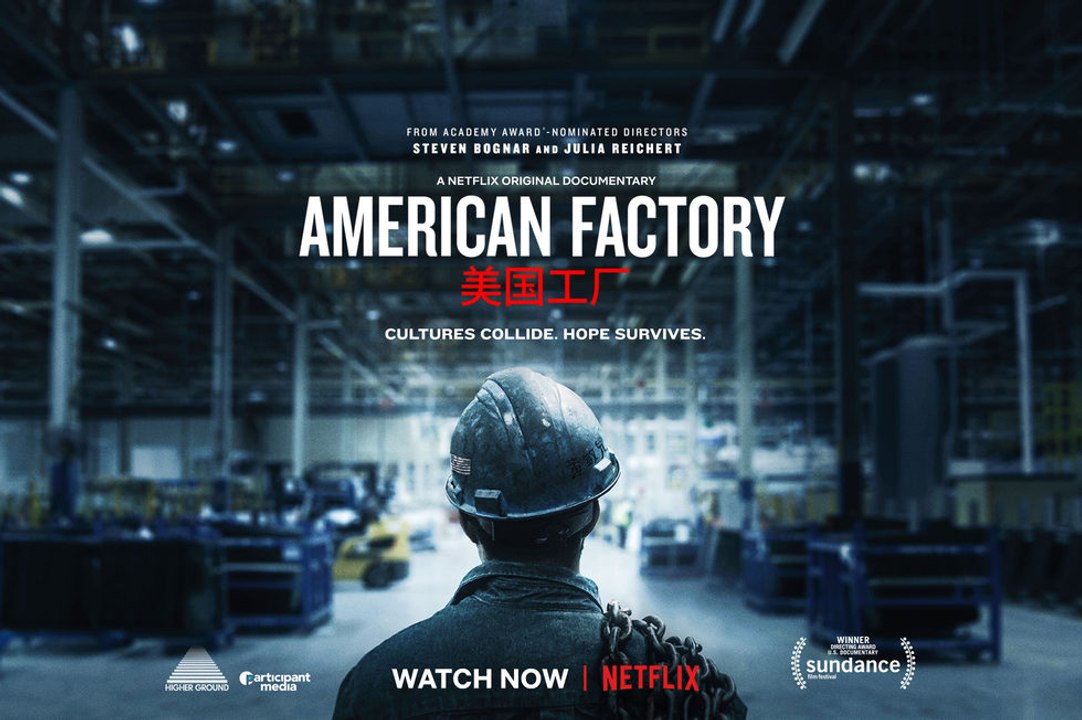
Japanese factories produce highquality products at low cost. They are the backbone of the country's economy, accounting for five per cent of the country's GDP. They have been challenged by tighter standards and increased competition as well as the cost pressures from the recent recession.
In a whitepaper published last year by the government, it was found that Japanese businesses were not ready to deal with a cutoff in parts procurement. The Japanese auto industry was hard hit by the recession. The supply chain is a critical part of the car manufacturing business. It relies on approximately 30,000 parts. This can lead to production being stopped. Some of the parts have no substitutes.
In order to keep the quality of their products high, Japanese manufacturers are working closely with suppliers to solve problems and improve efficiency. They are also encouraging feedback from workers, salesmen and quality inspectors.
Japanese manufacturers are concerned about the high number of accidents on the factory floor. There have been a series of safety scandals that have erupted across the country's manufacturing sector. This has led to greater scrutiny of the standard of work in factories.
Non-regular labor has also been a problem for Japanese goods production. Non-regular workers allow companies to reduce labor costs, but they increase the risk of accidents and de-skill the production floor. Companies are focusing on training regular workers to make them safer and better.
Japan's falling birthrate is the reason for its growing labor shortage. A 25-year high number of Japanese companies are complaining of a lack of labor. If the labor force continues to shrink, Japanese companies will face even greater challenges.
Although there are fewer skilled workers, many factories have cut costs. A growing number so-called "factries", employ fewer people than ten. These small workshops often produce some of the most advanced equipment in the world.
China and South Korea are threatening the Japanese manufacturing industry. Many factories are trying to cut costs and increase productivity as a result. However, the Japanese government warned that the industry would suffer if it loses its competitive advantage in foreign markets.
As Japan faces increased competition from Asia and abroad, it is facing questions about whether it can adjust its processes to meet demand and adapt quickly enough. And even if it can, the demand for skilled workers is expected to rise.
Japanese factories provide components for the global marketplace. They also supply advanced materials like silicon chips which are used in computers and smart phone. While Chinese factories excel in low-cost assembly operations they still rely on Japan to supply the essential components.
Even as they have worked to improve their productivity and quality, the Japanese have faced increased competition from abroad. The recession has lowered the value of their products in the domestic market, and they have been forced to cut costs. But despite these challenges, the Japanese have been able to achieve a high level of excellence in their production.
FAQ
Do we need to know about Manufacturing Processes before learning about Logistics?
No. You don't have to know about manufacturing processes before learning about logistics. Understanding the manufacturing process will allow you to better understand logistics.
What does it mean to warehouse?
A warehouse or storage facility is where goods are stored before they are sold. It can be either an indoor or outdoor space. In some cases, it may be a combination of both.
What are the products and services of logistics?
Logistics involves the transportation of goods from point A and point B.
They encompass all aspects transport, including packaging and loading, transporting, storage, unloading.
Logisticians ensure that the product is delivered to the correct place, at the right time, and under safe conditions. Logisticians assist companies in managing their supply chains by providing information such as demand forecasts, stock levels and production schedules.
They coordinate with vendors and suppliers, keep track of shipments, monitor quality standards and perform inventory and order replenishment.
What is the job of a logistics manger?
Logistics managers make sure all goods are delivered on schedule and without damage. This is achieved by using their knowledge and experience with the products of the company. He/she must also ensure sufficient stock to meet the demand.
What are my options for learning more about manufacturing
Hands-on experience is the best way to learn more about manufacturing. But if that is not possible you can always read books and watch educational videos.
Statistics
- Job #1 is delivering the ordered product according to specifications: color, size, brand, and quantity. (netsuite.com)
- In the United States, for example, manufacturing makes up 15% of the economic output. (twi-global.com)
- It's estimated that 10.8% of the U.S. GDP in 2020 was contributed to manufacturing. (investopedia.com)
- You can multiply the result by 100 to get the total percent of monthly overhead. (investopedia.com)
- According to the United Nations Industrial Development Organization (UNIDO), China is the top manufacturer worldwide by 2019 output, producing 28.7% of the total global manufacturing output, followed by the United States, Japan, Germany, and India.[52][53] (en.wikipedia.org)
External Links
How To
How to use lean manufacturing in the production of goods
Lean manufacturing (or lean manufacturing) is a style of management that aims to increase efficiency, reduce waste and improve performance through continuous improvement. It was first developed in Japan in the 1970s/80s by Taiichi Ahno, who was awarded the Toyota Production System (TPS), award from KanjiToyoda, the founder of TPS. Michael L. Watkins published the "The Machine That Changed the World", the first book about lean manufacturing. It was published in 1990.
Lean manufacturing can be described as a set or principles that are used to improve quality, speed and cost of products or services. It emphasizes the elimination and minimization of waste in the value stream. Lean manufacturing is called just-in-time (JIT), zero defect, total productive maintenance (TPM), or 5S. Lean manufacturing is about eliminating activities that do not add value, such as inspection, rework, and waiting.
Lean manufacturing can help companies improve their product quality and reduce costs. Additionally, it helps them achieve their goals more quickly and reduces employee turnover. Lean manufacturing has been deemed one of the best ways to manage the entire value-chain, including customers, distributors as well retailers and employees. Many industries worldwide use lean manufacturing. Toyota's philosophy is the foundation of its success in automotives, electronics and appliances, healthcare, chemical engineers, aerospace, paper and food, among other industries.
Lean manufacturing is based on five principles:
-
Define Value - Identify the value your business adds to society and what makes you different from competitors.
-
Reduce waste - Get rid of any activity that does not add value to the supply chain.
-
Create Flow. Ensure that your work is uninterrupted and flows seamlessly.
-
Standardize and Simplify – Make processes as consistent, repeatable, and as simple as possible.
-
Build relationships - Develop and maintain personal relationships with both your internal and external stakeholders.
Although lean manufacturing isn't a new concept in business, it has gained popularity due to renewed interest in the economy after the 2008 global financial crisis. Many businesses have adopted lean production techniques to make them more competitive. According to some economists, lean manufacturing could be a significant factor in the economic recovery.
With many benefits, lean manufacturing is becoming more common in the automotive industry. These benefits include increased customer satisfaction, reduced inventory levels and lower operating costs.
Any aspect of an enterprise can benefit from Lean manufacturing. Because it makes sure that all value chains are efficient and effectively managed, Lean Manufacturing is particularly helpful for organizations.
There are three main types of lean manufacturing:
-
Just-in Time Manufacturing: This lean manufacturing method is commonly called "pull systems." JIT is a method in which components are assembled right at the moment of use, rather than being manufactured ahead of time. This strategy aims to decrease lead times, increase availability of parts and reduce inventory.
-
Zero Defects Manufacturing - ZDM: ZDM focuses its efforts on making sure that no defective units leave a manufacturing facility. If a part needs to be fixed during the assembly line, it should be repaired rather than scrapped. This is true even for finished products that only require minor repairs prior to shipping.
-
Continuous Improvement (CI: Continuous improvement aims to increase the efficiency of operations by constantly identifying and making improvements to reduce or eliminate waste. Continuous Improvement involves continuous improvement of processes.