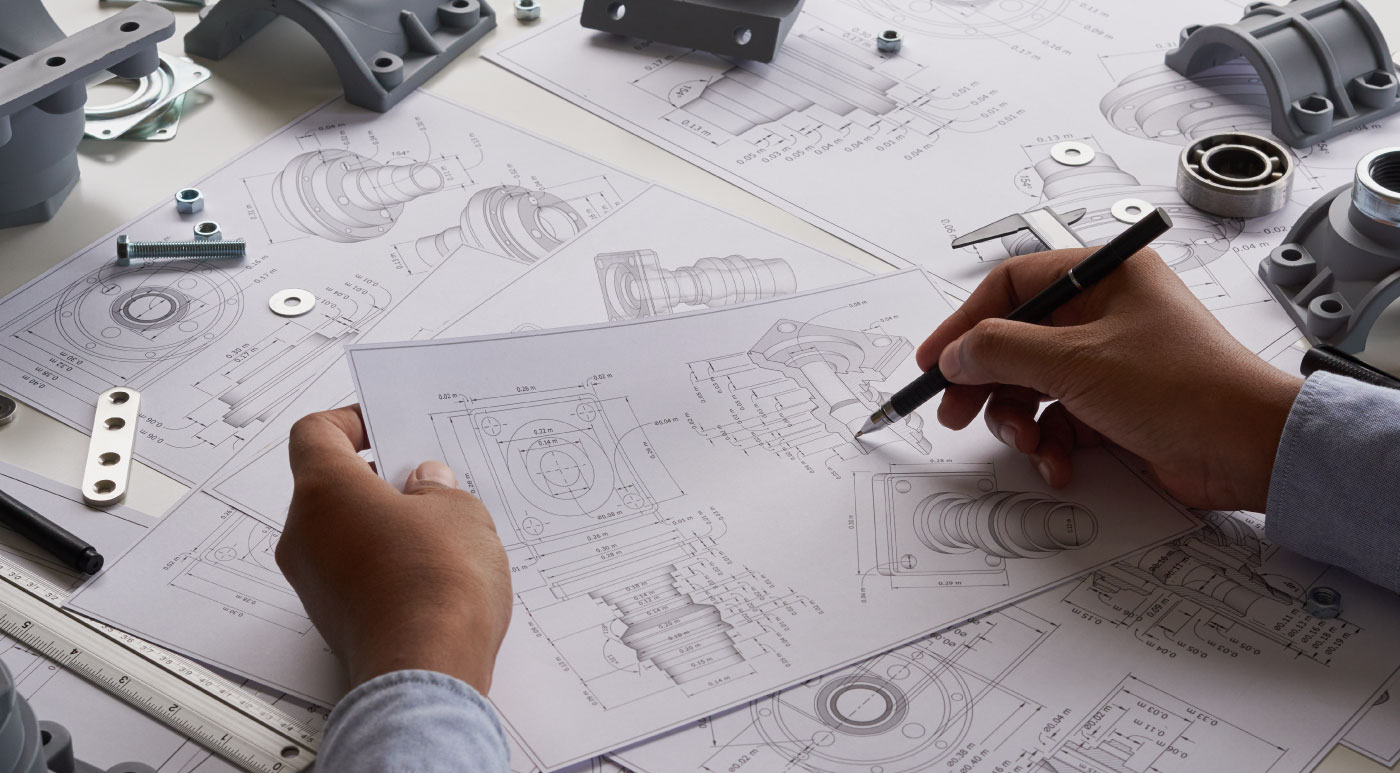
Food Processing: The third largest industrial sector, food processing includes producers of foods such as Little Debbie snack cakes and Drake's Devil Dogs. These companies employ a wide range of workers including production workers and packaging specialists.
Advanced Manufacturing is the fourth largest sector of the state economy. This field has more than 32,000 newly created jobs. Eastman Chemicals Consolidated Nuclear Security McKee Foods and McKee are three of the biggest employers in the sector.
Find a factory job in Tennessee.
The best way to start a manufacturing career in the state is through an apprenticeship or training program. These programs are designed for you to get practical experience in one area of the manufacturing process. These courses typically focus on a particular skill, such as welding or electrical work, and can be customized to suit your interests and qualifications.
Some programs cover a broader area such as manufacturing or quality management. These programs are usually taught by community colleges or other providers of training.
Those who are interested in pursuing a career in manufacturing can also look for manufacturing jobs through online job boards and classified ads. These sites offer a wealth of information about a range of companies and allow you to submit applications without having to speak to hiring managers.
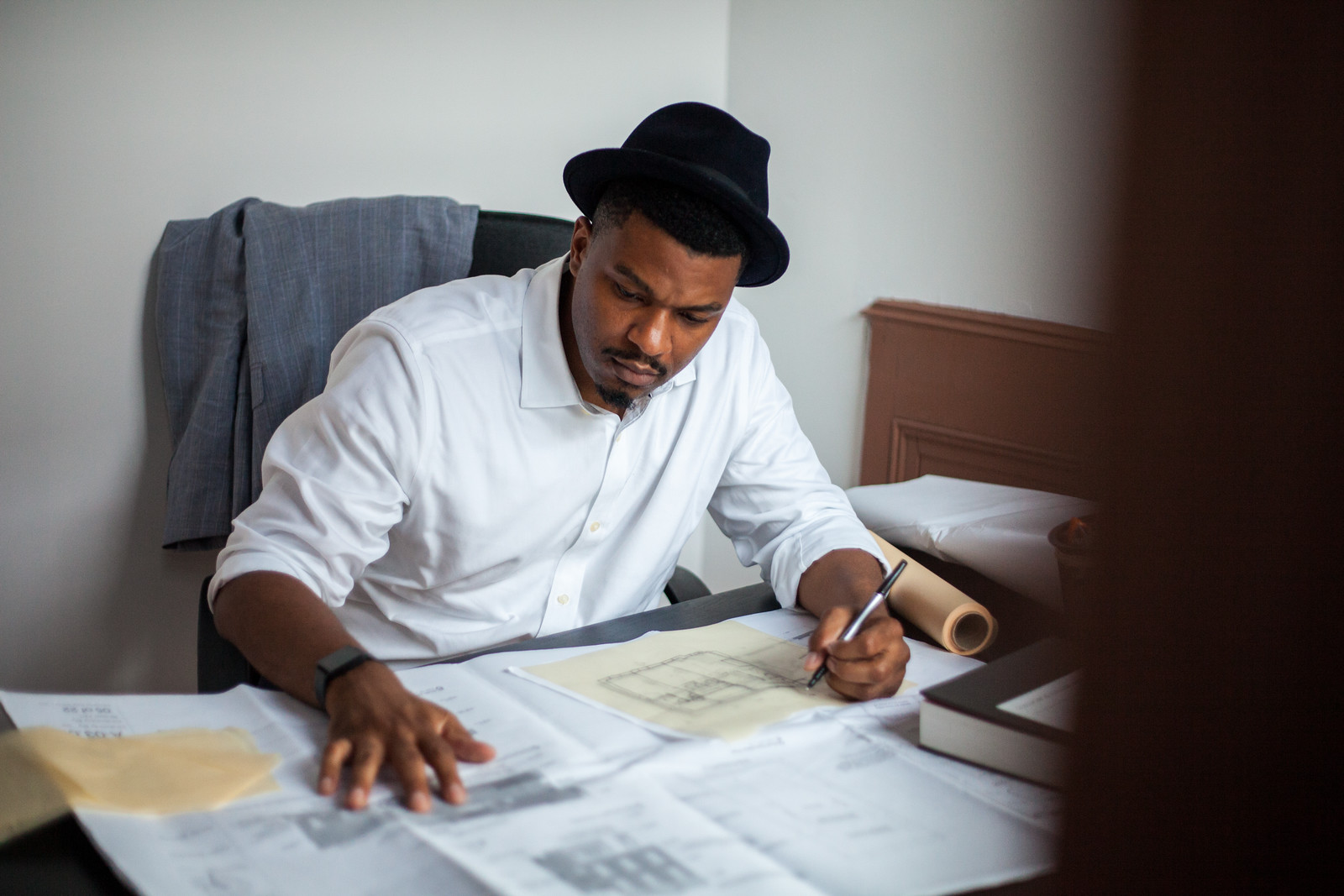
To find a position in the manufacturing industry, you should start by checking out the careers page on a website for a local or a national employer. This site can usually provide you with an overview of the company and a list of current open positions.
Other resources for finding a job in the manufacturing industry can include attending job fairs, which often offer opportunities to interview with multiple different companies. But these events can be hard to find, and may only represent a small portion of the available manufacturing jobs in your area.
FAQ
Why automate your warehouse
Automation has become increasingly important in modern warehousing. The rise of e-commerce has led to increased demand for faster delivery times and more efficient processes.
Warehouses have to be flexible to meet changing requirements. To do so, they must invest heavily in technology. Automation of warehouses offers many benefits. Here are some reasons why it's worth investing in automation:
-
Increases throughput/productivity
-
Reduces errors
-
Accuracy is improved
-
Safety increases
-
Eliminates bottlenecks
-
Allows companies scale more easily
-
Workers are more productive
-
Provides visibility into everything that happens in the warehouse
-
Enhances customer experience
-
Improves employee satisfaction
-
Reduces downtime and improves uptime
-
You can be sure that high-quality products will arrive on time
-
Removing human error
-
It ensures compliance with regulations
What are the responsibilities for a manufacturing manager
The manufacturing manager should ensure that every manufacturing process is efficient and effective. They must also be alert to any potential problems and take appropriate action.
They should also learn how to communicate effectively with other departments, including sales and marketing.
They should also be knowledgeable about the latest trends in the industry so they can use this information for productivity and efficiency improvements.
What are the goods of logistics?
Logistics are the activities involved in moving goods from point A to point B.
They encompass all aspects transport, including packaging and loading, transporting, storage, unloading.
Logisticians ensure that the right product reaches the right place at the right time and under safe conditions. They assist companies with their supply chain efficiency through information on demand forecasts. Stock levels, production times, and availability.
They monitor shipments in transit, ensure quality standards, manage inventories, replenish orders, coordinate with suppliers and other vendors, and offer support services for sales, marketing, and customer service.
Why is logistics important in manufacturing?
Logistics are an integral part any business. They help you achieve great results by helping you manage all aspects of product flow, from raw materials to finished goods.
Logistics also play a major role in reducing costs and increasing efficiency.
What is production planning?
Production Planning involves developing a plan for all aspects of the production, including scheduling, budgeting, casting, crew, location, equipment, props, etc. This document will ensure everything is in order and ready to go when you need it. It should also contain information on achieving the best results on set. This includes shooting schedules, locations, cast lists, crew details, and equipment requirements.
It is important to first outline the type of film you would like to make. You may have decided where to shoot or even specific locations you want to use. Once you have identified the scenes and locations, you can start to determine which elements are required for each scene. For example, you might decide that you need a car but don't know exactly what model you want. If this is the case, you might start searching online for car models and then narrow your options by selecting from different makes.
After you've found the perfect car, it's time to start thinking about adding extras. Are you looking for people to sit in the front seats? Or maybe you just need someone to push the car around. You might want to change your interior color from black and white. These questions will help guide you in determining the ideal look and feel for your car. It is also worth considering the types of shots that you wish to take. What type of shots will you choose? Maybe you want the engine or the steering wheels to be shown. These details will help identify the exact car you wish to film.
Once you have established all the details, you can create a schedule. You can create a schedule that will outline when you must start and finish your shoots. The schedule will show you when to get there, what time to leave, and when to return home. So everyone is clear about what they need to do. Hire extra staff by booking them ahead of time. It is not worth hiring someone who won’t show up because you didn’t tell him.
Also, consider how many days you will be filming your schedule. Some projects may only take a couple of days, while others could last for weeks. When creating your schedule, be aware of whether you need more shots per day. Multiple takes of the same location will lead to higher costs and take more time. It is better to be cautious and take fewer shots than you risk losing money if you are not sure if multiple takes are necessary.
Budgeting is another important aspect of production planning. You will be able to manage your resources if you have a realistic budget. You can always lower the budget if you encounter unexpected problems. It is important to not overestimate how much you will spend. If you underestimate how much something costs, you'll have less money to pay for other items.
Production planning is a detailed process. But, once you understand the workings of everything, it becomes easier for future projects to be planned.
What does the term manufacturing industries mean?
Manufacturing Industries are businesses that produce products for sale. Consumers are the people who purchase these products. This is accomplished by using a variety of processes, including production, distribution and retailing. They manufacture goods from raw materials using machines and other equipment. This includes all types of manufactured goods, including food items, clothing, building supplies, furniture, toys, electronics, tools, machinery, vehicles, pharmaceuticals, medical devices, chemicals, and many others.
What are the responsibilities of a production planner
Production planners ensure that all project aspects are completed on time, within budget and within the scope. A production planner ensures that the service and product meet the client's expectations.
Statistics
- It's estimated that 10.8% of the U.S. GDP in 2020 was contributed to manufacturing. (investopedia.com)
- [54][55] These are the top 50 countries by the total value of manufacturing output in US dollars for its noted year according to World Bank.[56] (en.wikipedia.org)
- Job #1 is delivering the ordered product according to specifications: color, size, brand, and quantity. (netsuite.com)
- According to a Statista study, U.S. businesses spent $1.63 trillion on logistics in 2019, moving goods from origin to end user through various supply chain network segments. (netsuite.com)
- (2:04) MTO is a production technique wherein products are customized according to customer specifications, and production only starts after an order is received. (oracle.com)
External Links
How To
How to use 5S to increase Productivity in Manufacturing
5S stands for "Sort", 'Set In Order", 'Standardize', & Separate>. Toyota Motor Corporation was the first to develop the 5S approach in 1954. This methodology helps companies improve their work environment to increase efficiency.
The basic idea behind this method is to standardize production processes, so they become repeatable, measurable, and predictable. This means that daily tasks such as cleaning and sorting, storage, packing, labeling, and packaging are possible. This knowledge allows workers to be more efficient in their work because they are aware of what to expect.
Implementing 5S requires five steps. These are Sort, Set In Order, Standardize. Separate. And Store. Each step has a different action and leads to higher efficiency. By sorting, for example, you make it easy to find the items later. When items are ordered, they are put together. After you have divided your inventory into groups you can store them in easy-to-reach containers. Make sure everything is correctly labeled when you label your containers.
Employees need to reflect on how they do their jobs. Employees must be able to see why they do what they do and find a way to achieve them without having to rely on their old methods. To be successful in the 5S system, employees will need to acquire new skills and techniques.
The 5S method not only increases efficiency but also boosts morale and teamwork. They are more motivated to achieve higher efficiency levels as they start to see improvement.