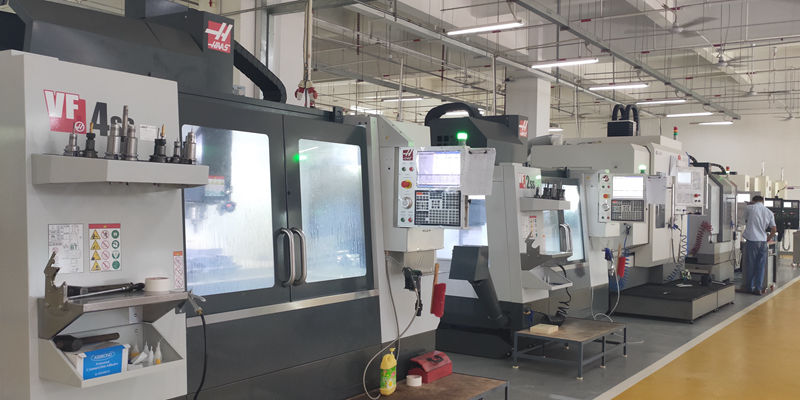
Advanced manufacturing refers specifically to the use innovative technology to improve processes and products. The technology used to achieve this can be classified as "advanced," "innovative," or "cutting edge." These industries are integrating innovative technologies into their manufacturing processes as they increase the number of advanced manufacturing companies. Below are examples of advanced production. Here are some of the most commonly used technologies in advanced production.
Continuous manufacturing
Continuous manufacturing dates back as far as the 1700s. It was used to produce pigiron in blast furnaces. Since then, the idea has spread to other industries, such as automotive, food, oil, refining, chemicals and pulp & paper. Continuous manufacturing is now gaining significant traction in biopharmaceutical, drawing the attention and support of CMOs as well as big pharma players.
The FDA and its partners recently discussed the benefits of continuous manufacturing for therapeutic proteins. This legislation would establish national standards and allow companies to create them. This legislation is intended to improve the creation and use of medical products. Companies would be encouraged to use continuous manufacturing for product development and improvement. But it is essential to ensure that continuous manufacture processes are safe.
Automated processes
Automating advanced manufacturing processes is a great way to increase efficiency and reduce costs. Automation can be used to make the most out of floor space, while increasing production efficiency. Manufacturers can cut costs and improve productivity by leveraging automation technology and collecting data. Process industry automation also saves time and money. The initial investment is not cheap, but it will ultimately increase the bottom line for a manufacturing company.
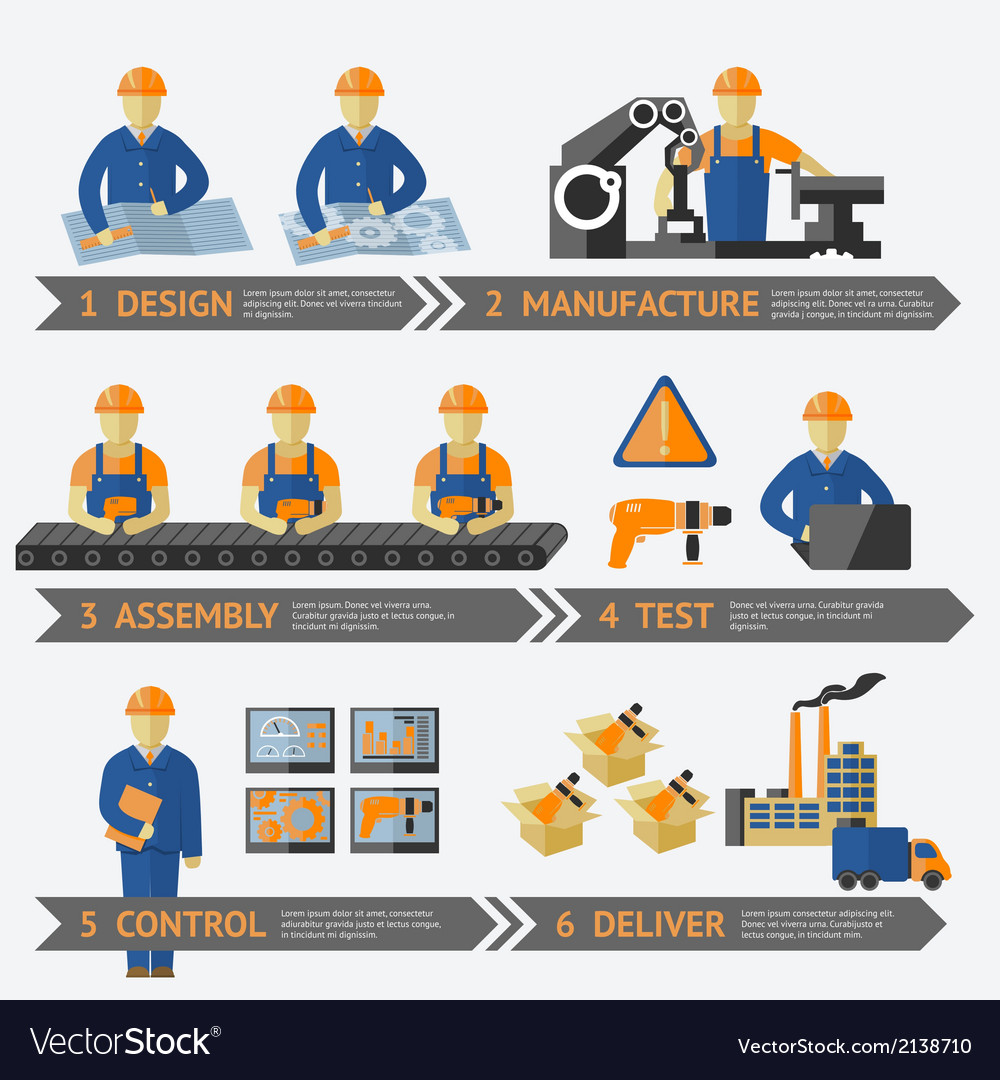
Modern companies combine advanced manufacturing processes and automated processes. Audi is one example. They use automated welding and bonding processes to reduce their production time while also saving energy and weight. Advanced manufacturing techniques, such as regenerative braking for conveyor systems are used. 3D printing, which is a major advancement in manufacturing, has only recently been adopted by mainstream companies. But what makes it so attractive to manufacturers?
Internet of Things
The IIoT revolution has transformed manufacturing with the help of sensors that monitor machines and their operations. These sensors collect data from all parts of the manufacturing process and send it to a central base station. This data is then processed and analyzed, which can be used to improve processes and eliminate waste. Advanced manufacturers use IIoT to monitor production processes and optimize their output. The IIoT industrial version is connected key fobs.
IIoT deployment will require a clear roadmap and sufficient development capabilities to enable the rollout of use cases in an efficient and scalable manner. This road map is from an automaker and shows three waves of deployment.
Cost-effectiveness
It is not always possible to compare the costs of advanced manufacturing with traditional production methods. The traditional cost-benefit analysis, however, is not sufficient to evaluate economic benefits. A holistic model that takes into account both the benefits and costs of technology can identify new benefits, and help speed decision-making. In this paper, Schroer and Munker develop an advanced cost-benefit tool that addresses the key issues associated with AMS implementation.
Information technology advancements are quickly changing the face of manufacturing. As production systems become more networked and smart, they are also becoming more efficient. Cost pressures are increasing the focus on productivity and the ability of companies to respond to customers' needs. The adoption of advanced manufacturing technologies is likely to accelerate the implementation and cost effectiveness of new technologies. As the industry continues digitizing, it is likely that such technologies will be adopted more quickly.
Human error reduction
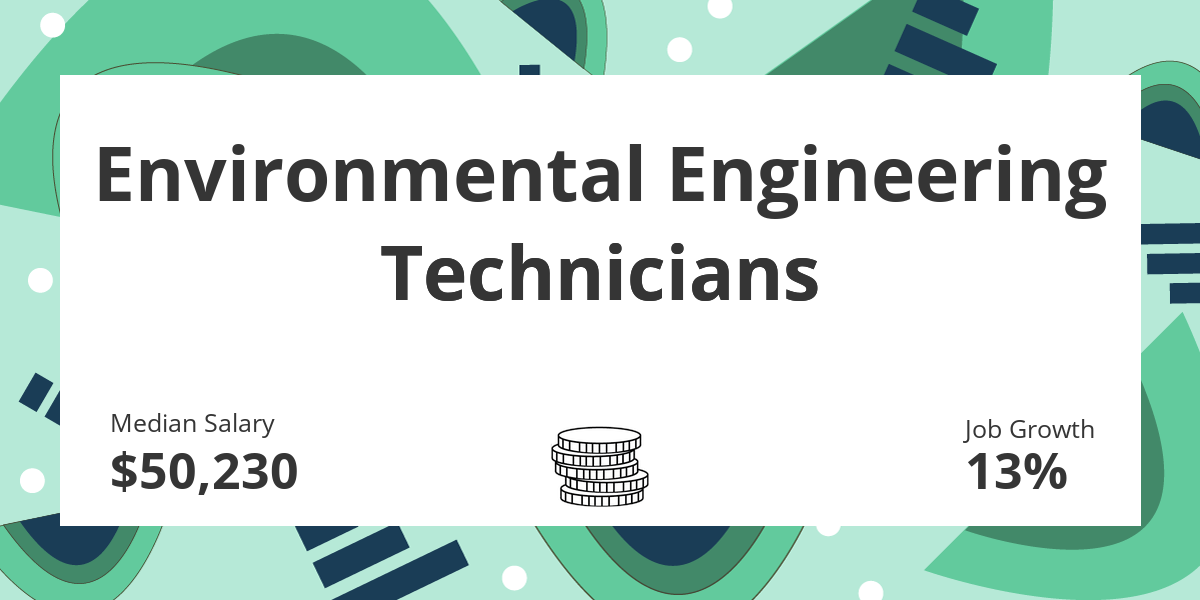
Although humans can make mistakes, the manufacturing process used to create a product is designed to minimize them. Human error can happen when employees don't read or understand instructions. For example, pharmaceutical laboratories must follow specific procedures when making drugs. Some employees believe they are familiar with a process and know how to use the correct ingredients. They then proceed to make the compound without consulting the written instructions.
A way to reduce human errors is to communicate effectively between junior and senior employees. Employers who are treated harshly will make mistakes. Therefore, managers should avoid punishing employees who ask questions. Employees should feel at ease asking questions. If they don't feel comfortable asking questions they won't be inclined to take corrective action. Respect senior employees' opinions and communicate with them in a friendly and professional manner.
FAQ
What is the difference between a production planner and a project manager?
The main difference between a production planner and a project manager is that a project manager is usually the person who plans and organizes the entire project, whereas a production planner is mainly involved in the planning stage of the project.
What is production management?
Production Planning involves developing a plan for all aspects of the production, including scheduling, budgeting, casting, crew, location, equipment, props, etc. This document aims to ensure that everything is planned and ready when you are ready to shoot. This document should include information about how to achieve the best results on-set. This information includes locations, crew details and equipment requirements.
The first step is to outline what you want to film. You may have already decided where you would like to shoot, or maybe there are specific locations or sets that you want to use. Once you have identified your locations and scenes it's time to begin figuring out what elements you will need for each one. You might decide you need a car, but not sure what make or model. To narrow your options, you can search online for available models.
Once you have found the right vehicle, you can think about adding accessories. What about additional seating? Or perhaps you need someone walking around the back of the car? You may want to change the interior's color from black or white. These questions will help to determine the style and feel of your car. It is also worth considering the types of shots that you wish to take. What type of shots will you choose? Maybe you want the engine or the steering wheels to be shown. These factors will help you determine which car style you want to film.
Once you've determined the above, it is time to start creating a calendar. You will know when you should start and when you should finish shooting. A schedule for each day will detail when you should arrive at the location and when you need leave. This way, everyone knows what they need to do and when. You can also make sure to book extra staff in advance if you have to hire them. It is not worth hiring someone who won’t show up because you didn’t tell him.
Also, consider how many days you will be filming your schedule. Some projects may only take a couple of days, while others could last for weeks. You should consider whether you will need more than one shot per week when creating your schedule. Multiple shots at the same location can increase costs and make it more difficult to complete. You can't be certain if you will need multiple takes so it is better not to shoot too many.
Budget setting is an important part of production planning. You will be able to manage your resources if you have a realistic budget. If you have to reduce your budget due to unexpected circumstances, you can always lower it later. You shouldn't underestimate the amount you'll spend. If you underestimate the cost of something, you will have less money left after paying for other items.
Production planning is a complicated process. But once you understand how everything works together, it becomes much easier to plan future project.
Why automate your warehouse
Modern warehousing is becoming more automated. E-commerce has increased the demand for quicker delivery times and more efficient processes.
Warehouses should be able adapt quickly to new needs. Technology is essential for warehouses to be able to adapt quickly to changing needs. Automating warehouses has many benefits. Here are some benefits of investing in automation
-
Increases throughput/productivity
-
Reduces errors
-
Accuracy is improved
-
Boosts safety
-
Eliminates bottlenecks
-
Companies can scale up more easily
-
It makes workers more efficient
-
Gives you visibility into all that is happening in your warehouse
-
Enhances customer experience
-
Improves employee satisfaction
-
This reduces downtime while increasing uptime
-
This ensures that quality products are delivered promptly
-
Eliminates human error
-
It ensures compliance with regulations
How can overproduction in manufacturing be reduced?
Improved inventory management is the key to reducing overproduction. This would reduce the time spent on unproductive activities like purchasing, storing and maintaining excess stock. This could help us free up our time for other productive tasks.
This can be done by using a Kanban system. A Kanbanboard is a visual tool that allows you to keep track of the work being done. Kanban systems allow work items to move through different states until they reach their final destination. Each state has a different priority level.
To illustrate, work can move from one stage or another when it is complete enough for it to be moved to a new stage. However, if a task is still at the beginning stages, it will remain so until it reaches the end of the process.
This allows for work to continue moving forward, while also ensuring that there is no work left behind. A Kanban board allows managers to monitor how much work is being completed at any given moment. This information allows them to adjust their workflow based on real-time data.
Lean manufacturing can also be used to reduce inventory levels. Lean manufacturing works to eliminate waste throughout every stage of the production chain. Any product that isn't adding value can be considered waste. Here are some examples of common types.
-
Overproduction
-
Inventory
-
Unnecessary packaging
-
Excess materials
These ideas can help manufacturers improve efficiency and reduce costs.
What does it mean to warehouse?
Warehouses and storage facilities are where goods are kept before being sold. It can be either an indoor or outdoor space. In some cases it could be both indoors and outdoors.
What is the difference between Production Planning and Scheduling?
Production Planning (PP), also known as forecasting and identifying production capacities, is the process that determines what product needs to be produced at any particular time. This can be done by forecasting demand and identifying production capabilities.
Scheduling is the process of assigning specific dates to tasks so they can be completed within the specified timeframe.
Statistics
- Many factories witnessed a 30% increase in output due to the shift to electric motors. (en.wikipedia.org)
- It's estimated that 10.8% of the U.S. GDP in 2020 was contributed to manufacturing. (investopedia.com)
- (2:04) MTO is a production technique wherein products are customized according to customer specifications, and production only starts after an order is received. (oracle.com)
- You can multiply the result by 100 to get the total percent of monthly overhead. (investopedia.com)
- In 2021, an estimated 12.1 million Americans work in the manufacturing sector.6 (investopedia.com)
External Links
How To
How to use the Just-In Time Method in Production
Just-intime (JIT), a method used to lower costs and improve efficiency in business processes, is called just-in-time. It's a way to ensure that you get the right resources at just the right time. This means that only what you use is charged to your account. The term was first coined by Frederick Taylor, who developed his theory while working as a foreman in the early 1900s. He noticed that workers were often paid overtime when they had to work late. He decided that workers would be more productive if they had enough time to complete their work before they started to work.
JIT is an acronym that means you need to plan ahead so you don’t waste your money. The entire project should be looked at from start to finish. You need to ensure you have enough resources to tackle any issues that might arise. You will have the resources and people to solve any problems you anticipate. This will ensure that you don't spend more money on things that aren't necessary.
There are different types of JIT methods:
-
Demand-driven: This is a type of JIT where you order the parts/materials needed for your project regularly. This will allow for you to track the material that you have left after using it. You'll also be able to estimate how long it will take to produce more.
-
Inventory-based : You can stock the materials you need in advance. This allows you to forecast how much you will sell.
-
Project-driven: This approach involves setting aside sufficient funds to cover your project's costs. If you know the amount you require, you can buy the materials you need.
-
Resource-based JIT: This type of JIT is most commonly used. Here you can allocate certain resources based purely on demand. If you have many orders, you will assign more people to manage them. If you don’t have many orders you will assign less people to the work.
-
Cost-based: This approach is very similar to resource-based. However, you don't just care about the number of people you have; you also need to consider how much each person will cost.
-
Price-based: This is a variant of cost-based. However, instead of focusing on the individual workers' costs, this looks at the total price of the company.
-
Material-based - This is a variant of cost-based. But instead of looking at the total company cost, you focus on how much raw material you spend per year.
-
Time-based: This is another variation of resource-based JIT. Instead of focusing solely on the amount each employee costs, focus on how long it takes for the project to be completed.
-
Quality-based: This is yet another variation of resource-based JIT. Instead of thinking about how much each employee costs or how long it takes to manufacture something, you think about how good the quality of your product is.
-
Value-based JIT: This is the latest form of JIT. In this case, you're not concerned with how well the products perform or whether they meet customer expectations. Instead, you focus on the added value that you provide to your market.
-
Stock-based: This inventory-based approach focuses on how many items are being produced at any one time. This is used to increase production and minimize inventory.
-
Just-in-time planning (JIT): This is a combination JIT and supply-chain management. It is the process that schedules the delivery of components within a short time of their order. It's important because it reduces lead times and increases throughput.