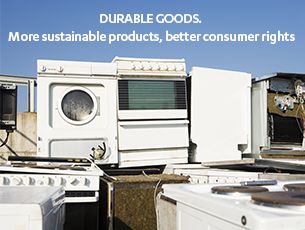
Lean thinking can help improve an organization's performance. It involves eliminating wastes and unvalued activities from your processes. It is also a means to create a lean culture within your organization. Lean culture refers to a set or principles that encourage employee morale, quality improvement, and productivity. It creates a more sustainable work environment.
The first step in implementing lean thinking is to identify value for your customer. This means understanding your customers' needs and the whole value chain. Once you've identified the value chain, you can identify the steps within your process. By identifying the steps within different processes, you can determine if your current process is inefficient. You can also use value stream mapping to visualize how your business is currently operating. The value streaming map displays the flow of the business, its workings, and the added value each process brings to the table.
Lean thinking is all about flow. It's the ability to swiftly switch between one activity and another. This is essential when responding quickly to customer demand. It also reduces the need for inventory and backlogs. It also enables workers to quickly switch from one task to another.
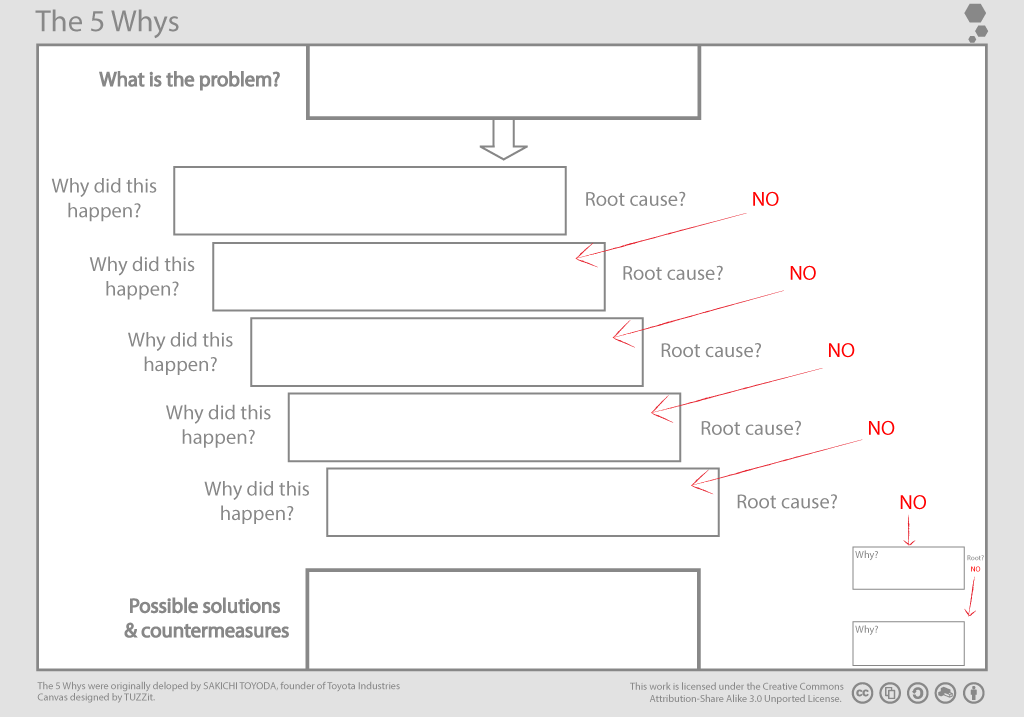
Lean organizations have a similar approach to managing output. They promote collaboration and communication. They celebrate and encourage quality assurance. They reduce unnecessary costs to customers and suppliers.
Lean thinking refers to a continuous process. It can be applied to any type or work. It can help to reduce environmental damage, reduce the waste, and improve employee motivation. Although lean thinking is often used in manufacturing, it can be used in all areas of business.
Creating a culture that fosters lean thinking is a key factor in implementing lean production practices. It should be clear about the value of lean production practices, as well as the motivation of employees. It also must be willing to take small steps forward on a regular basis. This is called "kaizen".
Lean thinking refers to continuous improvement that requires a kaizen spirit. To improve the quality of your product you have to be open to small improvements each day. This can be achieved by either implementing organizational changes or using standardized tasks. Standardized work is a visual representation of the flow of work. Everything is clearly located. It helps people see how to overcome obstacles and make work easier.
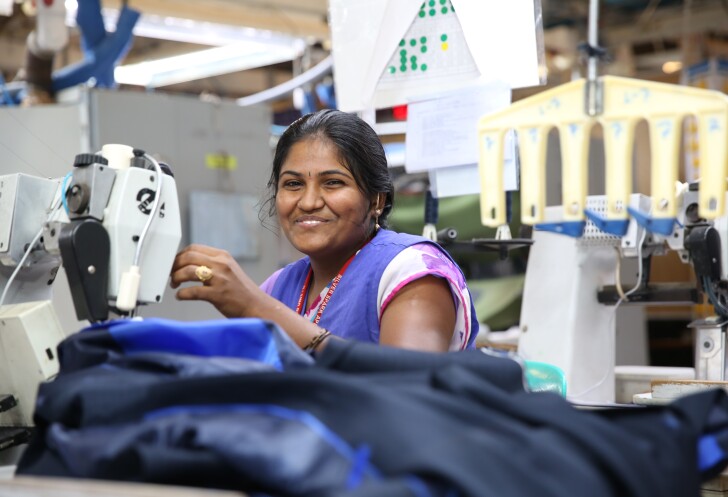
When implementing lean production methods, it is important to also consider other production metrics. The ratio of running time to downtime shows how frequently an asset is available for production. It also displays how often planned maintenance is necessary. The quality ratio measures how well a supplier can deliver high quality products.
It is also important to be aware of the risks involved in the "Just-In-Time" principle. This principle ensures that supplies arrive on time. It helps you focus your mind on the task at the hand and allows you to concentrate. But it can cause problems in the industry.
FAQ
How can we improve manufacturing efficiency?
First, determine which factors have the greatest impact on production time. Next, we must find ways to improve those factors. You can start by identifying the most important factors that impact production time. Once you have identified the factors, then try to find solutions.
Is automation necessary in manufacturing?
Automating is not just important for manufacturers, but also for service providers. It enables them to provide services faster and more efficiently. It reduces human errors and improves productivity, which in turn helps them lower their costs.
What are the 4 types manufacturing?
Manufacturing refers the process of turning raw materials into useful products with machines and processes. Manufacturing can include many activities such as designing and building, testing, packaging shipping, selling, servicing, and other related activities.
What is production planning?
Production Planning involves developing a plan for all aspects of the production, including scheduling, budgeting, casting, crew, location, equipment, props, etc. This document aims to ensure that everything is planned and ready when you are ready to shoot. This document should also include information on how to get the best result on set. This information includes locations, crew details and equipment requirements.
The first step in filming is to define what you want. You may have already decided where you would like to shoot, or maybe there are specific locations or sets that you want to use. Once you have determined your scenes and locations, it is time to start figuring out the elements that you will need for each scene. If you decide you need a car and don't know what model to choose, this could be an example. This is where you can look up car models online and narrow down your options by choosing from different makes and models.
After you have selected the car you want, you can begin to think about additional features. What about additional seating? Maybe you need someone to move around in the back. You may want to change the interior's color from black or white. These questions will help you determine the exact look and feel of your car. You can also think about the type of shots you want to get. What type of shots will you choose? Maybe you want the engine or the steering wheels to be shown. All of these things will help you identify the exact style of car you want to film.
Once you have all the information, you are ready to create a plan. You can create a schedule that will outline when you must start and finish your shoots. A schedule for each day will detail when you should arrive at the location and when you need leave. Everyone will know what they need and when. Book extra staff ahead of time if you need them. It is not worth hiring someone who won’t show up because you didn’t tell him.
Your schedule will also have to be adjusted to reflect the number of days required to film. Some projects may only take a couple of days, while others could last for weeks. When you are creating your schedule, you should always keep in mind whether you need more than one shot per day or not. Multiple takes at the same place will result in higher costs and longer completion times. It's better to be safe than sorry and shoot less takes if you're not certain whether you need more takes.
Another important aspect of production planning is setting budgets. As it will allow you and your team to work within your financial means, setting a realistic budget is crucial. Remember that you can always reduce the budget later on if you run into unforeseen problems. You shouldn't underestimate the amount you'll spend. You'll end up with less money after paying for other things if the cost is underestimated.
Planning production is a tedious process. Once you have a good understanding of how everything works together, planning future projects becomes easy.
What are my options for learning more about manufacturing
Practical experience is the best way of learning about manufacturing. But if that is not possible you can always read books and watch educational videos.
What are the responsibilities of a production planner
Production planners make sure that every aspect of the project is delivered on-time, within budget, and within schedule. They also ensure that the product/service meets the client’s needs.
Statistics
- [54][55] These are the top 50 countries by the total value of manufacturing output in US dollars for its noted year according to World Bank.[56] (en.wikipedia.org)
- Many factories witnessed a 30% increase in output due to the shift to electric motors. (en.wikipedia.org)
- You can multiply the result by 100 to get the total percent of monthly overhead. (investopedia.com)
- Job #1 is delivering the ordered product according to specifications: color, size, brand, and quantity. (netsuite.com)
- In 2021, an estimated 12.1 million Americans work in the manufacturing sector.6 (investopedia.com)
External Links
How To
How to Use the 5S to Increase Productivity In Manufacturing
5S stands to stand for "Sort", “Set In Order", “Standardize", and "Store". Toyota Motor Corporation created the 5S methodology in 1954. It allows companies to improve their work environment, thereby achieving greater efficiency.
This method aims to standardize production processes so that they are repeatable, measurable and predictable. This means that tasks such as cleaning, sorting, storing, packing, and labeling are performed daily. These actions allow workers to perform their job more efficiently, knowing what to expect.
There are five steps that you need to follow in order to implement 5S. Each step has a different action and leads to higher efficiency. If you sort items, it makes them easier to find later. When you set items in an order, you put items together. You then organize your inventory in groups. Labeling your containers will ensure that everything is correctly labeled.
Employees must be able to critically examine their work practices. Employees need to be able understand their motivations and discover alternative ways to do them. They will need to develop new skills and techniques in order for the 5S system to be implemented.
The 5S Method not only improves efficiency, but it also helps employees to be more productive and happier. They feel more motivated to work towards achieving greater efficiency as they see the results.