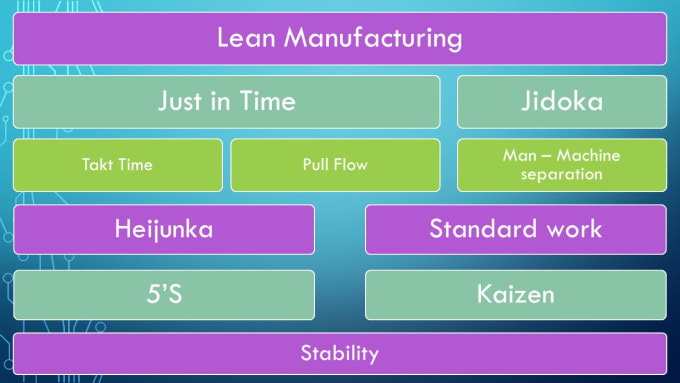
The Lean 5 principles stress the elimination of all waste, even those that don't add value to the product. Value stream mapping is also encouraged by the principles to help identify more efficient activities. To eliminate waste, you must distinguish value-added (necessary), from non-value–added (unnecessary). By eliminating unnecessary steps, a more efficient process can be created that consumes the least time, energy, materials, and is also less costly. This ensures that customers are satisfied and high quality products are produced in the shortest time possible.
Value
The Value of Lean 5 principles helps you improve the flow of your manufacturing processes by eliminating waste. It's possible to make production and shipping smoother by eliminating unnecessary steps. This process helps reduce inventory, saves time and eliminates work in progress.
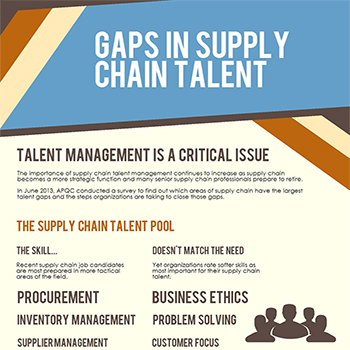
Value stream
Lean manufacturing uses the value stream to reduce waste. This method maps each step of a manufacturing process to identify those elements that are essential and eliminate those that don't. The value stream considers the entire product's lifecycle, from its conception to its disposal. Understanding this process is the key to eliminating waste. There are three types of waste in a value stream.
Flow
The first of the five lean principles, flow, involves identifying customer needs and evaluating those. This is essential for designing new products and services as customers may not always be able to express their needs clearly. The second step involves defining the value stream or the sequence of activities that will complete a project. This is an essential part of lean project management and requires close collaboration with all participants.
Pull
In a pull-system, a process starts only when there's a customer order. A pizza restaurant wouldn't make extra pizzas unless they received a order from a customer. Otherwise, they would be wasting time, resources, and ingredients.
Perfection
One of the five lean principles is perfection. Perfection is a state of being complete, exact, consistent. However, achieving perfection is an elusive goal. The purpose of this concept is to encourage continuous improvement. The result is a better performance for organizations.
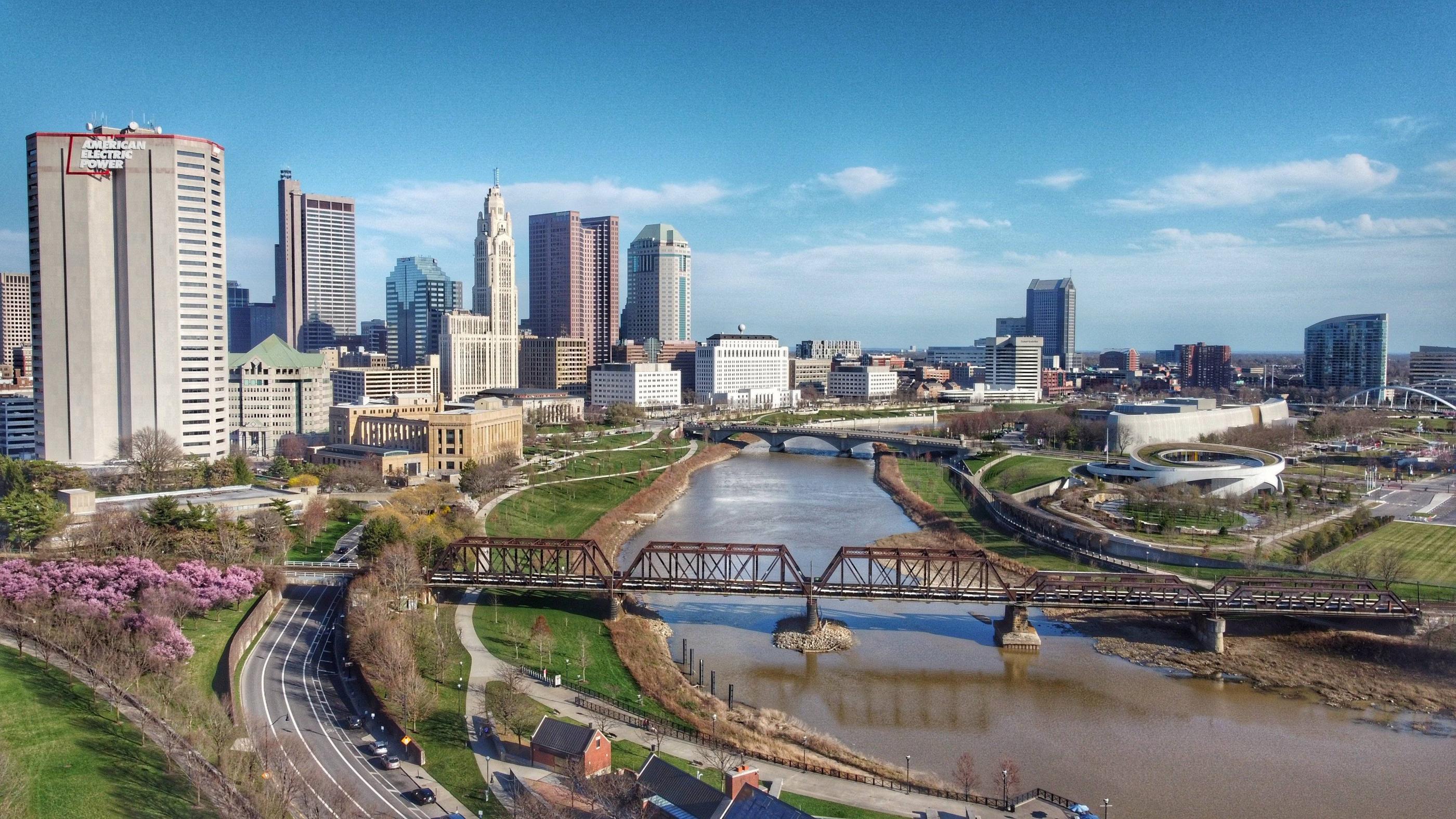
Collaboration between stakeholders
Stakeholder collaboration is a key element of lean project management. It is the collaboration of project team members to solve project problems and increase project value. Teams must identify the problems and areas that need improvement in order to plan. The doing stage is more about data gathering and execution than it is about executing. The organizational structure is also important for team collaboration.
FAQ
What are the 7 R's of logistics?
The acronym "7R's" of Logistics stands for seven principles that underpin logistics management. It was created by the International Association of Business Logisticians and published in 2004 under its "Seven Principles of Logistics Management".
The following letters make up the acronym:
-
Responsible - ensure that actions are in compliance with legal requirements and do not cause harm to others.
-
Reliable: Have faith in your ability or the ability to honor any promises made.
-
Reasonable - use resources efficiently and don't waste them.
-
Realistic - Take into consideration all aspects of operations including cost-effectiveness, environmental impact, and other factors.
-
Respectful - Treat people fairly and equitably
-
Be resourceful: Look for opportunities to save money or increase productivity.
-
Recognizable is a company that provides customers with value-added solutions.
Is there anything we should know about Manufacturing Processes prior to learning about Logistics.
No. No. However, knowing about manufacturing processes will definitely give you a better understanding of how logistics works.
What is the responsibility of a manufacturing manager?
A manufacturing manager has to ensure that all manufacturing processes work efficiently and effectively. They should be aware of any issues within the company and respond accordingly.
They should also learn how to communicate effectively with other departments, including sales and marketing.
They should also be aware of the latest trends in their industry and be able to use this information to help improve productivity and efficiency.
What is the role of a logistics manager
A logistics manager ensures that all goods are delivered on time and without damage. This is achieved by using their knowledge and experience with the products of the company. He/she must also ensure sufficient stock to meet the demand.
What does it mean to be a manufacturer?
Manufacturing Industries refers to businesses that manufacture products. Consumers are people who purchase these goods. These companies employ many processes to achieve this purpose, such as production and distribution, retailing, management and so on. They make goods from raw materials with machines and other equipment. This includes all types if manufactured goods.
Statistics
- According to the United Nations Industrial Development Organization (UNIDO), China is the top manufacturer worldwide by 2019 output, producing 28.7% of the total global manufacturing output, followed by the United States, Japan, Germany, and India.[52][53] (en.wikipedia.org)
- [54][55] These are the top 50 countries by the total value of manufacturing output in US dollars for its noted year according to World Bank.[56] (en.wikipedia.org)
- According to a Statista study, U.S. businesses spent $1.63 trillion on logistics in 2019, moving goods from origin to end user through various supply chain network segments. (netsuite.com)
- Many factories witnessed a 30% increase in output due to the shift to electric motors. (en.wikipedia.org)
- In 2021, an estimated 12.1 million Americans work in the manufacturing sector.6 (investopedia.com)
External Links
How To
How to Use Six Sigma in Manufacturing
Six Sigma is defined as "the application of statistical process control (SPC) techniques to achieve continuous improvement." Motorola's Quality Improvement Department in Tokyo, Japan developed Six Sigma in 1986. Six Sigma's basic concept is to improve quality and eliminate defects through standardization. In recent years, many companies have adopted this method because they believe there is no such thing as perfect products or services. Six Sigma seeks to reduce variation between the mean production value. You can calculate the percentage of deviation from the norm by taking a sample of your product and comparing it to the average. If this deviation is too big, you know something needs fixing.
Understanding the dynamics of variability within your business is the first step in Six Sigma. Once you've understood that, you'll want to identify sources of variation. You'll also want to determine whether these variations are random or systematic. Random variations happen when people make errors; systematic variations are caused externally. For example, if you're making widgets, and some of them fall off the assembly line, those would be considered random variations. You might notice that your widgets always fall apart at the same place every time you put them together.
Once you've identified the problem areas you need to find solutions. It might mean changing the way you do business or redesigning it entirely. To verify that the changes have worked, you need to test them again. If they don't work, you will need to go back to the drawing boards and create a new plan.