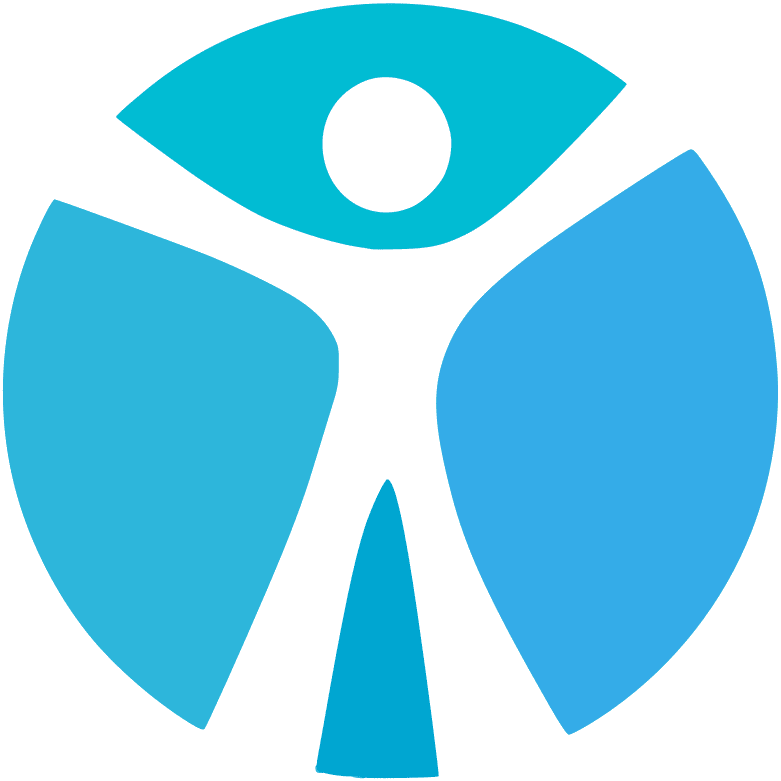
Using plain language and easy to understand explanations, the best books on lean manufacturing provide essential guidance to industry managers. The best-selling book covers a wide range of topics, including how to improve business operations, decrease expenses and improve quality. The book includes step-by-step instructions and detailed drawings that make it easy to implement. The book also includes information about the many different tools available for lean manufacturing.
The book gives an overview about the Toyota production process and Toyota's global success. It also describes Toyota's motivation, problem solving and management style. It provides information on Toyota's Lean strategy success as well as explains the 14 management concepts that underpin Toyota's business strategies. The book also contains a chapter on Toyota's involvement in the automotive market, which includes a section on Toyota using lean principles within the automotive sector.
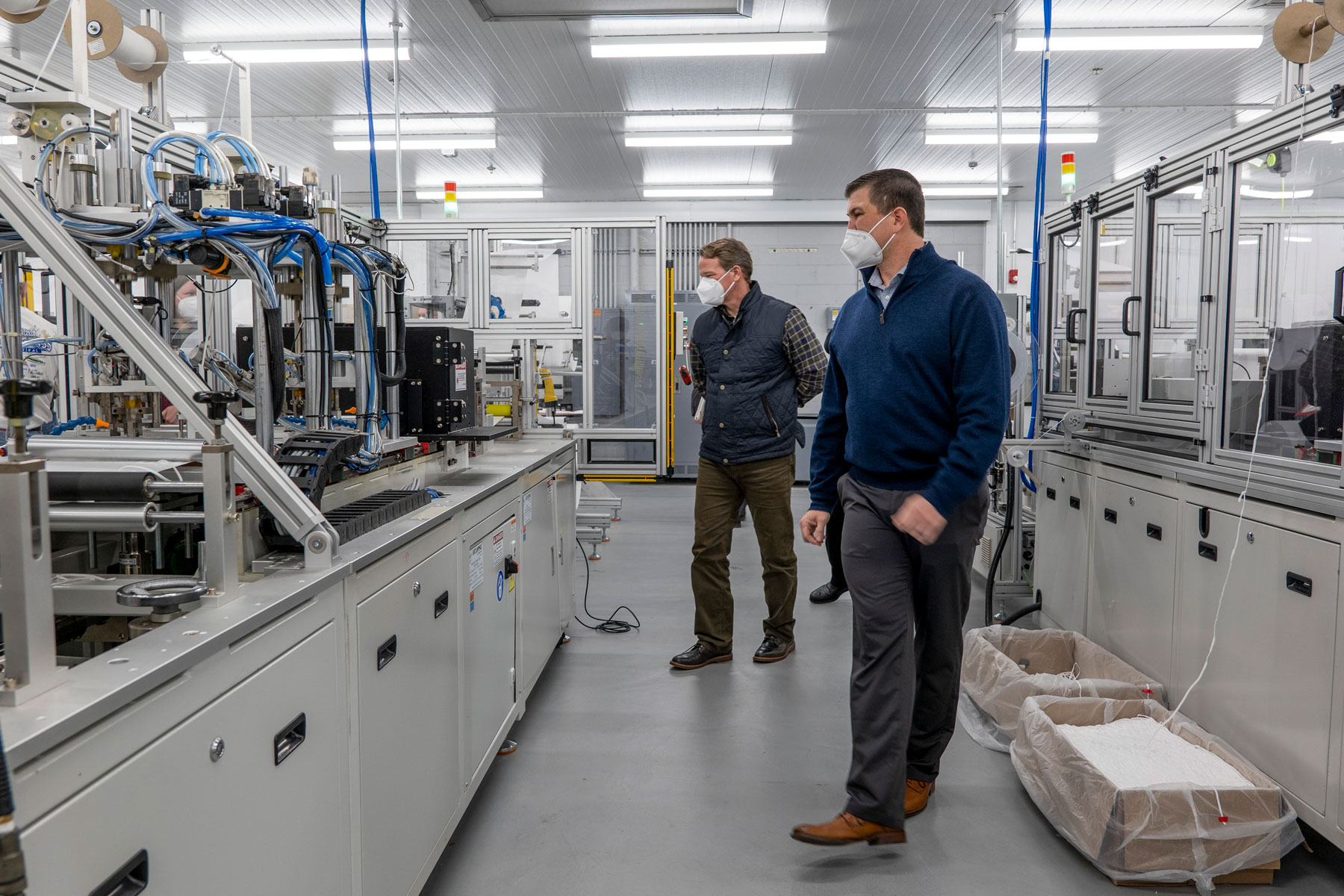
Lean manufacturing, or lean manufacturing, is a manufacturing method that aims at improving the quality of the products and/or services that a company produces. It eliminates waste to make the manufacturing process more efficient and less error-prone. Highly skilled workers and machines make manufacturing more efficient. These interactions make up the bulk of manufacturing company's overall costs.
The Lean Manufacturing Tool Book is one of the most popular books on lean production. The other two are The Toyota Way. 14 Management Principles for Improving Productivity and Quality. The Machine that Changed the World. How Toyota built a competitive advantage. These books cover the Toyota production system in detail and offer practical tips and steps for applying Lean techniques in any manufacturing setting. Lean Manufacturing Tool Book gives a detailed guide to the various tools required for Lean manufacturing. It provides expert advice and a list of the various tools available. The book includes information on Lean manufacturing concepts including Six Sigma, and Lean problem solving.
The Toyota Way was one of the first books to introduce Lean manufacturing. It discusses Toyota's management principles as well as how to implement them in your organization. It also includes organization profiles, as well as philosophies that form the foundation of Toyota's success. A new afterword discusses Lean's impact on the manufacturing sector since the book was published. It also provides updated frameworks for production processes, improving quality, and reducing costs.
The Machine that Changed the World: Why Lean Changed the World was the original book that fully explained the Toyota Production System (and its impact on the manufacturing industry). This book was published in 1990. It provides an overview of the system and gives the reader an important context for the role of Lean in the manufacturing industry since the book's publication. The book includes a revised introduction and an updated afterword to provide a better understanding about the Toyota Production System as well as its impact on global manufacturing. It also explains what the fundamental ideas are that underpin Lean today.
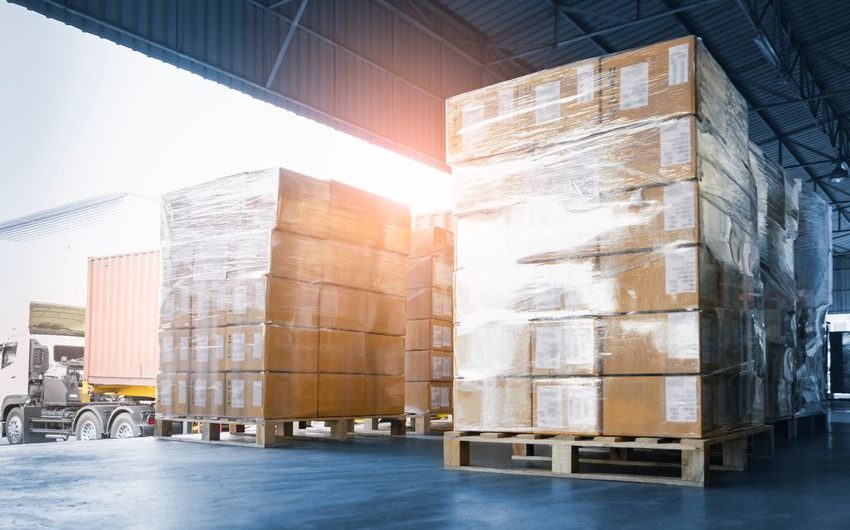
The Toyota Kata Flow-Focused Manufacturing Methodology: Another important book. It provides information about how Toyota works in partnership with their customers to provide top-quality products, and services. It explains how Toyota is committed to quality, problem-solving and speeding up business processes. It also explains Toyota's hiring and selection process, as well as how employees are motivated to produce high-quality products.
FAQ
What skills is required for a production planner?
A production planner must be organized, flexible, and able multitask to succeed. Effective communication with clients and colleagues is essential.
What are the 7 Rs of logistics.
The acronym 7Rs of Logistics refers to the seven core principles of logistics management. It was developed by the International Association of Business Logisticians (IABL) and published in 2004 as part of its "Seven Principles of Logistics Management" series.
The acronym consists of the following letters:
-
Responsible - ensure that all actions taken are within legal requirements and are not harmful to others.
-
Reliable: Have faith in your ability or the ability to honor any promises made.
-
Reasonable - use resources efficiently and don't waste them.
-
Realistic - consider all aspects of operations, including cost-effectiveness and environmental impact.
-
Respectful: Treat others with fairness and equity
-
You are resourceful and look for ways to save money while increasing productivity.
-
Recognizable - Provide value-added services to customers
What is the role of a manager in manufacturing?
A manufacturing manager must make sure that all manufacturing processes run smoothly and effectively. They must also be alert to any potential problems and take appropriate action.
They should also learn how to communicate effectively with other departments, including sales and marketing.
They should be informed about industry trends and be able make use of this information to improve their productivity and efficiency.
What do you mean by warehouse?
Warehouses and storage facilities are where goods are kept before being sold. You can have it indoors or outdoors. Sometimes, it can be both an indoor and outdoor space.
What does it mean to be a manufacturer?
Manufacturing Industries refers to businesses that manufacture products. Consumers are the people who purchase these products. To accomplish this goal, these companies employ a range of processes including distribution, sales, management, and production. They create goods from raw materials, using machines and various other equipment. This includes all types and varieties of manufactured goods, such as food items, clothings, building supplies, furnitures, toys, electronics tools, machinery vehicles, pharmaceuticals medical devices, chemicals, among others.
What is manufacturing and logistics?
Manufacturing is the process of creating goods from raw materials by using machines and processes. Logistics covers all aspects involved in managing supply chains, including procurement and production planning. Manufacturing and logistics are often considered together as a broader term that encompasses both the process of creating products and delivering them to customers.
Statistics
- [54][55] These are the top 50 countries by the total value of manufacturing output in US dollars for its noted year according to World Bank.[56] (en.wikipedia.org)
- It's estimated that 10.8% of the U.S. GDP in 2020 was contributed to manufacturing. (investopedia.com)
- In 2021, an estimated 12.1 million Americans work in the manufacturing sector.6 (investopedia.com)
- Job #1 is delivering the ordered product according to specifications: color, size, brand, and quantity. (netsuite.com)
- According to the United Nations Industrial Development Organization (UNIDO), China is the top manufacturer worldwide by 2019 output, producing 28.7% of the total global manufacturing output, followed by the United States, Japan, Germany, and India.[52][53] (en.wikipedia.org)
External Links
How To
How to use the Just In-Time Production Method
Just-intime (JIT), a method used to lower costs and improve efficiency in business processes, is called just-in-time. It's a way to ensure that you get the right resources at just the right time. This means that your only pay for the resources you actually use. Frederick Taylor first coined this term while working in the early 1900s as a foreman. Taylor observed that overtime was paid to workers if they were late in working. He realized that workers should have enough time to complete their jobs before they begin work. This would help increase productivity.
JIT is a way to plan ahead and make sure you don't waste any money. Also, you should look at the whole project from start-to-finish and make sure you have the resources necessary to address any issues. If you anticipate that there might be problems, you'll have enough people and equipment to fix them. This way you won't be spending more on things that aren’t really needed.
There are many JIT methods.
-
Demand-driven: This JIT is where you place regular orders for the parts/materials that are needed for your project. This will allow for you to track the material that you have left after using it. This will allow you to calculate how long it will take to make more.
-
Inventory-based: This is a type where you stock the materials required for your projects in advance. This allows you predict the amount you can expect to sell.
-
Project-driven : This is a method where you make sure that enough money is set aside to pay the project's cost. If you know the amount you require, you can buy the materials you need.
-
Resource-based JIT: This type of JIT is most commonly used. Here you can allocate certain resources based purely on demand. For example, if there is a lot of work coming in, you will have more people assigned to them. If you don't receive many orders, then you'll assign fewer employees to handle the load.
-
Cost-based: This is similar to resource-based, except that here you're not just concerned about how many people you have but how much each person costs.
-
Price-based: This is a variant of cost-based. However, instead of focusing on the individual workers' costs, this looks at the total price of the company.
-
Material-based - This is a variant of cost-based. But instead of looking at the total company cost, you focus on how much raw material you spend per year.
-
Time-based: This is another variation of resource-based JIT. Instead of focusing solely on the amount each employee costs, focus on how long it takes for the project to be completed.
-
Quality-based JIT: This is another variation of resource based JIT. Instead of worrying about the costs of each employee or how long it takes for something to be made, you should think about how quality your product is.
-
Value-based: This is one of the newest forms of JIT. In this instance, you are not concerned about the product's performance or meeting customer expectations. Instead, your focus is on the value you bring to the market.
-
Stock-based: This inventory-based approach focuses on how many items are being produced at any one time. It's used when you want to maximize production while minimizing inventory.
-
Just-in-time (JIT) planning: This is a combination of JIT and supply chain management. It is the process of scheduling components' delivery as soon as they have been ordered. It's important as it reduces leadtimes and increases throughput.