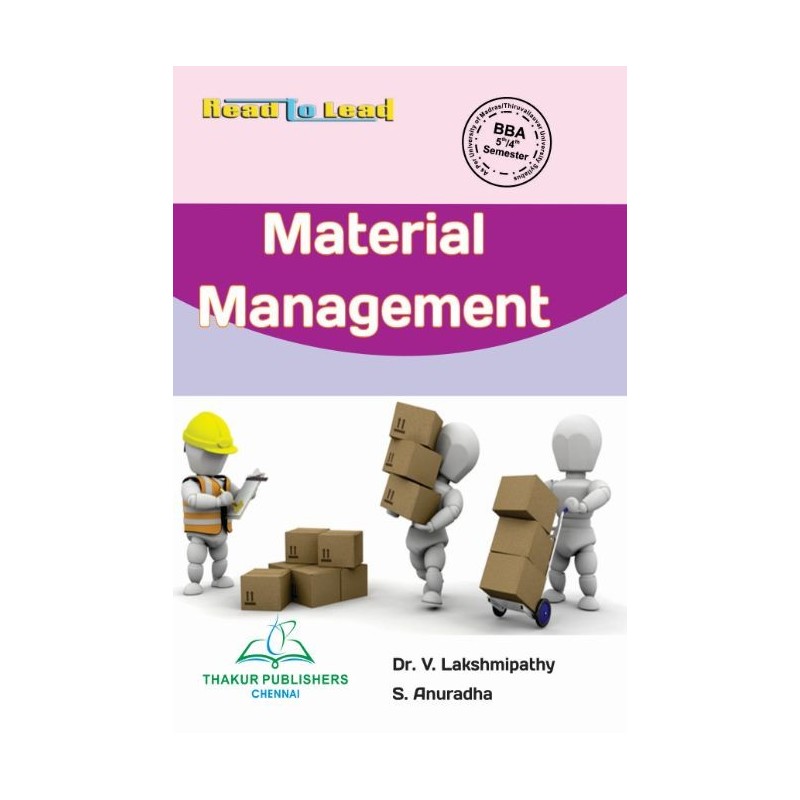
A manufacturing engineer job requires different levels of education and training. Some graduates may pursue a master's degree program that develops required business, process and product knowledge. The majority of manufacturing engineering engineers learn the bulk of their skills during their degree program. They get hands-on experience with measurements, experiments and standard tests. Employers will require them to obtain a license in order to operate a business.
Manufacturing engineer skills
Manufacturing engineers can rise from an entry-level to a managerial position depending on their position. They will be required to have the following skills in order to succeed: They should be well-versed in various disciplines, including math and critical thinking. They should also have excellent communication skills to work with different levels of an organization. These are just a few of the many skills that a manufacturing engineer will need to be successful in their role.
The primary duties of a manufacturing engineer include the development, maintenance, or modification of various processes or systems. They will also be responsible to assess the environmental impact on manufacturing processes. They will need to be analytical thinkers and designers, with a solid understanding of manufacturing processes. A manufacturing engineer must keep current with current trends and regulations, as well as stay on top of industry news. In addition, they must be able to work effectively with teams of engineers from various disciplines.
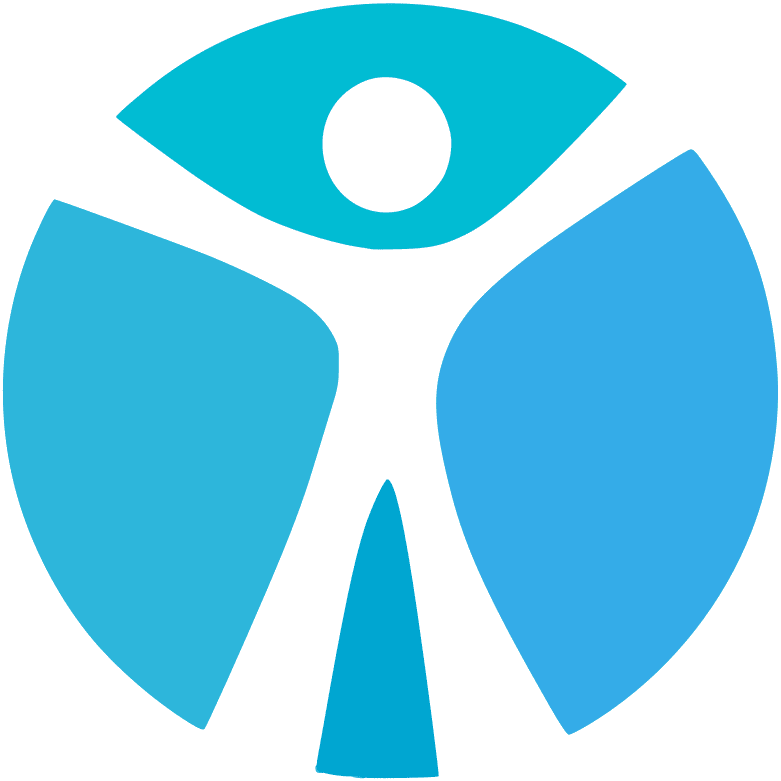
Manufacturing engineer responsibilities
A manufacturing engineer is responsible for everything from designing processes to determining costs. These engineers are responsible for the design and development of production processes. Although they are often based in offices, some may need to travel to other locations such as the factory floor. Some manufacturing engineers might need to oversee or direct production personnel. These employees are responsible the smooth running a production line.
As a manufacturing engineer, your main responsibility is to develop and implement manufacturing processes. You also need to monitor their efficiency. Manufacturing engineers can also analyse production processes and design equipment. Quality control systems are created to ensure high quality products. Manufacturing engineers are responsible for the design and development of manufacturing processes. They also adhere to safety and quality regulations. As a manufacturing engineer, their responsibilities extend beyond the office. They also need to research and produce reports and documentation.
For manufacturing engineers, the future looks bright
Manufacturing engineers have a great career outlook. Although they grow slower than other occupations in the economy, there is still a lot of job growth. Manufacturing engineers will increase in demand due to the growing manufacturing sector. For manufacturing companies to succeed, they need to be successful in planning, logistics, as well as new methods of production. Despite the slow growth, mechanical engineers are in high demand. Most job seekers will come from the school system.
According to the Bureau of Labor Statistics, the U.S. will see a 9% increase in manufacturing engineers between 2026 and 2027. These professionals need to enjoy teamwork and a challenging job environment. Career satisfaction is high for manufacturing engineers, and they typically remain in the field for a long time. Manufacturing engineers may be employed in factories that manufacture cars and trucks. In addition to manufacturing, they may be employed by research and development firms, wholesale trade, and consulting services. Some industrial engineers leave engineering to pursue managerial positions.
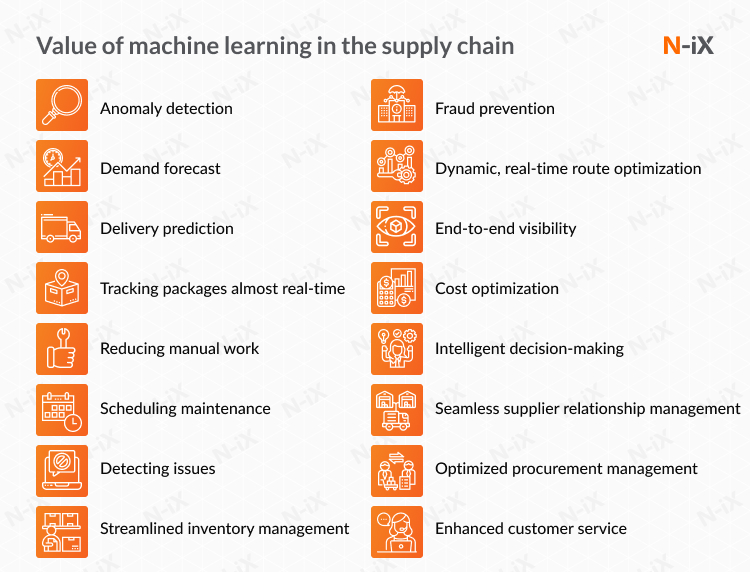
Manufacturing engineers need to be educated
Most manufacturing engineering jobs require a BSE degree. Students will be able to learn about general science, math and engineering concepts. They can also use computer-aided design software (CAD). They will also develop communication skills and a strong foundation in mathematics. Other required courses may include courses in humanities and ethics. While education requirements for manufacturing engineers are not uniform, BSEs are considered well-rounded.
The education requirements for a career in manufacturing engineering require strong mathematics and science backgrounds, as well as analytical and problem-solving skills. As well as being creative, they need to be able to work in a team. After graduation, manufacturing engineers work full-time. Manufacturing engineers are expected to travel extensively and observe various manufacturing processes at different locations. In addition to education requirements, manufacturing engineers must have a strong work ethic and a desire to learn about the latest trends in manufacturing.
FAQ
What skills do production planners need?
Production planners must be flexible, organized, and able handle multiple tasks. You must also be able to communicate effectively with clients and colleagues.
What is the responsibility of a manufacturing manager?
The manufacturing manager should ensure that every manufacturing process is efficient and effective. They should be alert for any potential problems in the company and react accordingly.
They should also learn how to communicate effectively with other departments, including sales and marketing.
They should be up to date on the latest trends and be able apply this knowledge to increase productivity and efficiency.
Can certain manufacturing steps be automated?
Yes! Since ancient times, automation has been in existence. The Egyptians discovered the wheel thousands and years ago. We now use robots to help us with assembly lines.
There are many applications for robotics in manufacturing today. These include:
-
Line robots
-
Robot welding
-
Robot painting
-
Robotics inspection
-
Robots that make products
There are many other examples of how manufacturing could benefit from automation. For example, 3D printing allows us to make custom products without having to wait for weeks or months to get them manufactured.
What does it mean to warehouse?
A warehouse or storage facility is where goods are stored before they are sold. It can be indoors or out. It could be one or both.
What are the 7 Rs of logistics.
The acronym 7R's for Logistics stands to represent the seven basic principles in logistics management. It was developed by International Association of Business Logisticians (IABL), and published as part of their "Seven Principles of Logistics Management Series" in 2004.
The acronym is composed of the following letters.
-
Responsible - ensure that all actions taken are within legal requirements and are not harmful to others.
-
Reliable: Have faith in your ability or the ability to honor any promises made.
-
Be responsible - Use resources efficiently and avoid wasting them.
-
Realistic - Take into consideration all aspects of operations including cost-effectiveness, environmental impact, and other factors.
-
Respectful - show respect and treat others fairly and fairly
-
Resourceful - look for opportunities to save money and increase productivity.
-
Recognizable - Provide value-added services to customers
What does manufacturing mean?
Manufacturing Industries are companies that manufacture products. Consumers are those who purchase these products. These companies employ many processes to achieve this purpose, such as production and distribution, retailing, management and so on. They make goods from raw materials with machines and other equipment. This covers all types of manufactured goods including clothing, food, building supplies and furniture, as well as electronics, tools, machinery, vehicles and pharmaceuticals.
Do we need to know about Manufacturing Processes before learning about Logistics?
No. It doesn't matter if you don't know anything about manufacturing before you learn about logistics. However, knowing about manufacturing processes will definitely give you a better understanding of how logistics works.
Statistics
- According to the United Nations Industrial Development Organization (UNIDO), China is the top manufacturer worldwide by 2019 output, producing 28.7% of the total global manufacturing output, followed by the United States, Japan, Germany, and India.[52][53] (en.wikipedia.org)
- You can multiply the result by 100 to get the total percent of monthly overhead. (investopedia.com)
- Job #1 is delivering the ordered product according to specifications: color, size, brand, and quantity. (netsuite.com)
- In 2021, an estimated 12.1 million Americans work in the manufacturing sector.6 (investopedia.com)
- It's estimated that 10.8% of the U.S. GDP in 2020 was contributed to manufacturing. (investopedia.com)
External Links
How To
How to use the Just-In Time Method in Production
Just-in-time is a way to cut costs and increase efficiency in business processes. It is a process where you get the right amount of resources at the right moment when they are needed. This means that your only pay for the resources you actually use. Frederick Taylor first coined this term while working in the early 1900s as a foreman. He saw how overtime was paid to workers for work that was delayed. He realized that workers should have enough time to complete their jobs before they begin work. This would help increase productivity.
JIT is an acronym that means you need to plan ahead so you don’t waste your money. Look at your entire project, from start to end. Make sure you have enough resources in place to deal with any unexpected problems. You'll be prepared to handle any potential problems if you know in advance. You won't have to pay more for unnecessary items.
There are different types of JIT methods:
-
Demand-driven: This is a type of JIT where you order the parts/materials needed for your project regularly. This will let you track the amount of material left over after you've used it. It will also allow you to predict how long it takes to produce more.
-
Inventory-based : You can stock the materials you need in advance. This allows you to forecast how much you will sell.
-
Project-driven: This is an approach where you set aside enough funds to cover the cost of your project. When you know how much you need, you'll purchase the appropriate amount of materials.
-
Resource-based JIT: This is the most popular form of JIT. This is where you assign resources based upon demand. For instance, if you have a lot of orders coming in, you'll assign more people to handle them. If you don't have many orders, you'll assign fewer people to handle the workload.
-
Cost-based: This is the same as resource-based except that you don't care how many people there are but how much each one of them costs.
-
Price-based: This is very similar to cost-based, except that instead of looking at how much each individual worker costs, you look at the overall price of the company.
-
Material-based: This approach is similar to cost-based. However, instead of looking at the total cost for the company, you look at how much you spend on average on raw materials.
-
Time-based JIT is another form of resource-based JIT. Instead of focusing solely on the amount each employee costs, focus on how long it takes for the project to be completed.
-
Quality-based JIT: This is another variation of resource based JIT. Instead of thinking about how much each employee costs or how long it takes to manufacture something, you think about how good the quality of your product is.
-
Value-based JIT is the newest form of JIT. You don't worry about whether the products work or if they meet customer expectations. Instead, you are focused on adding value to the marketplace.
-
Stock-based: This stock-based method focuses on the actual quantity of products being made at any given time. It is used when production goals are met while inventory is kept to a minimum.
-
Just-in-time planning (JIT): This is a combination JIT and supply-chain management. It's the process of scheduling delivery of components immediately after they are ordered. This is important as it reduces lead time and increases throughput.