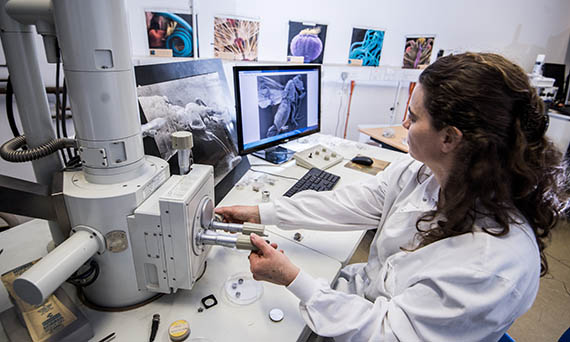
This article will cover the different types companies that are manufacturing in the U.S. The list will include industry trends as well as the costs involved in doing businesses in the U.S. Dun & Bradstreet can be a good resource for manufacturers because they collect information from a wide variety of reliable sources. This information helps manufacturers gauge their performance, growth potential, and competitive pressures. This information is vital for companies looking to expand.
List of American manufacturing companies
The United States has 50 states, covering a large part of North America. The northwestern region of the United States includes Alaska and Hawaii, while New York City and Washington, DC are the major cities along the Atlantic coast. Los Angeles and Chicago are also major cities. They are well-known for their influential architecture and filmmaking. There are many American manufacturing companies, so it is important that you find the one that best suits your needs.
Contacts at all levels of the manufacturing company list in the United States must be included, from the top management to the floor. The contact list can be long and include people responsible for everything from purchasing to health and safety, supply chain policies, and supply chain management. It should also include contacts responsible for quality assurance, purchasing, marketing, sales development, and procurement. It is important not to forget that the list may have been updated.
Industry trends
Manufacturers worry about rising labor and material costs as global demand rises. Some companies have resorted to outsourcing while others have increased their flexibility to move production lines rapidly. With this in place, manufacturers are increasingly looking to automated production and other sustainable manufacturing practices. Listed below are some of the key trends to keep an eye on. This article examines three of the most important trends in manufacturing in the USA.
The U.S. industrial sector is a crucial indicator of the country's economic health. A rebound in manufacturing signals that the economy is moving towards extended growth and recovery. Manufacturing faces many challenges, including labor shortages and difficult raw materials. Abhijit Shahide, BofA Securities Managing Director, discusses five major trends that will drive the manufacturing industry. The manufacturing industry is becoming more resilient in spite of technological advances.
Cost of doing business in America
The U.S. economy continues to be strong, but rising tariffs and costs are affecting the business outlook. Many people predict that the world will enter recession in 2020. However, it is impossible to know when. In any case, 2020 will see an increase in costs to do business in the U.S. This is good news for American businesses, but it also creates risks for newcomers.
Although the costs of labor and raw materials may seem small, registration and startup costs are not. Your business's profitability will be affected by these costs. However, you can lower your overall costs and keep it moving forward. These costs can be reduced if you are unable to do so. You may also consider cost-cutting options. It is possible to lease or hire equipment, or use existing resources in more efficient ways.
FAQ
What skills are required to be a production manager?
Production planners must be flexible, organized, and able handle multiple tasks. Communication skills are essential to ensure that you can communicate effectively with clients, colleagues, and customers.
What are the essential elements of running a logistics firm?
To be a successful businessman in logistics, you will need many skills and knowledge. Effective communication skills are necessary to work with suppliers and clients. You will need to know how to interpret data and draw conclusions. You need to be able work under pressure and manage stressful situations. You must be creative and innovative to develop new ideas to improve efficiency. Strong leadership qualities are essential to motivate your team and help them achieve their organizational goals.
You must be organized to meet tight deadlines.
What is production plan?
Production Planning involves developing a plan for all aspects of the production, including scheduling, budgeting, casting, crew, location, equipment, props, etc. This document will ensure everything is in order and ready to go when you need it. This document should include information about how to achieve the best results on-set. This includes information on shooting times, locations, cast lists and crew details.
First, you need to plan what you want to film. You might have an idea of where you want to film, or you may have specific locations or sets in mind. Once you have identified the scenes and locations, you can start to determine which elements are required for each scene. Perhaps you have decided that you need to buy a car but aren't sure which model. You could look online for cars to see what options are available, and then narrow down your choices by selecting between different makes or models.
After you have chosen the right car, you will be able to begin thinking about accessories. Do you have people who need to be seated in the front seat? Or maybe you just need someone to push the car around. Maybe you'd like to change the interior from black to a white color. These questions will help to determine the style and feel of your car. Also, think about what kind of shots you would like to capture. Will you be filming close-ups or wide angles? Maybe the engine or steering wheel is what you are looking to film. All of these things will help you identify the exact style of car you want to film.
Once you have determined all of the above, you can move on to creating a schedule. The schedule will show you when to begin shooting and when to stop. A schedule for each day will detail when you should arrive at the location and when you need leave. This way, everyone knows what they need to do and when. If you need to hire extra staff, you can make sure you book them in advance. It is not worth hiring someone who won’t show up because you didn’t tell him.
You will need to factor in the days that you have to film when creating your schedule. Some projects are quick and easy, while others take weeks. While creating your schedule, it is important to remember whether you will require more than one shot per day. Multiple shots at the same location can increase costs and make it more difficult to complete. It's better to be safe than sorry and shoot less takes if you're not certain whether you need more takes.
Budgeting is another crucial aspect of production plan. As it will allow you and your team to work within your financial means, setting a realistic budget is crucial. Keep in mind that you can always reduce your budget if you face unexpected difficulties. However, you shouldn't overestimate the amount of money you will spend. If you underestimate the cost of something, you will have less money left after paying for other items.
Planning production is a tedious process. Once you have a good understanding of how everything works together, planning future projects becomes easy.
What type of jobs is there in logistics
There are many jobs available in logistics. Some examples are:
-
Warehouse workers - They load trucks and pallets.
-
Transportation drivers: They drive trucks and trailers and deliver goods and make pick-ups.
-
Freight handlers - They sort and pack freight in warehouses.
-
Inventory managers - These are responsible for overseeing the stock of goods in warehouses.
-
Sales representatives: They sell products to customers.
-
Logistics coordinators - They plan and organize logistics operations.
-
Purchasing agents - They purchase goods and services needed for company operations.
-
Customer service agents - They answer phone calls and respond to emails.
-
Shipping clerks: They process shipping requests and issue bills.
-
Order fillers: They fill orders based off what has been ordered and shipped.
-
Quality control inspectors: They inspect outgoing and incoming products for any defects.
-
Others – There are many other types available in logistics. They include transport supervisors, cargo specialists and others.
How can I find out more about manufacturing?
Practical experience is the best way of learning about manufacturing. You can also read educational videos or take classes if this isn't possible.
How can efficiency in manufacturing be improved?
First, determine which factors have the greatest impact on production time. Then we need to find ways to improve these factors. If you don’t know where to begin, consider which factors have the largest impact on production times. Once you've identified them, try to find solutions for each of those factors.
Statistics
- In the United States, for example, manufacturing makes up 15% of the economic output. (twi-global.com)
- According to the United Nations Industrial Development Organization (UNIDO), China is the top manufacturer worldwide by 2019 output, producing 28.7% of the total global manufacturing output, followed by the United States, Japan, Germany, and India.[52][53] (en.wikipedia.org)
- [54][55] These are the top 50 countries by the total value of manufacturing output in US dollars for its noted year according to World Bank.[56] (en.wikipedia.org)
- Many factories witnessed a 30% increase in output due to the shift to electric motors. (en.wikipedia.org)
- In 2021, an estimated 12.1 million Americans work in the manufacturing sector.6 (investopedia.com)
External Links
How To
How to use 5S in Manufacturing to Increase Productivity
5S stands in for "Sort", the "Set In Order", "Standardize", or "Separate". Toyota Motor Corporation created the 5S methodology in 1954. It allows companies to improve their work environment, thereby achieving greater efficiency.
The basic idea behind this method is to standardize production processes, so they become repeatable, measurable, and predictable. This means that daily tasks such as cleaning and sorting, storage, packing, labeling, and packaging are possible. Workers can be more productive by knowing what to expect.
Implementing 5S requires five steps. These are Sort, Set In Order, Standardize. Separate. And Store. Each step requires a different action, which increases efficiency. Sorting things makes it easier to find them later. When you arrange items, you place them together. You then organize your inventory in groups. Labeling your containers will ensure that everything is correctly labeled.
Employees must be able to critically examine their work practices. Employees must be able to see why they do what they do and find a way to achieve them without having to rely on their old methods. To implement the 5S system, employees must acquire new skills and techniques.
In addition to increasing efficiency, the 5S method also improves morale and teamwork among employees. They feel more motivated to work towards achieving greater efficiency as they see the results.