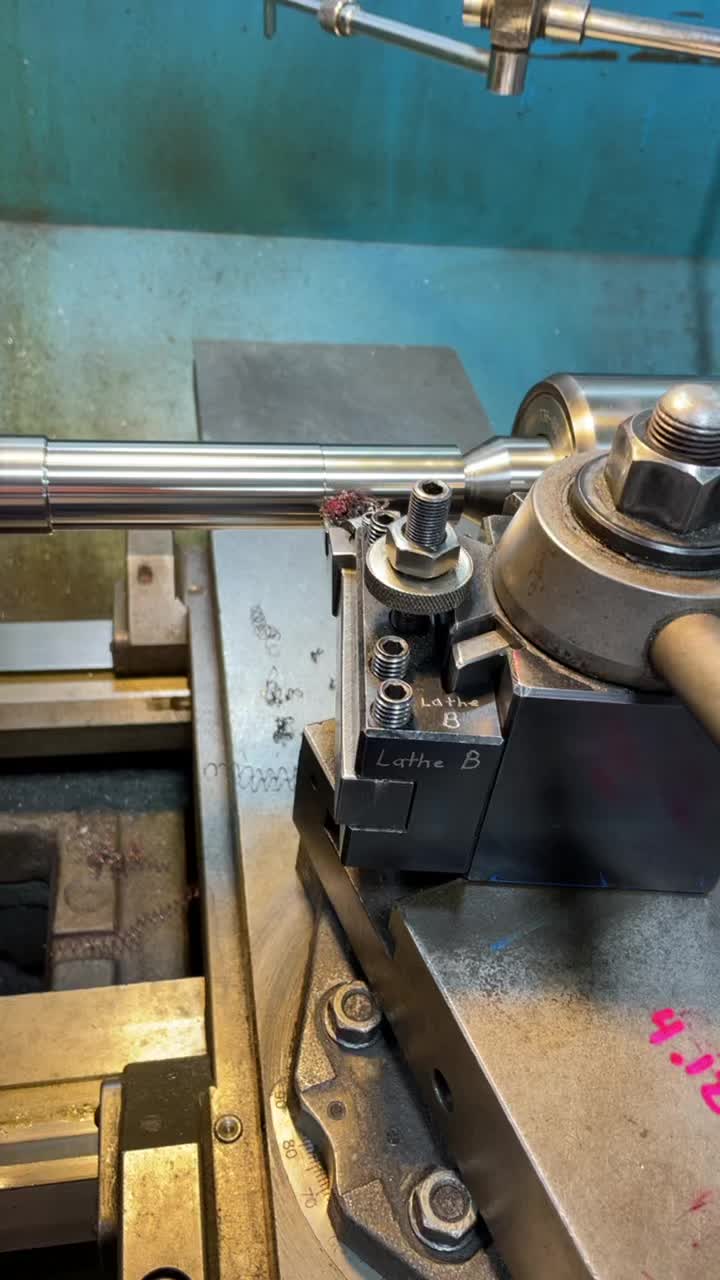
A Chemical Technician can be described as an artisan that is involved with the production of chemical products. The technician is responsible for testing the materials used in manufacturing. They may work in research and development, in manufacturing lines or laboratories.
They are usually supervised by chemists. They oversee the quality of the product and test new materials. As they gain experience, they could be promoted. Pharmacists are one of the many companies that hire them. Those who have a bachelor's degree in chemistry, biology, or engineering can earn more.
The average salary for a Chemical Technician is $48,990. Although pay for this job can vary by region, it is the median. This includes taxable wages and bonuses. It also covers the education, skills and experience of the worker. The highest earning Chemical Technicians earned more than $60,000 per year.
A Chemical Technician's job duties include conducting research and developing pharmaceuticals and chemicals. They analyze ingredients in medicines, food, or other products. They can also supervise workers in the production line.
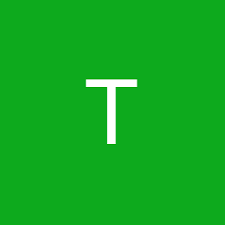
An associate's or bachelors degree in biology, chemistry, physics or computer science will be required for a career as Chemical Technician. You can also obtain a graduate or doctoral degree. Some companies prefer to hire chemical technicians who have a college degree. You may need a master's in order to work in other fields.
Visit a school placement office to find out more about job opportunities. You can also find many job banks online. American Chemical Society is another excellent resource. Local chapters may post job listings.
If you're looking for a job as a Chemical Technician, you should be prepared to work long hours. While most laboratories have a seven-day work week, some experienced workers are sometimes called in to perform odd-hours experiments or inspections.
The median salary of Chemical Technicians is $36,000 to $47,000. For experienced workers, the average salary is $11,000. Entry-level workers on the other side can earn between $15-18 an hour.
San Francisco, San Jose and San Jose are two of the top cities for Chemical Technician salary. Both cities beat the national average by over 20 percent. BLS reported that Chemical Technie in these cities earned $83,600.
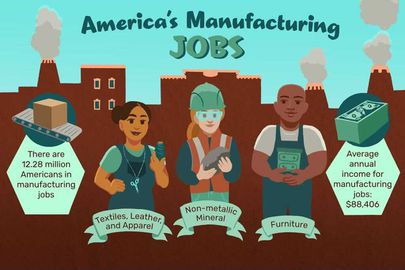
The Bureau of Labor Statistics states that the job growth for Chemical Technicians will be slower than average. While their employment is expected increase by 3 percentage points through 2014, the number will grow only by 4 percent over ten years. Due to this, skilled technicians will likely see an increase in demand.
As environmental issues become more pressing, there will be a greater demand for chemical R&D. These workers will have the best jobs in laboratories where they can test new materials.
FAQ
Is automation important in manufacturing?
Automation is important not only for manufacturers but also for service providers. It enables them to provide services faster and more efficiently. They can also reduce their costs by reducing human error and improving productivity.
What is manufacturing and logistics?
Manufacturing is the process of creating goods from raw materials by using machines and processes. Logistics includes all aspects related to supply chain management, such as procurement, distribution planning, inventory control and transportation. Manufacturing and logistics can often be grouped together to describe a larger term that covers both the creation of products, and the delivery of them to customers.
What are the 7 Rs of logistics?
The acronym "7R's" of Logistics stands for seven principles that underpin logistics management. It was developed by the International Association of Business Logisticians (IABL) and published in 2004 as part of its "Seven Principles of Logistics Management" series.
The following letters make up the acronym:
-
Responsible - to ensure that all actions are within the legal requirements and are not detrimental to others.
-
Reliable - Have confidence in your ability to fulfill all of your commitments.
-
Reasonable - make sure you use your resources well and don't waste them.
-
Realistic – consider all aspects of operations, from cost-effectiveness to environmental impact.
-
Respectful - Treat people fairly and equitably
-
Be resourceful: Look for opportunities to save money or increase productivity.
-
Recognizable: Provide customers with value-added service
How can manufacturing excess production be decreased?
Improved inventory management is the key to reducing overproduction. This would reduce the time needed to manage inventory. We could use these resources to do other productive tasks.
You can do this by adopting a Kanban method. A Kanbanboard is a visual tool that allows you to keep track of the work being done. A Kanban system allows work items to move through several states before reaching their final destination. Each state has a different priority level.
If work is moving from one stage to the other, then the current task can be completed and moved on to the next. It is possible to keep a task in the beginning stages until it gets to the end.
This allows you to keep work moving along while making sure that no work gets neglected. A Kanban board allows managers to monitor how much work is being completed at any given moment. This information allows them to adjust their workflow based on real-time data.
Another way to control inventory levels is to implement lean manufacturing. Lean manufacturing focuses on eliminating waste throughout the entire production chain. Anything that does not contribute to the product's value is considered waste. These are some of the most common types.
-
Overproduction
-
Inventory
-
Packaging not required
-
Overstock materials
Manufacturers can reduce their costs and improve their efficiency by using these ideas.
What are the responsibilities of a logistic manager?
A logistics manager makes sure that all goods are delivered on-time and in good condition. This is done through his/her expertise and knowledge about the company's product range. He/she should make sure that enough stock is on hand to meet the demands.
What is the difference in Production Planning and Scheduling, you ask?
Production Planning (PP), is the process of deciding what production needs to take place at any given time. This can be done by forecasting demand and identifying production capabilities.
Scheduling refers the process by which tasks are assigned dates so that they can all be completed within the given timeframe.
What is production planning?
Production Planning includes planning for all aspects related to production. This document is designed to make sure everything is ready for when you're ready to shoot. This document should also include information on how to get the best result on set. It should include information about shooting locations, casting lists, crew details, equipment requirements, and shooting schedules.
It is important to first outline the type of film you would like to make. You may have decided where to shoot or even specific locations you want to use. Once you've identified the locations and scenes you want to use, you can begin to plan what elements you need for each scene. One example is if you are unsure of the exact model you want but decide that you require a car. This is where you can look up car models online and narrow down your options by choosing from different makes and models.
After you have selected the car you want, you can begin to think about additional features. Do you have people who need to be seated in the front seat? Perhaps you have someone who needs to be able to walk around the back of your car. Maybe you'd like to change the interior from black to a white color. These questions will help you determine the exact look and feel of your car. Also, think about what kind of shots you would like to capture. Will you be filming close-ups or wide angles? Perhaps you want to show the engine or the steering wheel? These things will help you to identify the car that you are looking for.
Once you've determined the above, it is time to start creating a calendar. You will know when you should start and when you should finish shooting. Every day will have a time for you to arrive at the location, leave when you are leaving and return home when you are done. It will help everyone know exactly what they have to do and when. Book extra staff ahead of time if you need them. You should not hire anyone who doesn't show up because of your inaction.
Your schedule will also have to be adjusted to reflect the number of days required to film. Some projects may only take a couple of days, while others could last for weeks. When creating your schedule, be aware of whether you need more shots per day. Multiple takes of the same location will lead to higher costs and take more time. You can't be certain if you will need multiple takes so it is better not to shoot too many.
Another important aspect of production planning is setting budgets. You will be able to manage your resources if you have a realistic budget. Remember that you can always reduce the budget later on if you run into unforeseen problems. It is important to not overestimate how much you will spend. You will end up spending less money if you underestimate the cost of something.
Production planning is a detailed process. But, once you understand the workings of everything, it becomes easier for future projects to be planned.
Statistics
- You can multiply the result by 100 to get the total percent of monthly overhead. (investopedia.com)
- It's estimated that 10.8% of the U.S. GDP in 2020 was contributed to manufacturing. (investopedia.com)
- According to a Statista study, U.S. businesses spent $1.63 trillion on logistics in 2019, moving goods from origin to end user through various supply chain network segments. (netsuite.com)
- [54][55] These are the top 50 countries by the total value of manufacturing output in US dollars for its noted year according to World Bank.[56] (en.wikipedia.org)
- Job #1 is delivering the ordered product according to specifications: color, size, brand, and quantity. (netsuite.com)
External Links
How To
Six Sigma: How to Use it in Manufacturing
Six Sigma can be described as "the use of statistical process control (SPC), techniques to achieve continuous improvement." Motorola's Quality Improvement Department, Tokyo, Japan, developed it in 1986. Six Sigma's basic concept is to improve quality and eliminate defects through standardization. Many companies have adopted Six Sigma in recent years because they believe that there are no perfect products and services. The main goal of Six Sigma is to reduce variation from the mean value of production. If you take a sample and compare it with the average, you will be able to determine how much of the production process is different from the norm. If the deviation is excessive, it's likely that something needs to be fixed.
Understanding how your business' variability is a key step towards Six Sigma implementation is the first. Once you understand that, it is time to identify the sources of variation. Also, you will need to identify the sources of variation. Random variations are caused by human errors. Systematic variations can be caused by outside factors. These are, for instance, random variations that occur when widgets are made and some fall off the production line. It would be considered a systematic problem if every widget that you build falls apart at the same location each time.
Once you've identified the problem areas you need to find solutions. The solution could involve changing how you do things, or redesigning your entire process. After implementing the new changes, you should test them again to see if they worked. If they don't work you need to rework them and come up a better plan.