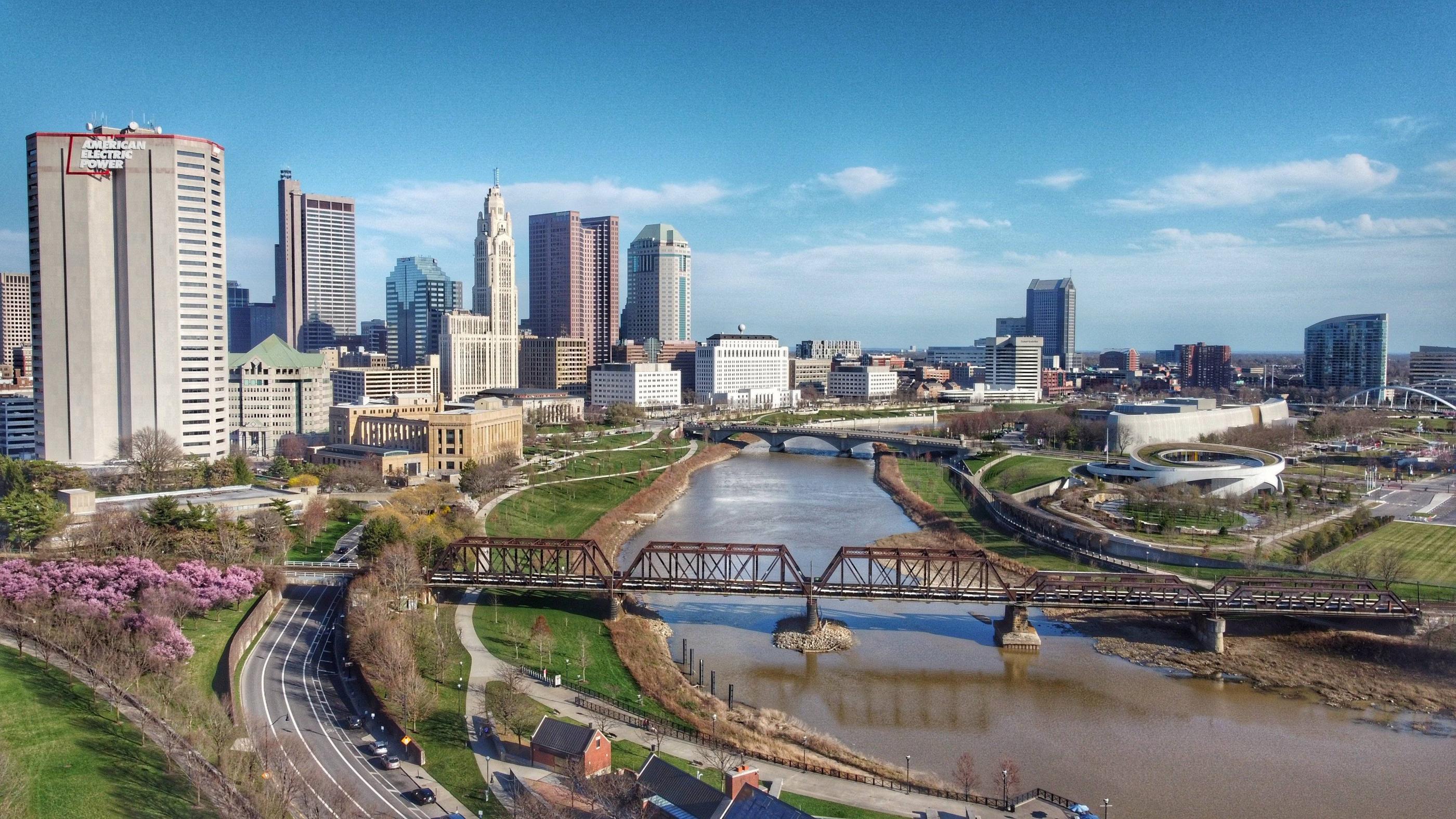
Among the tools in the lean toolbox are Hoshin Kanri, Visual board, Value Stream Mapping, and Process Observation and Analysis. These methods combine statistical data with quality control measures to improve process performance and reduce defects. Lean tools also help improve the safety and health of employees, cycle time, delivery time, and raw material quality. Check out our articles about lean tools for more information. We provide examples and explain some of the basics.
Hoshin Kari
Communication is key when it comes down to communicating the goals of each division to one another in order to implement the principles of Hoshin Kari. It is important to communicate clearly your company's objectives as well as the results that they produce. Google Images will allow you to view a sample Hoshin Kanri diagram. The idea behind the Hoshinkanri matrix is to ensure everyone is on the same page and can work together towards common goals.
Hoshin Kanri is an inclusive approach that will help you determine what areas of your business are in need of improvement. You can identify the specific activities that need improvement and create a clear plan from general goals to take concrete steps. It can help you visualize the relationship between each step and how it relates to others. Hoshin Kanri encourages the use of a collaborative approach in order to improve the overall company.
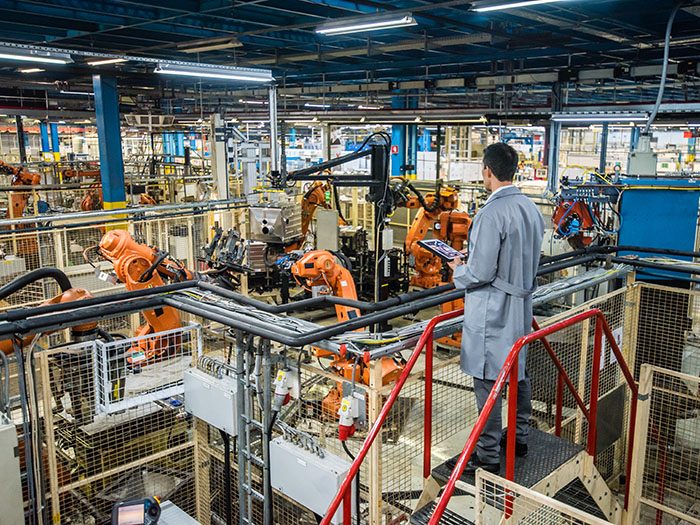
Visual board
Although the visual board is an effective tool to track the progress of a process it is not universal. You cannot use it as a tool if the implementation involves people. To create emotion behind the numbers, a visual management board must be made for each user. You can use it to track performance indicators such as the number of pieces produced in a given time or the hours worked. It is possible to use this tool in lean production environments, but there are key elements.
A visual management board's key feature is its ability to quickly communicate with all members of a team about what needs to happen and who is responsible. This information is easily viewed on the board in under 20 seconds. The results of these activities must also be visible to management to ensure that everyone is on the same page. Regular updates can be made to the visual management boards in order to ensure that everyone is on a similar page.
Value Stream Mapping
The facilitator must identify the bottleneck or constraint when value stream mapping is used in tools lean. A bottleneck would be the process step with the greatest WIP. A three-step process with a throughput rate 60 units/hour and a potential work in progress (WIP) of 42 units/hour would be a bottleneck. Step 2 would then be the bottleneck. The value stream map is a tool that can be used to identify bottlenecks and help you find ways to improve your process.
A value stream mapping is only possible if you understand the customer's perspective and the system. This is often a multi-functional and complex process. This may require extensive involvement and training. A value stream manager might be hired by larger companies to oversee the mapping. While value stream mapping can be a large project, even smaller projects can identify opportunities for improvement and save money. A powerful tool in tools Lean is value stream mapping.
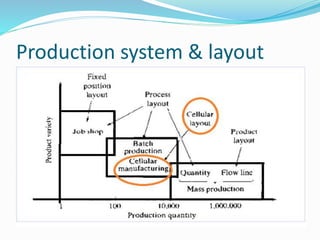
Process Observation and Analysis
Lean management centers on continuous improvement as well as process observation. Process observation is designed to maintain standards and ensure processes produce the expected outcomes. In the end, abandoned processes will become less efficient. Process observation and analysis can have cultural implications, so managers need to clearly explain the need for process observation and the benefits it provides. Managers must explain why process observation and analysis are important to their organization and their employees.
The first step in Lean implementation is to validate the process flow map through a walk-through. Once this step is verified, the next step is to analyze the data gathered. The Measure phase involves gathering data on the current product, process, or service. The project leader applies statistical hypotheses testing techniques to pinpoint the root cause. This analysis helps to determine if the problem is solved or improved.
FAQ
What does manufacturing industry mean?
Manufacturing Industries are companies that manufacture products. Consumers are those who purchase these products. These companies use various processes such as production, distribution, retailing, management, etc., to fulfill this purpose. They make goods from raw materials with machines and other equipment. This includes all types of manufactured goods, including food items, clothing, building supplies, furniture, toys, electronics, tools, machinery, vehicles, pharmaceuticals, medical devices, chemicals, and many others.
What do we need to know about Manufacturing Processes in order to learn more about Logistics?
No. No. It is important to know about the manufacturing processes in order to understand how logistics works.
What are the essential elements of running a logistics firm?
A successful logistics business requires a lot more than just knowledge. Good communication skills are essential to effectively communicate with your suppliers and clients. You will need to know how to interpret data and draw conclusions. You must be able and able to handle stress situations and work under pressure. You need to be innovative and creative to come up with new ways to increase efficiency. To motivate and guide your team towards reaching organizational goals, you must have strong leadership skills.
You should also be organized and efficient to meet tight deadlines.
What is the difference between Production Planning, Scheduling and Production Planning?
Production Planning (PP) refers to the process of determining how much production is needed at any given moment. This is accomplished by forecasting the demand and identifying production resources.
Scheduling involves the assignment of dates and times to tasks in order to complete them within the timeframe.
Statistics
- Many factories witnessed a 30% increase in output due to the shift to electric motors. (en.wikipedia.org)
- In the United States, for example, manufacturing makes up 15% of the economic output. (twi-global.com)
- You can multiply the result by 100 to get the total percent of monthly overhead. (investopedia.com)
- Job #1 is delivering the ordered product according to specifications: color, size, brand, and quantity. (netsuite.com)
- (2:04) MTO is a production technique wherein products are customized according to customer specifications, and production only starts after an order is received. (oracle.com)
External Links
How To
How to Use Six Sigma in Manufacturing
Six Sigma is "the application statistical process control (SPC), techniques for continuous improvement." Motorola's Quality Improvement Department created Six Sigma at their Tokyo plant, Japan in 1986. Six Sigma's main goal is to improve process quality by standardizing processes and eliminating defects. Many companies have adopted this method in recent years. They believe there is no such thing a perfect product or service. The main goal of Six Sigma is to reduce variation from the mean value of production. If you take a sample and compare it with the average, you will be able to determine how much of the production process is different from the norm. If you notice a large deviation, then it is time to fix it.
Understanding the nature of variability in your business is the first step to Six Sigma. Once you have this understanding, you will need to identify sources and causes of variation. It is important to identify whether the variations are random or systemic. Random variations occur when people make mistakes; systematic ones are caused by factors outside the process itself. If you make widgets and some of them end up on the assembly line, then those are considered random variations. You might notice that your widgets always fall apart at the same place every time you put them together.
After identifying the problem areas, you will need to devise solutions. That solution might involve changing the way you do things or redesigning the process altogether. After implementing the new changes, you should test them again to see if they worked. If they don't work you need to rework them and come up a better plan.