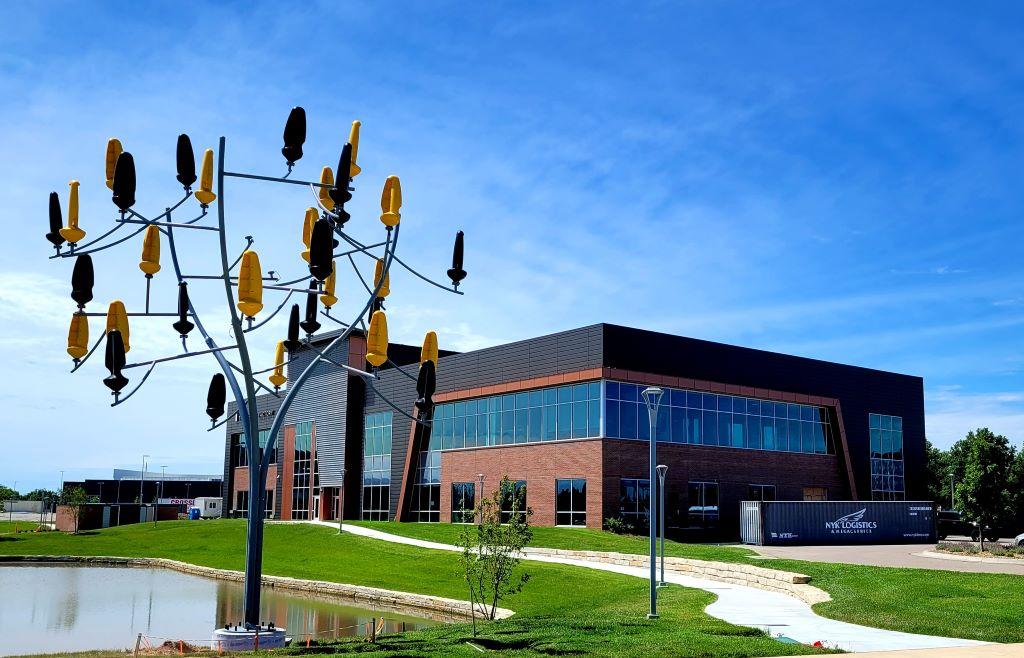
Hoshin Kanri and Value Stream Mapping are some of the lean tools. These methods use statistical data and quality control measures to reduce defects and improve process performance. The safety and well-being of employees, the cycle time, delivery times, and quality of raw materials are all improved by Lean tools. You can find more information in our articles about these tools. We also give examples and explain the basics.
Hoshin Kanri
Communicating the goals of each department is essential when it comes to Hoshinkanri implementation. It is crucial to clearly communicate the objectives of your company and the results they produce. You can view a sample Hoshin Kanri matrix by searching Google Images. The basic idea behind the matrix is that you want everyone to be aligned towards the same goals so everyone can work towards them.
Hoshin Kanri is a comprehensive method that can help identify areas in your business that require improvement. This method can help you to identify the activities that need to be improved and to establish a clear pathway from general goals towards concrete actions. It helps you track your progress, and shows how each step links to the next. Hoshin Kanri encourages collaboration to improve the company as a whole, rather than boring business plans.
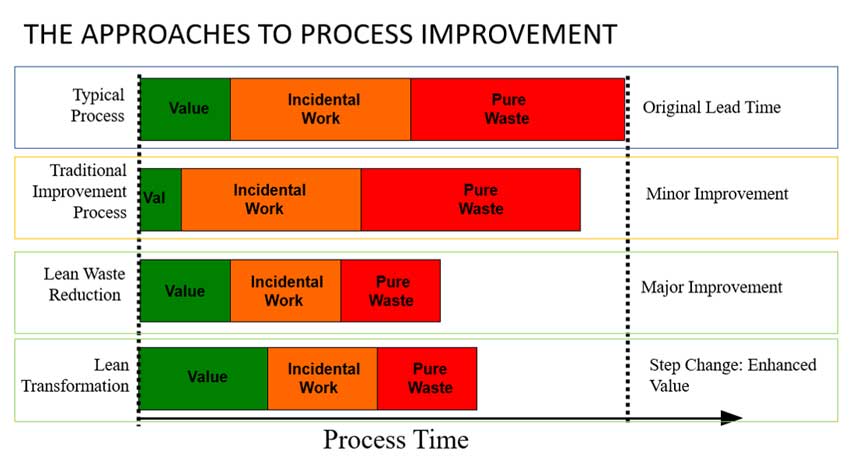
Visual board
The visual board is powerful in measuring the outcomes of a process but not an all-purpose tool. The visual board can only be used when people are involved in the process. Visual management boards should be created for individual users to give the numbers a human touch. It can also be a tool for tracking performance indicators like pieces produced per standard time or labor hours. Although there is no universal code, there a few key elements that make this tool work in a lean environment.
One of the key aspects of a visual management board is the ability to quickly communicate to all members of a team what needs to be done and who is responsible for each task. In less than 20 seconds, this information can be seen on the board. To ensure that everyone on the same page, managers must also see results from these activities. A visual management board that is updated frequently can be used to ensure that everyone stays on the right page.
Value Stream Mapping
Facilitators must identify any bottlenecks or constraints when using tools lean to value stream map. A bottleneck is the part of a process that has the lowest WIP. If a process is three steps long and has a throughput of 60 units/hour but a potential WIP rate of 42 units/hour, then Step 2 would be the bottleneck. A value streammap can be used to help identify bottlenecks or find improvements.
To properly conduct a value stream mapping, it is important to understand the system or process and the customer's perspective. This process can be cross-functional and complex. It might require extensive involvement by many people and training. Larger companies may hire a value stream manager for the mapping. Even though value stream mapping is a huge undertaking, it can be done by smaller companies that help to identify areas for improvement and possible savings. This is a powerful tool for tools lean.
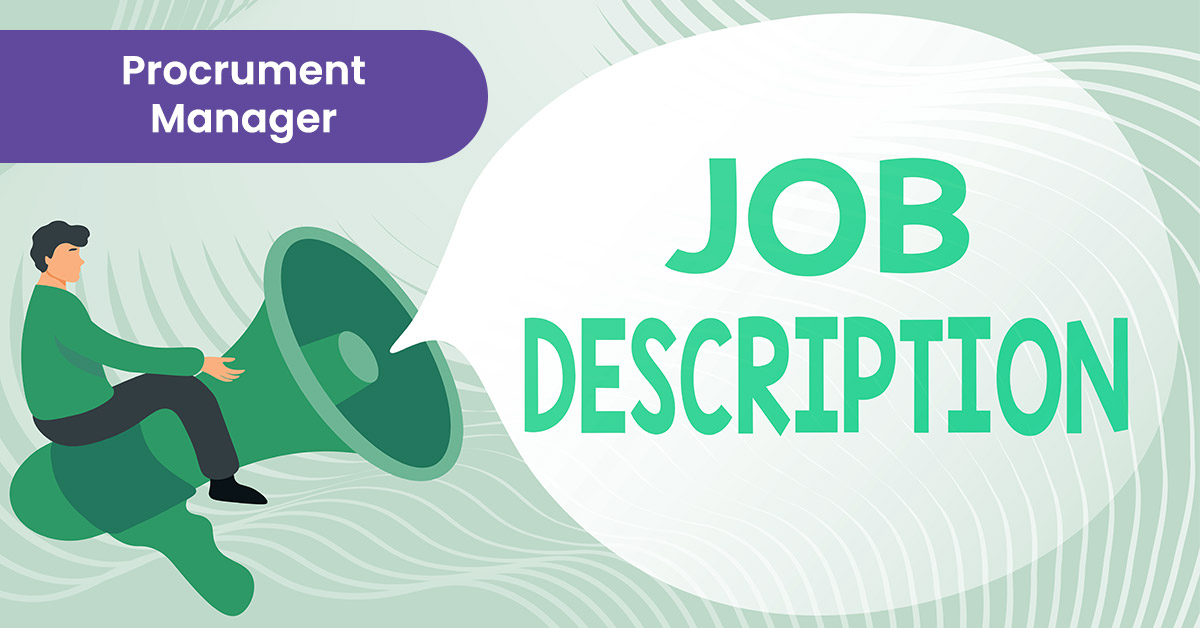
Process observation and analysis
Lean management is built on the concepts of continuous improvement, process observation and quality control. Process observation is a way to make sure standards are being maintained and that processes deliver the desired outcome. Processes that are abandoned will eventually fail. Process observation and analysis can have cultural implications, so managers need to clearly explain the need for process observation and the benefits it provides. Lean management systems include process observation and analysis. Managers need to communicate the importance of this part to their teams.
When implementing Lean, the first step is to verify the process flow map by conducting a walk-through of the process. The next step after this step is completed is to analyze all data. The Measure phase collects data regarding the current process, product, and/or service. The project leader uses statistical hypothesis testing techniques to identify the root cause of the problem. This analysis helps to determine if the problem is solved or improved.
FAQ
What are the differences between these four types?
Manufacturing refers the process of turning raw materials into useful products with machines and processes. It includes many different activities like designing, building and testing, packaging, shipping and selling, as well as servicing.
Are there any Manufacturing Processes that we should know before we can learn about Logistics?
No. No. Understanding the manufacturing process will allow you to better understand logistics.
How can I find out more about manufacturing?
Practical experience is the best way of learning about manufacturing. You can also read educational videos or take classes if this isn't possible.
Is automation important for manufacturing?
Automating is not just important for manufacturers, but also for service providers. It allows them provide faster and more efficient services. It reduces human errors and improves productivity, which in turn helps them lower their costs.
What is production management?
Production Planning is the creation of a plan to cover all aspects, such as scheduling, budgeting. Location, crew, equipment, props and other details. This document ensures that everything is prepared and available when you are ready for shooting. This document should include information about how to achieve the best results on-set. This includes information on shooting times, locations, cast lists and crew details.
It is important to first outline the type of film you would like to make. You may have already chosen the location you want, or there are locations or sets you prefer. Once you have determined your scenes and locations, it is time to start figuring out the elements that you will need for each scene. For example, you might decide that you need a car but don't know exactly what model you want. You could look online for cars to see what options are available, and then narrow down your choices by selecting between different makes or models.
Once you have found the right vehicle, you can think about adding accessories. Do you need people sitting in the front seats? You might also need someone to help you get around the back. Perhaps you would like to change the interior colour from black to white. These questions can help you decide the right look for your car. Also, think about what kind of shots you would like to capture. Do you want to film close-ups, or wider angles? Maybe you want the engine or the steering wheels to be shown. These things will help you to identify the car that you are looking for.
Once you have determined all of the above, you can move on to creating a schedule. You can create a schedule that will outline when you must start and finish your shoots. Each day will include the time when you need to arrive at the location, when you need to leave and when you need to return home. This way, everyone knows what they need to do and when. If you need to hire extra staff, you can make sure you book them in advance. You should not hire anyone who doesn't show up because of your inaction.
Also, consider how many days you will be filming your schedule. Some projects are quick and easy, while others take weeks. While creating your schedule, it is important to remember whether you will require more than one shot per day. Multiple takes at the same place will result in higher costs and longer completion times. It's better to be safe than sorry and shoot less takes if you're not certain whether you need more takes.
Budget setting is another important aspect in production planning. A realistic budget will help you work within your means. Remember that you can always reduce the budget later on if you run into unforeseen problems. However, you shouldn't overestimate the amount of money you will spend. If you underestimate how much something costs, you'll have less money to pay for other items.
Planning production is a tedious process. Once you have a good understanding of how everything works together, planning future projects becomes easy.
What does it mean to be a manufacturer?
Manufacturing Industries are those businesses that make products for sale. These products are sold to consumers. This is accomplished by using a variety of processes, including production, distribution and retailing. They create goods from raw materials, using machines and various other equipment. This includes all types if manufactured goods.
How can excess manufacturing production be reduced?
Improved inventory management is the key to reducing overproduction. This would reduce the time needed to manage inventory. By doing this, we could free up resources for other productive tasks.
This can be done by using a Kanban system. A Kanban board can be used to monitor work progress. Kanban systems allow work items to move through different states until they reach their final destination. Each state represents a different priority.
For instance, when work moves from one stage to another, the current task is complete enough to be moved to the next stage. However, if a task is still at the beginning stages, it will remain so until it reaches the end of the process.
This helps to keep work moving forward while ensuring that no work is left behind. Managers can see how much work has been done and the status of each task at any time with a Kanban Board. This information allows them to adjust their workflow based on real-time data.
Lean manufacturing is another option to control inventory levels. Lean manufacturing is about eliminating waste from all stages of the production process. Anything that does not contribute to the product's value is considered waste. The following are examples of common waste types:
-
Overproduction
-
Inventory
-
Packaging not required
-
Excess materials
Manufacturers can increase efficiency and decrease costs by implementing these ideas.
Statistics
- In the United States, for example, manufacturing makes up 15% of the economic output. (twi-global.com)
- According to the United Nations Industrial Development Organization (UNIDO), China is the top manufacturer worldwide by 2019 output, producing 28.7% of the total global manufacturing output, followed by the United States, Japan, Germany, and India.[52][53] (en.wikipedia.org)
- Many factories witnessed a 30% increase in output due to the shift to electric motors. (en.wikipedia.org)
- You can multiply the result by 100 to get the total percent of monthly overhead. (investopedia.com)
- Job #1 is delivering the ordered product according to specifications: color, size, brand, and quantity. (netsuite.com)
External Links
How To
How to use lean manufacturing in the production of goods
Lean manufacturing is a management system that aims at increasing efficiency and reducing waste. It was developed in Japan during the 1970s and 1980s by Taiichi Ohno, who received the Toyota Production System (TPS) award from TPS founder Kanji Toyoda. Michael L. Watkins published the original book on lean manufacturing, "The Machine That Changed the World," in 1990.
Lean manufacturing can be described as a set or principles that are used to improve quality, speed and cost of products or services. It is about eliminating defects and waste from all stages of the value stream. Lean manufacturing is called just-in-time (JIT), zero defect, total productive maintenance (TPM), or 5S. Lean manufacturing is about eliminating activities that do not add value, such as inspection, rework, and waiting.
Lean manufacturing can help companies improve their product quality and reduce costs. Additionally, it helps them achieve their goals more quickly and reduces employee turnover. Lean manufacturing has been deemed one of the best ways to manage the entire value-chain, including customers, distributors as well retailers and employees. Lean manufacturing can be found in many industries. Toyota's philosophy, for example, is what has enabled it to be successful in electronics, automobiles, medical devices, healthcare and chemical engineering as well as paper and food.
Five fundamental principles underlie lean manufacturing.
-
Define Value - Identify the value your business adds to society and what makes you different from competitors.
-
Reduce waste - Stop any activity that isn't adding value to the supply chains.
-
Create Flow - Ensure work moves smoothly through the process without interruption.
-
Standardize & simplify - Make processes consistent and repeatable.
-
Build relationships - Develop and maintain personal relationships with both your internal and external stakeholders.
Although lean manufacturing has always been around, it is gaining popularity in recent years because of a renewed interest for the economy after 2008's global financial crisis. To increase their competitiveness, many businesses have turned to lean manufacturing. Some economists even believe that lean manufacturing can be a key factor in economic recovery.
Lean manufacturing is becoming a popular practice in automotive. It has many advantages. These include higher customer satisfaction levels, reduced inventory levels as well as lower operating costs.
The principles of lean manufacturing can be applied in almost any area of an organization. Because it makes sure that all value chains are efficient and effectively managed, Lean Manufacturing is particularly helpful for organizations.
There are three types of lean manufacturing.
-
Just-in-Time Manufacturing: Also known as "pull systems", this type of lean manufacturing uses just-in-time manufacturing (JIT). JIT is a process in which components can be assembled at the point they are needed, instead of being made ahead of time. This approach is designed to reduce lead times and increase the availability of components. It also reduces inventory.
-
Zero Defects Manufacturing: ZDM ensures that no defective units leave the manufacturing plant. It is better to repair a part than have it removed from the production line if it needs to be fixed. This applies to finished products, which may need minor repairs before they are shipped.
-
Continuous Improvement (CI): CI aims to improve the efficiency of operations by continuously identifying problems and making changes in order to eliminate or minimize waste. It involves continuous improvement of processes, people, and tools.