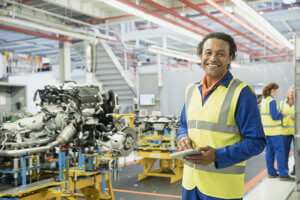
Supply chain risk management is essential for maintaining a strong operation, no matter if you're a small business owner or an enterprise unit of a large corporation. Risks vary from the mundane to the downright disastrous. A well-thought out plan and a proper implementation strategy can protect your organization from losses.
Data sharing is an integral part of a supply chains continuity plan. If your organization relies on a single supplier, you are prone to vendor failures and supplier dispute. You will be more likely to avoid supply interruptions if your company is part-of a multisupplier group. You may also have the ability to negotiate with another supplier.
Similarly, if your company has a complex network of contractors, you are at greater risk of vendor fraud, duplicate billing, and improper related-party billing. These risks can be mitigated by creating a risk assessment strategy that includes a complete assessment and assessment of all your suppliers, partners, as well other tier-1 components.
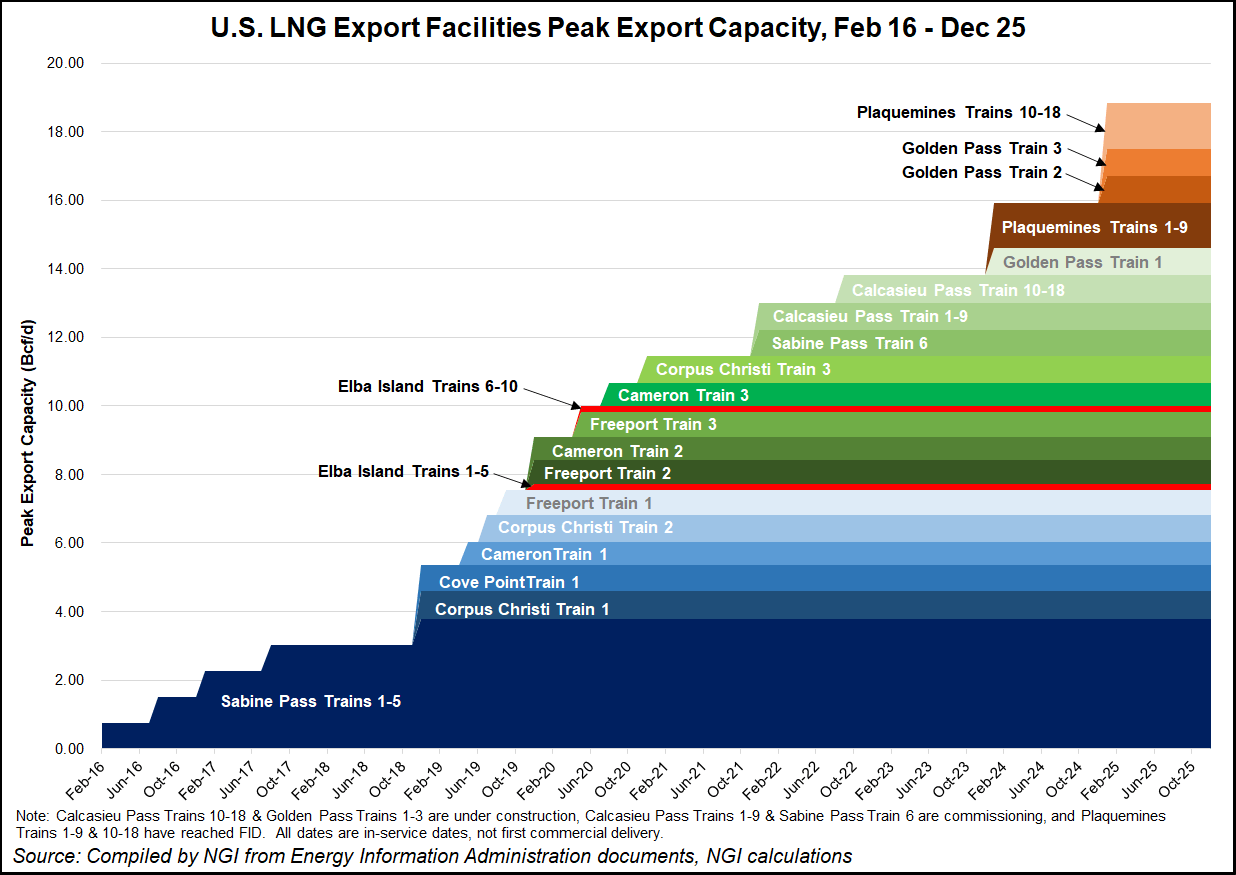
First, identify the critical elements of your supply chain. Next, measure and quantify them. Finally, create an action program. The plan should include all the items mentioned above, as well some additional. The most important element is a proactive monitoring system. Your executives need to have real-time, accurate data about supply chain risk. You can make better decisions and react quickly by monitoring supply risk in real-time.
While you are assessing your risks and quantifying them, it is crucial to keep in view that your supply chain's ability to withstand disruption is a function if governance. You must also consider the roles of stakeholders. One example is the supplier bankruptcy in the pharmaceutical sector that could have been prevented if the company had properly managed its suppliers.
It is crucial to have a plan that addresses the supply chain crisis. But, it is not always simple to put in place the right contingency strategies. Many businesses neglect to make the effort to have enough contingency planning for every risk they face. This plan should be developed with the greatest potential impact.
The PPPR or preventive, preparedness, response, and recovery methodology is a worldwide standard for supply chain risk management. It is a robust approach that can improve your ability to monitor and react to supply-chain disruptions, and is often used in conjunction with other strategies to protect your organization from risk. Using a PPPR as a guide can help you make the right decisions and stay ahead of your competition in today's marketplace.
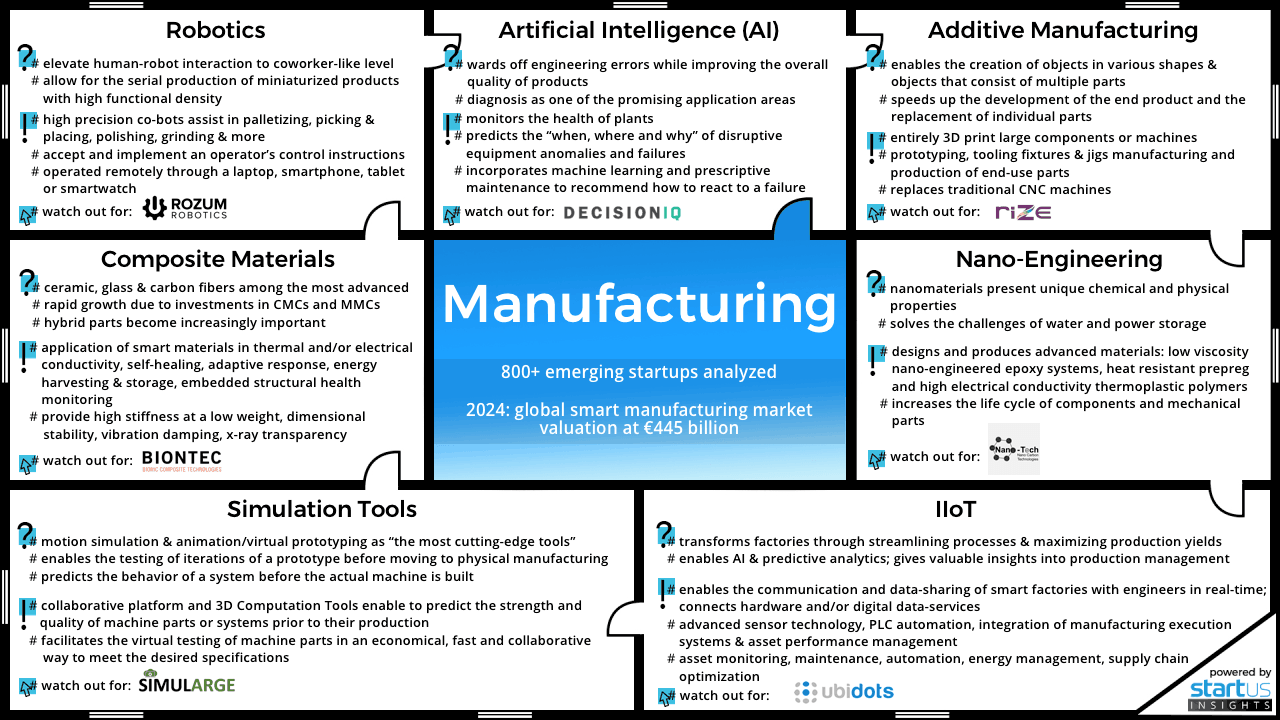
The right data can help you understand your suppliers' history and what they offer. This information will help you to make better decisions whether you are trying to increase your sourcing efforts or just tweaking your current processes. You can provide the right risk premiums to your insurers by having reliable data.
FAQ
What are the responsibilities for a manufacturing manager
A manufacturing manager must ensure that all manufacturing processes are efficient and effective. They must also be alert to any potential problems and take appropriate action.
They should also be able communicate with other departments, such as sales or marketing.
They should also be knowledgeable about the latest trends in the industry so they can use this information for productivity and efficiency improvements.
How does a production planner differ from a project manager?
A production planner is more involved in the planning phase of the project than a project manger.
Why automate your warehouse
Modern warehousing is becoming more automated. The rise of e-commerce has led to increased demand for faster delivery times and more efficient processes.
Warehouses need to adapt quickly to meet changing needs. Technology is essential for warehouses to be able to adapt quickly to changing needs. Automating warehouses has many benefits. Here are some benefits of investing in automation
-
Increases throughput/productivity
-
Reduces errors
-
Improves accuracy
-
Boosts safety
-
Eliminates bottlenecks
-
Allows companies scale more easily
-
This makes workers more productive
-
It gives visibility to everything that happens inside the warehouse
-
Enhances customer experience
-
Improves employee satisfaction
-
This reduces downtime while increasing uptime
-
Quality products delivered on time
-
Eliminates human error
-
It helps ensure compliance with regulations
What does manufacturing mean?
Manufacturing Industries refers to businesses that manufacture products. These products are sold to consumers. This is accomplished by using a variety of processes, including production, distribution and retailing. They produce goods from raw materials by using machines and other machinery. This includes all types of manufactured goods, including food items, clothing, building supplies, furniture, toys, electronics, tools, machinery, vehicles, pharmaceuticals, medical devices, chemicals, and many others.
What is the role of a production manager?
A production planner ensures all aspects of the project are delivered on time, within budget, and within scope. They also ensure the quality of the product and service meets the client's requirements.
Is automation important for manufacturing?
Not only are service providers and manufacturers important, but so is automation. Automation allows them to deliver services quicker and more efficiently. They can also reduce their costs by reducing human error and improving productivity.
Are there any Manufacturing Processes that we should know before we can learn about Logistics?
No. No. However, knowing about manufacturing processes will definitely give you a better understanding of how logistics works.
Statistics
- It's estimated that 10.8% of the U.S. GDP in 2020 was contributed to manufacturing. (investopedia.com)
- In 2021, an estimated 12.1 million Americans work in the manufacturing sector.6 (investopedia.com)
- [54][55] These are the top 50 countries by the total value of manufacturing output in US dollars for its noted year according to World Bank.[56] (en.wikipedia.org)
- Many factories witnessed a 30% increase in output due to the shift to electric motors. (en.wikipedia.org)
- (2:04) MTO is a production technique wherein products are customized according to customer specifications, and production only starts after an order is received. (oracle.com)
External Links
How To
How to use Lean Manufacturing in the production of goods
Lean manufacturing is a management style that aims to increase efficiency and reduce waste through continuous improvement. It was developed by Taiichi Okono in Japan, during the 1970s & 1980s. TPS founder Kanji Takoda awarded him the Toyota Production System Award (TPS). The first book published on lean manufacturing was titled "The Machine That Changed the World" written by Michael L. Watkins and published in 1990.
Lean manufacturing can be described as a set or principles that are used to improve quality, speed and cost of products or services. It emphasizes the elimination and minimization of waste in the value stream. Lean manufacturing is called just-in-time (JIT), zero defect, total productive maintenance (TPM), or 5S. Lean manufacturing eliminates non-value-added tasks like inspection, rework, waiting.
Lean manufacturing improves product quality and costs. It also helps companies reach their goals quicker and decreases employee turnover. Lean manufacturing can be used to manage all aspects of the value chain. Customers, suppliers, distributors, retailers and employees are all included. Lean manufacturing is widely practiced in many industries around the world. Toyota's philosophy is the foundation of its success in automotives, electronics and appliances, healthcare, chemical engineers, aerospace, paper and food, among other industries.
Five fundamental principles underlie lean manufacturing.
-
Define Value: Identify the social value of your business and what sets you apart.
-
Reduce waste - Stop any activity that isn't adding value to the supply chains.
-
Create Flow: Ensure that the work process flows without interruptions.
-
Standardize and simplify – Make processes as repeatable and consistent as possible.
-
Build Relationships- Develop personal relationships with both internal as well as external stakeholders.
Lean manufacturing is not a new concept, but it has been gaining popularity over the last few years due to a renewed interest in the economy following the global financial crisis of 2008. Many businesses have adopted lean manufacturing techniques to help them become more competitive. Many economists believe lean manufacturing will play a major role in economic recovery.
Lean manufacturing, which has many benefits, is now a standard practice in the automotive industry. These include improved customer satisfaction, reduced inventory levels, lower operating costs, increased productivity, and better overall safety.
It can be applied to any aspect of an organisation. Because it makes sure that all value chains are efficient and effectively managed, Lean Manufacturing is particularly helpful for organizations.
There are three main types in lean manufacturing
-
Just-in-Time Manufacturing (JIT): This type of lean manufacturing is commonly referred to as "pull systems." JIT is a process in which components can be assembled at the point they are needed, instead of being made ahead of time. This approach aims to reduce lead times, increase the availability of parts, and reduce inventory.
-
Zero Defects Manufacturing (ZDM): ZDM focuses on ensuring that no defective units leave the manufacturing facility. If a part needs to be fixed during the assembly line, it should be repaired rather than scrapped. This is true even for finished products that only require minor repairs prior to shipping.
-
Continuous Improvement (CI), also known as Continuous Improvement, aims at improving the efficiency of operations through continuous identification and improvement to minimize or eliminate waste. Continuous Improvement involves continuous improvement of processes.