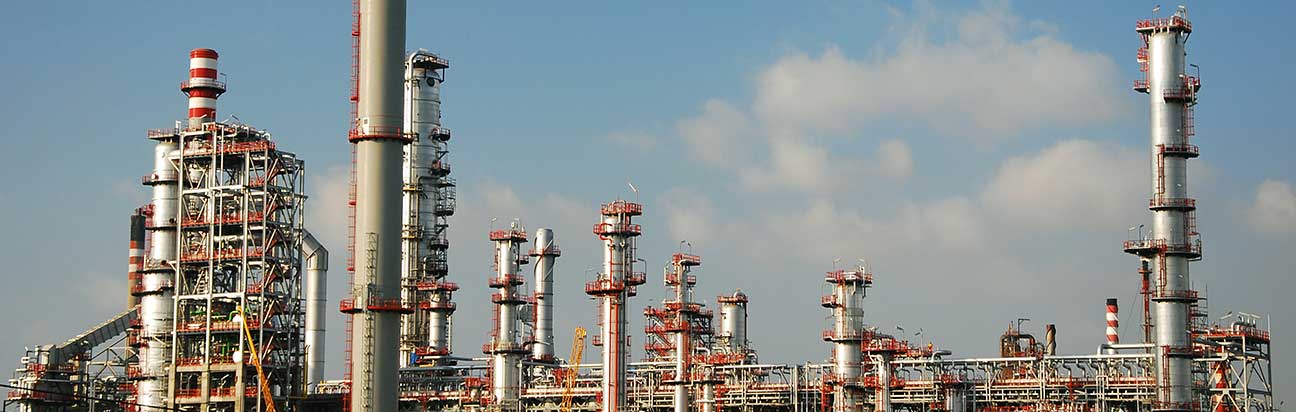
The Bureau Labor Statistics (BLS), an arm of Department of Labor, was established in 1884. It is a national statistical agency that collects, analyses, and disseminates vital economic information. It does research and analysis on a range of economic topics, including labor demand and prices, labor employment, wages, and the labor market. It also publishes various statistical reports and offers training in labor statistics for foreign countries.
Bureau Labor Statistics surveys the labor force to monitor and adjust wages and employment. It produces detailed industry estimates of nonfarm employment and wage rates. It also produces the Consumer Price Index, which measures prices of common consumer goods. The Bureau also measures changes in prices throughout the economy, including transport, housing and healthcare.
BLS publishes data for employment and wages in the United States, as well as other geographical areas. These data are often cited by economists, businessmen, and market participants. In addition to these reports, the Bureau also produces statistical tables, which allow users to view more detailed information on economic conditions. The Consumer Price Index is the most important. Other economic data is also produced by Bureau, such as Producers Price Index and Employment Situation Report.
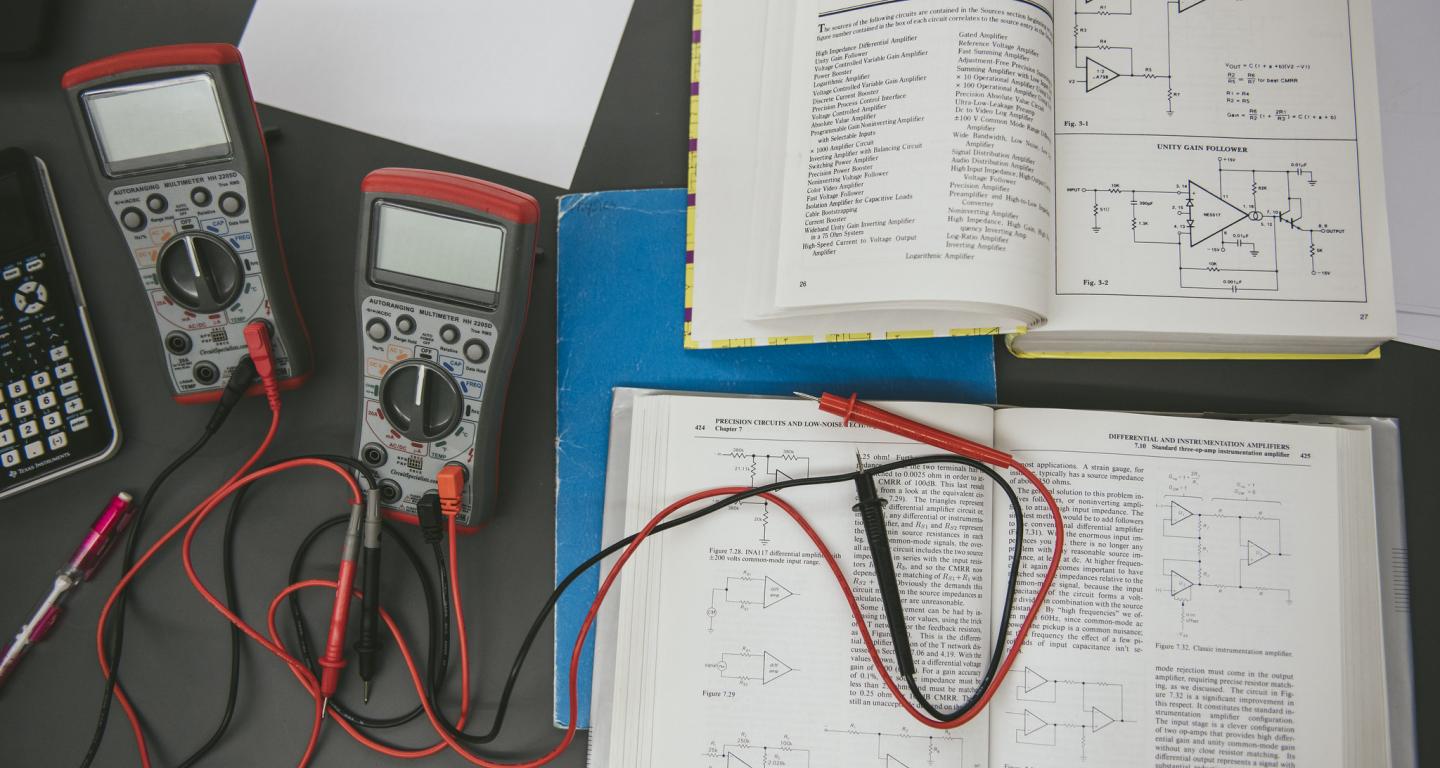
The Bureau of Labor Statistics does research on the employment of older Americans, teens, and women. It also compiles data about worker fatalities as well as non-fatal workplace injury. It also produces data files on low-wage workers. The Bureau also studies foreign-owned companies that have at most 10% of their stock held by foreigners.
The Bureau also publishes information regarding the national unemployment rate. This data is derived from Current Population Survey. The bureau also publishes various supplemental surveys. Current Employment Statistics, (CES) surveys approximately 670,000 worksites. BLS also studies the number of labor organizations and businesses in the country.
The Bureau also publishes "Employment and Earnings", which provides a national look at the labor market. This report contains information on the national unemployment rates, total employment, wages, as well as employment growth. The Bureau also publishes an index of the fastest growing jobs. The Bureau also provides listings of jobs in the labor force that pay the highest wages.
The Bureau employs a large number of people and has six regional offices. There are also several smaller local offices within the Bureau.
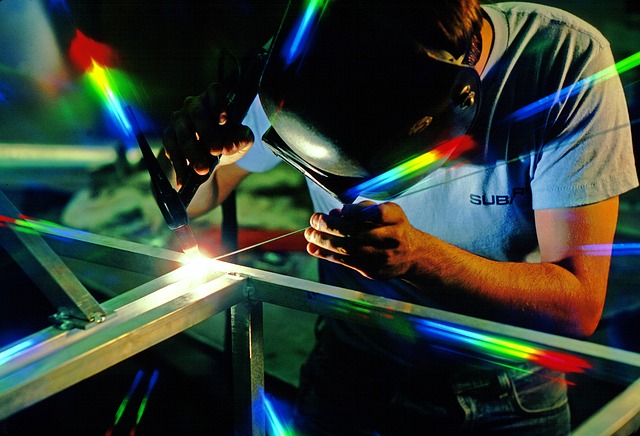
The Bureau also publishes a number of reports, which include the National Compensation Survey. The National Compensation Survey (US) is one of America's largest data gathering programs. This program tracks data on average earnings, hours work, and wages for employees in all industries. These data are then combined into an industry-specific average. The report is published quarterly in many industries. Other reports include the Occupational Outlook Quarterly, which offers analysis of the labor market for specific occupations.
The Bureau also houses an Office of Prices and Living Conditions that measures changes in prices. The Producer Price Index and Consumer Price Index is produced by the Office of Prices and Living Conditions. It also provides research about import and export prices.
FAQ
What is the difference between manufacturing and logistics
Manufacturing is the act of producing goods from raw materials using machines and processes. Logistics is the management of all aspects of supply chain activities, including procurement, production planning, distribution, warehousing, inventory control, transportation, and customer service. Sometimes manufacturing and logistics are combined to refer to a wider term that includes both the process of creating products as well as their delivery to customers.
What are the requirements to start a logistics business?
You need to have a lot of knowledge and skills to manage a successful logistic business. Good communication skills are essential to effectively communicate with your suppliers and clients. You should be able analyse data and draw inferences. You must be able and able to handle stress situations and work under pressure. To improve efficiency, you must be innovative and creative. You need to have strong leadership qualities to motivate team members and direct them towards achieving organizational goals.
It is also important to be efficient and well organized in order meet deadlines.
What jobs are available in logistics?
There are different kinds of jobs available in logistics. These are some of the jobs available in logistics:
-
Warehouse workers – They load, unload and transport pallets and trucks.
-
Transportation drivers – They drive trucks or trailers to transport goods and perform pick-ups.
-
Freight handlers are people who sort and pack freight into warehouses.
-
Inventory managers – They manage the inventory in warehouses.
-
Sales reps are people who sell products to customers.
-
Logistics coordinators: They plan and manage logistics operations.
-
Purchasing agents - They buy goods and services that are necessary for company operations.
-
Customer service representatives are available to answer customer calls and emails.
-
Shipping clerks - They process shipping orders and issue bills.
-
Order fillers - They fill orders based on what is ordered and shipped.
-
Quality control inspectors are responsible for inspecting incoming and outgoing products looking for defects.
-
Others - There is a variety of other jobs in logistics. These include transportation supervisors and cargo specialists.
Statistics
- In the United States, for example, manufacturing makes up 15% of the economic output. (twi-global.com)
- It's estimated that 10.8% of the U.S. GDP in 2020 was contributed to manufacturing. (investopedia.com)
- Many factories witnessed a 30% increase in output due to the shift to electric motors. (en.wikipedia.org)
- According to the United Nations Industrial Development Organization (UNIDO), China is the top manufacturer worldwide by 2019 output, producing 28.7% of the total global manufacturing output, followed by the United States, Japan, Germany, and India.[52][53] (en.wikipedia.org)
- You can multiply the result by 100 to get the total percent of monthly overhead. (investopedia.com)
External Links
How To
How to use the Just In-Time Production Method
Just-intime (JIT), which is a method to minimize costs and maximize efficiency in business process, is one way. It is a process where you get the right amount of resources at the right moment when they are needed. This means that you only pay for what you actually use. Frederick Taylor was the first to coin this term. He developed it while working as a foreman during the early 1900s. Taylor observed that overtime was paid to workers if they were late in working. He concluded that if workers were given enough time before they start work, productivity would increase.
JIT is a way to plan ahead and make sure you don't waste any money. It is important to look at your entire project from beginning to end and ensure that you have enough resources to handle any issues that may arise. You'll be prepared to handle any potential problems if you know in advance. You won't have to pay more for unnecessary items.
There are several types of JIT techniques:
-
Demand-driven: This JIT is where you place regular orders for the parts/materials that are needed for your project. This will allow for you to track the material that you have left after using it. This will let you know how long it will be to produce more.
-
Inventory-based : You can stock the materials you need in advance. This allows you to forecast how much you will sell.
-
Project-driven: This method allows you to set aside enough funds for your project. When you know how much you need, you'll purchase the appropriate amount of materials.
-
Resource-based JIT: This type of JIT is most commonly used. Here you can allocate certain resources based purely on demand. If you have many orders, you will assign more people to manage them. If you don’t have many orders you will assign less people to the work.
-
Cost-based: This is similar to resource-based, except that here you're not just concerned about how many people you have but how much each person costs.
-
Price-based: This is very similar to cost-based, except that instead of looking at how much each individual worker costs, you look at the overall price of the company.
-
Material-based - This is a variant of cost-based. But instead of looking at the total company cost, you focus on how much raw material you spend per year.
-
Time-based JIT: A variation on resource-based JIT. Instead of focusing solely on the amount each employee costs, focus on how long it takes for the project to be completed.
-
Quality-based JIT: This is another variation of resource based JIT. Instead of thinking about how much each employee costs or how long it takes to manufacture something, you think about how good the quality of your product is.
-
Value-based JIT: This is the latest form of JIT. You don't worry about whether the products work or if they meet customer expectations. Instead, you are focused on adding value to the marketplace.
-
Stock-based: This inventory-based approach focuses on how many items are being produced at any one time. This method is useful when you want to increase production while decreasing inventory.
-
Just-in-time (JIT) planning: This is a combination of JIT and supply chain management. It is the process of scheduling components' delivery as soon as they have been ordered. It's important because it reduces lead times and increases throughput.