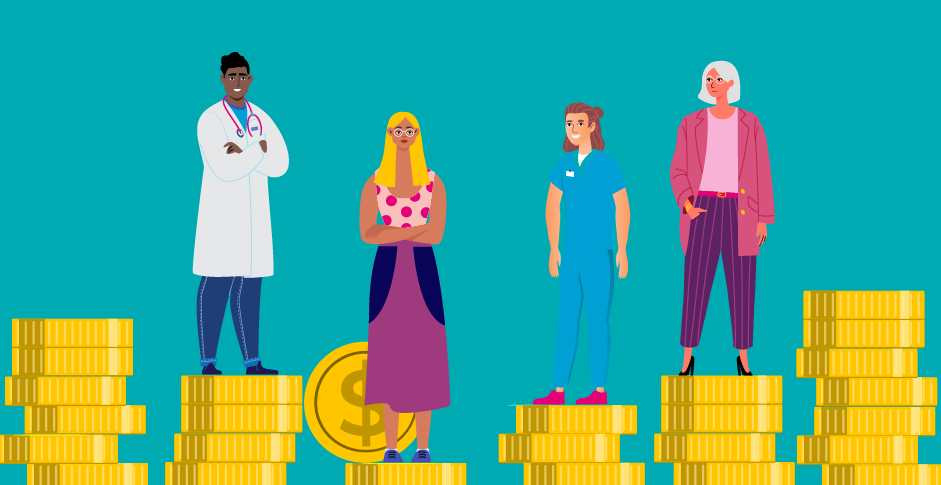
Additive manufacturing jobs are growing, regardless of whether you're a veteran professional or aspiring newcomer. In fact, the overall economic impact of additive manufacturing has been projected by McKinsey to reach $100 billion to $250 billion by 2025. Those interested in the field should consider educational and career paths that will prepare them for the future.
The most well-known career in additive manufacturing is that as a material scientist. They are responsible for testing materials' properties and creating new materials. These individuals can also help develop post-processing methods and conduct research into the future 3D printing materials.
Although there are many different types of material scientists out there, the average salary for them is $150,000. Many jobs involve research, development, or testing the mechanical property of materials. Others are more concerned with finding new applications in additive manufacturing.
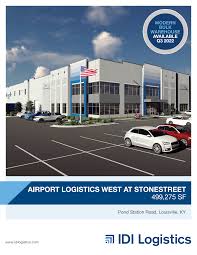
This industry has experienced significant growth in the last year. AT Kearney estimates that additive manufacturing could lead to the creation of up to five million skilled jobs within the US in a decade. There will be more companies that adopt this technology. This means there will be more demand for engineers, business professionals and marketing and sales specialists to support the business as well as the products it creates.
For a job in additive manufacturing, the primary qualifications are usually years of experience and a bachelor's in design software. However, the primary qualifications may differ from one position to another. Additional to a strong educational background, the most desirable job qualifications in additive manufacturing are communication skills, data analytics, and knowledge of manufacturing processes.
R&D is one of the most sought-after jobs in additive manufacturing. 58% expect to hire R&D roles within the next 12 month. These positions include designers, who create digital models of 3D objects, and industrialists, who are responsible for developing additive manufacturing processes.
The sales-related jobs are next in demand. These positions usually require a bachelor’s degree or above, although some employers will prefer candidates who have advanced degrees. In addition, sales personnel are needed for many different industries, including automobiles, aerospace, and food.

Software is another job that is growing quickly. Companies are using technology to create cross-platform software. This is a nonlinear career path. Employers increasingly seek applicants with mental elasticity and complex problem solving abilities. This type of job is possible by developing these skills and showing potential employers.
Finally, many job postings require a degree in computer science. While this is not the most common educational path, it can help professionals build the skills necessary for a career in additive manufacturing.
Although the future is uncertain for additive manufacturing, it is important to stay on top of the industry's growth. This will help you decide whether this is the right field for you. If you are interested in the industry, Joblist can help you find and apply for job opportunities.
FAQ
Why is logistics important in manufacturing?
Logistics are an integral part any business. They help you achieve great results by helping you manage all aspects of product flow, from raw materials to finished goods.
Logistics play an important role in reducing costs as well as increasing efficiency.
How can we improve manufacturing efficiency?
First, determine which factors have the greatest impact on production time. We must then find ways that we can improve these factors. If you don’t know how to start, look at which factors have the greatest impact upon production time. Once you have identified them, it is time to identify solutions.
What does it take to run a logistics business?
A successful logistics business requires a lot more than just knowledge. To communicate effectively with clients and suppliers, you must be able to communicate well. You need to understand how to analyze data and draw conclusions from it. You must be able to work well under pressure and handle stressful situations. You must be creative and innovative to develop new ideas to improve efficiency. Strong leadership qualities are essential to motivate your team and help them achieve their organizational goals.
You must be organized to meet tight deadlines.
What are manufacturing and logistics?
Manufacturing refers to the process of making goods using raw materials and machines. Logistics includes all aspects related to supply chain management, such as procurement, distribution planning, inventory control and transportation. Manufacturing and logistics are often considered together as a broader term that encompasses both the process of creating products and delivering them to customers.
Is automation important for manufacturing?
Not only is automation important for manufacturers, but it's also vital for service providers. It enables them to provide services faster and more efficiently. It reduces human errors and improves productivity, which in turn helps them lower their costs.
Why automate your factory?
Modern warehousing is becoming more automated. The rise of e-commerce has led to increased demand for faster delivery times and more efficient processes.
Warehouses must be able to quickly adapt to changing demands. To do so, they must invest heavily in technology. Automation of warehouses offers many benefits. Here are some benefits of investing in automation
-
Increases throughput/productivity
-
Reduces errors
-
Improves accuracy
-
Safety is boosted
-
Eliminates bottlenecks
-
Allows companies scale more easily
-
It makes workers more efficient
-
The warehouse can be viewed from all angles.
-
Enhances customer experience
-
Improves employee satisfaction
-
Minimizes downtime and increases uptime
-
High quality products delivered on-time
-
Human error can be eliminated
-
This helps to ensure compliance with regulations
Statistics
- According to the United Nations Industrial Development Organization (UNIDO), China is the top manufacturer worldwide by 2019 output, producing 28.7% of the total global manufacturing output, followed by the United States, Japan, Germany, and India.[52][53] (en.wikipedia.org)
- You can multiply the result by 100 to get the total percent of monthly overhead. (investopedia.com)
- (2:04) MTO is a production technique wherein products are customized according to customer specifications, and production only starts after an order is received. (oracle.com)
- In 2021, an estimated 12.1 million Americans work in the manufacturing sector.6 (investopedia.com)
- According to a Statista study, U.S. businesses spent $1.63 trillion on logistics in 2019, moving goods from origin to end user through various supply chain network segments. (netsuite.com)
External Links
How To
How to Use Lean Manufacturing in the Production of Goods
Lean manufacturing is a management style that aims to increase efficiency and reduce waste through continuous improvement. It was first developed in Japan in the 1970s/80s by Taiichi Ahno, who was awarded the Toyota Production System (TPS), award from KanjiToyoda, the founder of TPS. Michael L. Watkins published the "The Machine That Changed the World", the first book about lean manufacturing. It was published in 1990.
Lean manufacturing, often described as a set and practice of principles, is aimed at improving the quality, speed, cost, and efficiency of products, services, and other activities. It emphasizes eliminating waste and defects throughout the value stream. Lean manufacturing is also known as just in time (JIT), zero defect total productive maintenance(TPM), and five-star (S). Lean manufacturing is about eliminating activities that do not add value, such as inspection, rework, and waiting.
Lean manufacturing not only improves product quality but also reduces costs. Companies can also achieve their goals faster by reducing employee turnover. Lean manufacturing has been deemed one of the best ways to manage the entire value-chain, including customers, distributors as well retailers and employees. Lean manufacturing is widely practiced in many industries around the world. Toyota's philosophy, for example, is what has enabled it to be successful in electronics, automobiles, medical devices, healthcare and chemical engineering as well as paper and food.
Five fundamental principles underlie lean manufacturing.
-
Define Value - Identify the value your business adds to society and what makes you different from competitors.
-
Reduce waste - Stop any activity that isn't adding value to the supply chains.
-
Create Flow: Ensure that the work process flows without interruptions.
-
Standardize and Simplify – Make processes as consistent, repeatable, and as simple as possible.
-
Building Relationships – Establish personal relationships with both external and internal stakeholders.
Although lean manufacturing has always been around, it is gaining popularity in recent years because of a renewed interest for the economy after 2008's global financial crisis. Many businesses have adopted lean manufacturing techniques to help them become more competitive. Some economists even believe that lean manufacturing can be a key factor in economic recovery.
With many benefits, lean manufacturing is becoming more common in the automotive industry. These benefits include increased customer satisfaction, reduced inventory levels and lower operating costs.
Any aspect of an enterprise can benefit from Lean manufacturing. Because it makes sure that all value chains are efficient and effectively managed, Lean Manufacturing is particularly helpful for organizations.
There are three main types in lean manufacturing
-
Just-in Time Manufacturing (JIT), also known as "pull system": This form of lean manufacturing is often referred to simply as "pull". JIT stands for a system where components are assembled on the spot rather than being made in advance. This approach is designed to reduce lead times and increase the availability of components. It also reduces inventory.
-
Zero Defects Manufacturing (ZDM): ZDM focuses on ensuring that no defective units leave the manufacturing facility. If a part is required to be repaired on the assembly line, it should not be scrapped. This applies to finished products, which may need minor repairs before they are shipped.
-
Continuous Improvement (CI), also known as Continuous Improvement, aims at improving the efficiency of operations through continuous identification and improvement to minimize or eliminate waste. Continuous Improvement (CI) involves continuous improvement in processes, people, tools, and infrastructure.