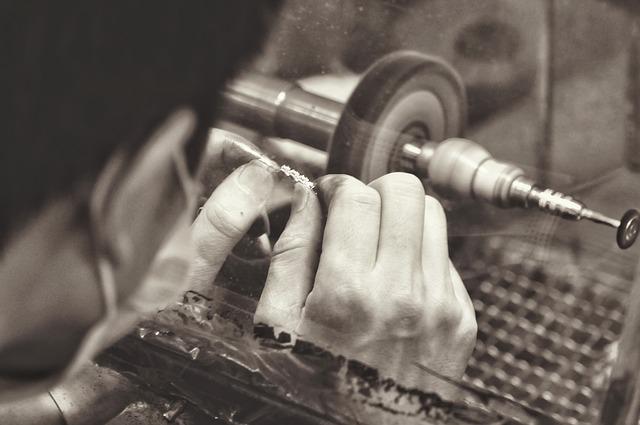
A basic understanding of Articulated-arm and Anthropomorphic robotic arms is essential for their successful operation. This article will provide an overview of the differences between the two types, as well as the Mechanical or Sensor units in an arm-robot. We will explore the capabilities of each type and how they can be used to improve our daily lives. These are important design considerations. For example, we should consider the weight of the component to be handled, and the weight of the required gripper. It is also important to consider the attachment's centre of mass. This must be close to the center point of the component being gripped. In addition, we should consider whether a particular attachment has a far-away center of gravity, thereby requiring a higher payload.
Robots with articulated arms
Articulated arm robots are versatile. Each six-axis unit comes with a flexible arm, similar to a normal human arm. It rotates around its base and bends in the middle, like a human elbow. The wrist of an Articulated-Arm robot can also move in an arc, like a human's, and can rotate its hand as well. This allows the robot's grasp of objects at any part of the component.
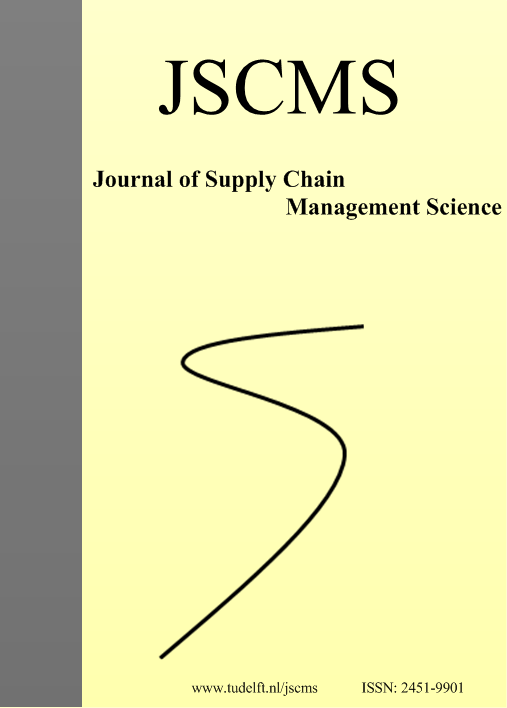
Anthropomorphic robotic arms
Anthropomorphic robotic arms are robots that imitate human arm movement. These robotic arms are designed to handle different objects. They use telereplication of human motion to implement the operator’s motion patterns. These robots have been proven useful in a variety of applications. Researchers have created a method that can decode human movements and translate them into robotic arms.
Mechanical unit in arm robots
There are many functions to the mechanical unit of arm robotics. Robotic wrists allow the end-effector to be placed on a workpiece. The wrist is equipped with two rotary joints. One allows the endeffector to rotate, and the other allows the wrist to move in a particular direction. Both the wrists and the end effector have different degrees. These units can be combined and used to move parts onto pallets.
Sensor unit in arm robots
A sensor unit inside an arm robot's robotic arm is designed to detect changes in human body heat. This sensor is placed on the robotic arm's gripper end, where it can contact a temperature-measurement object. Once it detects changes in temperature, it sends a signal to the STM32 single-chip microcomputer in the robot arm's base. The STM32 controls robot actions and alerts the operator when temperatures rise. Normal operations will not require it to stop the robot from moving.
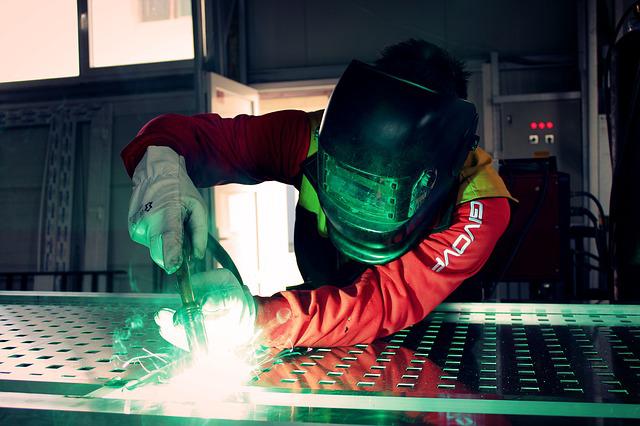
Cost to join an arms robot
If you're looking to build a robotic arm, you may wonder how much it costs. An arm robot's cost will vary depending on its size, safety components, and tooling. The larger the robot, the higher the price will be, as will the additional peripherals and tooling you need. The application is another factor that influences cost. A larger robot will have a higher payload and be able to reach greater distances. But, this is usually offset by a lower cost for safety features.
FAQ
Why automate your warehouse
Automation has become increasingly important in modern warehousing. The rise of e-commerce has led to increased demand for faster delivery times and more efficient processes.
Warehouses must be able to quickly adapt to changing demands. Technology investment is necessary to enable warehouses to respond quickly to changing demands. Automating warehouses has many benefits. These are some of the benefits that automation can bring to warehouses:
-
Increases throughput/productivity
-
Reduces errors
-
Improves accuracy
-
Safety is boosted
-
Eliminates bottlenecks
-
Allows companies to scale more easily
-
Increases efficiency of workers
-
It gives visibility to everything that happens inside the warehouse
-
Enhances customer experience
-
Improves employee satisfaction
-
Reduces downtime and improves uptime
-
You can be sure that high-quality products will arrive on time
-
Eliminates human error
-
Helps ensure compliance with regulations
Is automation important in manufacturing?
Not only are service providers and manufacturers important, but so is automation. Automation allows them to deliver services quicker and more efficiently. It reduces human errors and improves productivity, which in turn helps them lower their costs.
What skills are required to be a production manager?
A production planner must be organized, flexible, and able multitask to succeed. Also, you must be able and willing to communicate with clients and coworkers.
What can I do to learn more about manufacturing?
Hands-on experience is the best way to learn more about manufacturing. But if that is not possible you can always read books and watch educational videos.
What are manufacturing and logistic?
Manufacturing refers to the process of making goods using raw materials and machines. Logistics includes all aspects related to supply chain management, such as procurement, distribution planning, inventory control and transportation. As a broad term, manufacturing and logistics often refer to both the creation and delivery of products.
What is production planning?
Production planning is the process of creating a plan that covers all aspects of production. This includes scheduling, budgeting and crew, location, equipment, props, and more. This document aims to ensure that everything is planned and ready when you are ready to shoot. This document should include information about how to achieve the best results on-set. This includes information on shooting times, locations, cast lists and crew details.
First, you need to plan what you want to film. You may have decided where to shoot or even specific locations you want to use. Once you have identified your locations and scenes, you can start working out which elements you require for each scene. For example, you might decide that you need a car but don't know exactly what model you want. To narrow your options, you can search online for available models.
After you've found the perfect car, it's time to start thinking about adding extras. Do you need people sitting in the front seats? Or perhaps you need someone walking around the back of the car? Maybe you'd like to change the interior from black to a white color. These questions will help guide you in determining the ideal look and feel for your car. It is also worth considering the types of shots that you wish to take. You will be filming close-ups and wide angles. Maybe you want to show the engine and the steering wheel. These factors will help you determine which car style you want to film.
Once you have determined all of the above, you can move on to creating a schedule. You can create a schedule that will outline when you must start and finish your shoots. Every day will have a time for you to arrive at the location, leave when you are leaving and return home when you are done. Everyone will know what they need and when. It is possible to make arrangements in advance for additional staff if you are looking to hire. It's not worth paying someone to show up if you haven't told him.
It is important to calculate the amount of filming days when you are creating your schedule. Some projects take only a few days while others can last several weeks. When you are creating your schedule, you should always keep in mind whether you need more than one shot per day or not. Multiple shots at the same location can increase costs and make it more difficult to complete. If you aren't sure whether you need multiple shots, it is best to take fewer photos than you would like.
Budgeting is another important aspect of production planning. A realistic budget will help you work within your means. You can always lower the budget if you encounter unexpected problems. However, you shouldn't overestimate the amount of money you will spend. If you underestimate how much something costs, you'll have less money to pay for other items.
Production planning can be a complex process. However, once you know how everything works together it will become easier to plan future projects.
Statistics
- According to the United Nations Industrial Development Organization (UNIDO), China is the top manufacturer worldwide by 2019 output, producing 28.7% of the total global manufacturing output, followed by the United States, Japan, Germany, and India.[52][53] (en.wikipedia.org)
- In 2021, an estimated 12.1 million Americans work in the manufacturing sector.6 (investopedia.com)
- (2:04) MTO is a production technique wherein products are customized according to customer specifications, and production only starts after an order is received. (oracle.com)
- Job #1 is delivering the ordered product according to specifications: color, size, brand, and quantity. (netsuite.com)
- You can multiply the result by 100 to get the total percent of monthly overhead. (investopedia.com)
External Links
How To
How to use lean manufacturing in the production of goods
Lean manufacturing is a management system that aims at increasing efficiency and reducing waste. It was first developed in Japan in the 1970s/80s by Taiichi Ahno, who was awarded the Toyota Production System (TPS), award from KanjiToyoda, the founder of TPS. Michael L. Watkins published the original book on lean manufacturing, "The Machine That Changed the World," in 1990.
Lean manufacturing refers to a set of principles that improve the quality, speed and costs of products and services. It emphasizes eliminating waste and defects throughout the value stream. Lean manufacturing can be described as just-in–time (JIT), total productive maintenance, zero defect (TPM), or even 5S. Lean manufacturing eliminates non-value-added tasks like inspection, rework, waiting.
Lean manufacturing improves product quality and costs. It also helps companies reach their goals quicker and decreases employee turnover. Lean Manufacturing is one of the most efficient ways to manage the entire value chains, including suppliers and customers as well distributors and retailers. Lean manufacturing can be found in many industries. Toyota's philosophy is a great example of this. It has helped to create success in automobiles as well electronics, appliances and healthcare.
Five basic principles of Lean Manufacturing are included in lean manufacturing
-
Define Value - Determine the value that your business brings to society. Also, identify what sets you apart from your competitors.
-
Reduce waste - Get rid of any activity that does not add value to the supply chain.
-
Create Flow: Ensure that the work process flows without interruptions.
-
Standardize & Simplify - Make processes as consistent and repeatable as possible.
-
Develop Relationships: Establish personal relationships both with internal and external stakeholders.
Although lean manufacturing has always been around, it is gaining popularity in recent years because of a renewed interest for the economy after 2008's global financial crisis. Many companies have adopted lean manufacturing methods to increase their marketability. According to some economists, lean manufacturing could be a significant factor in the economic recovery.
Lean manufacturing is now becoming a common practice in the automotive industry, with many benefits. These include improved customer satisfaction, reduced inventory levels, lower operating costs, increased productivity, and better overall safety.
You can apply Lean Manufacturing to virtually any aspect of your organization. Lean manufacturing is most useful in the production sector of an organisation because it ensures that each step in the value-chain is efficient and productive.
There are three main types:
-
Just-in Time Manufacturing, (JIT): This kind of lean manufacturing is also commonly known as "pull-systems." JIT stands for a system where components are assembled on the spot rather than being made in advance. This strategy aims to decrease lead times, increase availability of parts and reduce inventory.
-
Zero Defects Manufacturing (ZDM): ZDM focuses on ensuring that no defective units leave the manufacturing facility. If a part is required to be repaired on the assembly line, it should not be scrapped. This applies to finished goods that may require minor repairs before shipment.
-
Continuous Improvement (CI): CI aims to improve the efficiency of operations by continuously identifying problems and making changes in order to eliminate or minimize waste. Continuous Improvement involves continuous improvement of processes.