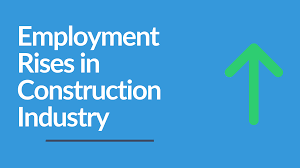
The surprising trend in the list of state manufacturers shows that the most popular suspects, such the southeastern, are not far from the top. But this trend is changing and many states show that you can trade off cost and quality of labor to get the best deals. This trend shows us that there are many factors which influence the state's ability or inability to attract manufacturing jobs. How can you decide the right location to start your business?
Group Five
This page lists all five Group Five manufacturers in each state. Group Five's range includes steel pipes as well structural components and industrial engineering items. The company offers pipe design services. They offer the best price to quality ratio in steel thickness and grade. To meet all your requirements, the company uses modern CAD systems and computer finite analyses programs.
Group Three
The United States Census Bureau reports that approximately 50,000 manufacturers are located in Group Three. This group has low unemployment rates, high economic growth and has a low rate of GDP growth. This is because the majority of manufacturers in this group have small businesses. Despite these limitations, the data can still be considered a useful guide. Here is a list listing the top state manufacturers. Read on to learn more.
Audi, Mercedes-Benz, and BMW are the biggest three manufacturers in Europe. Honda and Toyota have dropped to fifth and sixth, respectively. However, the Detroit Three have reclaimed the Big Three title. The following table lists the top-selling carmakers in each state and their sales. The link below will take you to the list of top-selling cars in each state. There are many models that these manufacturers offer, including SUVs, midsize sedans and minivans.
FAQ
What is production planning?
Production Planning refers to the development of a plan for every aspect of production. This document ensures that everything is prepared and available when you are ready for shooting. This document should also include information on how to get the best result on set. It should include information about shooting locations, casting lists, crew details, equipment requirements, and shooting schedules.
The first step in filming is to define what you want. You may have already chosen the location you want, or there are locations or sets you prefer. Once you have identified your locations and scenes, you can start working out which elements you require for each scene. If you decide you need a car and don't know what model to choose, this could be an example. You could look online for cars to see what options are available, and then narrow down your choices by selecting between different makes or models.
Once you have found the right vehicle, you can think about adding accessories. Do you have people who need to be seated in the front seat? Or maybe you just need someone to push the car around. Perhaps you would like to change the interior colour from black to white. These questions will help determine the look and feel you want for your car. Another thing you can do is think about what type of shots are desired. Will you be filming close-ups or wide angles? Maybe you want to show your engine or the steering wheel. This will allow you to determine the type of car you want.
Once you have established all the details, you can create a schedule. You can create a schedule that will outline when you must start and finish your shoots. The schedule will show you when to get there, what time to leave, and when to return home. Everyone knows exactly what they should do and when. Book extra staff ahead of time if you need them. You don't want to hire someone who won't show up because he didn't know.
It is important to calculate the amount of filming days when you are creating your schedule. Some projects are quick and easy, while others take weeks. You should consider whether you will need more than one shot per week when creating your schedule. Multiple takes of the same location will lead to higher costs and take more time. It's better to be safe than sorry and shoot less takes if you're not certain whether you need more takes.
Budget setting is another important aspect in production planning. It is important to set a realistic budget so you can work within your budget. If you have to reduce your budget due to unexpected circumstances, you can always lower it later. However, you shouldn't overestimate the amount of money you will spend. If you underestimate the cost of something, you will have less money left after paying for other items.
Production planning is a complicated process. But once you understand how everything works together, it becomes much easier to plan future project.
How can excess manufacturing production be reduced?
Improved inventory management is the key to reducing overproduction. This would reduce the time spent on unproductive activities like purchasing, storing and maintaining excess stock. This could help us free up our time for other productive tasks.
You can do this by adopting a Kanban method. A Kanbanboard is a visual tool that allows you to keep track of the work being done. Kanban systems allow work items to move through different states until they reach their final destination. Each state represents a different priority.
As an example, if work is progressing from one stage of the process to another, then the current task is complete and can be transferred to the next. If a task is still in its beginning stages, it will continue to be so until it reaches the end.
This allows for work to continue moving forward, while also ensuring that there is no work left behind. A Kanban board allows managers to monitor how much work is being completed at any given moment. This data allows them adjust their workflow based upon real-time data.
Another way to control inventory levels is to implement lean manufacturing. Lean manufacturing works to eliminate waste throughout every stage of the production chain. Any product that isn't adding value can be considered waste. Here are some examples of common types.
-
Overproduction
-
Inventory
-
Packaging that is not necessary
-
Excess materials
These ideas will help manufacturers increase efficiency and lower costs.
What does manufacturing industry mean?
Manufacturing Industries is a group of businesses that produce goods for sale. Consumers are those who purchase these products. These companies use a variety processes such as distribution, retailing and management to accomplish their purpose. They make goods from raw materials with machines and other equipment. This covers all types of manufactured goods including clothing, food, building supplies and furniture, as well as electronics, tools, machinery, vehicles and pharmaceuticals.
Is automation important for manufacturing?
Not only is automation important for manufacturers, but it's also vital for service providers. Automation allows them to deliver services quicker and more efficiently. They can also reduce their costs by reducing human error and improving productivity.
Why is logistics important for manufacturing?
Logistics is an integral part of every business. They enable you to achieve outstanding results by helping manage product flow from raw materials through to finished goods.
Logistics plays a significant role in reducing cost and increasing efficiency.
What are the 7 Rs of logistics?
The 7R's of Logistics is an acronym for the seven basic principles of logistics management. It was developed and published by the International Association of Business Logisticians in 2004 as part of the "Seven Principles of Logistics Management".
The acronym is composed of the following letters.
-
Responsible - to ensure that all actions are within the legal requirements and are not detrimental to others.
-
Reliable – have faith in your ability and capability to keep promises.
-
Reasonable - use resources efficiently and don't waste them.
-
Realistic - consider all aspects of operations, including cost-effectiveness and environmental impact.
-
Respectful - Treat people fairly and equitably
-
Be resourceful: Look for opportunities to save money or increase productivity.
-
Recognizable - Provide value-added services to customers
Statistics
- It's estimated that 10.8% of the U.S. GDP in 2020 was contributed to manufacturing. (investopedia.com)
- In 2021, an estimated 12.1 million Americans work in the manufacturing sector.6 (investopedia.com)
- You can multiply the result by 100 to get the total percent of monthly overhead. (investopedia.com)
- [54][55] These are the top 50 countries by the total value of manufacturing output in US dollars for its noted year according to World Bank.[56] (en.wikipedia.org)
- Job #1 is delivering the ordered product according to specifications: color, size, brand, and quantity. (netsuite.com)
External Links
How To
How to Use Just-In-Time Production
Just-in time (JIT), is a process that reduces costs and increases efficiency in business operations. This is where you have the right resources at the right time. This means that you only pay the amount you actually use. Frederick Taylor developed the concept while working as foreman in early 1900s. He saw how overtime was paid to workers for work that was delayed. He decided that workers would be more productive if they had enough time to complete their work before they started to work.
The idea behind JIT is that you should plan ahead and have everything ready so you don't waste money. The entire project should be looked at from start to finish. You need to ensure you have enough resources to tackle any issues that might arise. If you anticipate that there might be problems, you'll have enough people and equipment to fix them. This way you won't be spending more on things that aren’t really needed.
There are many JIT methods.
-
Demand-driven JIT: You order the parts and materials you need for your project every other day. This will allow you to track how much material you have left over after using it. It will also allow you to predict how long it takes to produce more.
-
Inventory-based: This is a type where you stock the materials required for your projects in advance. This allows for you to anticipate how much you can sell.
-
Project-driven: This is an approach where you set aside enough funds to cover the cost of your project. You will be able to purchase the right amount of materials if you know what you need.
-
Resource-based JIT: This type of JIT is most commonly used. Here you can allocate certain resources based purely on demand. You might assign more people to help with orders if there are many. If you don’t have many orders you will assign less people to the work.
-
Cost-based: This is a similar approach to resource-based but you are not only concerned with how many people you have, but also how much each one costs.
-
Price-based: This approach is very similar to the cost-based method except that you don't look at individual workers costs but the total cost of the company.
-
Material-based - This is a variant of cost-based. But instead of looking at the total company cost, you focus on how much raw material you spend per year.
-
Time-based JIT: This is another variant of resource-based JIT. Instead of focusing only on how much each employee is costing, you should focus on how long it takes to complete your project.
-
Quality-based: This is yet another variation of resource-based JIT. Instead of worrying about the costs of each employee or how long it takes for something to be made, you should think about how quality your product is.
-
Value-based JIT : This is the newest type of JIT. In this instance, you are not concerned about the product's performance or meeting customer expectations. Instead, you focus on the added value that you provide to your market.
-
Stock-based. This method is inventory-based and focuses only on the actual production at any given point. This method is useful when you want to increase production while decreasing inventory.
-
Just-intime planning (JIT), is a combination JIT/sales chain management. This refers to the scheduling of the delivery of components as soon after they are ordered. It's important as it reduces leadtimes and increases throughput.