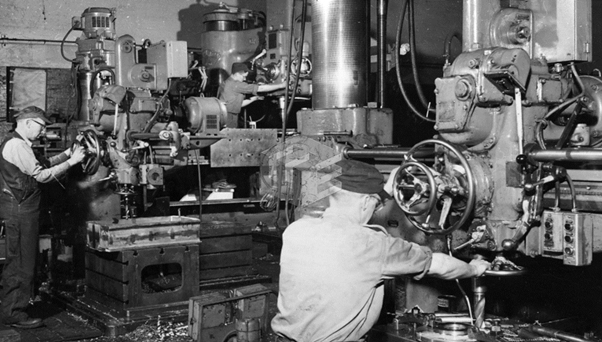
In the world of lean manufacturing, andon means a visual indication that points out and calls attention to problems for the express purpose of resolving them with long-term fixes. This tool empowers the plant floor operator and increases teamwork.
Andon (
The word is of Japanese origin and comes from the paper-covered lanterns of the Edo era, which is the period between the seventeenth and nineteenth centuries. It is also used to describe a Japanese system that ties light signals or sound to a particular process issue to alert the operators and management.
Toyota uses it as a principle to guide its Jidoka or built-in quality. This is a crucial component of Toyota's TPS. In the US, the term is often used to describe a commercial concept allowing production line workers to stop a line when there are problems with safety or quality.
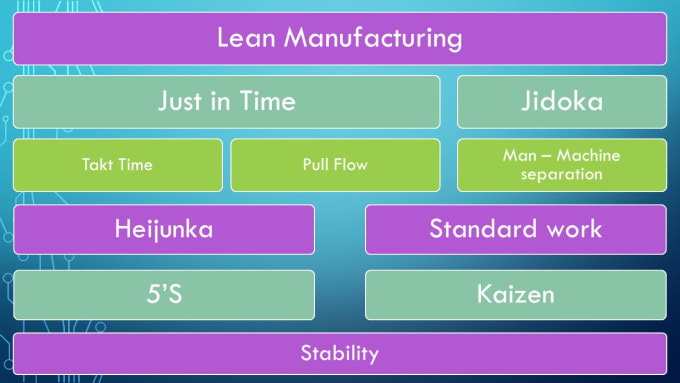
What is the meaning of andon?
Andon is a lean manufacturing system that was pioneered by Toyota. The system is very simple. It consists of a white board with green, orange and red lights. Each color indicates the different status of production. When the green light is lit, the production line is running normally. When the yellow signal is lit, an issue has been detected and is under investigation. The production is stopped when the red light comes on. Workers can take a break, prepare parts, go to help or fill their bins, etc.
The Andon board is easy to use and the supervisors can immediately understand what happened. The system was designed to give immediate feedback, ensuring that all problems are solved as quickly as possible.
There are many different types of andons. However, the most common type is a red LED with a sound. These signal alert and resolve systems help identify problems that might lead to downtime, or repeat issues.
An effective andon board can help to keep the production running in case of a malfunction. It is a simple but effective tool which increases productivity and reduces downtime. It also improves the product quality and safety.
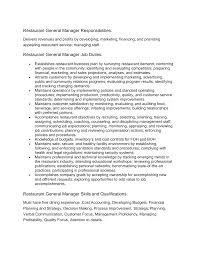
What is Andon Toyota?
Toyota had a cord that employees could pull on the production floor if they suspected a problem with a car. If a worker felt the car was compromised, they could instantly stop the production line by pulling this cord.
Modern andon uses technology to deliver curated information to make it easier to identify problems as they arise, to send real-time notifications to all stakeholders, and to pinpoint the root causes that need a permanent fix. Nevertheless, a human touch is required to interpret and act on this information.
How to make andon work?
Creating a culture of openness and honesty among workers and supervisors is essential. The more they are hesitant, the more they're likely to conceal problems and miss a chance to fix them. The quickest way to improve this is to tie line stops to problem resolution, so that workers are more likely to hit the button and pull the cord when they see something amiss.
FAQ
What skills does a production planner need?
A production planner must be organized, flexible, and able multitask to succeed. It is also important to be able communicate with colleagues and clients.
How can manufacturing excess production be decreased?
Improved inventory management is the key to reducing overproduction. This would decrease the time that is spent on inefficient activities like purchasing, storing, or maintaining excess stock. This would allow us to use our resources for more productive tasks.
A Kanban system is one way to achieve this. A Kanban board can be used to monitor work progress. Work items are moved through various states to reach their destination in a Kanban system. Each state represents a different priority.
As an example, if work is progressing from one stage of the process to another, then the current task is complete and can be transferred to the next. But if a task remains in the beginning stages it will stay that way until it reaches its end.
This allows for work to continue moving forward, while also ensuring that there is no work left behind. Managers can view the Kanban board to see how much work they have done. This data allows them adjust their workflow based upon real-time data.
Another way to control inventory levels is to implement lean manufacturing. Lean manufacturing emphasizes eliminating waste in all phases of production. Anything that does not contribute to the product's value is considered waste. These are some of the most common types.
-
Overproduction
-
Inventory
-
Packaging that is not necessary
-
Material surplus
These ideas will help manufacturers increase efficiency and lower costs.
What does warehouse refer to?
Warehouses and storage facilities are where goods are kept before being sold. It can be an outdoor or indoor area. Sometimes, it can be both an indoor and outdoor space.
Can some manufacturing processes be automated?
Yes! Yes. Automation has been around since ancient time. The Egyptians invent the wheel thousands of year ago. Nowadays, we use robots for assembly lines.
There are many applications for robotics in manufacturing today. These include:
-
Assembly line robots
-
Robot welding
-
Robot painting
-
Robotics inspection
-
Robots that produce products
Automation can be applied to manufacturing in many other ways. 3D printing, for example, allows us to create custom products without waiting for them to be made.
What is the difference between Production Planning, Scheduling and Production Planning?
Production Planning (PP), is the process of deciding what production needs to take place at any given time. This is accomplished by forecasting the demand and identifying production resources.
Scheduling is the process of assigning specific dates to tasks so they can be completed within the specified timeframe.
What does manufacturing mean?
Manufacturing Industries are companies that manufacture products. Consumers are the people who purchase these products. This is accomplished by using a variety of processes, including production, distribution and retailing. They produce goods from raw materials by using machines and other machinery. This includes all types of manufactured goods, including food items, clothing, building supplies, furniture, toys, electronics, tools, machinery, vehicles, pharmaceuticals, medical devices, chemicals, and many others.
What are manufacturing & logistics?
Manufacturing refers to the process of making goods using raw materials and machines. Logistics is the management of all aspects of supply chain activities, including procurement, production planning, distribution, warehousing, inventory control, transportation, and customer service. Sometimes manufacturing and logistics are combined to refer to a wider term that includes both the process of creating products as well as their delivery to customers.
Statistics
- According to a Statista study, U.S. businesses spent $1.63 trillion on logistics in 2019, moving goods from origin to end user through various supply chain network segments. (netsuite.com)
- Job #1 is delivering the ordered product according to specifications: color, size, brand, and quantity. (netsuite.com)
- (2:04) MTO is a production technique wherein products are customized according to customer specifications, and production only starts after an order is received. (oracle.com)
- According to the United Nations Industrial Development Organization (UNIDO), China is the top manufacturer worldwide by 2019 output, producing 28.7% of the total global manufacturing output, followed by the United States, Japan, Germany, and India.[52][53] (en.wikipedia.org)
- Many factories witnessed a 30% increase in output due to the shift to electric motors. (en.wikipedia.org)
External Links
How To
How to use 5S in Manufacturing to Increase Productivity
5S stands in for "Sort", the "Set In Order", "Standardize", or "Separate". Toyota Motor Corporation invented the 5S strategy in 1954. It helps companies achieve higher levels of efficiency by improving their work environment.
This method aims to standardize production processes so that they are repeatable, measurable and predictable. Cleaning, sorting and packing are all done daily. Through these actions, workers can perform their jobs more efficiently because they know what to expect from them.
Implementing 5S requires five steps. These are Sort, Set In Order, Standardize. Separate. And Store. Each step has a different action and leads to higher efficiency. By sorting, for example, you make it easy to find the items later. When you set items in an order, you put items together. Once you have separated your inventory into groups and organized them, you will store these groups in easily accessible containers. Make sure everything is correctly labeled when you label your containers.
Employees need to reflect on how they do their jobs. Employees need to understand the reasons they do certain jobs and determine if there is a better way. To be successful in the 5S system, employees will need to acquire new skills and techniques.
The 5S method not only increases efficiency but also boosts morale and teamwork. Once they start to notice improvements, they are motivated to keep working towards their goal of increasing efficiency.