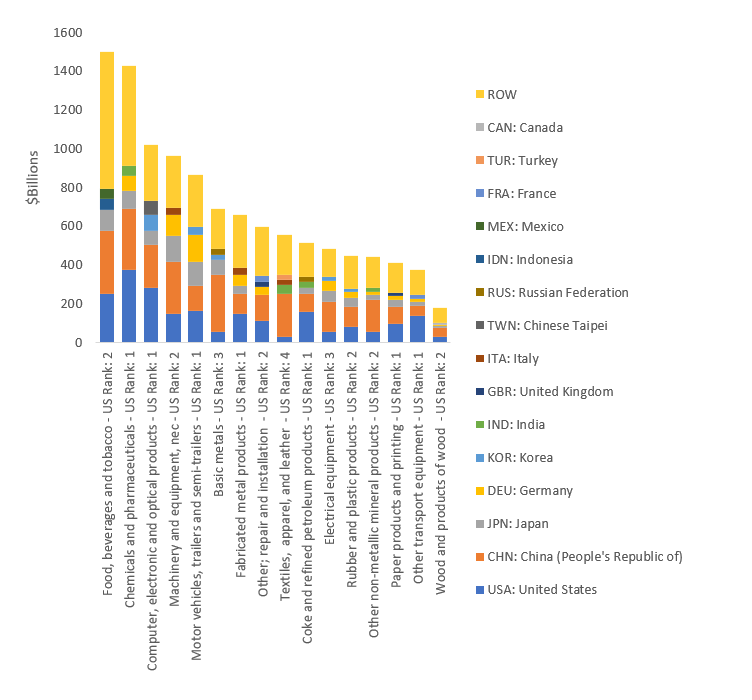
Purchasing Managers, also known as Materials Managers, are responsible for sourcing and coordinating all purchasing activities. They interact with suppliers, vendors, and other purchasing agents. They must be knowledgeable about the company's purchasing process and how to improve it. They must also know how to negotiate the best deal for the company.
Also, purchasing managers need to keep up-to date and accurate records of purchases. They analyze customer needs, analyze financial reports, evaluate vendor capabilities, and evaluate price trends. They also coordinate purchasing activities with other departments. They might have to work extra if the company is in urgent need of supplies from international market.
As well as managing inventory and logistics, purchasing managers coordinate and manage them. They make decisions about the best way to purchase products and ensure they meet company quality standards. They help to manage budgets and coordinate with their staff to ensure that purchases can be made at the most affordable price. They also work to find the best vendors and negotiate contracts.
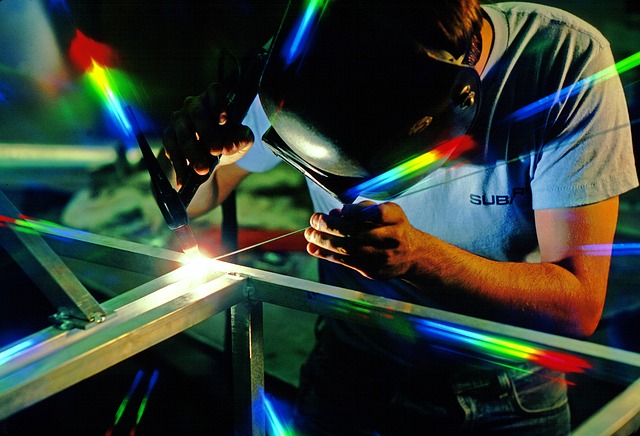
All purchasing employees are monitored and managed by Purchasing Managers. They also evaluate the quality of purchased goods, the speed of delivery, and how much they cost. They also make contacts with suppliers and sellers and visit their distribution centers. They make sure suppliers follow the terms of their contracts. They might also need to address disciplinary issues or team building.
A Purchasing Manager should have exceptional communication skills, analytic abilities, and strategic thinking skills. They should be able to evaluate the impact that different products have on a company. They should also have the knowledge to manage suppliers and their relations. They should also be able take business decisions and increase sales. They also should be able to handle complicated purchases. They must be able assess new vendors, evaluate their capabilities and determine the best vendor for the company.
A bachelor's degree or equivalent in business is required of most purchasing managers. It is helpful to have some experience in supply chain management and inventory management. They will also need to be proficient in Microsoft Office as well as other programs.
A good purchasing manager will be able negotiate the best contracts and find the best deals. They should also have the ability to coordinate all purchasing activities. Manage inventories and track vendor and supplier performance. They must also be able to manage a group of purchasing agents.
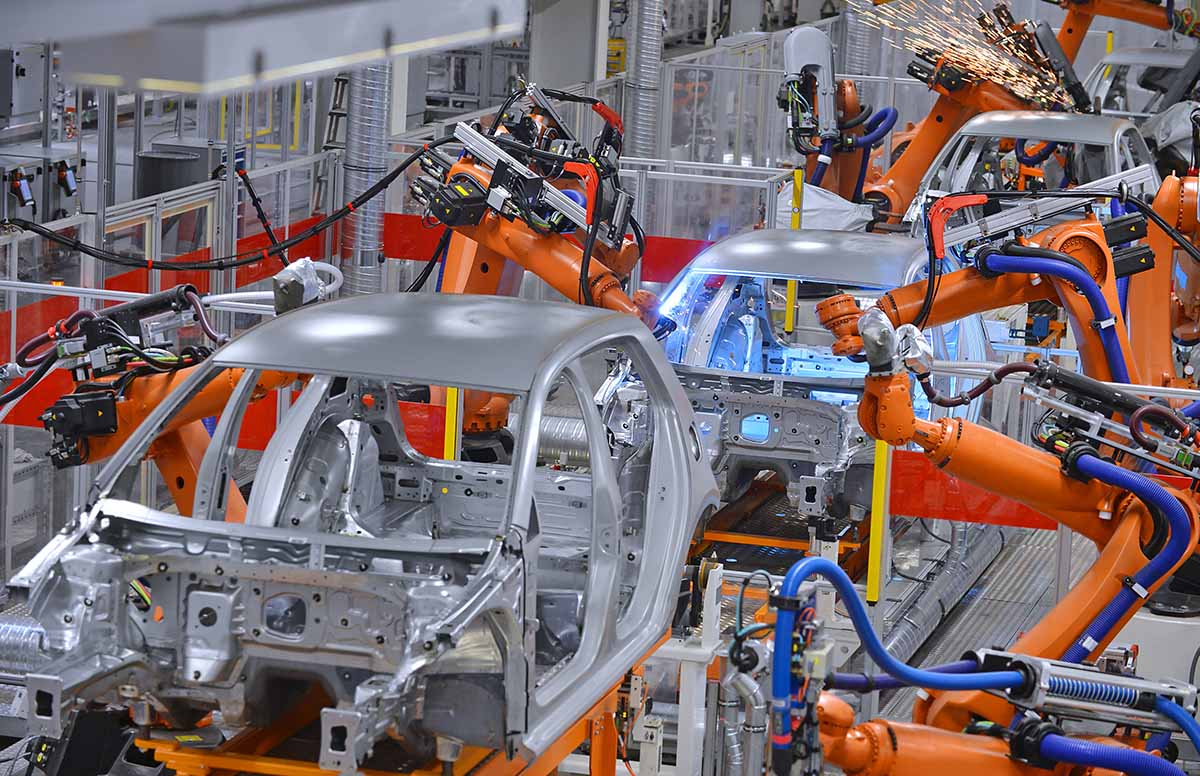
The description of the role of the purchasing manager must also mention how buying is crucial to company success. It should also include how vital it is for the company that they stay ahead of their competitors. It should also include a statement about how the company values employees' work-life balance. It should include a call for action to encourage applicants.
Purchasing Managers may also work overtime if the company needs to purchase materials and equipment for an international market. They may also have to deal with vendors and sellers and attend trade shows.
FAQ
What are the differences between these four types?
Manufacturing refers to the transformation of raw materials into useful products by using machines and processes. It involves many different activities such as designing, building, testing, packaging, shipping, selling, servicing, etc.
Why is logistics important in manufacturing?
Logistics are essential to any business. They enable you to achieve outstanding results by helping manage product flow from raw materials through to finished goods.
Logistics plays a significant role in reducing cost and increasing efficiency.
What is the difference between a production planner and a project manager?
The primary difference between a producer planner and a manager of a project is that the manager usually plans and organizes the whole project, while a production planner is only involved in the planning stage.
How can we reduce manufacturing overproduction?
Better inventory management is key to reducing excess production. This would decrease the time that is spent on inefficient activities like purchasing, storing, or maintaining excess stock. This could help us free up our time for other productive tasks.
This can be done by using a Kanban system. A Kanban Board is a visual display that tracks work progress. In a Kanban system, work items move through a sequence of states until they reach their final destination. Each state represents a different priority level.
As an example, if work is progressing from one stage of the process to another, then the current task is complete and can be transferred to the next. But if a task remains in the beginning stages it will stay that way until it reaches its end.
This allows for work to continue moving forward, while also ensuring that there is no work left behind. Managers can see how much work has been done and the status of each task at any time with a Kanban Board. This information allows them to adjust their workflow based on real-time data.
Lean manufacturing is another option to control inventory levels. Lean manufacturing is about eliminating waste from all stages of the production process. Anything that does nothing to add value to a product is waste. There are several types of waste that you might encounter:
-
Overproduction
-
Inventory
-
Packaging that is not necessary
-
Materials in excess
These ideas will help manufacturers increase efficiency and lower costs.
What is the job of a logistics manger?
A logistics manager ensures that all goods are delivered on time and without damage. This is done using his/her knowledge of the company's products. He/she must also ensure sufficient stock to meet the demand.
Why automate your warehouse
Modern warehousing is becoming more automated. With the rise of ecommerce, there is a greater demand for faster delivery times as well as more efficient processes.
Warehouses must be able to quickly adapt to changing demands. To do so, they must invest heavily in technology. Automation of warehouses offers many benefits. Here are some reasons why it's worth investing in automation:
-
Increases throughput/productivity
-
Reduces errors
-
Increases accuracy
-
Safety enhancements
-
Eliminates bottlenecks
-
Companies can scale up more easily
-
Makes workers more efficient
-
This gives you visibility into what happens in the warehouse
-
Enhances customer experience
-
Improves employee satisfaction
-
Reducing downtime and increasing uptime
-
You can be sure that high-quality products will arrive on time
-
Human error can be eliminated
-
This helps to ensure compliance with regulations
What are the 7 Rs of logistics?
The acronym "7R's" of Logistics stands for seven principles that underpin logistics management. It was developed by the International Association of Business Logisticians (IABL) and published in 2004 as part of its "Seven Principles of Logistics Management" series.
The acronym is made up of the following letters:
-
Responsible - ensure that actions are in compliance with legal requirements and do not cause harm to others.
-
Reliable - Have confidence in your ability to fulfill all of your commitments.
-
Reasonable - make sure you use your resources well and don't waste them.
-
Realistic - consider all aspects of operations, including cost-effectiveness and environmental impact.
-
Respectful - show respect and treat others fairly and fairly
-
Reliable - Find ways to save money and increase your productivity.
-
Recognizable - provide customers with value-added services.
Statistics
- Many factories witnessed a 30% increase in output due to the shift to electric motors. (en.wikipedia.org)
- According to the United Nations Industrial Development Organization (UNIDO), China is the top manufacturer worldwide by 2019 output, producing 28.7% of the total global manufacturing output, followed by the United States, Japan, Germany, and India.[52][53] (en.wikipedia.org)
- It's estimated that 10.8% of the U.S. GDP in 2020 was contributed to manufacturing. (investopedia.com)
- In the United States, for example, manufacturing makes up 15% of the economic output. (twi-global.com)
- Job #1 is delivering the ordered product according to specifications: color, size, brand, and quantity. (netsuite.com)
External Links
How To
Six Sigma and Manufacturing
Six Sigma is "the application statistical process control (SPC), techniques for continuous improvement." It was developed by Motorola's Quality Improvement Department at their plant in Tokyo, Japan, in 1986. Six Sigma's core idea is to improve the quality of processes by standardizing and eliminating defects. Many companies have adopted Six Sigma in recent years because they believe that there are no perfect products and services. Six Sigma seeks to reduce variation between the mean production value. It is possible to measure the performance of your product against an average and find the percentage of time that it differs from the norm. If there is a significant deviation from the norm, you will know that something needs to change.
Understanding the nature of variability in your business is the first step to Six Sigma. Once you understand this, you can then identify the causes of variation. It is important to identify whether the variations are random or systemic. Random variations are caused when people make mistakes. While systematic variations are caused outside of the process, they can occur. For example, if you're making widgets, and some of them fall off the assembly line, those would be considered random variations. It would be considered a systematic problem if every widget that you build falls apart at the same location each time.
Once you've identified where the problems lie, you'll want to design solutions to eliminate those problems. You might need to change the way you work or completely redesign the process. After implementing the new changes, you should test them again to see if they worked. If they didn't work, then you'll need to go back to the drawing board and come up with another plan.