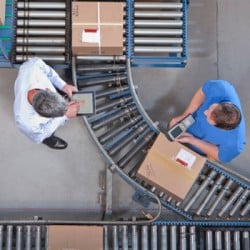
A manufacturing strategy allows a company to focus on areas where it is different from competitors. This is essential to establishing a competitive advantage that will help you survive in the long run.
Your manufacturing strategy should match your business goals and mission statement. It should also be backed by strong team leadership. It will help to ensure that resources are allocated correctly and that all employees know their roles in the success of the business.
Your team will need to discuss and divide the key areas needed for your manufacturing strategy. After your team has done this, it is time to set up a plan in each of these areas.
If you want to improve your employee's productivity, for example, then your team could discuss ways to improve their quality and efficiency. This is crucial as improving the performance of your employees will lead to a better working environment for them and ultimately, increased output for the business.
In the same vein, you can also look at your overall production capacity and determine if it is adequate for the current and future needs of your business. If not, you may need to invest in more equipment or a new location.
No matter what kind of product you manufacture, it is important that your production be cost-effective. It is crucial to reduce waste and meet customer demands.
Improving your inventory management system is one of best ways to improve the production process. With a stock management system, you will be able to identify which inventory levels need to be adjusted. You will not have to worry about overstocking and having a lot of items left in your warehouse.
Producing to order can also help you reduce the amount of inventory that you keep. This is great for businesses offering niche products that can't be found on the highstreet.
This method allows for the production of finished goods on demand, as opposed to storing them in storage until orders come in. This can significantly cut down on the amount of inventory you produce and the associated costs.
It is also possible to choose to assemble the products after they are confirmed. This allows you to avoid the waste of material and labour associated with large-scale production. This strategy is ideal for companies that want to streamline their production processes while still offering a variety of products.
The key to implementing this strategy is having a clear understanding of the products that you are producing and how you intend to manufacture them. This is particularly important if your company produces products that are exclusive to it or if the industry you're in has complicated specifications.
FAQ
Why is logistics important in manufacturing?
Logistics are an essential part of any business. They can help you achieve great success by helping you manage product flow from raw material to finished goods.
Logistics are also important in reducing costs and improving efficiency.
Is automation necessary in manufacturing?
Automation is essential for both manufacturers and service providers. It enables them to provide services faster and more efficiently. It also helps to reduce costs and improve productivity.
What is manufacturing and logistics?
Manufacturing is the production of goods using raw materials. Logistics is the management of all aspects of supply chain activities, including procurement, production planning, distribution, warehousing, inventory control, transportation, and customer service. Manufacturing and logistics can often be grouped together to describe a larger term that covers both the creation of products, and the delivery of them to customers.
What is the responsibility of a production planner?
Production planners make sure that every aspect of the project is delivered on-time, within budget, and within schedule. A production planner ensures that the service and product meet the client's expectations.
What skills do production planners need?
Being a production planner is not easy. You need to be organized and flexible. You must also be able to communicate effectively with clients and colleagues.
How can manufacturing reduce production bottlenecks?
The key to avoiding bottlenecks in production is to keep all processes running smoothly throughout the entire production cycle, from the time you receive an order until the time when the product ships.
This includes planning for both capacity requirements and quality control measures.
The best way to do this is to use continuous improvement techniques such as Six Sigma.
Six Sigma management is a system that improves quality and reduces waste within your organization.
It seeks to eliminate variation and create consistency in your work.
Statistics
- Job #1 is delivering the ordered product according to specifications: color, size, brand, and quantity. (netsuite.com)
- Many factories witnessed a 30% increase in output due to the shift to electric motors. (en.wikipedia.org)
- It's estimated that 10.8% of the U.S. GDP in 2020 was contributed to manufacturing. (investopedia.com)
- You can multiply the result by 100 to get the total percent of monthly overhead. (investopedia.com)
- In 2021, an estimated 12.1 million Americans work in the manufacturing sector.6 (investopedia.com)
External Links
How To
How to use 5S in Manufacturing to Increase Productivity
5S stands to stand for "Sort", “Set In Order", “Standardize", and "Store". Toyota Motor Corporation created the 5S methodology in 1954. It allows companies to improve their work environment, thereby achieving greater efficiency.
This method has the basic goal of standardizing production processes to make them repeatable. This means that every day tasks such cleaning, sorting/storing, packing, and labeling can be performed. Through these actions, workers can perform their jobs more efficiently because they know what to expect from them.
Five steps are required to implement 5S: Sort, Set In Order, Standardize. Separate. Each step requires a different action, which increases efficiency. By sorting, for example, you make it easy to find the items later. You arrange items by placing them in an order. You then organize your inventory in groups. Make sure everything is correctly labeled when you label your containers.
Employees must be able to critically examine their work practices. Employees must be able to see why they do what they do and find a way to achieve them without having to rely on their old methods. To implement the 5S system, employees must acquire new skills and techniques.
The 5S method not only increases efficiency but also boosts morale and teamwork. As they begin to see improvements, they feel motivated to continue working towards the goal of achieving higher levels of efficiency.