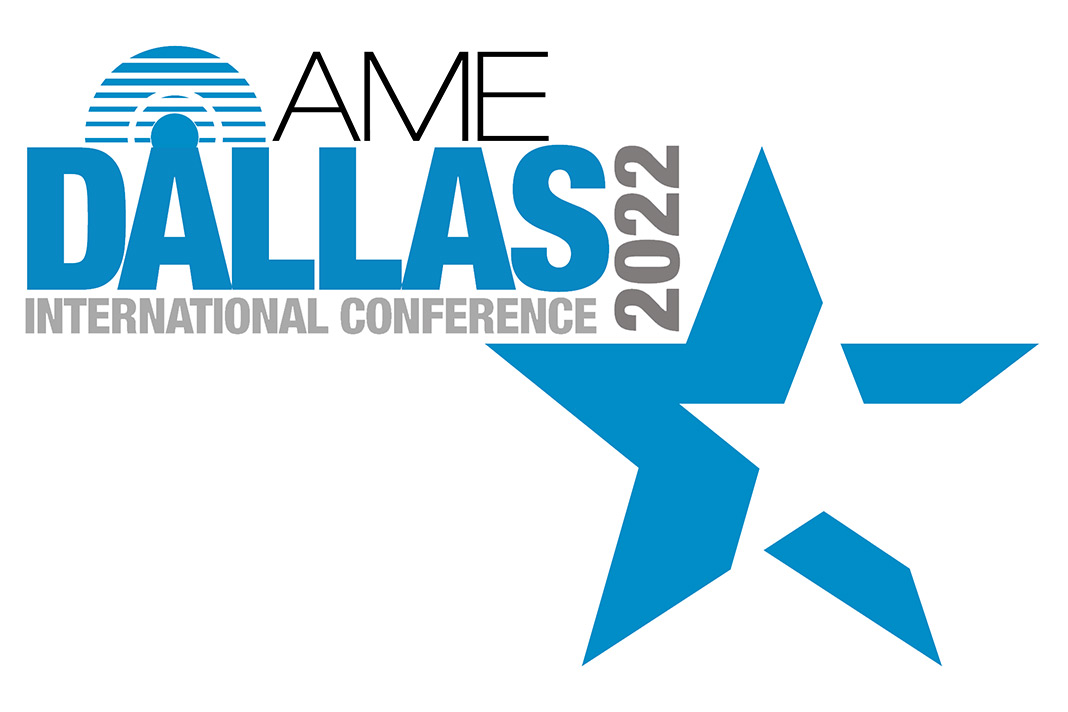
The purchase and delivery management of materials is the responsibility of a material manager. They come typically from inventory or material management. Their knowledge of the types of raw materials required to make a product is valuable. They should be resourceful in locating these materials. They need to build good relationships and negotiate the best delivery and price rates with vendors. It is also important to consider the salary of a material manager. Listed below are some tips to help you get the job.
Job description
A materials manager is responsible to manage stock and purchasing operations. They must have excellent problem-solving and stock management skills. A material manager's job involves managing inventory, budgets and efficiencies. As well as managing inventory, the position must coordinate and supervise subordinates. This role requires an advanced degree. Materials managers must also have experience in similar roles.
A materials manager usually holds a bachelor’s degree in business administration, or another related field. A master's degree is preferred for supervisor positions. Although an advanced degree may be more useful than on the job experience, education can also be beneficial. Materials managers should have at minimum three years of experience working in a manufacturing environment before they can apply for a managerial position.
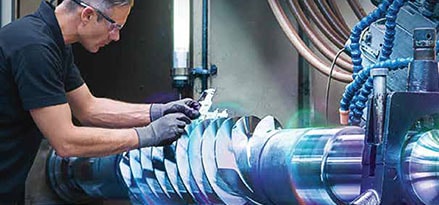
Responsibilities
Materials managers' role is to assess existing projects and decide what materials are needed to make finished products. The materials manager may also keep track of inventory using the company's supply-chain management system. He or she could also be responsible for stocking spare parts to repair faulty products. He or she may also be responsible in training employees about the proper use of inventory management systems. These positions are important in many companies. However, not all of these require extensive training.
Job Description: A material supervisor oversees the procurement of materials to a company. They also oversee the storage and distribution. The job requires experience in supply chain management, inventory control, and logistics. These skills are a plus. They will also work closely with the purchasing department, vendors, and production departments to determine requirements and plan distribution. These positions require a bachelor’s degree in business as well as a strong analytical mind.
Education necessary
If you are considering a career as a material manager, you should be aware of the educational requirements for this position. This position requires a strong management skill set and a solid understanding of logistics and receipt. As a material manager, you will work with QC personnel and higher-level managers. Planning functions and delegating responsibility to subordinates are part of your job description. Managers should be able evaluate subordinates' performance, and foster harmonious working relationships.
Generally, materials managers have a Bachelor's degree in a related field. For companies to hire material managers with this education, they may require at least two-three years of experience. Higher-ranking positions might require additional education. Many material managers hold certifications, such as those offered by the American Purchasing Society (CPSCP) and the APICS (the Association of Purchasing Professionals).
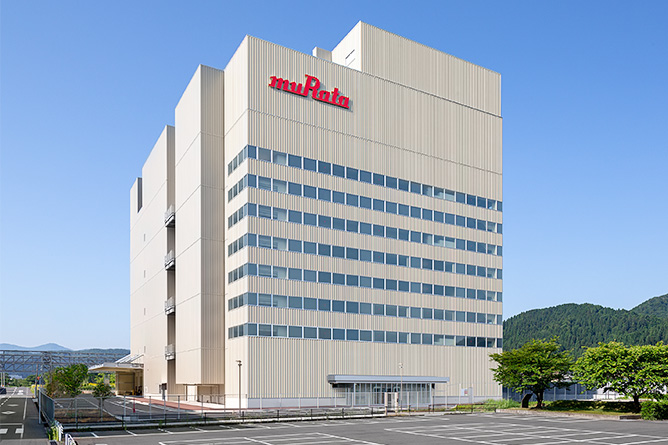
Salary
The average salary for Materials Managers is approximately $78,500. This number is based on the salaries of 106 TurboTax users. This figure includes taxable wages and tips as well as bonuses. The exact salary varies, from $25,000 to $168,000, depending on experience and education. To reflect inflation, salary data is adjusted annually. If you're considering a career as a Materials Manager, read on to discover the typical salary for this role.
To become a materials manager, you'll need to have a background in management. It is important to have an understanding of logistics, shipping, and receiving. A good understanding of the industry you wish to work in is essential if you work in the manufacturing sector. This will allow your to negotiate the best possible prices with suppliers. The type of training and experience a materials manager has will determine the salary they earn.
FAQ
Is there anything we should know about Manufacturing Processes prior to learning about Logistics.
No. No. Understanding the manufacturing process will allow you to better understand logistics.
Can we automate some parts of manufacturing?
Yes! Yes. The Egyptians discovered the wheel thousands and years ago. Nowadays, we use robots for assembly lines.
In fact, there are several applications of robotics in manufacturing today. These include:
-
Line robots
-
Robot welding
-
Robot painting
-
Robotics inspection
-
Robots that create products
Automation could also be used to improve manufacturing. 3D printing makes it possible to produce custom products in a matter of days or weeks.
What are the responsibilities of a logistic manager?
A logistics manager ensures that all goods are delivered on time and without damage. This is accomplished by using the experience and knowledge gained from working with company products. He/she also needs to ensure adequate stock to meet demand.
Statistics
- In 2021, an estimated 12.1 million Americans work in the manufacturing sector.6 (investopedia.com)
- According to a Statista study, U.S. businesses spent $1.63 trillion on logistics in 2019, moving goods from origin to end user through various supply chain network segments. (netsuite.com)
- Job #1 is delivering the ordered product according to specifications: color, size, brand, and quantity. (netsuite.com)
- Many factories witnessed a 30% increase in output due to the shift to electric motors. (en.wikipedia.org)
- It's estimated that 10.8% of the U.S. GDP in 2020 was contributed to manufacturing. (investopedia.com)
External Links
How To
How to Use 5S for Increasing Productivity in Manufacturing
5S stands as "Sort", Set In Order", Standardize", Separate" and "Store". The 5S methodology was developed at Toyota Motor Corporation in 1954. It assists companies in improving their work environments and achieving higher efficiency.
This method aims to standardize production processes so that they are repeatable, measurable and predictable. It means tasks like cleaning, sorting or packing, labeling, and storing are done every day. Through these actions, workers can perform their jobs more efficiently because they know what to expect from them.
Five steps are required to implement 5S: Sort, Set In Order, Standardize. Separate. Each step is a different action that leads to greater efficiency. If you sort items, it makes them easier to find later. When you arrange items, you place them together. Next, organize your inventory into categories and store them in containers that are easily accessible. Make sure everything is correctly labeled when you label your containers.
Employees must be able to critically examine their work practices. Employees must understand why they do certain tasks and decide if there's another way to accomplish them without relying on the old ways of doing things. They will need to develop new skills and techniques in order for the 5S system to be implemented.
In addition to improving efficiency, the 5S system also increases morale and teamwork among employees. They will feel motivated to strive for higher levels of efficiency once they start to see results.