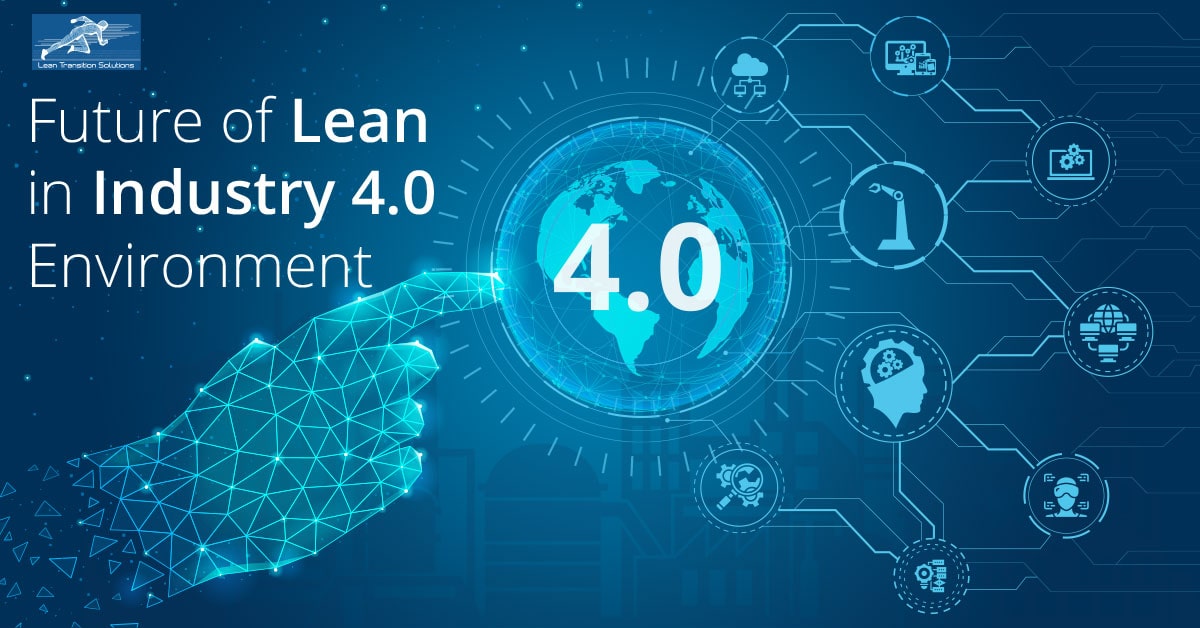
Opportunities in the manufacturing of wind turbines
There are many tasks required to manufacture wind turbines. These jobs could include blade epoxies or tower assembly. Some wind turbine manufacturing companies also contract with third-party suppliers to manufacture various components. Wind turbine components can be huge so they must be moved quickly and efficiently. For this purpose, companies require teams of logisticians and rail freight driver drivers.
A bachelor's degree is usually required for jobs in wind turbine manufacturing, but some positions require a master's degree. Most jobs in the wind turbine industry require engineering or environmental engineering concentrations. Entry-level engineers should have advanced computer skills, and must also hold a degree. They work closely with more experienced staff to ensure quality control. They might also be responsible for more complicated projects.
The manufacturing of wind turbines involves several processes
The main components of a turbine's wind turbine are the blades. Each blade has two faces connected by integral shear Webs. The support for the blades is provided by a shell fairing and a spar. These structures can withstand both edgewise and flapwise loads. The spar resists edgewise bends caused by wind pressure or gravitational forces. The blades are shaped to withstand these forces.
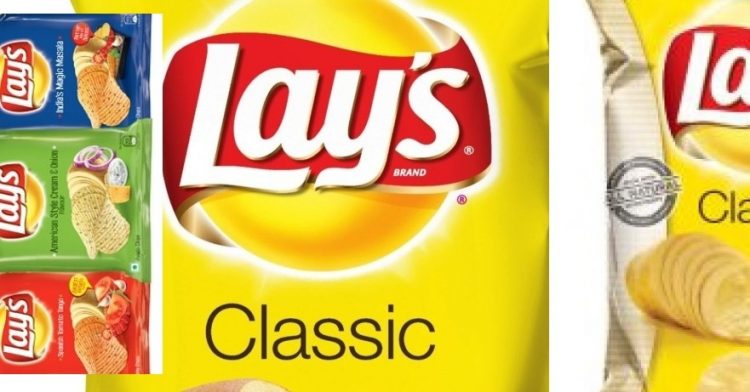
The blades can be made of a variety materials. Aluminum and lightweight woods are also options. While fiberglass is the most commonly used material for commercial windturbine blades, it can be made from other materials as well. The blades can then be covered in foil and joined to tubes which pump resin.
Competitors in wind turbine manufacturing
Although Chinese manufacturers are a rising force in global wind industry, it is not yet the dominant one. Chinese turbine manufacturers have not been able to overthrow incumbents in developed countries. They may still be able to expand their overseas operations if they invest more in local manufacturing.
Large turbine manufacturers are outsourcing more parts. However, many people are choosing to make their own components. This has both its advantages and disadvantages. Companies such as Vestas in Pueblo, Colorado, have embraced this strategy, manufacturing wind turbine towers for third-party US projects. This agreement allows the tower factory to use up 25 percent of its manufacturing capacity and supports 100 jobs in the local area. This approach has a downside: poor quality control. Some outsourced components have failed in the past, including gearbox failures and blade cracking. Some foundations built offshore even contain low-quality steel.
Manufacturing wind turbines poses health and safety risks
Health and safety is one of the most important issues in wind turbine manufacturing. The hazards faced by workers can result in long-term injuries or even fatalities. There are several ways to reduce the risk. These include proper training and routine inspections. These tips will help you keep your employees safe at work in a windturbine manufacturing plant.
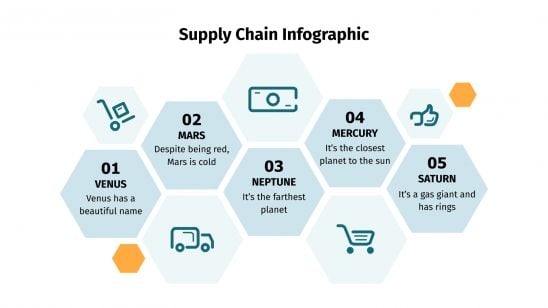
Exposure to dangerous gases, vapors and dust is one of the greatest hazards in the manufacturing of wind turbine blades. To reduce this risk, workers must wear respirators. They also need to be trained on how to use them. This is possible only with proper training. Ear protection is also a critical factor.
FAQ
What is production planning?
Production Planning refers to the development of a plan for every aspect of production. This document will ensure everything is in order and ready to go when you need it. This document should also include information on how to get the best result on set. This includes shooting schedules, locations, cast lists, crew details, and equipment requirements.
First, you need to plan what you want to film. You may have decided where to shoot or even specific locations you want to use. Once you have identified your locations and scenes it's time to begin figuring out what elements you will need for each one. For example, you might decide that you need a car but don't know exactly what model you want. If this is the case, you might start searching online for car models and then narrow your options by selecting from different makes.
After you have selected the car you want, you can begin to think about additional features. What about additional seating? You might also need someone to help you get around the back. You might want to change your interior color from black and white. These questions can help you decide the right look for your car. Also, think about what kind of shots you would like to capture. Will you be filming close-ups or wide angles? Maybe you want the engine or the steering wheels to be shown. These details will help identify the exact car you wish to film.
Once you've determined the above, it is time to start creating a calendar. You can use a schedule to determine when and where you need it to be shot. Each day will include the time when you need to arrive at the location, when you need to leave and when you need to return home. This way, everyone knows what they need to do and when. You can also make sure to book extra staff in advance if you have to hire them. There is no point in hiring someone who won't turn up because you didn't let him know.
You will need to factor in the days that you have to film when creating your schedule. Some projects take only a few days while others can last several weeks. When you are creating your schedule, you should always keep in mind whether you need more than one shot per day or not. Multiplying takes in the same area will result both in increased costs and a longer time. If you are unsure if you need multiple takes, it is better to err on the side of caution and shoot fewer takes rather than risk wasting money.
Budget setting is an important part of production planning. You will be able to manage your resources if you have a realistic budget. If you have to reduce your budget due to unexpected circumstances, you can always lower it later. However, it is important not to overestimate the amount that you will spend. You will end up spending less money if you underestimate the cost of something.
Planning production is a tedious process. Once you have a good understanding of how everything works together, planning future projects becomes easy.
What is the distinction between Production Planning or Scheduling?
Production Planning (PP), also known as forecasting and identifying production capacities, is the process that determines what product needs to be produced at any particular time. This is done through forecasting demand and identifying production capacities.
Scheduling refers to the process of allocating specific dates to tasks in order that they can be completed within a specified timeframe.
What does warehouse mean?
A warehouse is a place where goods are stored until they are sold. It can be either an indoor or outdoor space. It could be one or both.
What does it mean to be a manufacturer?
Manufacturing Industries are businesses that produce products for sale. Consumers are people who purchase these goods. This is accomplished by using a variety of processes, including production, distribution and retailing. They produce goods from raw materials by using machines and other machinery. This includes all types manufactured goods such as clothing, building materials, furniture, electronics, tools and machinery.
What is the job of a production plan?
Production planners ensure all aspects of the project are delivered within time and budget. A production planner ensures that the service and product meet the client's expectations.
What are the 7 Rs of logistics.
The acronym 7R's for Logistics stands to represent the seven basic principles in logistics management. It was created by the International Association of Business Logisticians and published in 2004 under its "Seven Principles of Logistics Management".
The acronym is made up of the following letters:
-
Responsive - ensure all actions are legal and not harmful to others.
-
Reliable - Have confidence in your ability to fulfill all of your commitments.
-
Reasonable - make sure you use your resources well and don't waste them.
-
Realistic – consider all aspects of operations, from cost-effectiveness to environmental impact.
-
Respectful – Treat others fairly and equitably.
-
You are resourceful and look for ways to save money while increasing productivity.
-
Recognizable is a company that provides customers with value-added solutions.
Are there any Manufacturing Processes that we should know before we can learn about Logistics?
No. No. Knowing about manufacturing processes will help you understand how logistics works.
Statistics
- In 2021, an estimated 12.1 million Americans work in the manufacturing sector.6 (investopedia.com)
- In the United States, for example, manufacturing makes up 15% of the economic output. (twi-global.com)
- (2:04) MTO is a production technique wherein products are customized according to customer specifications, and production only starts after an order is received. (oracle.com)
- Many factories witnessed a 30% increase in output due to the shift to electric motors. (en.wikipedia.org)
- According to a Statista study, U.S. businesses spent $1.63 trillion on logistics in 2019, moving goods from origin to end user through various supply chain network segments. (netsuite.com)
External Links
How To
How to use the Just In-Time Production Method
Just-in-time is a way to cut costs and increase efficiency in business processes. This is where you have the right resources at the right time. This means that you only pay the amount you actually use. Frederick Taylor was the first to coin this term. He developed it while working as a foreman during the early 1900s. After observing how workers were paid overtime for late work, he realized that overtime was a common practice. He decided to ensure workers have enough time to do their jobs before starting work to improve productivity.
JIT is a way to plan ahead and make sure you don't waste any money. The entire project should be looked at from start to finish. You need to ensure you have enough resources to tackle any issues that might arise. If you expect problems to arise, you will be able to provide the necessary equipment and personnel to address them. You won't have to pay more for unnecessary items.
There are many JIT methods.
-
Demand-driven JIT: You order the parts and materials you need for your project every other day. This will allow you to track how much material you have left over after using it. This will allow you to calculate how long it will take to make more.
-
Inventory-based: This allows you to store the materials necessary for your projects in advance. This allows you predict the amount you can expect to sell.
-
Project-driven: This means that you have enough money to pay for your project. When you know how much you need, you'll purchase the appropriate amount of materials.
-
Resource-based JIT : This is probably the most popular type of JIT. Here, you allocate certain resources based on demand. You might assign more people to help with orders if there are many. If you don’t have many orders you will assign less people to the work.
-
Cost-based: This is a similar approach to resource-based but you are not only concerned with how many people you have, but also how much each one costs.
-
Price-based: This is a variant of cost-based. However, instead of focusing on the individual workers' costs, this looks at the total price of the company.
-
Material-based: This is quite similar to cost-based, but instead of looking at the total cost of the company, you're concerned with how much raw materials you spend on average.
-
Time-based: This is another variation of resource-based JIT. Instead of focusing on the cost of each employee, you will focus on the time it takes to complete a project.
-
Quality-based JIT is another variant of resource-based JIT. Instead of thinking about the cost of each employee or the time it takes to produce something, you focus on how good your product quality.
-
Value-based JIT : This is the newest type of JIT. This is where you don't care about how the products perform or whether they meet customers' expectations. Instead, you're focused on how much value you add to the market.
-
Stock-based is an inventory-based system that measures the number of items produced at any given moment. It's useful when you want maximum production and minimal inventory.
-
Just-in time (JIT), planning: This is a combination JIT/supply chain management. It is the process of scheduling components' delivery as soon as they have been ordered. It's important as it reduces leadtimes and increases throughput.