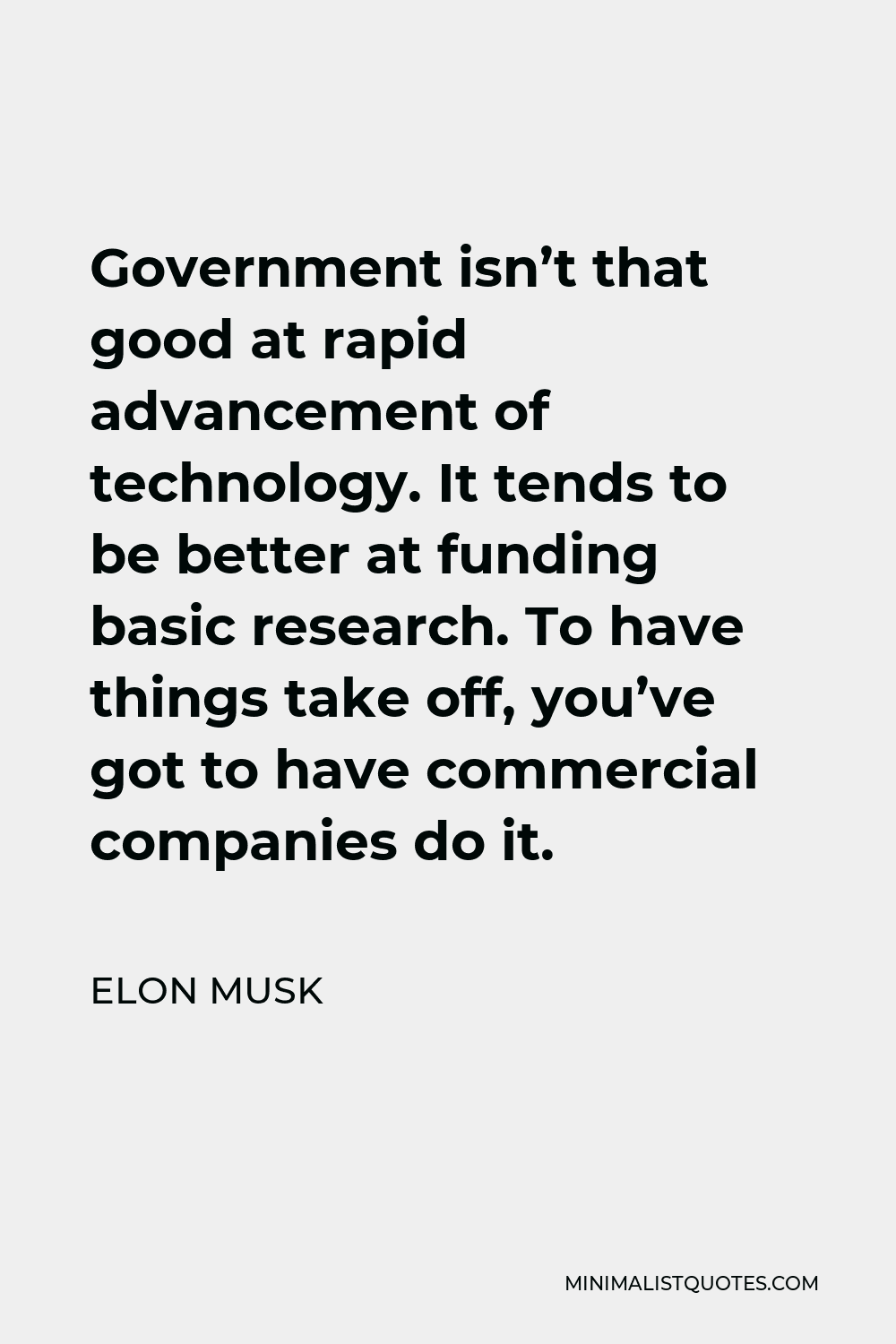
Purchasing Managers, also known as Materials Managers, are responsible for sourcing and coordinating all purchasing activities. They work with vendors, suppliers, and other purchasing agents. They need to have a good understanding of the company's purchasing process, and how to improve it. They must also be able and willing to negotiate the best deals possible for the company.
Purchaser managers must also keep accurate and current purchasing records. They analyse customer requirements, assess financial reports, evaluate vendor capabilities and evaluate price trends. They coordinate purchasing activities and work with other departments. They may need to work overtime when the company has urgent needs for supplies from international markets.
Purchasing managers also coordinate and manage inventory and logistics. They determine the best method of purchasing and ensure that purchased items are in compliance with company quality standards. They coordinate with staff to manage their budgets and ensure that purchases are made at the lowest possible price. They also work to find the best vendors and negotiate contracts.
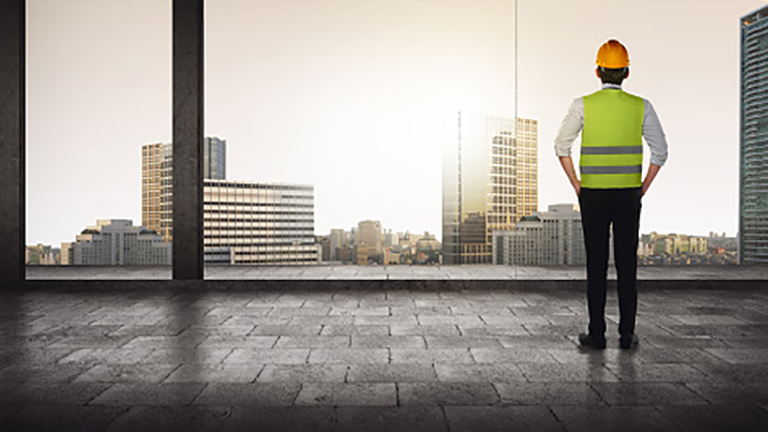
Purchasing Managers also monitor and manage the time schedules of all purchasing employees. They also assess the quality of purchased goods and the delivery time. They meet with suppliers and buyers and visit their distribution facilities. They also make sure that suppliers comply with the terms of the contract. They may also have responsibility for team building and disciplinary issues.
Excellent communication skills and analytical abilities are essential for purchasing managers. They also need to be strategic thinkers. They need to be able analyse the effects of various products on the company. They should also know how to manage suppliers. They should be able make business decisions, and increase sales. They should be able manage complicated purchases. They should be able evaluate potential vendors and analyze their capabilities to find the right vendor for the company.
A bachelor's degree in business is required for purchasing managers. A bachelor's degree in business or a related field is helpful. They should also be familiar with Microsoft Office and other software programs.
The best purchasing manager should be capable of finding the best deals, and negotiating the most favorable contracts. They should also be able to coordinate all purchasing activities, manage inventories, and keep track of vendor and supplier performance. They should also have the ability to manage a team of purchasing agents.
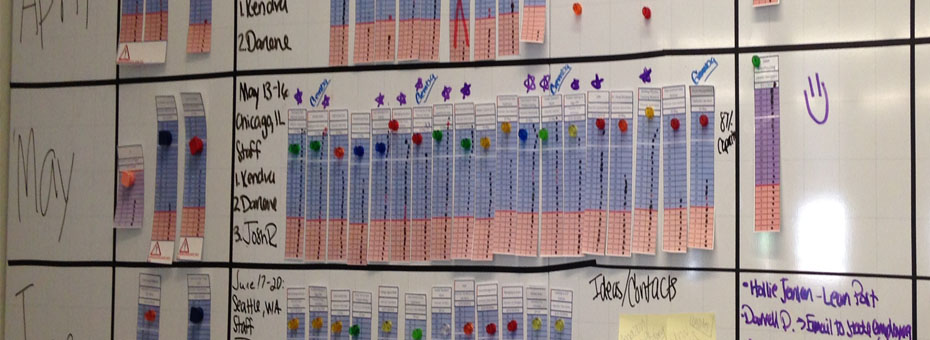
The job description of a purchasing manager should mention the importance of purchasing to the company. It should also include how vital it is for the company that they stay ahead of their competitors. It should also reflect how much the company values its employees' personal and professional lives. It should also contain a call-to-action to encourage applicants.
Sometimes, the Purchasing Manager may be required to work overtime in order to purchase equipment and materials for an international marketplace. They might also need to meet with sellers and vendors or attend trade shows.
FAQ
What are the products and services of logistics?
Logistics are the activities involved in moving goods from point A to point B.
They encompass all aspects transport, including packaging and loading, transporting, storage, unloading.
Logisticians ensure that the product is delivered to the correct place, at the right time, and under safe conditions. They provide information on demand forecasts as well stock levels, production schedules and availability of raw material.
They can also track shipments in transit and monitor quality standards.
What are the four types in manufacturing?
Manufacturing is the process by which raw materials are transformed into useful products through machines and processes. Manufacturing can include many activities such as designing and building, testing, packaging shipping, selling, servicing, and other related activities.
What does "warehouse" mean?
A warehouse is an area where goods are stored before being sold. It can be either an indoor or outdoor space. It may also be an indoor space or an outdoor area.
What are the 7 Rs of logistics?
The acronym 7R's of Logistic is an acronym that stands for seven fundamental principles of logistics management. It was published in 2004 by the International Association of Business Logisticians as part of their "Seven Principles of Logistics Management" series.
The acronym consists of the following letters:
-
Responsible - ensure that all actions taken are within legal requirements and are not harmful to others.
-
Reliable: Have faith in your ability or the ability to honor any promises made.
-
It is reasonable to use resources efficiently and not waste them.
-
Realistic - Consider all aspects of operations, including environmental impact and cost effectiveness.
-
Respectful – Treat others fairly and equitably.
-
Resourceful - look for opportunities to save money and increase productivity.
-
Recognizable provides value-added products and services to customers
What is production plan?
Production Planning includes planning for all aspects related to production. It is important to have everything ready and planned before you start shooting. It should also contain information on achieving the best results on set. This information includes locations, crew details and equipment requirements.
The first step is to outline what you want to film. You may have already decided where you would like to shoot, or maybe there are specific locations or sets that you want to use. Once you have identified your locations and scenes it's time to begin figuring out what elements you will need for each one. One example is if you are unsure of the exact model you want but decide that you require a car. This is where you can look up car models online and narrow down your options by choosing from different makes and models.
After you've found the perfect car, it's time to start thinking about adding extras. What about additional seating? Or maybe you just need someone to push the car around. You may want to change the interior's color from black or white. These questions will help guide you in determining the ideal look and feel for your car. It is also worth considering the types of shots that you wish to take. What type of shots will you choose? Maybe you want to show your engine or the steering wheel. These details will help identify the exact car you wish to film.
Once you have all the information, you are ready to create a plan. You can create a schedule that will outline when you must start and finish your shoots. The schedule will show you when to get there, what time to leave, and when to return home. Everyone knows exactly what they should do and when. If you need to hire extra staff, you can make sure you book them in advance. You should not hire anyone who doesn't show up because of your inaction.
When creating your schedule, you will also need to consider the number of days you need to film. Some projects can be completed in a matter of days or weeks. Others may take several days. It is important to consider whether you require more than one photo per day when you create your schedule. Multiple takes of the same location will lead to higher costs and take more time. If you aren't sure whether you need multiple shots, it is best to take fewer photos than you would like.
Another important aspect of production planning is setting budgets. Setting a realistic budget is essential as it will allow you to work within your means. It is possible to reduce the budget at any time if you experience unexpected problems. However, you shouldn't overestimate the amount of money you will spend. If you underestimate the cost of something, you will have less money left after paying for other items.
Production planning is a complicated process. But once you understand how everything works together, it becomes much easier to plan future project.
What are manufacturing and logistics?
Manufacturing is the production of goods using raw materials. Logistics is the management of all aspects of supply chain activities, including procurement, production planning, distribution, warehousing, inventory control, transportation, and customer service. As a broad term, manufacturing and logistics often refer to both the creation and delivery of products.
What is the role of a production manager?
A production planner ensures all aspects of the project are delivered on time, within budget, and within scope. They ensure that the product or service is of high quality and meets client requirements.
Statistics
- You can multiply the result by 100 to get the total percent of monthly overhead. (investopedia.com)
- In the United States, for example, manufacturing makes up 15% of the economic output. (twi-global.com)
- In 2021, an estimated 12.1 million Americans work in the manufacturing sector.6 (investopedia.com)
- (2:04) MTO is a production technique wherein products are customized according to customer specifications, and production only starts after an order is received. (oracle.com)
- Job #1 is delivering the ordered product according to specifications: color, size, brand, and quantity. (netsuite.com)
External Links
How To
How to Use the Just In Time Method in Production
Just-intime (JIT), which is a method to minimize costs and maximize efficiency in business process, is one way. It allows you to get the right amount resources at the right time. This means that you only pay for what you actually use. Frederick Taylor was the first to coin this term. He developed it while working as a foreman during the early 1900s. He saw how overtime was paid to workers for work that was delayed. He realized that workers should have enough time to complete their jobs before they begin work. This would help increase productivity.
JIT is an acronym that means you need to plan ahead so you don’t waste your money. It is important to look at your entire project from beginning to end and ensure that you have enough resources to handle any issues that may arise. If you anticipate that there might be problems, you'll have enough people and equipment to fix them. You won't have to pay more for unnecessary items.
There are different types of JIT methods:
-
Demand-driven: This type of JIT allows you to order the parts/materials required for your project on a regular basis. This will enable you to keep track of how much material is left after you use it. It will also allow you to predict how long it takes to produce more.
-
Inventory-based: This type allows you to stock the materials needed for your projects ahead of time. This allows for you to anticipate how much you can sell.
-
Project-driven : This is a method where you make sure that enough money is set aside to pay the project's cost. When you know how much you need, you'll purchase the appropriate amount of materials.
-
Resource-based JIT is the most widespread form. This is where you assign resources based upon demand. You will, for example, assign more staff to deal with large orders. If you don't receive many orders, then you'll assign fewer employees to handle the load.
-
Cost-based: This is the same as resource-based except that you don't care how many people there are but how much each one of them costs.
-
Price-based: This is a variant of cost-based. However, instead of focusing on the individual workers' costs, this looks at the total price of the company.
-
Material-based: This approach is similar to cost-based. However, instead of looking at the total cost for the company, you look at how much you spend on average on raw materials.
-
Time-based JIT: This is another variant of resource-based JIT. Instead of worrying about how much each worker costs, you can focus on how long the project takes.
-
Quality-based: This is yet another variation of resource-based JIT. Instead of focusing on the cost of each worker or how long it takes, think about how high quality your product is.
-
Value-based JIT is the newest form of JIT. In this scenario, you're not concerned about how products perform or whether customers expect them to meet their expectations. Instead, you focus on the added value that you provide to your market.
-
Stock-based: This stock-based method focuses on the actual quantity of products being made at any given time. It's used when you want to maximize production while minimizing inventory.
-
Just-in-time (JIT) planning: This is a combination of JIT and supply chain management. It refers to the process of scheduling the delivery of components as soon as they are ordered. This is important as it reduces lead time and increases throughput.