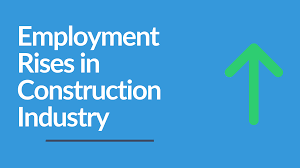
This is the place to go if you want news about manufacturing. Fusion 360 community members discuss the week's happenings and share news regarding manufacturing innovation. Fusion 360 covers all aspects of the industry, including Alexandria Industries and Festo's expansion plans. Fusion 360 provides news and information on a variety of topics. Here are some recent articles about manufacturing innovations. Continue reading to find out more.
Alexandria Industries
Alexandria Industries recently announced that they are expanding their operations in Douglas County. While they currently employ 480 people, the company is investing several million dollars in the new facility to grow even more. Alexandria Industries' growth has been faster than their revenue and employment levels before the recession. However, they are still struggling to find qualified candidates for 50 new positions. These positions are $15-30 per hour with benefits. Alexandria Industries is looking for a new career.
Alexandria Industries recently promoted new management in order to support their growth. Jonathan D. Olson will be the CFO of Alexandria Industries. He is committed to investing and supporting the company's employees. He was also appointed the company's CFO. He is looking to improve the working environment of employees and invest heavily in training programs. Alexandria Plastics, Inc., a manufacturer and distributor of foam-molded and plastic injection parts, will be integrated into this acquisition, which will enhance the company’s capabilities.
Festo U.S. expansion plans
Festo Corp. just announced expansion plans for North American manufacturing operations. The company will increase its presence in Mason by three times and create 350 additional jobs. This expansion will bring in $90 million and create new jobs over five more years. Festo will also provide support services and industrial training solutions. A new Didactic Learning Centre will be added to the expansion, which will serve colleges and manufacturing companies throughout the Tristate region.
The new Mason facility will be used to produce automation components. The new facility will be home to both a Research and Development Center and Global Production Center. Upon completion, both will employ more than 1,000 people. The company will create new jobs as well as a new research center to develop automation systems. This expansion is part the company's larger plan to target the U.S. market.
Additive Manufacturing
With technology's advancement, manufacturers are now seeing the benefits of additive production in the manufacturing process. To reach the global marketplace, several companies have made partnerships. Some of these partnerships involve Voxeljet and AGC Ceramic, a glass and ceramic company. Voxeljet is partnering with AGC Ceramic to bring Brightorb, an innovative ceramic material, to the market and optimize VX1000 for 3D printing ceramic powder. Stratasys is also partnering with Tata Technologies to promote Indian additive manufacturing technologies.
Collaboration agreements are not the only thing that is being done for additive manufacturing. New technologies are also being developed. Optimus 3D purchased a fourth Renishaw metal additive production system. Moreover, the company has also expanded its 3D printing machine portfolio to include metal powder. With these developments, additive manufacture is poised to be an essential component of advanced PLM. The company will become more IoT-oriented as well as integrated. These new developments will lead to the rapid growth of a wide variety of industries.
Collaborative Manufacturing
What is collaborative manufacturing? Collaborative manufacturing involves input directly from plant floor systems. This information is important for the management process. It also involves an interactive process between the manufacturing and design team. Collaboration in manufacturing can improve productivity and quality, while reducing the amount of workers required to complete each step. But what are the real benefits of collaborative production? Let's examine a few. How can collaborative manufacturing improve plant performance. Learn more.
Many industries are now adopting collaborative manufacturing. It is used for product development, product design improvement, inventory sync across the supply chain, and logistics cost reduction. Additionally, collaborative manufacturing helps to reduce time-to -market and volume as well as shorten manufacturing cycles between suppliers. Collaborative manufacturing can bring significant benefits to everyone, so it is crucial for companies. It is not right for everyone. Be sure to consider the benefits before you adopt collaborative manufacturing.
FAQ
What types of jobs can you find in logistics
There are different kinds of jobs available in logistics. Some examples are:
-
Warehouse workers – They load and unload pallets and trucks.
-
Transportation drivers: They drive trucks and trailers and deliver goods and make pick-ups.
-
Freight handlers are people who sort and pack freight into warehouses.
-
Inventory managers – These people oversee inventory at warehouses.
-
Sales reps are people who sell products to customers.
-
Logistics coordinators – They plan and coordinate logistics operations.
-
Purchasing agents - They buy goods and services that are necessary for company operations.
-
Customer service representatives – They answer emails and phone calls from customers.
-
Shippers clerks - They process shipping order and issue bills.
-
Order fillers: They fill orders based off what has been ordered and shipped.
-
Quality control inspectors: They inspect outgoing and incoming products for any defects.
-
Others – There are many other types available in logistics. They include transport supervisors, cargo specialists and others.
What skills do production planners need?
Production planners must be flexible, organized, and able handle multiple tasks. Effective communication with clients and colleagues is essential.
What is the responsibility of a logistics manager?
Logistics managers make sure all goods are delivered on schedule and without damage. This is done through his/her expertise and knowledge about the company's product range. He/she should ensure that sufficient stock is available in order to meet customer demand.
Statistics
- Job #1 is delivering the ordered product according to specifications: color, size, brand, and quantity. (netsuite.com)
- In 2021, an estimated 12.1 million Americans work in the manufacturing sector.6 (investopedia.com)
- In the United States, for example, manufacturing makes up 15% of the economic output. (twi-global.com)
- You can multiply the result by 100 to get the total percent of monthly overhead. (investopedia.com)
- It's estimated that 10.8% of the U.S. GDP in 2020 was contributed to manufacturing. (investopedia.com)
External Links
How To
How to Use Lean Manufacturing in the Production of Goods
Lean manufacturing refers to a method of managing that seeks to improve efficiency and decrease waste. It was developed by Taiichi Okono in Japan, during the 1970s & 1980s. TPS founder Kanji Takoda awarded him the Toyota Production System Award (TPS). Michael L. Watkins published the original book on lean manufacturing, "The Machine That Changed the World," in 1990.
Lean manufacturing is often defined as a set of principles used to improve the quality, speed, and cost of products and services. It emphasizes the elimination and minimization of waste in the value stream. Lean manufacturing is also known as just in time (JIT), zero defect total productive maintenance(TPM), and five-star (S). Lean manufacturing eliminates non-value-added tasks like inspection, rework, waiting.
Lean manufacturing is a way for companies to achieve their goals faster, improve product quality, and lower costs. Lean manufacturing has been deemed one of the best ways to manage the entire value-chain, including customers, distributors as well retailers and employees. Lean manufacturing is widely used in many industries. Toyota's philosophy is the foundation of its success in automotives, electronics and appliances, healthcare, chemical engineers, aerospace, paper and food, among other industries.
Five fundamental principles underlie lean manufacturing.
-
Define Value - Determine the value that your business brings to society. Also, identify what sets you apart from your competitors.
-
Reduce Waste – Eliminate all activities that don't add value throughout the supply chain.
-
Create Flow – Ensure that work flows smoothly throughout the process.
-
Standardize and Simplify – Make processes as consistent, repeatable, and as simple as possible.
-
Building Relationships – Establish personal relationships with both external and internal stakeholders.
Lean manufacturing isn’t new, but it has seen a renewed interest since 2008 due to the global financial crisis. Many businesses are now using lean manufacturing to improve their competitiveness. According to some economists, lean manufacturing could be a significant factor in the economic recovery.
Lean manufacturing is now becoming a common practice in the automotive industry, with many benefits. These include improved customer satisfaction, reduced inventory levels, lower operating costs, increased productivity, and better overall safety.
Any aspect of an enterprise can benefit from Lean manufacturing. Lean manufacturing is most useful in the production sector of an organisation because it ensures that each step in the value-chain is efficient and productive.
There are three main types in lean manufacturing
-
Just-in Time Manufacturing, (JIT): This kind of lean manufacturing is also commonly known as "pull-systems." JIT is a process in which components can be assembled at the point they are needed, instead of being made ahead of time. This method reduces lead times, increases availability, and decreases inventory.
-
Zero Defects Manufacturing (ZDM),: ZDM is a system that ensures no defective units are left the manufacturing facility. It is better to repair a part than have it removed from the production line if it needs to be fixed. This applies to finished products, which may need minor repairs before they are shipped.
-
Continuous Improvement: Continuous Improvement aims to improve efficiency by continually identifying problems and making adjustments to eliminate or minimize waste. Continuous improvement involves continuous improvement of processes and people as well as tools.