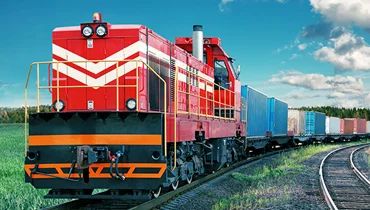
Kanban is a method of reducing costs and improving efficiency in manufacturing. These principles reduce downtime and inefficiencies. They also result in faster manufacturing and delivery, as well as better customer service. It also allows for continuous improvements.
Kanban is an organizational system that helps to monitor and control the flow of work. It helps manufacturers and teams to better track and monitor the processes they perform, and to improve productivity. Kanban involves the creation of a visual representation of the steps involved in a particular process and the identification and minimization or inefficiencies.
Kanban can be used either manually or through a software program. This software helps the team decide what they should do, and who should do it. It optimizes the process. Employees can also adapt to feedback and make improvements in their work processes using the kanban method. It is also useful in brainstorming.
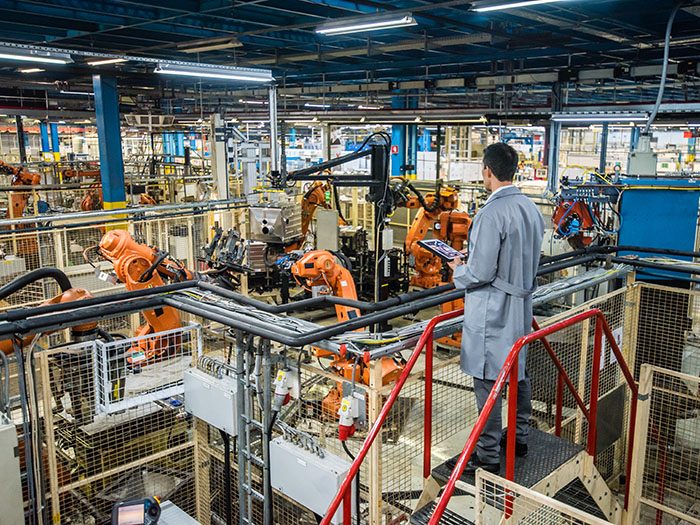
Kanban boards are a common example of Kanban in manufacturing. They depict a process. The board shows the order in which the steps are listed. For example, the first task is to contact a supplier. The second task is ordering the necessary supplies to complete the job. The third task involves manufacturing. The fourth task involves testing the product and shipping it.
The kanban method also allows the team to visualize their process, and to make small improvements as necessary. You can use the kanban board to improve communication between teams and identify and fix any bottlenecks.
Kanban can also be used to reduce waste and increase information sharing. This is especially important when a company is trying to implement Lean principles. Waste comes in many forms, and it can add up over the course of a manufacturing process. When a manufacturer removes waste, they add true value to every phase of the process. Kanban can also be used for inventory management. It can be used as a way to reduce inventory overstocking.
Kanban can be used to simplify the process and cut down on costs. Kanbans can be used to reduce the number and complexity of tasks, as well as to improve efficiency. It can also improve communication and reduce downtime. The kanban approach is a wonderful example of how technology can be used in order to complete a seemingly difficult task.
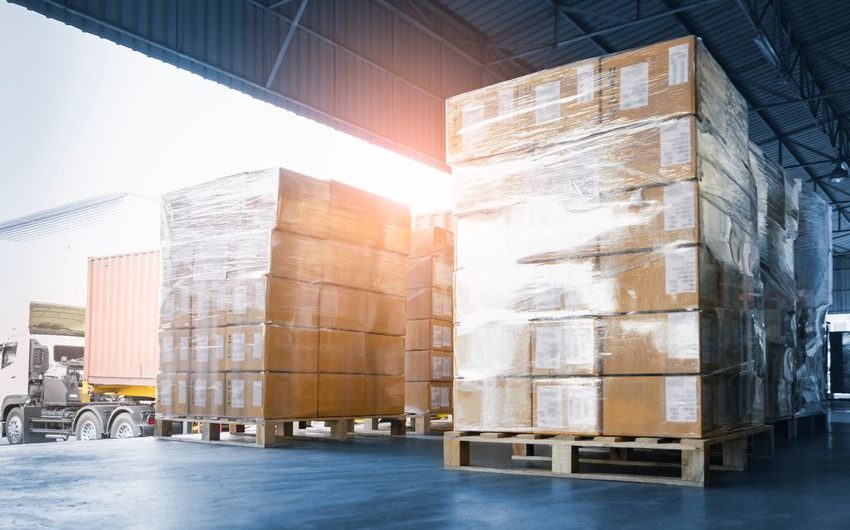
The kanban method is also useful as a brainstorming tool, and to improve productivity. Kanban can be used to link companies to suppliers and to improve communication. It also helps to improve quality, and to streamline the production process.
A board is one of the most popular Kanban examples in manufacturing. Here tasks are grouped by priority and time taken to complete them. A board can also display the steps involved with a process (such as design and manufacturing, testing, etc.
FAQ
What is the difference between a production planner and a project manager?
A production planner is more involved in the planning phase of the project than a project manger.
Is it necessary to be familiar with Manufacturing Processes before we learn about Logistics.
No. No. Knowing about manufacturing processes will help you understand how logistics works.
What kind of jobs are there in logistics?
There are many types of jobs in logistics. Some of them are:
-
Warehouse workers - They load trucks and pallets.
-
Transportation drivers - They drive trucks and trailers to deliver goods and carry out pick-ups.
-
Freight handlers, - They sort out and pack freight in warehouses.
-
Inventory managers – They manage the inventory in warehouses.
-
Sales reps are people who sell products to customers.
-
Logistics coordinators are responsible for organizing and planning logistics operations.
-
Purchasing agents: They are responsible for purchasing goods and services to support company operations.
-
Customer service representatives - They answer calls and emails from customers.
-
Shipping clerks: They process shipping requests and issue bills.
-
Order fillers are people who fill orders based only on what was ordered.
-
Quality control inspectors - They check incoming and outgoing products for defects.
-
Others – There are many other types available in logistics. They include transport supervisors, cargo specialists and others.
Statistics
- In the United States, for example, manufacturing makes up 15% of the economic output. (twi-global.com)
- It's estimated that 10.8% of the U.S. GDP in 2020 was contributed to manufacturing. (investopedia.com)
- You can multiply the result by 100 to get the total percent of monthly overhead. (investopedia.com)
- In 2021, an estimated 12.1 million Americans work in the manufacturing sector.6 (investopedia.com)
- Job #1 is delivering the ordered product according to specifications: color, size, brand, and quantity. (netsuite.com)
External Links
How To
How to Use the Just-In-Time Method in Production
Just-in-time is a way to cut costs and increase efficiency in business processes. It's the process of obtaining the right amount and timing of resources when you need them. This means that you only pay the amount you actually use. Frederick Taylor, a 1900s foreman, first coined the term. He saw how overtime was paid to workers for work that was delayed. He then concluded that if he could ensure that workers had enough time to do their job before starting to work, this would improve productivity.
JIT teaches you to plan ahead and prepare everything so you don’t waste time. The entire project should be looked at from start to finish. You need to ensure you have enough resources to tackle any issues that might arise. You can anticipate problems and have enough equipment and people available to fix them. This way, you won't end up paying extra money for things that weren't really necessary.
There are many JIT methods.
-
Demand-driven JIT: This is a JIT that allows you to regularly order the parts/materials necessary for your project. This will allow you to track how much material you have left over after using it. This will allow you to calculate how long it will take to make more.
-
Inventory-based: This is a type where you stock the materials required for your projects in advance. This allows you to predict how much you can expect to sell.
-
Project-driven: This approach involves setting aside sufficient funds to cover your project's costs. You will be able to purchase the right amount of materials if you know what you need.
-
Resource-based JIT : This is probably the most popular type of JIT. This is where you assign resources based upon demand. For instance, if you have a lot of orders coming in, you'll assign more people to handle them. If you don’t have many orders you will assign less people to the work.
-
Cost-based: This approach is very similar to resource-based. However, you don't just care about the number of people you have; you also need to consider how much each person will cost.
-
Price-based: This is very similar to cost-based, except that instead of looking at how much each individual worker costs, you look at the overall price of the company.
-
Material-based: This approach is similar to cost-based. However, instead of looking at the total cost for the company, you look at how much you spend on average on raw materials.
-
Time-based JIT: This is another variant of resource-based JIT. Instead of focusing on how much each employee costs, you focus on how long it takes to complete the project.
-
Quality-based JIT is another variant of resource-based JIT. Instead of focusing on the cost of each worker or how long it takes, think about how high quality your product is.
-
Value-based JIT: This is the latest form of JIT. This is where you don't care about how the products perform or whether they meet customers' expectations. Instead, your focus is on the value you bring to the market.
-
Stock-based: This is an inventory-based method that focuses on the actual number of items being produced at any given time. This method is useful when you want to increase production while decreasing inventory.
-
Just-in-time (JIT) planning: This is a combination of JIT and supply chain management. It refers to the process of scheduling the delivery of components as soon as they are ordered. It's important as it reduces leadtimes and increases throughput.