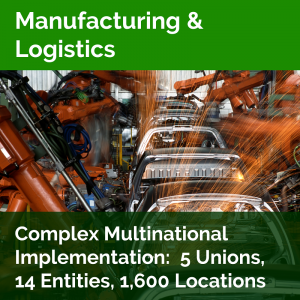
A job director is responsible for job manufacturing. The responsibilities and duties of a job manager are the same as those of a manufacturing associate. This article will cover the requirements for a job manager in manufacturing. The job requires a skilled workforce to handle various operations. A flexible workflow is essential as it helps to track development and manage projects. This type of production line demands a skilled workforce. It requires employees who can keep up with the pace, and be able deliver quality products on-time.
The job of a job director in manufacturing
A job director of manufacturing oversees the daily operations and management of a manufacturing unit. They ensure that products are finished on time and at a high quality standard. To create a new product, a director of manufacturing must collaborate closely with engineers and designers. They must also evaluate the product's feasibility, market fit, and impact on processes and quality before it goes into large-scale production. Also, a director in manufacturing must be able to demonstrate leadership skills. They should be able to mentor employees under their supervision and implement improvements to processes and equipment.
Directors of manufacturing typically have a bachelor's degree. However, employers will prefer to hire qualified candidates. Directors of manufacturing should have at minimum five years' experience working in management. Candidates must be able adapt to a fast learning curve.
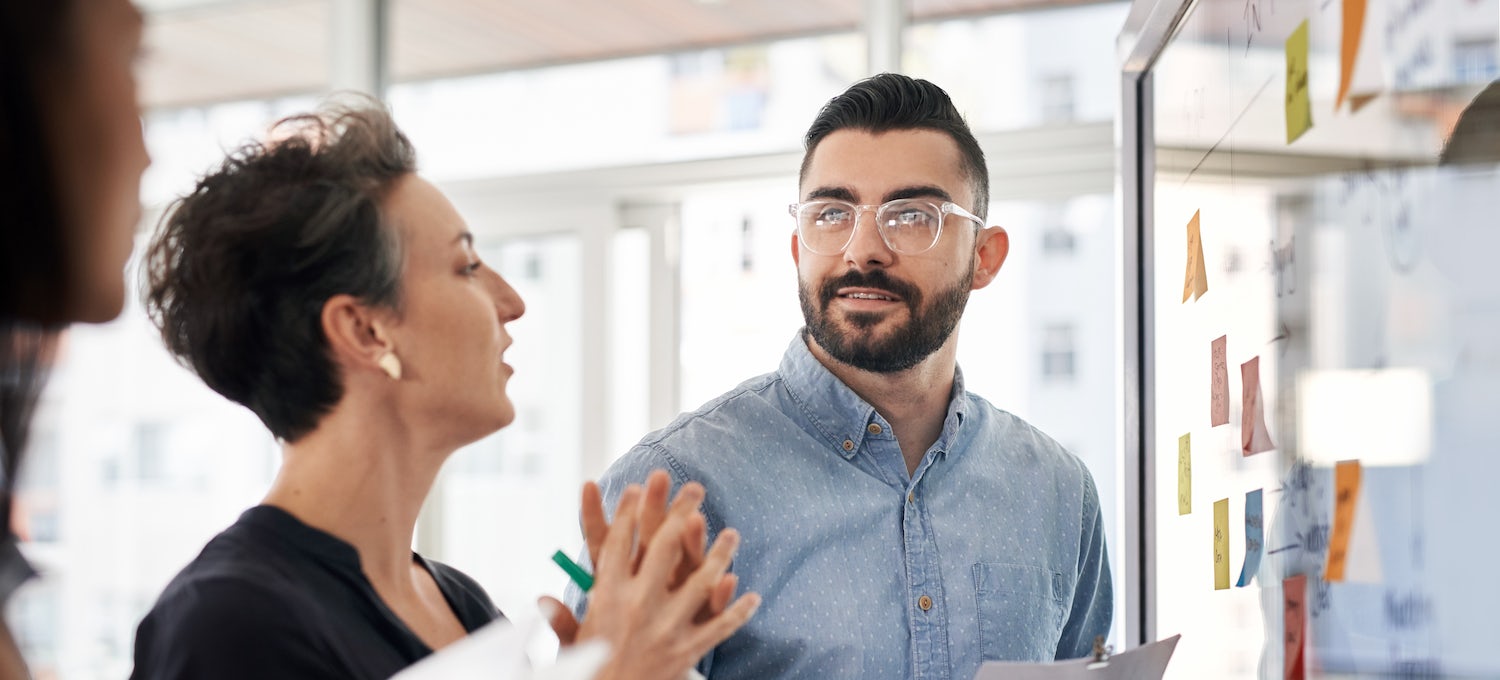
Duties of a manufacturing associate
Manufacturing associates can have many duties, but they are often required to perform repetitive tasks and assembly line work. To avoid injury, associates need to be strong in their body mechanics. They may also have to lift heavy materials or stand for long periods of time.
Duties of a manufacturing associate can range from inspecting parts to reading engineering drawings and executing manufacturing documents. They also have to coordinate with other members of the team and produce reports. You will need to be organized, detail-oriented and good communicators.
Also, quality control is a major responsibility. They should be familiar with the manufacturing process and be able determine if products meet company standards. They will also need to observe the final products and detect any quality issues.
Qualifications for a job as a director of manufacturing
As a director of manufacturing, your job will require you to be responsible for managing all manufacturing units. In this role, you will need to maintain high standards of quality, as well as implementing and evaluating new ideas and techniques to cut costs. You will also have to evaluate the performance of your staff. For a job as a director in manufacturing, you will need to demonstrate leadership, organizational skills and problem solving.
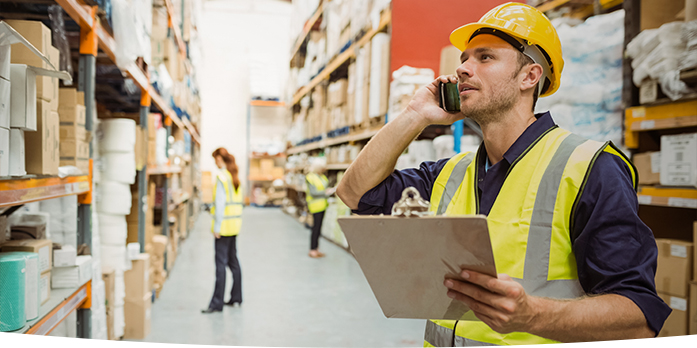
As a manufacturing director you will work alongside engineers and designers in order to develop products for companies. To ensure everyone understands their roles and is on the same page, you will need excellent communication skills. You will be able manage the company effectively if you can communicate well. Additionally, you will be required to coach and mentor the employees under your direction as a director in manufacturing. As an example, you'll need to give training to employees about safety protocols, risk mitigation and new equipment.
FAQ
What does it mean to warehouse?
A warehouse is a place where goods are stored until they are sold. It can be an indoor space or an outdoor area. In some cases, it may be a combination of both.
What is the job of a logistics manger?
A logistics manager makes sure that all goods are delivered on-time and in good condition. This is accomplished by using the experience and knowledge gained from working with company products. He/she also needs to ensure adequate stock to meet demand.
How is a production manager different from a producer planner?
The main difference between a production planner and a project manager is that a project manager is usually the person who plans and organizes the entire project, whereas a production planner is mainly involved in the planning stage of the project.
Is automation important for manufacturing?
Not only are service providers and manufacturers important, but so is automation. They can provide services more quickly and efficiently thanks to automation. They can also reduce their costs by reducing human error and improving productivity.
Is it necessary to be familiar with Manufacturing Processes before we learn about Logistics.
No. No. But, being familiar with manufacturing processes will give you a better understanding about how logistics works.
What are the 7 Rs of logistics?
The acronym 7R's for Logistics stands to represent the seven basic principles in logistics management. It was created by the International Association of Business Logisticians and published in 2004 under its "Seven Principles of Logistics Management".
The acronym is made up of the following letters:
-
Responsible - ensure that all actions taken are within legal requirements and are not harmful to others.
-
Reliable: Have faith in your ability or the ability to honor any promises made.
-
Reasonable - use resources efficiently and don't waste them.
-
Realistic – Consider all aspects, including cost-effectiveness as well as environmental impact.
-
Respectful - Treat people fairly and equitably
-
You are resourceful and look for ways to save money while increasing productivity.
-
Recognizable - Provide value-added services to customers
How can manufacturing overproduction be reduced?
In order to reduce excess production, you need to develop better inventory management methods. This would reduce the time needed to manage inventory. We could use these resources to do other productive tasks.
You can do this by adopting a Kanban method. A Kanban board, a visual display to show the progress of work, is called a Kanban board. In a Kanban system, work items move through a sequence of states until they reach their final destination. Each state represents a different priority.
To illustrate, work can move from one stage or another when it is complete enough for it to be moved to a new stage. A task that is still in the initial stages of a process will be considered complete until it moves on to the next stage.
This allows work to move forward and ensures that no work is missed. A Kanban board allows managers to monitor how much work is being completed at any given moment. This information allows managers to adjust their workflow based off real-time data.
Lean manufacturing is another way to manage inventory levels. Lean manufacturing seeks to eliminate waste from every step of the production cycle. Anything that does not contribute to the product's value is considered waste. These are some of the most common types.
-
Overproduction
-
Inventory
-
Unnecessary packaging
-
Material surplus
Manufacturers can reduce their costs and improve their efficiency by using these ideas.
Statistics
- [54][55] These are the top 50 countries by the total value of manufacturing output in US dollars for its noted year according to World Bank.[56] (en.wikipedia.org)
- Job #1 is delivering the ordered product according to specifications: color, size, brand, and quantity. (netsuite.com)
- According to a Statista study, U.S. businesses spent $1.63 trillion on logistics in 2019, moving goods from origin to end user through various supply chain network segments. (netsuite.com)
- You can multiply the result by 100 to get the total percent of monthly overhead. (investopedia.com)
- In 2021, an estimated 12.1 million Americans work in the manufacturing sector.6 (investopedia.com)
External Links
How To
Six Sigma: How to Use it in Manufacturing
Six Sigma is defined by "the application SPC (statistical process control) techniques to achieve continuous improvements." Motorola's Quality Improvement Department, Tokyo, Japan, developed it in 1986. The basic idea behind Six Sigma is to improve quality by improving processes through standardization and eliminating defects. In recent years, many companies have adopted this method because they believe there is no such thing as perfect products or services. Six Sigma aims to reduce variation in the production's mean value. This means that you can take a sample from your product and then compare its performance to the average to find out how often the process differs from the norm. If the deviation is excessive, it's likely that something needs to be fixed.
Understanding how your business' variability is a key step towards Six Sigma implementation is the first. Once you've understood that, you'll want to identify sources of variation. These variations can also be classified as random or systematic. Random variations are caused when people make mistakes. While systematic variations are caused outside of the process, they can occur. Random variations would include, for example, the failure of some widgets to fall from the assembly line. If however, you notice that each time you assemble a widget it falls apart in exactly the same spot, that is a problem.
Once you've identified where the problems lie, you'll want to design solutions to eliminate those problems. That solution might involve changing the way you do things or redesigning the process altogether. Test them again once you've implemented the changes. If they fail, you can go back to the drawing board to come up with a different plan.