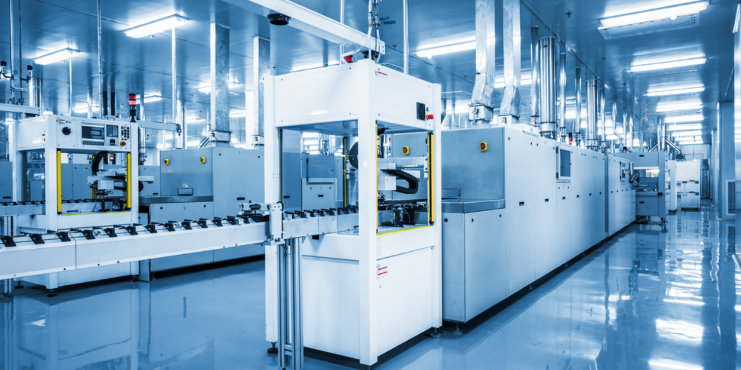
The surprising trend in the list of state manufacturers shows that the most popular suspects, such the southeastern, are not far from the top. This trend is changing. Many states now show that labor costs and quality can be traded to make the best deals. This trend shows that there are many factors that determine a state's ability to attract manufacturing jobs. How can you pick the right location for your business?
Group Five
You've found the right place if you are looking for a state-by-state list of Group Five companies. The Group Five portfolio includes steel pipes and structural components as well as industrial engineering products. The company provides pipe design services that offer the best price-to quality ratio for steel grade and thickness, as well as stiffening thin-walled pipes. The company makes use of the most recent CAD systems to design your pipes.
Group Three
The United States Census Bureau reports that approximately 50,000 manufacturers are located in Group Three. It has a low unemployment rate and a high rate economic growth. However it also has a low GDP growth rate. Because the majority of these manufacturers are small, this is why it has low unemployment rates. These limitations aside, the data can still serve as a guide. Listed below are the top manufacturers in each state. Continue reading to learn more.
The three largest European manufacturers are Audi, Mercedes-Benz and BMW. Honda and Toyota have dropped to fifth and sixth, respectively. However, the Detroit Three have reclaimed the Big Three title. This table shows the sales figures for each of these carmakers. Click the link to see the state's top-selling vehicle. There are many models for these manufacturers, including SUVs, minivans, and midsize sedans.
FAQ
What's the difference between Production Planning & Scheduling?
Production Planning (PP), is the process of deciding what production needs to take place at any given time. Forecasting demand is one way to do this.
Scheduling involves the assignment of dates and times to tasks in order to complete them within the timeframe.
What are the 4 types manufacturing?
Manufacturing is the process that transforms raw materials into useful products. Manufacturing involves many activities, including designing, building, testing and packaging, shipping, selling, service, and so on.
Is it possible to automate certain parts of manufacturing
Yes! Automation has been around since ancient times. The wheel was invented by the Egyptians thousands of years ago. To help us build assembly lines, we now have robots.
There are many uses of robotics today in manufacturing. They include:
-
Automated assembly line robots
-
Robot welding
-
Robot painting
-
Robotics inspection
-
Robots that produce products
Manufacturing could also benefit from automation in other ways. 3D printing makes it possible to produce custom products in a matter of days or weeks.
What is the difference between manufacturing and logistics
Manufacturing is the process of creating goods from raw materials by using machines and processes. Logistics includes all aspects related to supply chain management, such as procurement, distribution planning, inventory control and transportation. Manufacturing and logistics are often considered together as a broader term that encompasses both the process of creating products and delivering them to customers.
Statistics
- In 2021, an estimated 12.1 million Americans work in the manufacturing sector.6 (investopedia.com)
- According to the United Nations Industrial Development Organization (UNIDO), China is the top manufacturer worldwide by 2019 output, producing 28.7% of the total global manufacturing output, followed by the United States, Japan, Germany, and India.[52][53] (en.wikipedia.org)
- It's estimated that 10.8% of the U.S. GDP in 2020 was contributed to manufacturing. (investopedia.com)
- According to a Statista study, U.S. businesses spent $1.63 trillion on logistics in 2019, moving goods from origin to end user through various supply chain network segments. (netsuite.com)
- In the United States, for example, manufacturing makes up 15% of the economic output. (twi-global.com)
External Links
How To
How to use 5S in Manufacturing to Increase Productivity
5S stands in for "Sort", the "Set In Order", "Standardize", or "Separate". Toyota Motor Corporation was the first to develop the 5S approach in 1954. It allows companies to improve their work environment, thereby achieving greater efficiency.
The basic idea behind this method is to standardize production processes, so they become repeatable, measurable, and predictable. This means that daily tasks such as cleaning and sorting, storage, packing, labeling, and packaging are possible. Through these actions, workers can perform their jobs more efficiently because they know what to expect from them.
There are five steps to implementing 5S, including Sort, Set In Order, Standardize, Separate and Store. Each step is a different action that leads to greater efficiency. By sorting, for example, you make it easy to find the items later. Once you have placed items in an ordered fashion, you will put them together. After you have divided your inventory into groups you can store them in easy-to-reach containers. Finally, label all containers correctly.
Employees need to reflect on how they do their jobs. Employees must understand why they do certain tasks and decide if there's another way to accomplish them without relying on the old ways of doing things. To be successful in the 5S system, employees will need to acquire new skills and techniques.
The 5S method not only increases efficiency but also boosts morale and teamwork. They are more motivated to achieve higher efficiency levels as they start to see improvement.