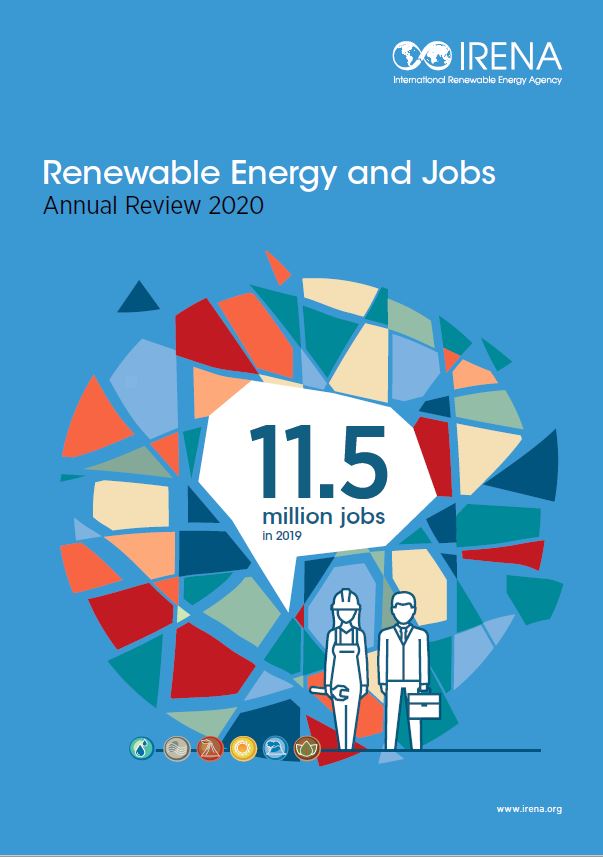
Every five years between 2 and 7 years of age, the Census Bureau collects vital statistics that is essential for understanding the economy. The Economic Census provides the basis for all industry and business statistics.
The Economic Census surveys business establishments based on the primary activity of each business. The establishments classified into different industries are determined by the activity they perform as well as their geographical location. This classification is derived from the North American Industry Classification System (NAICS).
Businesses and business owners
Surveys of entrepreneurs and businesses are conducted using a company/firm basis rather than an establishment. Companies and firms are defined by businesses with paid employees who report annual receipts at least $1,000. This survey covers sole proprietorships, nonfarm partners and reimbursable companies that are subjected to the Internal Revenue Service Tax.
Characteristics of business owners and firms
The Census Bureau's Survey of Business Owners includes both minority and female business owners. It was first a special project in 1969 for minority-owned companies, but it became part of the Economic Census in 1972 with the Survey of Women-Owned Businesses.
This is a relational database with information on 6 million single units and 1.8million multi-units. The Bureau uses the information in its economic data programs including the Census Bureau’s Economic Census and the County Business Patterns Program, as well as special summary and reimbursable statistics for non-employers.
Business Register and Census Bureau's Statistical Abstract of Business Enterprises
SBO stands for Statistical Abstract of Business Enterprises. It is the Census Bureau’s main source of infomation on non-employers. This database is a multi-relational database containing records for every known establishment in the United States with paid employees. The data is collected by firm or owner and used to compile the statistics for the Economic Census and Survey of Business Owners.
SBO contains a number statistical measures that are not included in other census programmes, including establishment births, deaths, firm startups and shutdowns, job creation, and destruction. The SBO also includes demographic characteristics of owners, such as age and education, and provides information about home-based business and participation in franchises.
SBO Data for Women and Minority Owned Businesses
The Survey of Minority and Women-Owned Business (SMWOB) is an annual survey of businesses other than farms. It includes firms that file income tax as sole proprietorships, partnerships, corporations or individual proprietorships as well as those with at least $1,000 in receipts per year. The survey is the primary source for statistics on minority- and women owned businesses. It also provides an estimate of their annual total receipts.
This is a valuable resource for researchers who are interested in minority- and women's-owned business. It also gives a general overview of racial differences among different state-industry classes, ZIP codes and other categories.
FAQ
What are manufacturing and logistics?
Manufacturing is the act of producing goods from raw materials using machines and processes. Logistics covers all aspects involved in managing supply chains, including procurement and production planning. Sometimes manufacturing and logistics are combined to refer to a wider term that includes both the process of creating products as well as their delivery to customers.
How can I learn about manufacturing?
The best way to learn about manufacturing is through hands-on experience. However, if that's not possible, you can always read books or watch educational videos.
What is production plan?
Production Planning involves developing a plan for all aspects of the production, including scheduling, budgeting, casting, crew, location, equipment, props, etc. It is important to have everything ready and planned before you start shooting. It should also contain information on achieving the best results on set. This includes shooting schedules, locations, cast lists, crew details, and equipment requirements.
First, you need to plan what you want to film. You might have an idea of where you want to film, or you may have specific locations or sets in mind. Once you have determined your scenes and locations, it is time to start figuring out the elements that you will need for each scene. For example, you might decide that you need a car but don't know exactly what model you want. If this is the case, you might start searching online for car models and then narrow your options by selecting from different makes.
Once you have found the right car, you can start thinking about extras. Do you have people who need to be seated in the front seat? Or perhaps you need someone walking around the back of the car? Maybe you want to change the interior color from black to white? These questions will help guide you in determining the ideal look and feel for your car. Another thing you can do is think about what type of shots are desired. What type of shots will you choose? Maybe you want the engine or the steering wheels to be shown. All of these things will help you identify the exact style of car you want to film.
Once you have made all the necessary decisions, you can start to create a schedule. You can create a schedule that will outline when you must start and finish your shoots. You will need to know when you have to be there, what time you have to leave and when your return home. So everyone is clear about what they need to do. Hire extra staff by booking them ahead of time. There is no point in hiring someone who won't turn up because you didn't let him know.
When creating your schedule, you will also need to consider the number of days you need to film. Some projects take only a few days while others can last several weeks. While creating your schedule, it is important to remember whether you will require more than one shot per day. Multiplying takes in the same area will result both in increased costs and a longer time. It's better to be safe than sorry and shoot less takes if you're not certain whether you need more takes.
Budgeting is another important aspect of production planning. Setting a realistic budget is essential as it will allow you to work within your means. Remember that you can always reduce the budget later on if you run into unforeseen problems. You shouldn't underestimate the amount you'll spend. If you underestimate the cost of something, you will have less money left after paying for other items.
Production planning is a complicated process. But once you understand how everything works together, it becomes much easier to plan future project.
Is it necessary to be familiar with Manufacturing Processes before we learn about Logistics.
No. No. Understanding the manufacturing process will allow you to better understand logistics.
Why is logistics important in manufacturing?
Logistics are an integral part any business. They are essential to any business's success.
Logistics play a key role in reducing expenses and increasing efficiency.
Can some manufacturing processes be automated?
Yes! Automation has been around since ancient times. The wheel was invented by the Egyptians thousands of years ago. Robots are now used to assist us in assembly lines.
In fact, there are several applications of robotics in manufacturing today. They include:
-
Robots for assembly line
-
Robot welding
-
Robot painting
-
Robotics inspection
-
Robots that create products
Manufacturing can also be automated in many other ways. 3D printing is a way to make custom products quickly and without waiting weeks or months for them to be manufactured.
Statistics
- (2:04) MTO is a production technique wherein products are customized according to customer specifications, and production only starts after an order is received. (oracle.com)
- In 2021, an estimated 12.1 million Americans work in the manufacturing sector.6 (investopedia.com)
- According to the United Nations Industrial Development Organization (UNIDO), China is the top manufacturer worldwide by 2019 output, producing 28.7% of the total global manufacturing output, followed by the United States, Japan, Germany, and India.[52][53] (en.wikipedia.org)
- Job #1 is delivering the ordered product according to specifications: color, size, brand, and quantity. (netsuite.com)
- [54][55] These are the top 50 countries by the total value of manufacturing output in US dollars for its noted year according to World Bank.[56] (en.wikipedia.org)
External Links
How To
How to Use Six Sigma in Manufacturing
Six Sigma is defined as "the application of statistical process control (SPC) techniques to achieve continuous improvement." Motorola's Quality Improvement Department, Tokyo, Japan, developed it in 1986. The basic idea behind Six Sigma is to improve quality by improving processes through standardization and eliminating defects. Many companies have adopted Six Sigma in recent years because they believe that there are no perfect products and services. Six Sigma's main objective is to reduce variations from the production average. This means that if you take a sample of your product, then measure its performance against the average, you can find out what percentage of the time the process deviates from the norm. If there is a significant deviation from the norm, you will know that something needs to change.
Understanding the dynamics of variability within your business is the first step in Six Sigma. Once you understand this, you can then identify the causes of variation. It is important to identify whether the variations are random or systemic. Random variations are caused by human errors. Systematic variations can be caused by outside factors. If you make widgets and some of them end up on the assembly line, then those are considered random variations. You might notice that your widgets always fall apart at the same place every time you put them together.
Once you've identified the problem areas you need to find solutions. The solution could involve changing how you do things, or redesigning your entire process. Test them again once you've implemented the changes. If they don’t work, you’ll need to go back and rework the plan.