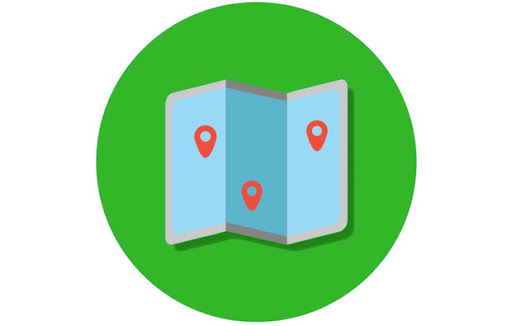
CEVA Logistics offers logistics services. These companies offer various benefits to employees. These companies offer a variety of benefits to their employees. Here are the steps you need to take in order for you apply for a job as a logistics professional. You can search for jobs by region.
Job description
CEVA Logistics provides a wide range of job opportunities for individuals with various educations and work experience. The company's core values are dedication to customer service and on-time delivery. The company is also looking for individuals who are passionate and willing to work hard. Candidates who have some or no previous experience in logistics and who have a positive attitude will be given preference when applying for a job.
CEVA Logistics is seeking a Process/Industrial Engineer to design and implement new processes and improve efficiency. The ideal candidate is energetic, self-driven and able to work with other plant employees. These tasks include managing projects and designing process layouts. They need to be knowledgeable in robotics and the other manufacturing processes that can improve quality and efficiency.
Education is necessary
CEVA Logistics offers many opportunities for candidates interested in a career with the company, including sales rep and warehouse manager. You can also choose to be operations supervisors. This involves overseeing all aspects of the company's day, including inventory and scheduling. These positions usually have a team. Candidates for these roles typically have a bachelor’s degree and supervisory or management experience.
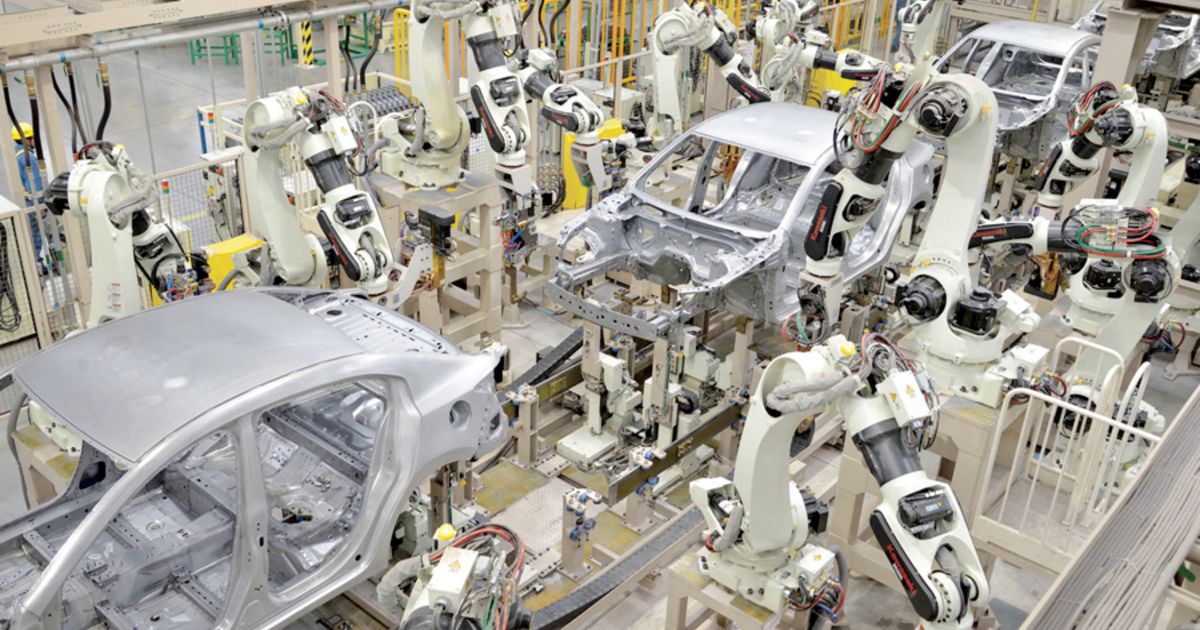
You can apply online, or through recruiters, if you are interested. To apply online, candidates must first create an account on the company’s career portal. Candidates can connect to their LinkedIn profiles to create a profile and attach their resumes. After creating their profile, they can choose the desired country or region and get in touch to a recruiter.
Salary range
To apply for a CEVA Logistics position, you must first create an account on the company's career portal. You can connect to your LinkedIn profile and upload a resume. Additionally, you can manually input information about your experience, skills, and other relevant information. Next, you will need to choose the region or country in which you want to work. You'll then receive contact information for a recruiter in the region.
The salary structure at CEVA Logistics varies depending on the job title, experience and where you live. The Vice President of CEVA Logistics makes $166,000 a year, while an Air Break Bulk Specialist earns $24,000. However, salaries can be different in each location, depending on the economic conditions in that area.
Localities
CEVA Logistics offers a rewarding career in logistics. The company has many job openings at various locations. They have different responsibilities, and different experience requirements. To apply for a specific job, just type the job title in search box along with your location. You can search for Edison job listings. Experience in driving is a must. You also need to be able communicate with customers and other employees.
There are many career opportunities at CEVA Logistics, including supervisory positions. Supervisors oversee the day-to-day operations of the company. They manage inventory, coordinate schedules, and oversee the activities of employees. Operations supervisors are typically responsible for managing a team, coordinating schedules and overseeing employees. Strong leadership and management skills are also necessary.
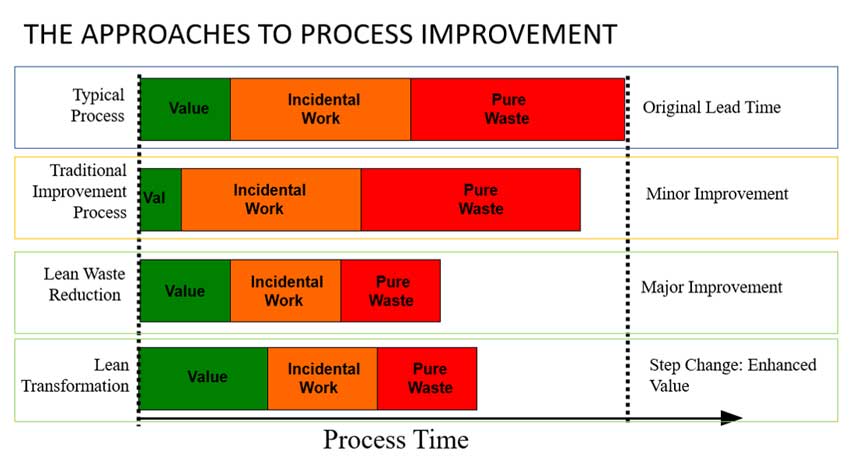
Applying online
CEVA Logistics can help you find a job in the logistic industry. Ceva Logistics, an international logistics company, was established in 2006 as a result the merger of two Australian and Texan contracts logistics companies. Its operations are now located in more than 950 countries. Job seekers can apply for full-time or part-time positions.
Although many positions at CEVA do require some experience, most are entry-level. Other positions require little or no experience. Customer service representative, dispatcher, and admin clerk are some of the entry-level jobs.
FAQ
What are the 7 Rs of logistics management?
The acronym "7R's" of Logistics stands for seven principles that underpin logistics management. It was developed by the International Association of Business Logisticians (IABL) and published in 2004 as part of its "Seven Principles of Logistics Management" series.
The following letters make up the acronym:
-
Responsible – ensure that all actions are legal and don't cause harm to anyone else.
-
Reliable - Have confidence in your ability to fulfill all of your commitments.
-
Use resources effectively and sparingly.
-
Realistic – consider all aspects of operations, from cost-effectiveness to environmental impact.
-
Respectful - treat people fairly and equitably.
-
Responsive - Look for ways to save time and increase productivity.
-
Recognizable - provide customers with value-added services.
What are the main products of logistics?
Logistics involves the transportation of goods from point A and point B.
These include all aspects related to transport such as packaging, loading and transporting, storing, transporting, unloading and warehousing inventory management, customer service. Distribution, returns, recycling are some of the options.
Logisticians make sure that the right product arrives at the right place at the correct time and in safe conditions. They assist companies with their supply chain efficiency through information on demand forecasts. Stock levels, production times, and availability.
They also keep track of shipments in transit, monitor quality standards, perform inventories and order replenishment, coordinate with suppliers and vendors, and provide support services for sales and marketing.
What is the role of a logistics manager
A logistics manager makes sure that all goods are delivered on-time and in good condition. This is done by using his/her experience and knowledge of the company's products. He/she also needs to ensure adequate stock to meet demand.
What is the difference between a production planner and a project manager?
The primary difference between a producer planner and a manager of a project is that the manager usually plans and organizes the whole project, while a production planner is only involved in the planning stage.
Statistics
- It's estimated that 10.8% of the U.S. GDP in 2020 was contributed to manufacturing. (investopedia.com)
- You can multiply the result by 100 to get the total percent of monthly overhead. (investopedia.com)
- In the United States, for example, manufacturing makes up 15% of the economic output. (twi-global.com)
- [54][55] These are the top 50 countries by the total value of manufacturing output in US dollars for its noted year according to World Bank.[56] (en.wikipedia.org)
- (2:04) MTO is a production technique wherein products are customized according to customer specifications, and production only starts after an order is received. (oracle.com)
External Links
How To
How to use 5S in Manufacturing to Increase Productivity
5S stands to stand for "Sort", “Set In Order", “Standardize", and "Store". The 5S methodology was developed at Toyota Motor Corporation in 1954. This methodology helps companies improve their work environment to increase efficiency.
The basic idea behind this method is to standardize production processes, so they become repeatable, measurable, and predictable. This means that daily tasks such as cleaning and sorting, storage, packing, labeling, and packaging are possible. Through these actions, workers can perform their jobs more efficiently because they know what to expect from them.
Five steps are required to implement 5S: Sort, Set In Order, Standardize. Separate. Each step is a different action that leads to greater efficiency. If you sort items, it makes them easier to find later. Once you have placed items in an ordered fashion, you will put them together. After you have divided your inventory into groups you can store them in easy-to-reach containers. Labeling your containers will ensure that everything is correctly labeled.
Employees need to reflect on how they do their jobs. Employees must understand why they do certain tasks and decide if there's another way to accomplish them without relying on the old ways of doing things. They must learn new skills and techniques in order to implement the 5S system.
In addition to improving efficiency, the 5S system also increases morale and teamwork among employees. They feel more motivated to work towards achieving greater efficiency as they see the results.