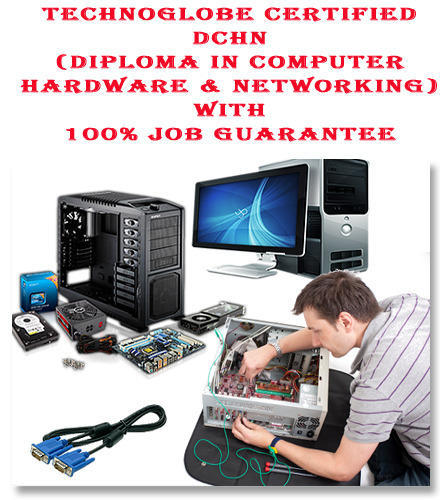
The United States is currently the third-largest manufacturer in the globe. Its manufacturing output reached a record high of $2.00 trillion in Q1 2018, nearly double what it was before the Great Recession. Despite the strong domestic economy, the United States' manufacturing industry continues to take a sloppy approach to solving its current problems. This could be due to a shortage of skilled labor or investment, but we must be more aggressive in dealing with the problems facing our industry.
Since 2000, jobs have dropped by 5 million
Five million US manufacturing jobs have been lost in the last five years. Some claim that the rise of trade with China is to blame. However, only about a quarter the decline in manufacturing jobs can be attributed to this. In addition to trade with China, manufacturing jobs were lost in local markets that didn't compete with Chinese imports. But the reasons for the decline in manufacturing jobs are many. The following are some of the reasons:
The US manufacturing sector saw almost a third decline in employment over the last 20 decades. It stood at 17 million in 1965, and fell to just 12 million in 2010. Trade is not responsible for the decline in manufacturing jobs. However, it has been caused structural problems like a decline of capital investment, output, and productivity. These problems are not sustainable. While productivity gains have a major role to play in the decline, they weren't enough to offset the loss of manufacturing jobs. Automation is the problem, and not productivity improvements.
Strong demand exists for manufactured goods
The demand for manufactured goods in the United States remains strong, despite the fact the percentage of consumers spending on them has declined over the last few decades. In 1945, 58% of personal spending on durable goods was made, while it is now only 28%. This is because the costs of manufacturing and selling durable goods have dropped, while the contents have increased. Computers, televisions, sound equipment, and other electronic devices have seen significant drops in their prices.
The US has seen an increase in manufactured goods production due to the recovery in manufacturing activity. The Fifth District Manufacturing Activity Survey shows that demand for manufactured goods is strong and production is ramping up, although supply chain bottlenecks are hampering output. Increased production has put pressure on supply chains. Many respondents reported experiencing supply chain disruptions that have affected their ability to keep necessary inventories. Backlogs of orders and vendor lead times have also increased.
Over the past decade, the trade deficit for manufactured goods has more then doubled
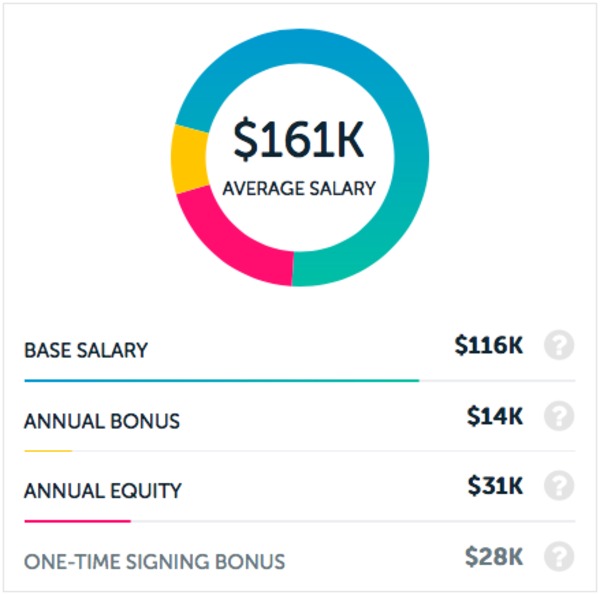
Some economists fear that the U.S.'s trade surplus may lead to lower global economic growth and greater instability among its trading partner. Others point out that high imports of US manufactured goods are not necessarily a bad thing for the U.S. economy, which is a key to maintaining global economic stability. High levels of foreign market demand can make it difficult for the U.S. to achieve full employment.
The U.S. trade deficit in manufactured goods has nearly doubled since 2000. The US deficit has been growing partly because of the increase in Chinese imports. However, the problem is more serious. This imbalance is concentrated in manufacturing where wages have dropped and employment has declined significantly since 1990. US manufacturing employment fell dramatically from 26% in 1970 to 8.5% in 2016. Some economists attribute China's increasing competition to the decline, but most blame the decline on automation, productivity increases and the shifting of consumer demand away form goods to services.
The shotgun approach of industry is the best.
The US manufacturing industry is well-respected for its advanced manufacturing efforts and has many other initiatives. However, some countries have chosen to bring the internet of everything into manufacturing. The US, in contrast, is more focused on various technologies and integrates traditional mass media with Internet marketing. The result is a shotgun approach, where companies focus on many different technologies and aim for a broad customer base.
FAQ
How can manufacturing efficiency improved?
The first step is to identify the most important factors affecting production time. Next, we must find ways to improve those factors. If you don’t know where to begin, consider which factors have the largest impact on production times. Once you have identified the factors, then try to find solutions.
What is the role and responsibility of a Production Planner?
Production planners make sure that every aspect of the project is delivered on-time, within budget, and within schedule. They also ensure that the product/service meets the client’s needs.
What are the goods of logistics?
Logistics refers to all activities that involve moving goods from A to B.
They include all aspects associated with transport including packaging, loading transporting, unloading storage, warehousing inventory management customer service, distribution returns and recycling.
Logisticians make sure that the right product arrives at the right place at the correct time and in safe conditions. Logisticians help companies improve their supply chain efficiency by providing information about demand forecasts and stock levels, production schedules, as well as availability of raw materials.
They can also track shipments in transit and monitor quality standards.
How can manufacturing avoid production bottlenecks
To avoid production bottlenecks, ensure that all processes run smoothly from the moment you receive your order to the time the product ships.
This includes both planning for capacity and quality control.
This can be done by using continuous improvement techniques, such as Six Sigma.
Six Sigma management is a system that improves quality and reduces waste within your organization.
It seeks to eliminate variation and create consistency in your work.
Statistics
- [54][55] These are the top 50 countries by the total value of manufacturing output in US dollars for its noted year according to World Bank.[56] (en.wikipedia.org)
- (2:04) MTO is a production technique wherein products are customized according to customer specifications, and production only starts after an order is received. (oracle.com)
- According to the United Nations Industrial Development Organization (UNIDO), China is the top manufacturer worldwide by 2019 output, producing 28.7% of the total global manufacturing output, followed by the United States, Japan, Germany, and India.[52][53] (en.wikipedia.org)
- It's estimated that 10.8% of the U.S. GDP in 2020 was contributed to manufacturing. (investopedia.com)
- Job #1 is delivering the ordered product according to specifications: color, size, brand, and quantity. (netsuite.com)
External Links
How To
Six Sigma in Manufacturing
Six Sigma is "the application statistical process control (SPC), techniques for continuous improvement." Motorola's Quality Improvement Department, Tokyo, Japan, developed it in 1986. Six Sigma's main goal is to improve process quality by standardizing processes and eliminating defects. This method has been adopted by many companies in recent years as they believe there are no perfect products or services. Six Sigma's main objective is to reduce variations from the production average. This means that you can take a sample from your product and then compare its performance to the average to find out how often the process differs from the norm. If there is a significant deviation from the norm, you will know that something needs to change.
Understanding how your business' variability is a key step towards Six Sigma implementation is the first. Once you have this understanding, you will need to identify sources and causes of variation. These variations can also be classified as random or systematic. Random variations occur when people make mistakes; systematic ones are caused by factors outside the process itself. For example, if you're making widgets, and some of them fall off the assembly line, those would be considered random variations. If however, you notice that each time you assemble a widget it falls apart in exactly the same spot, that is a problem.
Once you identify the problem areas, it is time to create solutions. This could mean changing your approach or redesigning the entire process. Once you have implemented the changes, it is important to test them again to ensure they work. If they don’t work, you’ll need to go back and rework the plan.