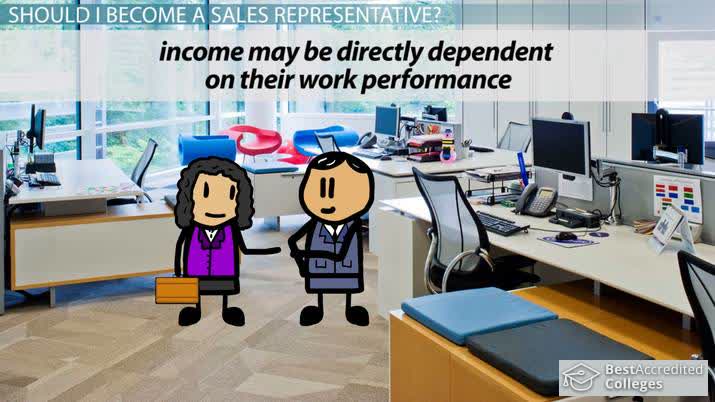
Look for opportunities in supply chain management if you're looking to pursue a career in this field. You will need to know how many people are working in the particular industry, what skills they require, and what type of jobs are out there. When it comes to job search, you can connect with recruiters or human resource professionals. Depending upon your goals, you might also consider joining a professional group to learn about certification programs.
Supply chain management can be a dynamic field that requires a broad range of skills. It may seem difficult and complex, but it's also extremely rewarding. You have many options and flexibility, and the opportunity to apply your skills across a range of industries.
Logistics and supply chain management require critical thinking, project management, interpersonal communications, and sustainability skills. They also need to be able interact with stakeholders at all levels. They must be able understand and implement international regulations as well as new technologies.
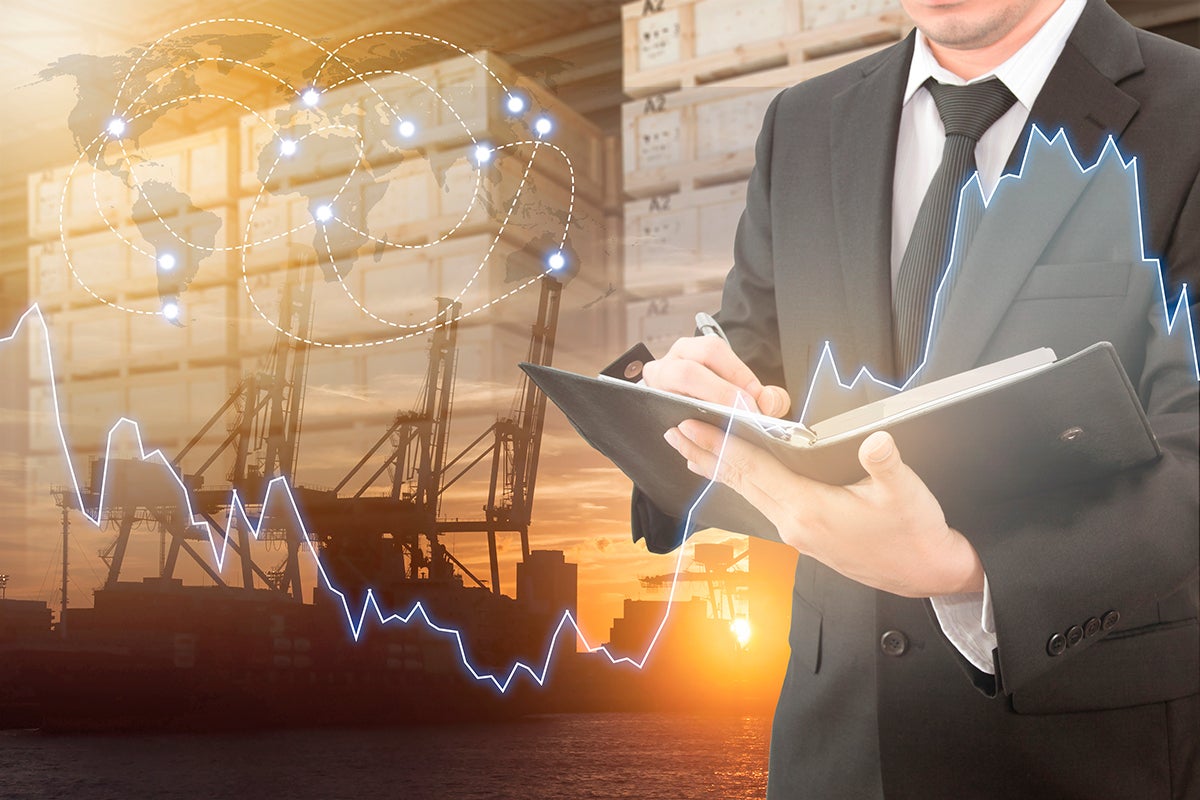
Companies today look at their supply chains from a larger perspective. You'll see that not all supply chains are the same. One company might have multiple product areas that you can work on while another family-owned business may offer fewer career advancement options. Your satisfaction can also be affected greatly by the company's size.
You will need to establish a strong network in order to get started. You should get to know supply chain managers and HR professionals. Also, learn about the industries that are of interest to you. Once you have established a strong network, you are ready to look for a position in the supply chain. Most supply chain jobs are competitive, and you'll have to show that you have the requisite expertise and experience.
Supply chain management is unpredictable and fast-paced. You must be flexible and be able solve problems quickly. If you are able to solve problems quickly, you can avoid interruptions in your supply chain. This will help you achieve your goals.
As part of a supply-chain career, you will also need to organize and collect data. This knowledge is vital for making decisions and allocating staff resources effectively. For all processes involved in serving customers, data collection and management must be done well.
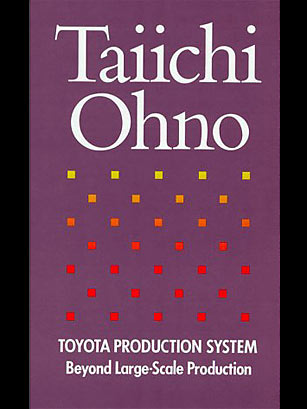
The supply chain manager should also be capable of managing projects and managing finances. Although they may be responsible for managing several projects simultaneously, they should also be able decide which ones to prioritize. They'll need to weigh the pros and cons of each decision.
For those who want to pursue a supply chain management career, you can find positions in retail, healthcare, transportation, manufacturing, and food service. The salary and job opportunities for these positions are varied. For each industry, you will need to possess a minimum of three years of experience.
Supply chain management is a growing field, and there are plenty of jobs for you to consider. You can use what you love about working with people to make a career out of this fast-paced field.
FAQ
How can we increase manufacturing efficiency?
First, we need to identify which factors are most critical in affecting production times. We must then find ways that we can improve these factors. If you don’t know how to start, look at which factors have the greatest impact upon production time. Once you've identified them, try to find solutions for each of those factors.
What does it take for a logistics enterprise to succeed?
You need to have a lot of knowledge and skills to manage a successful logistic business. You must have good communication skills to interact effectively with your clients and suppliers. You should be able analyse data and draw inferences. You must be able manage stress and pressure under pressure. To improve efficiency, you must be innovative and creative. You need to have strong leadership qualities to motivate team members and direct them towards achieving organizational goals.
You should also be organized and efficient to meet tight deadlines.
What is the difference between a production planner and a project manager?
The difference between a product planner and project manager is that a planer is typically the one who organizes and plans the entire project. A production planner, however, is mostly involved in the planning stages.
What are the jobs in logistics?
Logistics can offer many different jobs. Here are some examples:
-
Warehouse workers - They load and unload trucks and pallets.
-
Transportation drivers - They drive trucks and trailers to deliver goods and carry out pick-ups.
-
Freight handlers, - They sort out and pack freight in warehouses.
-
Inventory managers - These are responsible for overseeing the stock of goods in warehouses.
-
Sales representatives: They sell products to customers.
-
Logistics coordinators are responsible for organizing and planning logistics operations.
-
Purchasing agents – They buy goods or services necessary to run a company.
-
Customer service representatives - Answer calls and email from customers.
-
Shipping clerks: They process shipping requests and issue bills.
-
Order fillers are people who fill orders based only on what was ordered.
-
Quality control inspectors (QCI) - They inspect all incoming and departing products for potential defects.
-
Other - Logistics has many other job opportunities, including transportation supervisors, logistics specialists, and cargo specialists.
What is the role and responsibility of a Production Planner?
A production planner ensures all aspects of the project are delivered on time, within budget, and within scope. They make sure that the product and services meet client expectations.
What is the difference between Production Planning, Scheduling and Production Planning?
Production Planning (PP), also known as forecasting and identifying production capacities, is the process that determines what product needs to be produced at any particular time. This is accomplished by forecasting the demand and identifying production resources.
Scheduling refers the process by which tasks are assigned dates so that they can all be completed within the given timeframe.
How can I find out more about manufacturing?
Experience is the best way for you to learn about manufacturing. You can read books, or watch instructional videos if you don't have the opportunity to do so.
Statistics
- In the United States, for example, manufacturing makes up 15% of the economic output. (twi-global.com)
- (2:04) MTO is a production technique wherein products are customized according to customer specifications, and production only starts after an order is received. (oracle.com)
- [54][55] These are the top 50 countries by the total value of manufacturing output in US dollars for its noted year according to World Bank.[56] (en.wikipedia.org)
- Job #1 is delivering the ordered product according to specifications: color, size, brand, and quantity. (netsuite.com)
- Many factories witnessed a 30% increase in output due to the shift to electric motors. (en.wikipedia.org)
External Links
How To
How to Use Six Sigma in Manufacturing
Six Sigma is defined as "the application of statistical process control (SPC) techniques to achieve continuous improvement." It was developed by Motorola's Quality Improvement Department at their plant in Tokyo, Japan, in 1986. Six Sigma's basic concept is to improve quality and eliminate defects through standardization. Many companies have adopted this method in recent years. They believe there is no such thing a perfect product or service. Six Sigma aims to reduce variation in the production's mean value. You can calculate the percentage of deviation from the norm by taking a sample of your product and comparing it to the average. If there is a significant deviation from the norm, you will know that something needs to change.
Understanding how variability works in your company is the first step to Six Sigma. Once you understand this, you can then identify the causes of variation. This will allow you to decide if these variations are random and systematic. Random variations occur when people make mistakes; systematic ones are caused by factors outside the process itself. If you make widgets and some of them end up on the assembly line, then those are considered random variations. It would be considered a systematic problem if every widget that you build falls apart at the same location each time.
Once you've identified the problem areas you need to find solutions. It might mean changing the way you do business or redesigning it entirely. To verify that the changes have worked, you need to test them again. If they don't work, you will need to go back to the drawing boards and create a new plan.