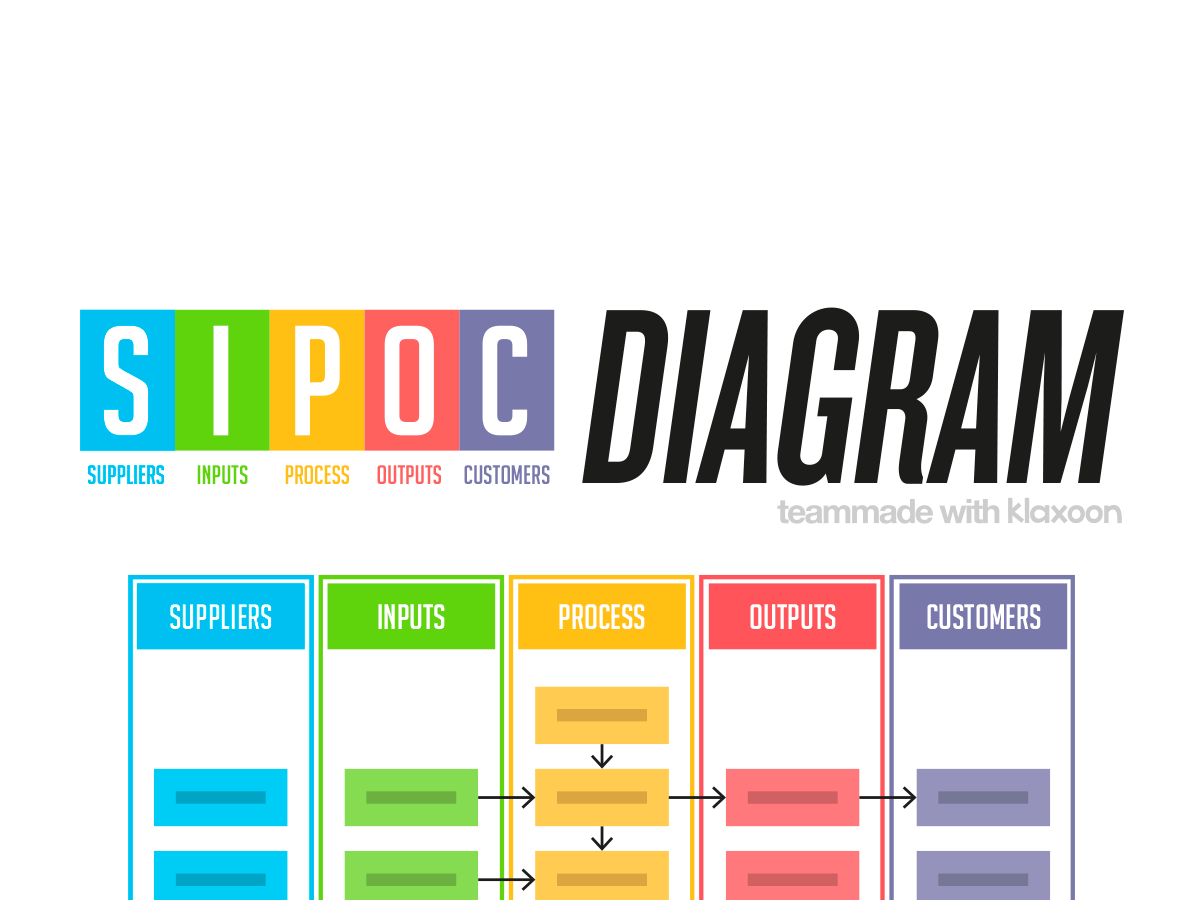
Creating a bill of materials (BOM) is an essential part of the manufacturing process. The bill of materials (BOM) outlines all the items required to make end products. This includes raw materials, assembly procedures, and so on. It is essential for any company, no matter if they are selling directly to customers or via retail channels. It helps companies to keep track of their stock, avoid waste, and reduce production mistakes. It can also help companies avoid stockouts.
A bill to materials is a detailed and tabular document that lists the components in an assembly. It also lists the parts required to build the assembly. The parts and the subassemblies might be purchased from third parties or manufactured within the company. The parts will need to be identified with a unique part number. This allows the assembly staff to easily identify and gather all the materials they require. Note any special requirements that may be required on the bill. These special requirements could lead to delays or even errors during the manufacturing process.
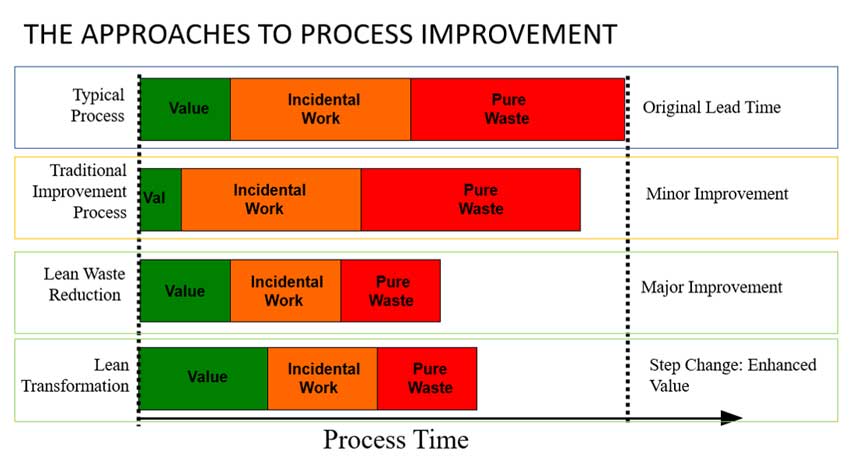
Companies are able to keep track of components and raw materials with bills of materials. They enable more productive production. They can prevent stockouts and allow companies to forecast their sales. These documents are also useful for companies in tracking the production materials and avoiding over-ordering.
A bill-of-materials is a document listing the materials, components and subassemblies that are required to manufacture a product. A bill of materials lists labor and time required to complete each stage. It is also important to note that the bill of materials must include the supplier(s) for each component. It may also contain other critical details for the production. It is important that you note that every company will have a different bill of materials.
Bills of materials are used in manufacturing processes to make sure that the finished product functions properly. They can also be used to help companies plan and order materials, prevent waste, and reduce production mistakes. The bill of material helps manufacturers identify the materials necessary to make a product, and then determine the correct amounts. Important to remember that the bill of materials is a roadmap for the finished product. It can be difficult for a bill to material to be created, especially when there are multiple parts. However, there are software solutions that make it easy to create a bill for materials.
To meet the specifications and needs of the project, a bill is made. It can be used to communicate with manufacturing and supply-chain partners, as well as as a blueprint. This document assists companies in avoiding over-ordering material and keeping track of all components.
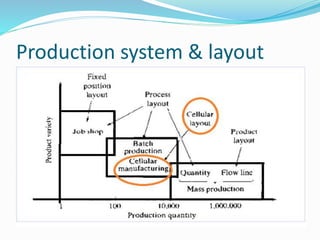
A bill of material is essential for any company who sells directly to customers through retail channels. Bills of material allow for greater productivity and profits. They can be used to help companies avoid waste, make production mistakes, and reduce stockouts.
FAQ
What are the 7 Rs of logistics.
The acronym 7Rs of Logistics refers to the seven core principles of logistics management. It was developed by International Association of Business Logisticians (IABL), and published as part of their "Seven Principles of Logistics Management Series" in 2004.
The acronym is made up of the following letters:
-
Responsible – ensure that all actions are legal and don't cause harm to anyone else.
-
Reliable: Have faith in your ability or the ability to honor any promises made.
-
Use resources effectively and sparingly.
-
Realistic - Consider all aspects of operations, including environmental impact and cost effectiveness.
-
Respectful – Treat others fairly and equitably.
-
Resourceful - look for opportunities to save money and increase productivity.
-
Recognizable - provide customers with value-added services.
What is the importance of automation in manufacturing?
Not only is automation important for manufacturers, but it's also vital for service providers. Automation allows them to deliver services quicker and more efficiently. It helps them to lower costs by reducing human errors, and improving productivity.
What are the responsibilities of a logistic manager?
Logistics managers make sure all goods are delivered on schedule and without damage. This is achieved by using their knowledge and experience with the products of the company. He/she must also ensure sufficient stock to meet the demand.
How can manufacturing overproduction be reduced?
It is essential to find better ways to manage inventory to reduce overproduction. This would reduce the amount of time spent on unnecessary activities such as purchasing, storing, and maintaining excess stock. This could help us free up our time for other productive tasks.
You can do this by adopting a Kanban method. A Kanbanboard is a visual tool that allows you to keep track of the work being done. Work items are moved through various states to reach their destination in a Kanban system. Each state represents an individual priority level.
If work is moving from one stage to the other, then the current task can be completed and moved on to the next. It is possible to keep a task in the beginning stages until it gets to the end.
This allows for work to continue moving forward, while also ensuring that there is no work left behind. A Kanban board allows managers to monitor how much work is being completed at any given moment. This information allows managers to adjust their workflow based off real-time data.
Lean manufacturing is another option to control inventory levels. Lean manufacturing emphasizes eliminating waste in all phases of production. Any product that isn't adding value can be considered waste. Some common types of waste include:
-
Overproduction
-
Inventory
-
Unnecessary packaging
-
Exceed materials
These ideas can help manufacturers improve efficiency and reduce costs.
How does a Production Planner differ from a Project Manager?
A production planner is more involved in the planning phase of the project than a project manger.
What is production management?
Production Planning includes planning for all aspects related to production. This document aims to ensure that everything is planned and ready when you are ready to shoot. You should also have information to ensure the best possible results on set. This information includes locations, crew details and equipment requirements.
The first step is to decide what you want. You may have already chosen the location you want, or there are locations or sets you prefer. Once you have identified your locations and scenes it's time to begin figuring out what elements you will need for each one. One example is if you are unsure of the exact model you want but decide that you require a car. In this case, you could start looking up cars online to find out what models are available and then narrow your choices by choosing between different makes and models.
Once you have found the right car, you can start thinking about extras. You might need to have people in the front seats. Or maybe you just need someone to push the car around. You may want to change the interior's color from black or white. These questions can help you decide the right look for your car. You can also think about the type of shots you want to get. You will be filming close-ups and wide angles. Maybe the engine or steering wheel is what you are looking to film. These factors will help you determine which car style you want to film.
Once you have all the information, you are ready to create a plan. You can create a schedule that will outline when you must start and finish your shoots. Every day will have a time for you to arrive at the location, leave when you are leaving and return home when you are done. So everyone is clear about what they need to do. If you need to hire extra staff, you can make sure you book them in advance. It is not worth hiring someone who won’t show up because you didn’t tell him.
Your schedule will also have to be adjusted to reflect the number of days required to film. Some projects only take one or two days, while others may last weeks. While creating your schedule, it is important to remember whether you will require more than one shot per day. Multiple shots at the same location can increase costs and make it more difficult to complete. It's better to be safe than sorry and shoot less takes if you're not certain whether you need more takes.
Another important aspect of production planning is setting budgets. Setting a realistic budget is essential as it will allow you to work within your means. You can always lower the budget if you encounter unexpected problems. But, don't underestimate how much money you'll spend. You will end up spending less money if you underestimate the cost of something.
Production planning is a very detailed process, but once you understand how everything works together, it becomes easier to plan future projects.
How can manufacturing avoid production bottlenecks
The key to avoiding bottlenecks in production is to keep all processes running smoothly throughout the entire production cycle, from the time you receive an order until the time when the product ships.
This includes both quality control and capacity planning.
The best way to do this is to use continuous improvement techniques such as Six Sigma.
Six Sigma can be used to improve the quality and decrease waste in all areas of your company.
It seeks to eliminate variation and create consistency in your work.
Statistics
- It's estimated that 10.8% of the U.S. GDP in 2020 was contributed to manufacturing. (investopedia.com)
- Job #1 is delivering the ordered product according to specifications: color, size, brand, and quantity. (netsuite.com)
- According to the United Nations Industrial Development Organization (UNIDO), China is the top manufacturer worldwide by 2019 output, producing 28.7% of the total global manufacturing output, followed by the United States, Japan, Germany, and India.[52][53] (en.wikipedia.org)
- In the United States, for example, manufacturing makes up 15% of the economic output. (twi-global.com)
- [54][55] These are the top 50 countries by the total value of manufacturing output in US dollars for its noted year according to World Bank.[56] (en.wikipedia.org)
External Links
How To
How to use the Just In-Time Production Method
Just-intime (JIT), a method used to lower costs and improve efficiency in business processes, is called just-in-time. It's a way to ensure that you get the right resources at just the right time. This means you only pay what you use. Frederick Taylor, a 1900s foreman, first coined the term. He observed how workers were paid overtime if there were delays in their work. He realized that workers should have enough time to complete their jobs before they begin work. This would help increase productivity.
JIT is a way to plan ahead and make sure you don't waste any money. The entire project should be looked at from start to finish. You need to ensure you have enough resources to tackle any issues that might arise. You can anticipate problems and have enough equipment and people available to fix them. This way, you won't end up paying extra money for things that weren't really necessary.
There are many types of JIT methods.
-
Demand-driven: This is a type of JIT where you order the parts/materials needed for your project regularly. This will enable you to keep track of how much material is left after you use it. This will let you know how long it will be to produce more.
-
Inventory-based: This allows you to store the materials necessary for your projects in advance. This allows you to predict how much you can expect to sell.
-
Project-driven: This approach involves setting aside sufficient funds to cover your project's costs. Knowing how much money you have available will help you purchase the correct amount of materials.
-
Resource-based JIT : This is probably the most popular type of JIT. Here, you allocate certain resources based on demand. For instance, if you have a lot of orders coming in, you'll assign more people to handle them. If you don’t have many orders you will assign less people to the work.
-
Cost-based: This is a similar approach to resource-based but you are not only concerned with how many people you have, but also how much each one costs.
-
Price-based pricing: This is similar in concept to cost-based but instead you look at how much each worker costs, it looks at the overall company's price.
-
Material-based: This approach is similar to cost-based. However, instead of looking at the total cost for the company, you look at how much you spend on average on raw materials.
-
Time-based JIT is another form of resource-based JIT. Instead of focusing on how much each employee costs, you focus on how long it takes to complete the project.
-
Quality-based JIT - This is another form of resource-based JIT. Instead of focusing on the cost of each worker or how long it takes, think about how high quality your product is.
-
Value-based JIT : This is the newest type of JIT. In this instance, you are not concerned about the product's performance or meeting customer expectations. Instead, you're focused on how much value you add to the market.
-
Stock-based: This inventory-based approach focuses on how many items are being produced at any one time. It's useful when you want maximum production and minimal inventory.
-
Just-in-time (JIT) planning: This is a combination of JIT and supply chain management. It is the process of scheduling components' delivery as soon as they have been ordered. It is essential because it reduces lead-times and increases throughput.