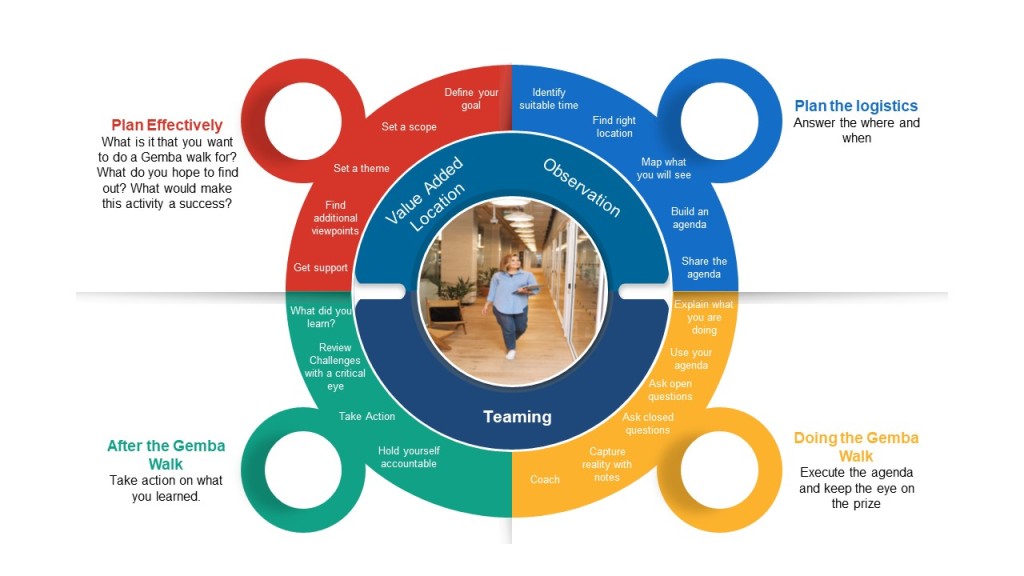
The manufacturing process includes the creation of a bill-of-materials (BOM). It outlines every item necessary for producing end products, from raw materials to assembly procedures. It is essential for any company, no matter if they are selling directly to customers or via retail channels. It is essential for companies to keep track and prevent waste. It is also useful for companies to avoid stockouts.
A bill or materials is a detailed, tabular document that lists each component of an assembly. This document lists all the parts needed to make the assembly. The parts and the subassemblies might be purchased from third parties or manufactured within the company. A unique part number will be required to identify the parts. This allows the assembly team to properly identify and gather the materials they need. You should also note any special requirements in the bill of materials. These special requirements could cause delays or even make the manufacturing process more difficult.
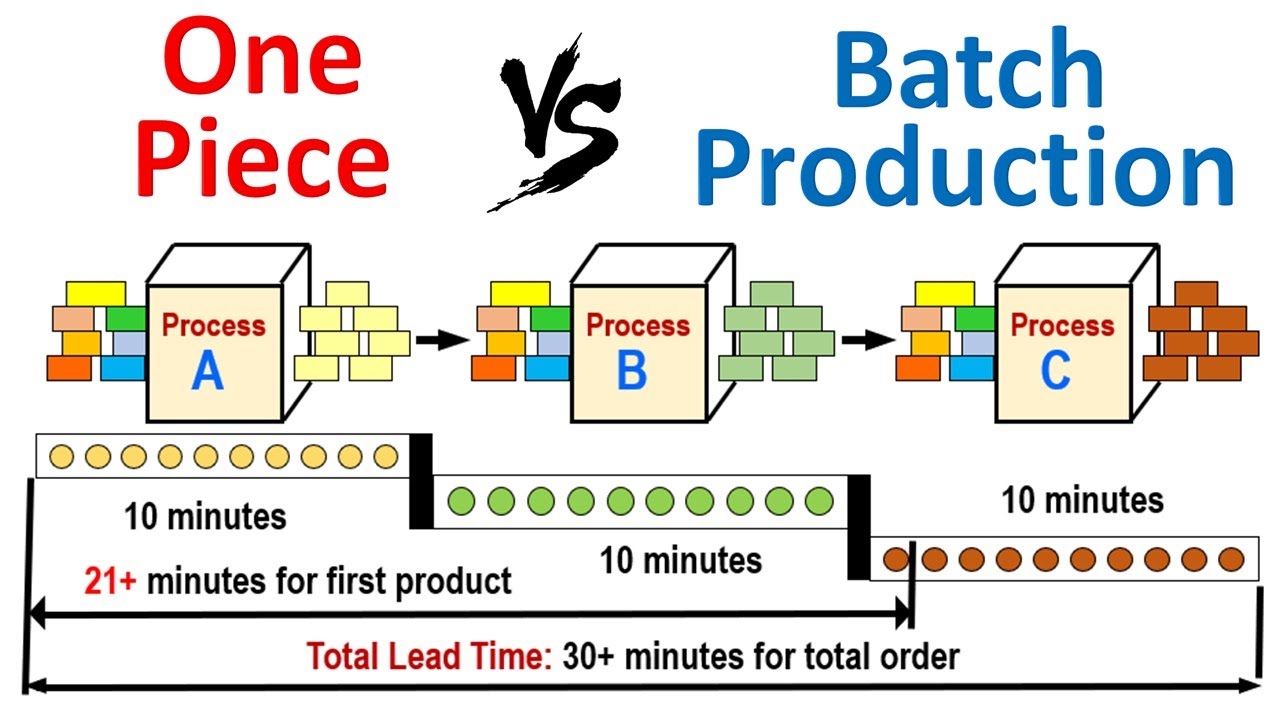
Companies value bills of material because they enable them to accurately track components and raw material. They also enable for higher productivity in production. They reduce stockouts and help companies forecast their sales. These documents enable companies to track production materials and avoid over-ordering.
A bill is a document that lists materials, components, as well as subassemblies required to produce a product. The bill lists the labor and the time it takes to complete each step of the assembly. It is also important that the bill be inclusive of the supplier(s), for each component. Other details may be included if they are necessary for the production process. It is crucial to note that the bill of materials may differ from company to company.
In manufacturing processes, bills of material are used to ensure that the product functions correctly. They help companies plan and order material, minimize waste, and reduce production errors. The bill of materials helps manufacturers to identify the raw materials needed to make a product and determine the proper amounts for each piece. It is important to understand that the bill is a roadmap of the final product. It can be difficult for a bill to material to be created, especially when there are multiple parts. However, it is possible to create a bill-of-materials using specialized software.
A bill to materials is created to meet project specifications and requirements. It can be used to communicate with manufacturing and supply-chain partners, as well as as a blueprint. This document is useful for companies in order to avoid over-ordering materials and keep track of all components used in the production process.
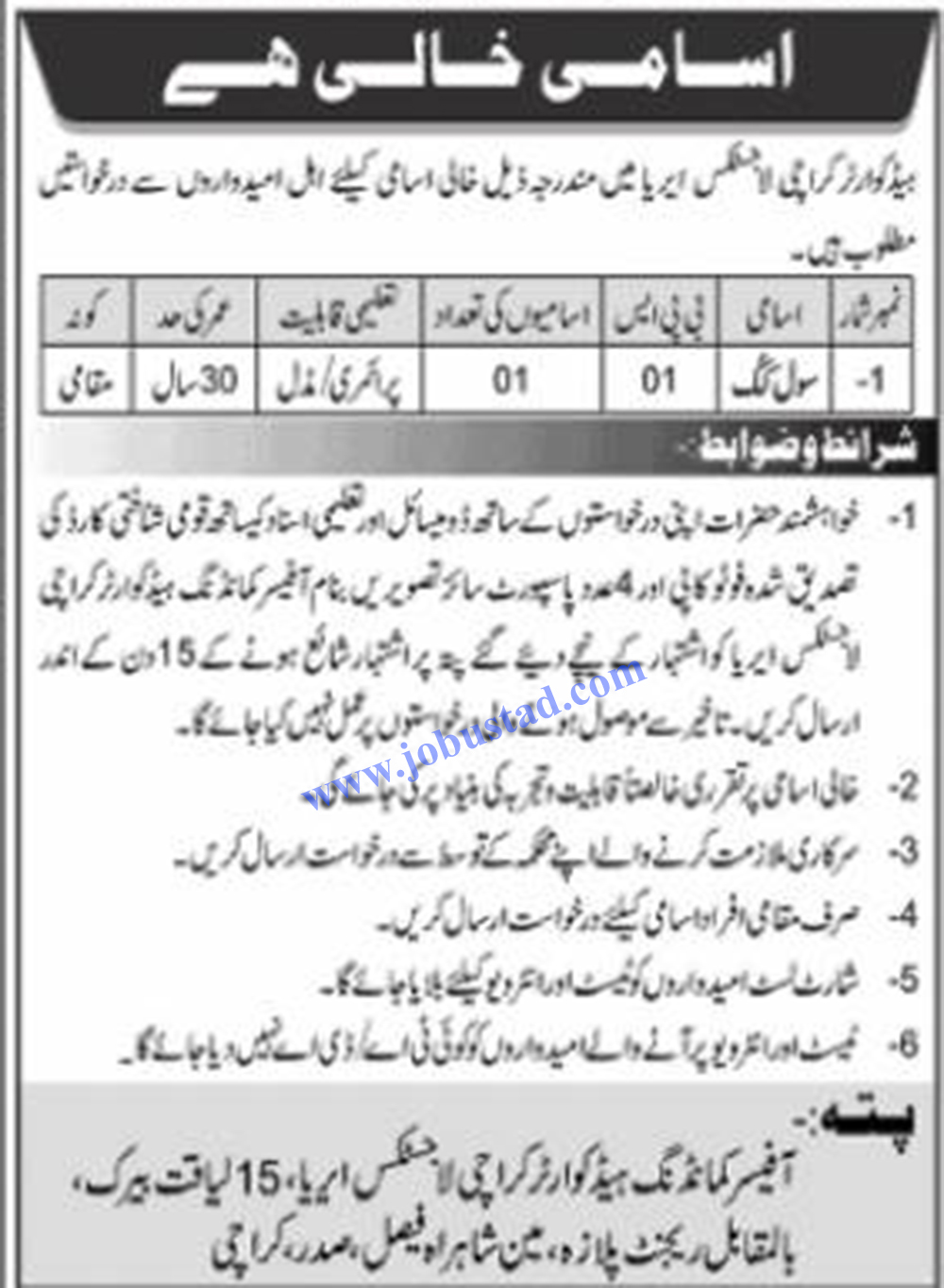
Any company that sells directly to customers or through retail channels needs a bill of materials. Bills of material allow for greater productivity and profits. They are a great way for companies to cut down on waste, prevent stockouts and make production more efficient.
FAQ
Do we need to know about Manufacturing Processes before learning about Logistics?
No. It doesn't matter if you don't know anything about manufacturing before you learn about logistics. Knowing about manufacturing processes will help you understand how logistics works.
Is automation important for manufacturing?
Automating is not just important for manufacturers, but also for service providers. It enables them to provide services faster and more efficiently. It helps them to lower costs by reducing human errors, and improving productivity.
Can we automate some parts of manufacturing?
Yes! Yes. The wheel was invented by the Egyptians thousands of years ago. Nowadays, we use robots for assembly lines.
In fact, there are several applications of robotics in manufacturing today. They include:
-
Line robots
-
Robot welding
-
Robot painting
-
Robotics inspection
-
Robots create products
There are many other examples of how manufacturing could benefit from automation. For example, 3D printing allows us to make custom products without having to wait for weeks or months to get them manufactured.
What are the main products of logistics?
Logistics refers to all activities that involve moving goods from A to B.
They encompass all aspects transport, including packaging and loading, transporting, storage, unloading.
Logisticians ensure that the product is delivered to the correct place, at the right time, and under safe conditions. They help companies manage their supply chain efficiency by providing information on demand forecasts, stock levels, production schedules, and availability of raw materials.
They also keep track of shipments in transit, monitor quality standards, perform inventories and order replenishment, coordinate with suppliers and vendors, and provide support services for sales and marketing.
Statistics
- According to a Statista study, U.S. businesses spent $1.63 trillion on logistics in 2019, moving goods from origin to end user through various supply chain network segments. (netsuite.com)
- It's estimated that 10.8% of the U.S. GDP in 2020 was contributed to manufacturing. (investopedia.com)
- [54][55] These are the top 50 countries by the total value of manufacturing output in US dollars for its noted year according to World Bank.[56] (en.wikipedia.org)
- According to the United Nations Industrial Development Organization (UNIDO), China is the top manufacturer worldwide by 2019 output, producing 28.7% of the total global manufacturing output, followed by the United States, Japan, Germany, and India.[52][53] (en.wikipedia.org)
- You can multiply the result by 100 to get the total percent of monthly overhead. (investopedia.com)
External Links
How To
How to Use Six Sigma in Manufacturing
Six Sigma can be described as "the use of statistical process control (SPC), techniques to achieve continuous improvement." Motorola's Quality Improvement Department developed it at their Tokyo plant in Japan in 1986. Six Sigma's main goal is to improve process quality by standardizing processes and eliminating defects. This method has been adopted by many companies in recent years as they believe there are no perfect products or services. Six Sigma's main objective is to reduce variations from the production average. If you take a sample and compare it with the average, you will be able to determine how much of the production process is different from the norm. If it is too large, it means that there are problems.
Understanding the nature of variability in your business is the first step to Six Sigma. Once you have a good understanding of the basics, you can identify potential sources of variation. Also, you will need to identify the sources of variation. Random variations are caused when people make mistakes. While systematic variations are caused outside of the process, they can occur. These are, for instance, random variations that occur when widgets are made and some fall off the production line. You might notice that your widgets always fall apart at the same place every time you put them together.
Once you've identified where the problems lie, you'll want to design solutions to eliminate those problems. It might mean changing the way you do business or redesigning it entirely. After implementing the new changes, you should test them again to see if they worked. If they didn't work, then you'll need to go back to the drawing board and come up with another plan.