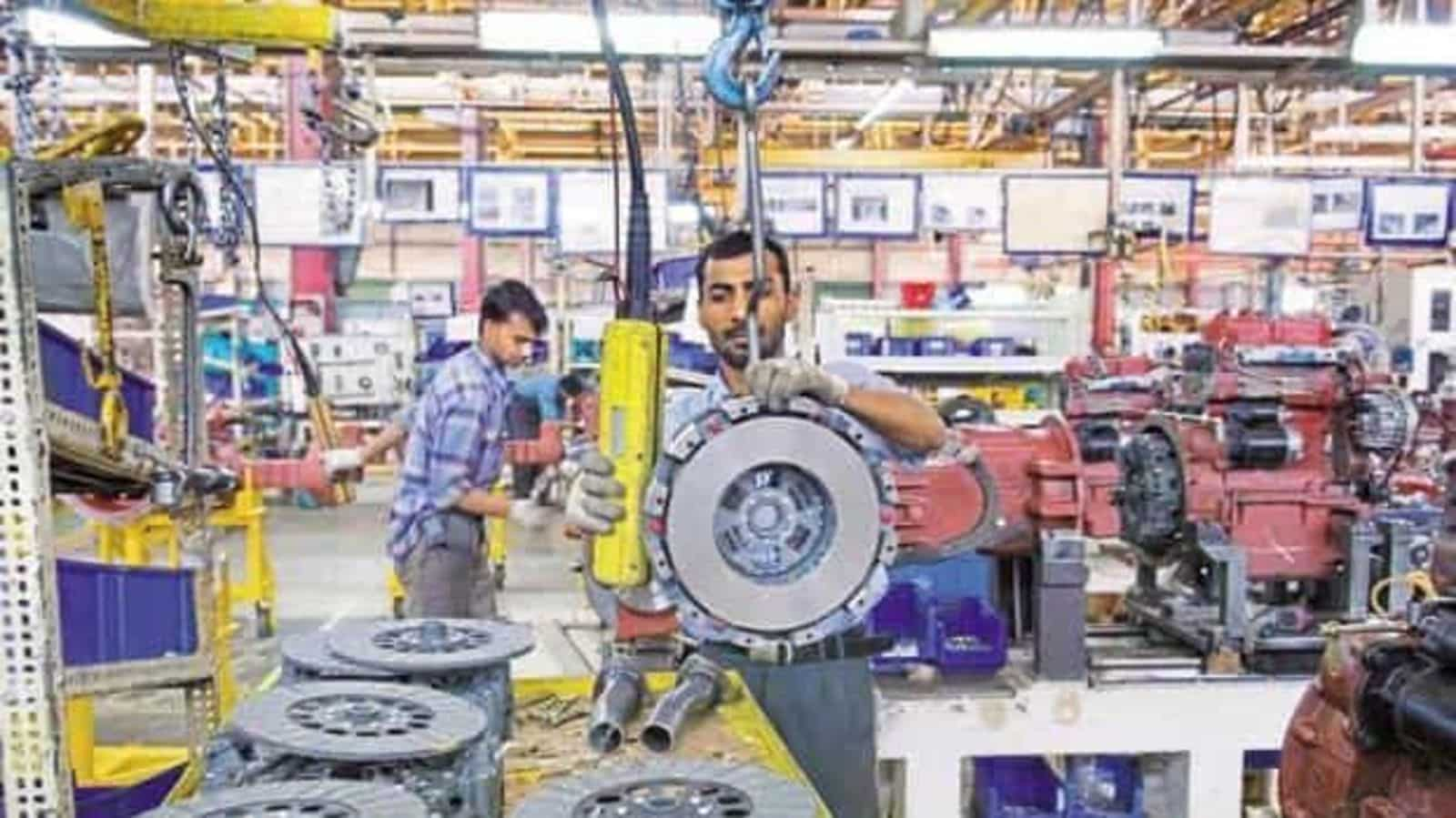
Whether you have a passion for design or you are a seasoned professional, an industrial designer career is a great choice. Industrial designers work closely with engineers and production professionals to develop product concepts. In addition to designing, industrial designers also conduct investigations into materials and perform market research. These designers often present their designs and ideas to sales staff and decision-makers. They can work in the industry full time or as freelancers.
Industrial designers design physical prototypes. The type of design may dictate the method used to create these prototypes. The prototypes are used in order to evaluate the function and design of the product. These prototypes serve as a visual representation.
Industrial designers often work with engineers to design and develop prototypes. The prototypes are designed using software like AutoCAD and SolidWorks. To sketch the plans, they meet with their clients. They should have high artistic and analytical abilities.
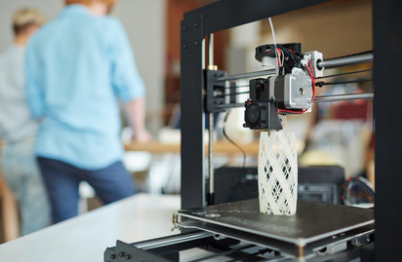
Industrial designers may also have to travel to the manufacturing or testing facilities of their clients. They may also have to meet with clients on weekends or evenings.
Industrial designers often work in offices, but they can also work as freelancers. Industrial designers have the option to work abroad. To work abroad, you must pass international exams and speak English. Additionally, you will need to have a solid education. For up to three years, industrial designers may work abroad.
Bachelor's degrees are required for industrial designers. Some employers also prefer candidates with graphic design skills. An industrial designer might want to enroll in a CAD bootcamp. These classes are typically free and can help to teach you the necessary tools. After completing these classes, you can become a professional designer. CAD certification is recognized by industrial design firms.
Industrial designers are responsible for creating functional, attractive designs. They can design many items, such medical equipment or consumer electronics. Industrial designers need to be knowledgeable about the products they design. Industrial designers must be proficient in problem-solving and writing. They also aim to lower production costs. They are creative and have a passion to design products.
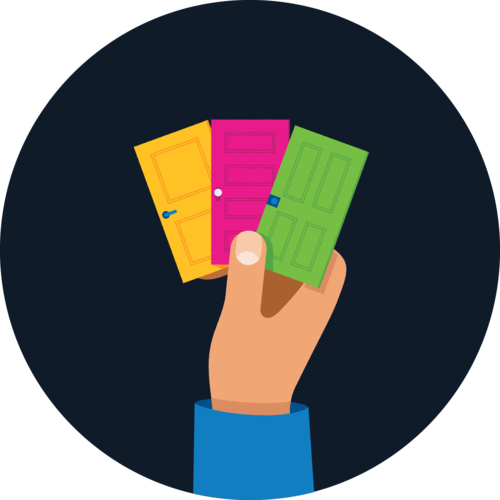
An industrial designer's resume should address their personal career goals. They should also include information about their previous work experiences and the company's needs. A portfolio of their past work should also be included. This portfolio may include design projects from internships and classes.
For prototypes and concept development, industrial designers often collaborate closely with engineers and manufacturing experts. They may also work with marketing experts to promote their products. They often present their designs to decision makers, sales personnel, and the general public. They may also travel to the manufacturing or testing facilities of their client. They may have to meet with clients or sales representatives on weekends or evenings.
FAQ
What's the difference between Production Planning & Scheduling?
Production Planning (PP) is the process of determining what needs to be produced at any given point in time. This is done through forecasting demand and identifying production capacities.
Scheduling refers the process by which tasks are assigned dates so that they can all be completed within the given timeframe.
What is production planning?
Production Planning is the creation of a plan to cover all aspects, such as scheduling, budgeting. Location, crew, equipment, props and other details. This document is designed to make sure everything is ready for when you're ready to shoot. It should also provide information about how best to produce the best results while on set. This information includes locations, crew details and equipment requirements.
First, you need to plan what you want to film. You may already know where you want the film to be shot, or perhaps you have specific locations and sets you wish to use. Once you've identified the locations and scenes you want to use, you can begin to plan what elements you need for each scene. You might decide you need a car, but not sure what make or model. In this case, you could start looking up cars online to find out what models are available and then narrow your choices by choosing between different makes and models.
After you have chosen the right car, you will be able to begin thinking about accessories. Do you have people who need to be seated in the front seat? You might also need someone to help you get around the back. You might want to change your interior color from black and white. These questions can help you decide the right look for your car. You can also think about the type of shots you want to get. Are you going to be shooting close-ups? Or wide angles? Maybe you want to show your engine or the steering wheel. All of these things will help you identify the exact style of car you want to film.
Once you have all the information, you are ready to create a plan. You will know when you should start and when you should finish shooting. You will need to know when you have to be there, what time you have to leave and when your return home. So everyone is clear about what they need to do. Book extra staff ahead of time if you need them. There is no point in hiring someone who won't turn up because you didn't let him know.
Your schedule will also have to be adjusted to reflect the number of days required to film. Some projects only take one or two days, while others may last weeks. You should consider whether you will need more than one shot per week when creating your schedule. Multiple takes of the same location will lead to higher costs and take more time. If you are unsure if you need multiple takes, it is better to err on the side of caution and shoot fewer takes rather than risk wasting money.
Another important aspect of production planning is setting budgets. As it will allow you and your team to work within your financial means, setting a realistic budget is crucial. Keep in mind that you can always reduce your budget if you face unexpected difficulties. However, it is important not to overestimate the amount that you will spend. If you underestimate how much something costs, you'll have less money to pay for other items.
Production planning is a complicated process. But once you understand how everything works together, it becomes much easier to plan future project.
What does warehouse refer to?
A warehouse is an area where goods are stored before being sold. It can be either an indoor or outdoor space. In some cases, it may be a combination of both.
What are my options for learning more about manufacturing
Experience is the best way for you to learn about manufacturing. However, if that's not possible, you can always read books or watch educational videos.
Statistics
- In 2021, an estimated 12.1 million Americans work in the manufacturing sector.6 (investopedia.com)
- (2:04) MTO is a production technique wherein products are customized according to customer specifications, and production only starts after an order is received. (oracle.com)
- It's estimated that 10.8% of the U.S. GDP in 2020 was contributed to manufacturing. (investopedia.com)
- According to a Statista study, U.S. businesses spent $1.63 trillion on logistics in 2019, moving goods from origin to end user through various supply chain network segments. (netsuite.com)
- In the United States, for example, manufacturing makes up 15% of the economic output. (twi-global.com)
External Links
How To
How to Use the Just In Time Method in Production
Just-intime (JIT), a method used to lower costs and improve efficiency in business processes, is called just-in-time. It's the process of obtaining the right amount and timing of resources when you need them. This means you only pay what you use. The term was first coined by Frederick Taylor, who developed his theory while working as a foreman in the early 1900s. Taylor observed that overtime was paid to workers if they were late in working. He decided to ensure workers have enough time to do their jobs before starting work to improve productivity.
The idea behind JIT is that you should plan ahead and have everything ready so you don't waste money. You should also look at the entire project from start to finish and make sure that you have sufficient resources available to deal with any problems that arise during the course of your project. If you anticipate that there might be problems, you'll have enough people and equipment to fix them. This way you won't be spending more on things that aren’t really needed.
There are many JIT methods.
-
Demand-driven JIT: This is a JIT that allows you to regularly order the parts/materials necessary for your project. This will allow for you to track the material that you have left after using it. This will allow you to calculate how long it will take to make more.
-
Inventory-based: You stock materials in advance to make your projects easier. This allows you predict the amount you can expect to sell.
-
Project-driven: This is an approach where you set aside enough funds to cover the cost of your project. Knowing how much money you have available will help you purchase the correct amount of materials.
-
Resource-based JIT: This type of JIT is most commonly used. Here, you allocate certain resources based on demand. For example, if there is a lot of work coming in, you will have more people assigned to them. If there aren't many orders, you will assign fewer people.
-
Cost-based: This is similar to resource-based, except that here you're not just concerned about how many people you have but how much each person costs.
-
Price-based: This is a variant of cost-based. However, instead of focusing on the individual workers' costs, this looks at the total price of the company.
-
Material-based: This approach is similar to cost-based. However, instead of looking at the total cost for the company, you look at how much you spend on average on raw materials.
-
Time-based JIT is another form of resource-based JIT. Instead of worrying about how much each worker costs, you can focus on how long the project takes.
-
Quality-based JIT: Another variation on resource-based JIT. Instead of thinking about how much each employee costs or how long it takes to manufacture something, you think about how good the quality of your product is.
-
Value-based JIT: This is the latest form of JIT. In this instance, you are not concerned about the product's performance or meeting customer expectations. Instead, your focus is on the value you bring to the market.
-
Stock-based: This inventory-based approach focuses on how many items are being produced at any one time. It's used when you want to maximize production while minimizing inventory.
-
Just-in time (JIT), planning: This is a combination JIT/supply chain management. This refers to the scheduling of the delivery of components as soon after they are ordered. It reduces lead times and improves throughput.