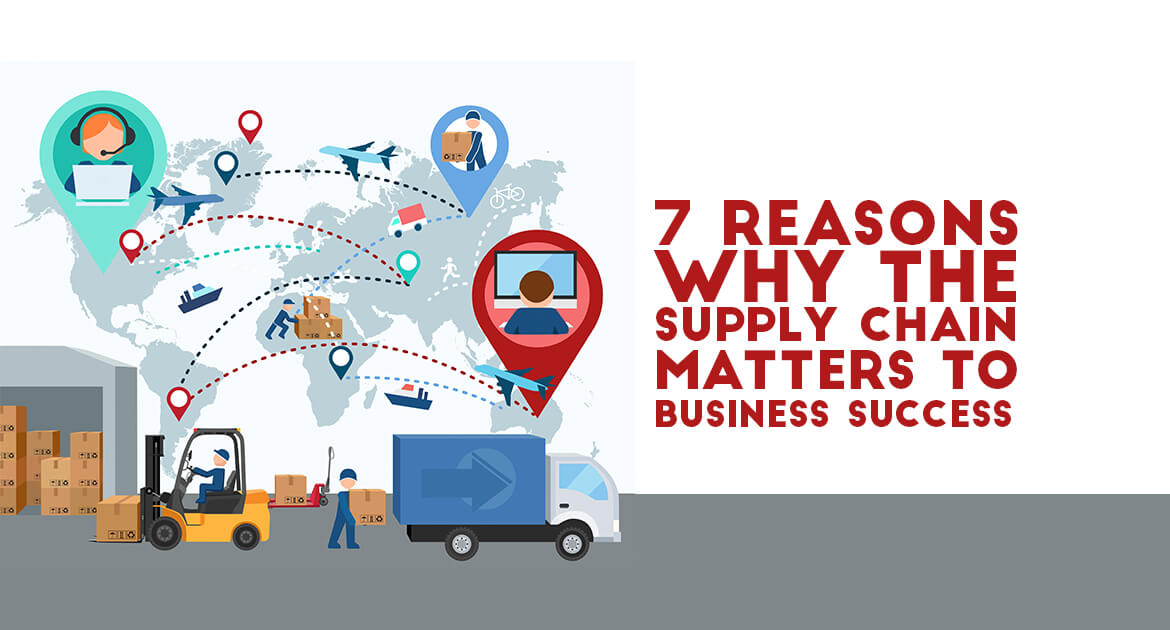
Are you looking for a job in Walmart asset security? Learn more about the salary and safety procedures associated with these positions. Apply today if you feel that Walmart is the right fit for you. You can find out more about Walmart's Asset Protection Associate Salary Range, Compensation, and Safety procedures. Also, learn more about the benefits of this position. Online applications are available for more information. To get started, you need to have an account.
Walmart associates for asset protection are paid a range of salary
Walmart Asset Protection Associate salaries range from Rs 1.8 Lakhs to Rs 2.2 Lakhs annually. This salary is calculated using statistical methods as well as actual salaries from 6 employees. The following information will help you learn more about the job. Based on six anonymous Glassdoor salaries, the following salary estimates were generated by Asset Protection Associates. This information does not include bonuses, overtime, or other compensation.
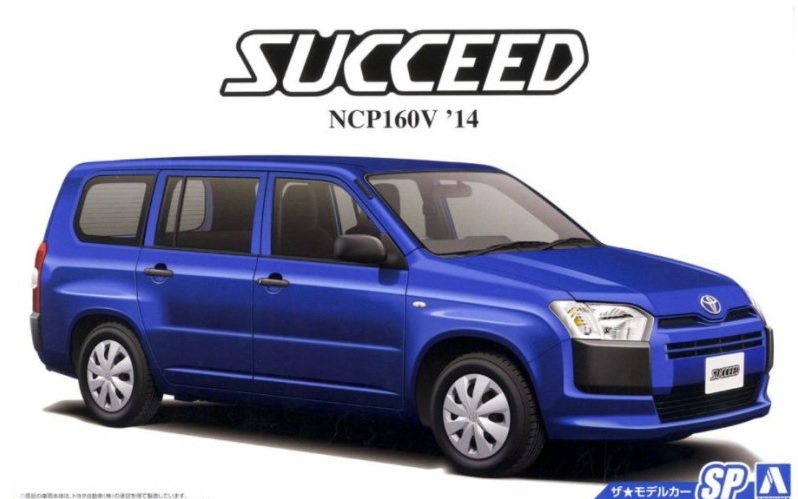
This job is ideal for people who have criminal records and a background in loss prevention. Walmart has many career options and pay ranges available for asset protection associates, regardless of whether you're looking for a career as a criminal justice or retail loss prevention specialist. Walmart Careers provides job descriptions that can be accessed by interested applicants. You will find more information about the job and responsibilities. Simply sign the disclosures to apply and create a profile. If you are applying for a position as an AP manager, you will need to fill out an online application and upload a copy of your resume.
Safety procedures
Walmart is one the most important and diverse retailers in the United States. This means that there are many safety and security issues. Here are the top priorities and safety protocols for Walmart’s Asset Protection program. Mike Lamb, vice president for Walmart US's asset safety and protection department, describes how these policies work to protect Walmart's valuable assets. He also addresses the most common issues and potential solutions. This program protects the company's assets and keeps customers and associates safe.
Associate: Walmart Asset Protection Program Associates are the frontline of crime prevention. They help store managers and employees keep their stores safe from theft and fraud. Entry-level positions do not require formal qualifications, but managers must hold a bachelor's degree in criminal law or a Loss Prevention Qualified Certificate. Entry-level positions do not require a Loss Prevention Qualified Certificate, but a degree in criminal law or a Loss Prevention Qualified Certificate can be very beneficial.
Compensation
Based on 974 employees with the same job title, Walmart Asset Protection's average annual compensation is $33,000. The figure includes tips, taxable wages and bonuses and can range from $18,500 to $53,000 depending upon the person's education and experience. These figures are not representative of actual Walmart Asset Protection salaries. However, this information can be used as a guideline to help you determine what salary you should receive.
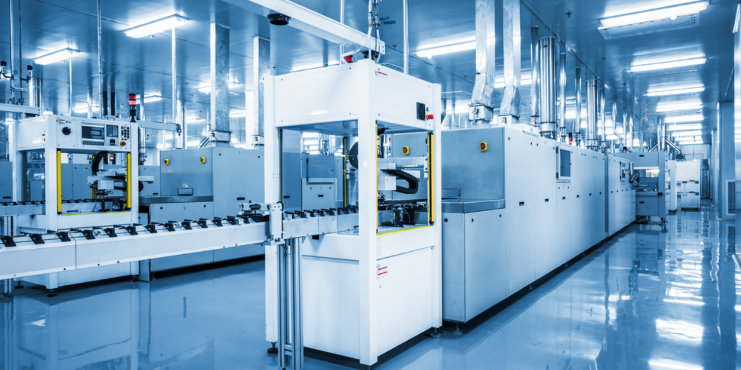
Wal-Mart will continue to give bonuses to store managers that can be tied to store performance. Walmart also acknowledges that longer-term employees are likely to be given raises than those who only started. Associates with years of experience can request raises up to twice a year. The average hourly wage range is between $12 and $16. The following table shows you the typical Walmart Ap Host salary. Visit the official Walmart website for more information.
FAQ
How is a production manager different from a producer planner?
The primary difference between a producer planner and a manager of a project is that the manager usually plans and organizes the whole project, while a production planner is only involved in the planning stage.
Why is logistics important for manufacturing?
Logistics is an integral part of every business. They enable you to achieve outstanding results by helping manage product flow from raw materials through to finished goods.
Logistics play an important role in reducing costs as well as increasing efficiency.
Are there ways to automate parts of manufacturing?
Yes! Yes! Automation has existed since ancient times. The Egyptians created the wheel thousands years ago. Robots are now used to assist us in assembly lines.
In fact, there are several applications of robotics in manufacturing today. These include:
-
Automated assembly line robots
-
Robot welding
-
Robot painting
-
Robotics inspection
-
Robots that create products
There are many other examples of how manufacturing could benefit from automation. For example, 3D printing allows us to make custom products without having to wait for weeks or months to get them manufactured.
How can manufacturing efficiency be improved?
The first step is to determine the key factors that impact production time. We then need to figure out how to improve these variables. If you don’t know where to begin, consider which factors have the largest impact on production times. Once you've identified them all, find solutions to each one.
What is the distinction between Production Planning or Scheduling?
Production Planning (PP), or production planning, is the process by which you determine what products are needed at any given time. Forecasting and identifying production capacity are two key elements to this process.
Scheduling is the process of assigning specific dates to tasks so they can be completed within the specified timeframe.
What are the 7 Rs of logistics.
The acronym 7R's of Logistic is an acronym that stands for seven fundamental principles of logistics management. It was developed and published by the International Association of Business Logisticians in 2004 as part of the "Seven Principles of Logistics Management".
The following letters form the acronym:
-
Responsive - ensure all actions are legal and not harmful to others.
-
Reliable - Have confidence in your ability to fulfill all of your commitments.
-
Be responsible - Use resources efficiently and avoid wasting them.
-
Realistic – Consider all aspects, including cost-effectiveness as well as environmental impact.
-
Respectful – Treat others fairly and equitably.
-
Responsive - Look for ways to save time and increase productivity.
-
Recognizable - provide customers with value-added services.
Statistics
- According to a Statista study, U.S. businesses spent $1.63 trillion on logistics in 2019, moving goods from origin to end user through various supply chain network segments. (netsuite.com)
- [54][55] These are the top 50 countries by the total value of manufacturing output in US dollars for its noted year according to World Bank.[56] (en.wikipedia.org)
- Job #1 is delivering the ordered product according to specifications: color, size, brand, and quantity. (netsuite.com)
- You can multiply the result by 100 to get the total percent of monthly overhead. (investopedia.com)
- It's estimated that 10.8% of the U.S. GDP in 2020 was contributed to manufacturing. (investopedia.com)
External Links
How To
How to Use the Just In Time Method in Production
Just-in-time is a way to cut costs and increase efficiency in business processes. It's the process of obtaining the right amount and timing of resources when you need them. This means that you only pay the amount you actually use. Frederick Taylor first coined this term while working in the early 1900s as a foreman. After observing how workers were paid overtime for late work, he realized that overtime was a common practice. He decided that workers would be more productive if they had enough time to complete their work before they started to work.
JIT is an acronym that means you need to plan ahead so you don’t waste your money. The entire project should be looked at from start to finish. You need to ensure you have enough resources to tackle any issues that might arise. You will have the resources and people to solve any problems you anticipate. This way, you won't end up paying extra money for things that weren't really necessary.
There are many JIT methods.
-
Demand-driven: This JIT is where you place regular orders for the parts/materials that are needed for your project. This will allow for you to track the material that you have left after using it. This will allow you to calculate how long it will take to make more.
-
Inventory-based: This is a type where you stock the materials required for your projects in advance. This allows you to predict how much you can expect to sell.
-
Project-driven: This method allows you to set aside enough funds for your project. Once you have an idea of how much material you will need, you can purchase the necessary materials.
-
Resource-based JIT: This is the most popular form of JIT. Here, you allocate certain resources based on demand. If you have many orders, you will assign more people to manage them. If you don't receive many orders, then you'll assign fewer employees to handle the load.
-
Cost-based : This is similar in concept to resource-based. But here, you aren't concerned about how many people your company has but how much each individual costs.
-
Price-based: This is similar to cost-based but instead of looking at individual workers' salaries, you look at the total company price.
-
Material-based is an alternative to cost-based. Instead of looking at the total cost in the company, this method focuses on the average amount of raw materials that you consume.
-
Time-based: Another variation of resource-based JIT. Instead of focusing on how much each employee costs, you focus on how long it takes to complete the project.
-
Quality-based JIT: This is another variation of resource based JIT. Instead of thinking about the cost of each employee or the time it takes to produce something, you focus on how good your product quality.
-
Value-based JIT: One of the most recent forms of JIT. In this scenario, you're not concerned about how products perform or whether customers expect them to meet their expectations. Instead, your goal is to add value to the market.
-
Stock-based: This inventory-based approach focuses on how many items are being produced at any one time. It's used when you want to maximize production while minimizing inventory.
-
Just-intime (JIT), planning is a combination JIT management and supply chain management. It is the process of scheduling components' delivery as soon as they have been ordered. It's important as it reduces leadtimes and increases throughput.